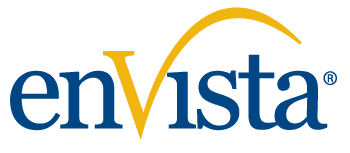
Planning Strategy
Warehousing & Distribution
Transportation
Network Design
Software Selection & Implementation
Material Handling
Robotics Integration
Warehouse Control Systems
SLAM Line Automation
IT Managed Services
Microsoft Application Management
Distribution
Manufacturing
Third-Party Logistics
Food & Beverage
Private Equity
Why enVista?
Leadership Team
- Honors & Awards
Home > 4 Warehouse Management System Case Studies

4 Warehouse Management System Case Studies
- July 23, 2020
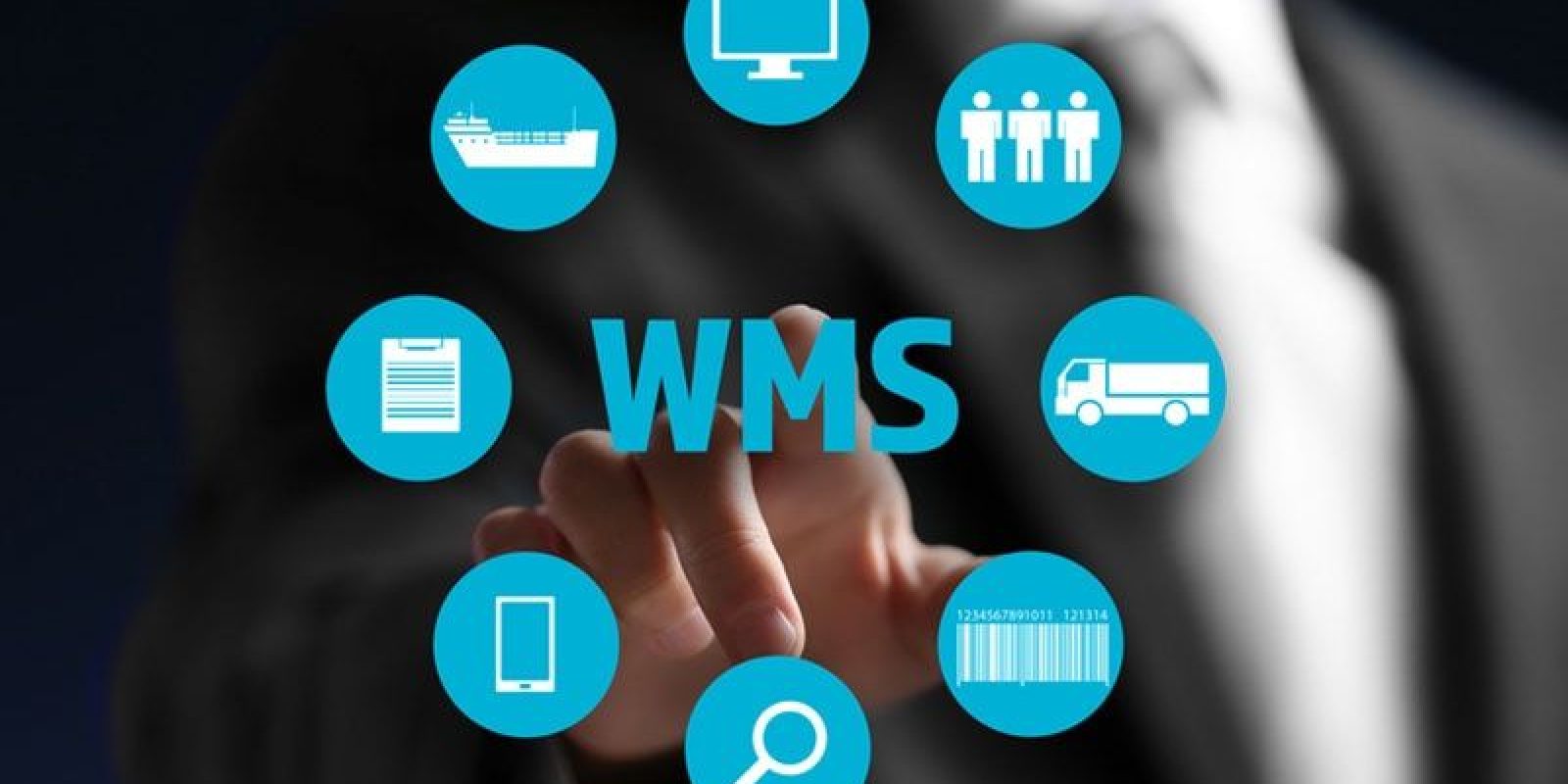
Successful WMS Implementation Case Studies
Warehouse Management Systems (WMS) represent a major investment in your supply chain and operational efficiency. While it can be difficult to gauge your estimated time to value, these four cases featuring enVista clients provide a warehouse management system business case and showcase outcomes after successful WMS implementations.
In this post, we’ll cover four examples of WMS implementations and how they helped companies to optimize warehouse operations :
- Nature’s Best
- Performance Bike
- Bradshaw International
- Men’s Wearhouse
Four WMS Implementation Examples
1. nature’s best.
*Note: Since project completion, Nature’s Best has been acquired by KeHE.*
Leading the market of health and natural foods distribution, Nature’s Best serves Certified Organic products in over twelve states. Nature’s Best was experiencing high labor costs based on time and manpower to transport temperature-controlled food products between four buildings on its DC campus. The company’s zones were organized to suit either small or large clients – a key competitive differentiator. Because of the facility layout, the overall distribution process was inefficient; each product was touched 18 times on its way to the customer. Nature’s Best technology, distribution processes and buildings also needed updating to keep pace with growth projections.
enVista was called upon to address and resolve the challenges Nature’s Best was facing and did so using its consult, implement and operate (CIO) methodology to create a customized solution.
Phase One: Consult
A supply chain strategy that met Nature’s Best’s business goals was developed. enVista conducted a material flow analysis and redesigned the internal flow processes to increase efficiencies. As a result, a global WMS was selected that addressed all of Nature’s Best’s concerns and determined construction needs for the distribution center (DC). Operations would be consolidated to one DC, and enVista designed the new facility with various temperature-controlled zones.
Phase Two: Implement
As Nature’s Best began construction, enVista supervised the integration and implemented a Manhattan Associates WMS including interface design, configuration, training, facility preparation and labor standards among other features. Nature’s Best shifted from a mechanized to non-mechanized system and from paper to radio-frequency (RF) devices with voice-based technology. enVista managed the move of $25 million of inventory and trained the company team on new system processes.
Phase Three: Operate
During go-live, enVista ensured a seamless transition into Nature’s Best new facility, systems and processes. Throughout the Consult, Implement, and Operate phases, sales were steady – even growing – and upon completion, the project was delivered on time and within budget. The chosen system required few modifications for Nature’s Best’s business model, which would lower costs and allow for easier upgrades in the future.
The new system reduced labor costs by over 30 percent and more than doubled productivity. Ninety-seven percent of full-time employees were retained, and temporary and non-value-added positions were eliminated. Nature’s Best went consultant-free only four weeks after go-live.
Download Nature’s Best Case Study
Example 2: Performance Bike
Performance Bike is a privately-held, specialty retailer focused on bicycles and accessories. The company had expanded to over 110 retail locations since its founding in 1982. Performance Bike had a DC in Chapel Hill, NC, with over 60 associates and partners with a 3PL in Long Beach, CA.
Due to compliance issues with the U.S. Postal Service barcodes, Performance Bike had to make system changes to its Manhattan PkMS WMS. The company’s experience with Manhattan Associates gave it a flexible approach when considering an upgrade. enVista’s enABLE methodology was used for the upgrade, and many of the roles typically filled by software or consulting companies were completed by Performance Bike.
Because of the prior experience and flexibility of Performance Bike and enVista, the WMS implementation was under budget and on time. Team members from both enVista and Performance Bike worked together to complete and implement the WMS. The vice president of warehouse operations for Performance Bike noted enVista’s customer-centric approach and flexibility.
The WMS upgrade was implemented in less than 6 months. There were very minor changes to the user experience, so trainings were seamless and increased productivity. Performance Bike experienced a pick per hour increase of 50 to 100 units per hour, exceeding the company’s executives’ expectations.
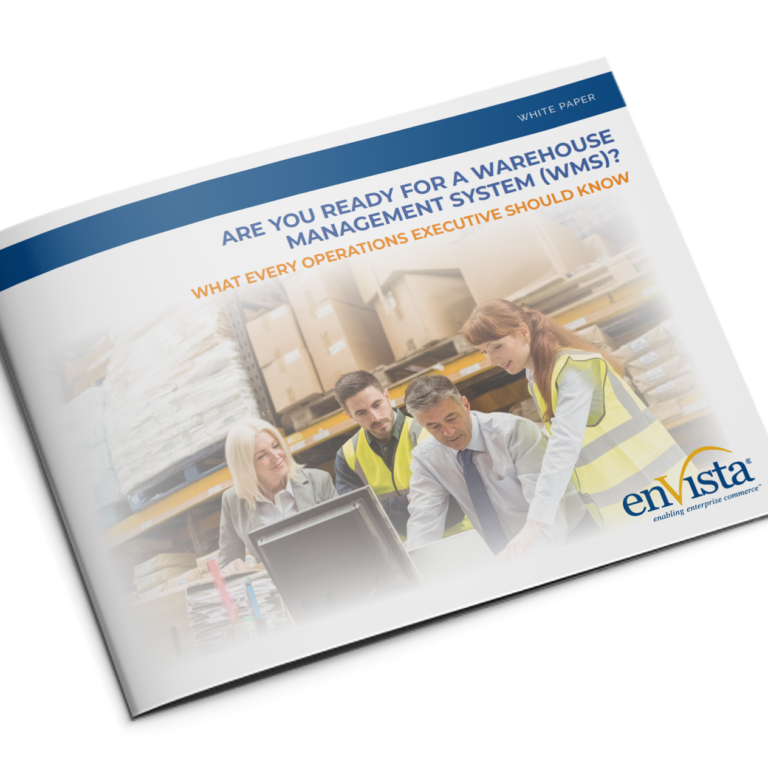
Are you Ready for a Warehouse Management System?
Discover what every operations executive should know about selecting a WMS to ensure a positive ROI, and improved operations.
Example 3: Bradshaw International
Bradshaw International’s Good Cook™ brand is sold in over 30,000 U.S. retail stores. Bradshaw is a leading marketer of kitchenware products and launched Good Cook to incorporate quality, value and service into every product. This philosophy has allowed Good Cook to achieve the best position for kitchen tools and gadgets with 43 percent of the market.
Bradshaw was asked to participate in Wal-Mart’s direct store delivery consolidation (DSDC) program as Good Cook is distributed in the stores. The program was designed to allow shippers to directly replenish Wal-Mart stores in less-than-case-pack quantities. To do so, Bradshaw had to make changes to several parts of its current distribution systems.
Changes to electric data interchange (EDI), order management, and a pick/pack operation integrated with a new WMS would be required to handle the new variable volumes. enVista was asked to help design and integrate the DSDC program. To meet Walmart’s DSDC objectives, the team had to design and build a new pick/pack module, select the technology to be used by the picking team, and integrate it with the WMS. The order management software , EDI software and billing system had to be modified to accommodate the structures required by Walmart’s DSDC program.
The team profiled SKU movements, identified pick and storage mediums to model replenishment rates, and formulated labor plans and proper work flows. Bradshaw IT and enVista worked together to make configuration changes to the RedPrairie WMS and integrate it with the Pick from Light System and EDI software. The joint team also specified data maps from order capture to order management to WMS through EDI transmissions to move the infrastructure to industry standards.
With enVista’s help, Bradshaw successfully integrated the DSDC program into operations. Shipping volumes increased beyond expectations, but the new WMS has allowed Bradshaw to keep up with demand. The program was implemented with almost no customer disruption.
Example 4: Men’s Wearhouse
Founded in 1973, Men’s Wearhouse is one of the country’s largest specialty retailers of men’s apparel with over 700 stores. The stores carry a full selection of high-end men’s clothing and accessories.
Men’s Warehouse’s main DC was a 1.1-million square foot facility in Houston, Texas. It is the core retail distribution center for Men’s Warehouse retail stores, as well as 60 percent of merchandise from K&G Retail stores, acquired in 1999. A significant percentage of its garment-on-hanger merchandise is shipped by dedicated fleet to regional hubs across the country. enVista’s main objective was to consolidate retail and e-commerce systems to run all operations on a single platform and a central material handling equipment (MHE) integration point.
enVista acted as the program management role for supply chain execution and MHE software functions for all facilities. The implementation of the new systems platform occurred in two distinct phases.
The first phase focused on using the new systems platform to more efficiently meet Men’s Wearhouse’s growing e-commerce business needs. A new WMS and distributed order management system were implemented and integrated to an e-commerce web platform. These systems allowed strategic decision making regarding e-commerce order fulfillment and room for growth, along with the accuracy and flexibility necessary for seamless execution and delivery.
Phase two focused on implementing the new WMS and a consolidated warehouse control system (WCS) in Men’s Wearhouse’s Retail Distribution Operation. The WMS replaced the retailer’s legacy system, and the WCS consolidated the management of several operations into one system. Men’s Wearhouse now has the ability to dynamically change product flow, unit allocation, and achieve more effective utilization of Case Level ASN receiving with the new WMS. The system’s ability to recognize and execute on cross-docking opportunities created improved throughput and lower overall processing costs.
With the implementation of a common WMS and standardized processes, Men’s Wearhouse was able to share recourses across operations and respond to seasonal increases in workload more effectively. The implementation of WMS and WCS gives the company the ability to consolidate its distinct Men’s Wearhouse and K&G distribution operations to reduce costs and increase overall processing efficiency.
Download Men’s Wearhouse Case Study
Conclusion: enVista’s WMS Expertise
Getting your WMS right and making sure it’s integrated properly across your supply chain technology stack is critical to realizing quick ROI and improved operational efficiencies.
enVista has completed hundreds of WMS implementation projects in its nearly two decades of experience, and our vendor agnostic approach to consulting and implementation ensures you get objective help for your most critical projects. We’re passionate about supply chains and delivering solutions that are the right fit for our clients and would love to help you optimize your supply chain.
If you have a WMS project on the horizon or want to learn more about how we can help you, let’s have a conversation .
About the Author
enVista Thought Leadership
Related posts.
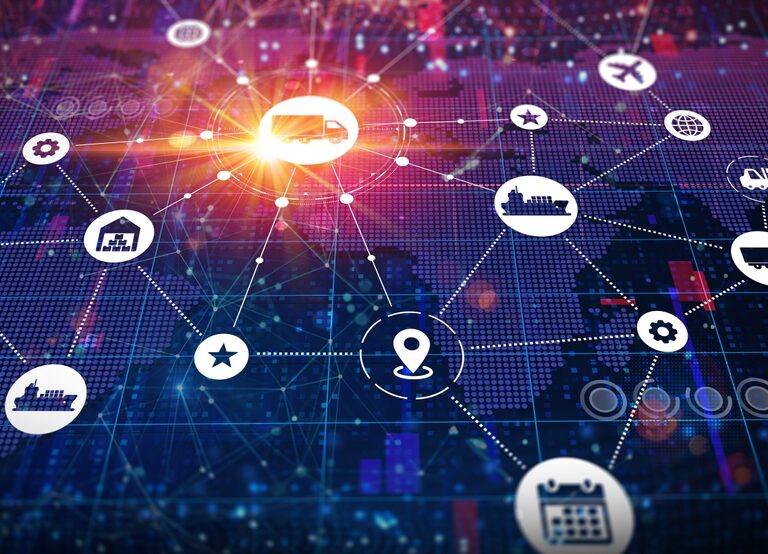
7 Supply Chain Planning Strategies to Reduce Waste on Low-Volume Products
Efficient management of slow-moving SKUs can reduce waste, optimize inventory and boost profitability. Learn more supply chain planning strategies.
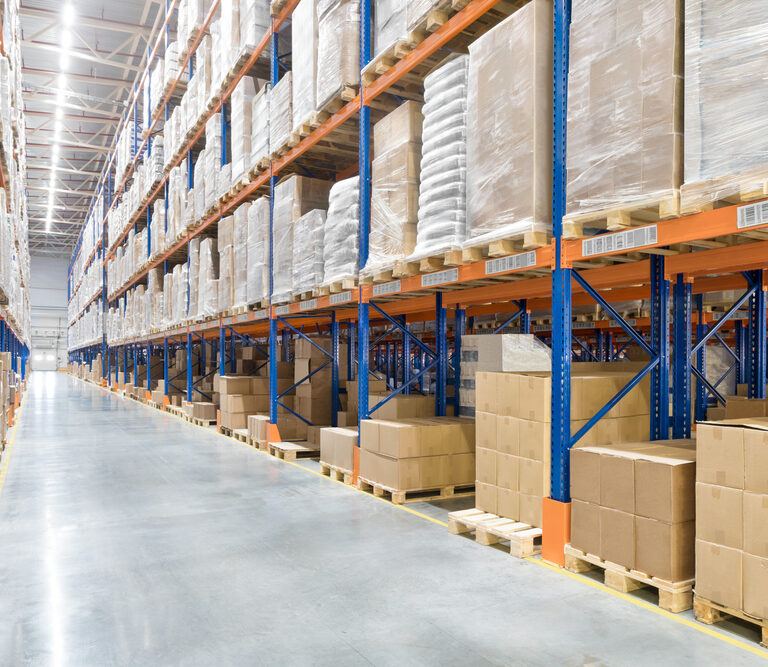
Increase ROI Through Successful Warehouse Slotting
A well-thought-out slotting strategy also enables businesses to minimize wasted space and maximize storage capacity within the warehouse. Increase ROI using the right tools, strategy and management plan with successful warehouse slotting.
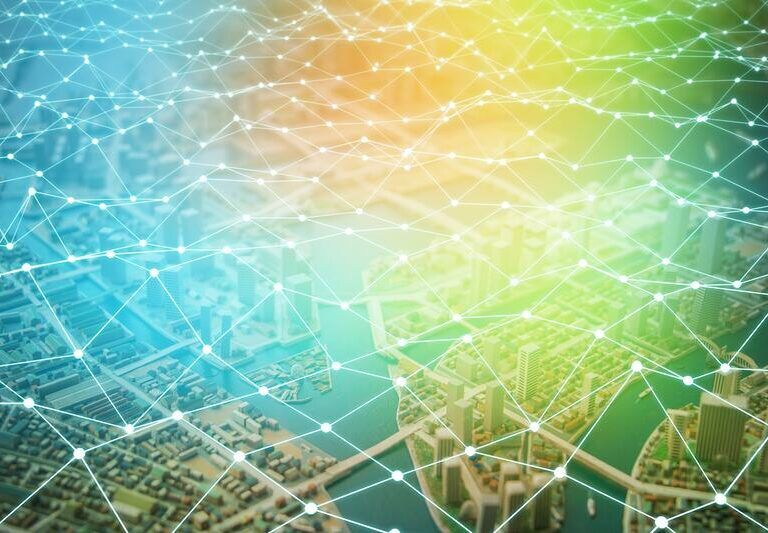
What Is Supply Chain Strategy? Developing and Optimizing Your Supply Chain Network
Learn the basics of supply chain strategy, the role it plays and the benefits an optimized strategy can have on your business.
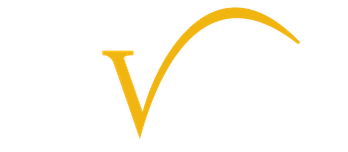
- 877-684-7700
Subscribe to Our Insights
About envista.
- Company Overview
- Cookie Policy
- Privacy Policy
- Privacy Notice for CA Residents
- Terms of Use
We support your right to privacy and transparency about how we collect and use your personal data.
Privacy overview.
Cookie | Duration | Description |
---|---|---|
__cfruid | session | Cloudflare sets this cookie to identify trusted web traffic. |
cookielawinfo-checkbox-advertisement | 1 year | This cookie is set by the GDPR Cookie Consent plugin to record the user consent for the cookies in the "Advertisement" category. |
cookielawinfo-checkbox-analytics | 11 months | This cookie is set by GDPR Cookie Consent plugin to store the user consent for the cookies in the category "Analytics". |
cookielawinfo-checkbox-functional | 11 months | The cookie is set by GDPR cookie consent to record the user consent for the cookies in the category "Functional". |
cookielawinfo-checkbox-necessary | 11 months | This cookie is set by GDPR Cookie Consent plugin to store the user consent for the cookies in the category "Necessary". |
cookielawinfo-checkbox-others | 11 months | This cookie is set by GDPR Cookie Consent plugin to store the user consent for the cookies in the category "Other. |
cookielawinfo-checkbox-performance | 11 months | This cookie is set by GDPR Cookie Consent plugin to store the user consent for the cookies in the category "Performance". |
elementor | never | This cookie is used by the website's WordPress theme. It allows the website owner to implement or change the website's content in real-time. |
viewed_cookie_policy | 11 months | The cookie is set by the GDPR Cookie Consent plugin to store whether or not user has consented to the use of cookies. It does not store any personal data. |
Cookie | Duration | Description |
---|---|---|
__cf_bm | 30 minutes | This cookie is set by Cloudflare to support Cloudflare Bot Management. |
__hssc | 30 minutes | This cookie is set by HubSpot to keep track of sessions and to determine if HubSpot should increment the session number and timestamps in the __hstc cookie. |
bcookie | 2 years | This cookie is set by LinkedIn, from LinkedIn share buttons and ad tags, to recognize browser ID. |
lang | session | This cookie is used to store the language preferences of a user to serve up content in that stored language the next time user visit the website. |
lidc | 1 day | This cookie is set by LinkedIn to facilitate data center selection. |
SnapABugHistory | 1 year | This cookie is set by the provider SnapEngage, a live chat software, for recording the landing page and origin of the visitor. |
SnapABugRef | 2 hours | This cookie is set by the provider SnapEngage, a live chat software, for recording the landing page and origin of the visitor. |
SnapABugUserAlias | 1 year | This cookie is set by the provider SnapEngage for our website's live chat functionality and is used for sending alias to chat agent and update the chat case. |
SnapABugVisit | session | This cookie is set by the provider SnapEngage, a live chat software, for identifying a new user session. |
Cookie | Duration | Description |
---|---|---|
__hssrc | session | This cookie is set by Hubspot whenever it changes the session cookie; if it is set to 1 it indicates that the user has restarted the browser, and if the cookie does not exist, it is assumed to be a new session. |
_ga | 2 years | This cookie is set by Google Analytics to calculate visitor, session and campaign data and keep track of site usage for our website's analytics report. The cookie stores information anonymously and assigns a randomly generated number to recognize unique visitors. |
_gat_gtag_UA_4433982_2 | 1 minute | This cookie is set by Google to distinguish users. |
_gid | 1 day | Installed by Google Analytics, _gid cookie stores information on how visitors use a website, while also creating an analytics report of the website's performance. Some of the data that are collected include the number of visitors, their source, and the pages they visit anonymously. |
_uetsid | 1 day | This cookie is used to collect analytical information about how users use our website. This information is used to compile report and improve site. |
AnalyticsSyncHistory | 1 month | This cookie is used by LinkedIn to store information about the time a sync took place with the lms_analytics cookie. |
Cookie | Duration | Description |
---|---|---|
__hstc | 1 year 24 days | This is the main cookie set by Hubspot for tracking visitors to our website and contains the domain, initial timestamp (first visit), last timestamp (last visit), current timestamp (this visit), and session number (increments for each subsequent session). |
_gcl_au | 3 months | This cookie is set by Google Tag Manager to experiment advertisement efficiency of our website. |
_uetvid | 1 year 24 days | This cookie is used by Microsoft Bing to store and track users across visits to our website in order to engage with them based on past visits. |
bscookie | 2 years | This cookie is a browser ID cookie set by Linked share Buttons and ad tags. |
d-a8e6 | 1 year | This cookie is set by Terminus and is used to track website user devices. |
hubspotutk | 1 year 24 days | This cookie is used by HubSpot to keep track of the visitors to our website and is passed to Hubspot on form submission and used when deduplicating contacts. |
IDE | 1 year 24 days | This cookie is used by Google to store information about how users use our website to present them with relevant ads and according to the user profile. |
MUID | 1 year 24 days | This cookie is set by Bing to recognize unique web browsers visiting Microsoft sites and is used for advertising, site analytics, and other operations. |
s-9da4 | 15 minutes | This cookie is set by Terminus and is used to track website user sessions. |
TDCPM | 1 year | TDCPM cookie is set by Cloudflare service to store a unique ID that identifies a returning user's device which is then used for targeted advertising. |
TDID | 1 year | TDID cookie is set by Cloudflare service to store a unique ID that identifies a returning user's device which is then used for targeted advertising. |
test_cookie | 15 minutes | This cookie is set by doubleclick.net to determine if the user's browser supports cookies. |
UserMatchHistory | 1 month | This cookie is used by Linkedin to track visitors on multiple websites, in order to present relevant advertisement based on the visitor's preferences. |
visitorId | 1 year | This cookie is used by ZoomInfo to enhance user information. |
Cookie | Duration | Description |
---|---|---|
li_gc | 2 years | This cookie is used to store consent of guests regarding the use of cookies for non-essential purposes. |
Contact enVista
We and our partners use cookies to give you the best online experience, including to personalize content, advertising, and web analytics. You can reject cookies by changing your browser settings. To learn more about the cookies we use see our Cookie Policy .
- Supply Chains
- Manufacturing
- Transportation
- Warehouse Operations
- Rail Logistics
- Ports & Terminals
- Road Traffic
- Passenger Terminals
- Business Processes
- Asset Management
- Social Processes
- Why simulation
- AnyLogic Timeline
- Artificial Intelligence
- Digital Twin
- Enterprise Simulation
- Get started
- White papers
Case studies
- Training and events
- AnyLogic Conference
- Documentation
- For academia
- Academic articles
- Clients & Testimonials
- --> Supply Chains
- --> Manufacturing
- --> Transportation
- --> Warehouse Operations
- --> Rail Logistics
- --> Oil & Gas
- --> Ports & Terminals
- --> Road Traffic
- --> Passenger Terminals
- --> Healthcare
- --> Business Processes
- --> Asset Management
- --> Marketing
- --> Social Processes
- --> Defense
Walmart’s Alphabot: Designing Material Handling System with Simulation
Walmart, the world’s largest retailer by revenue, was looking for an automation technology that would help complete orders faster and at a lower cost in the company’s fast-growing online grocery business. They wanted to evaluate Alert Innovation’s Goods-to-Person (GTP) concept, Alphabot (an AGV or robot-based system), which could automate the grocery pickup process by using autonomous mobile carts capable of operating in all three dimensions within a multilevel storage structure.
Optimizing E-Commerce Warehouse Operations
The global e-commerce sector has seen 320% growth in five years, and demand is increasing following the COVID-19 pandemic. To reduce costs and remain competitive, DHL Supply Chain ran a warehouse operations optimization project. The project involved developing a smart and robust warehouse simulation tool for testing wave picking strategies.
Optimizing Warehouse Operations for Pharmaceutical Distribution Company
Cardinal Health, a billion-dollar pharmaceutical distribution and logistics firm, manages multiple products from brand name pharmaceuticals and generic drugs to over the counter drugs, health & beauty items and their own private label. They face a multitude of typical distribution warehouse challenges that are further complicated by the nature of pharmaceutical products. Brian Heath, Director of Advanced Analytics at Cardinal Health, and an experienced user of AnyLogic software, employed agent based modeling to solve various business problems, saving Cardinal Health over $3 Million annually.
Warehouse Simulation for Choosing Optimal Picking Algorithm
Kuehne+Nagel, a leading global provider of logistics solutions, was involved in planning a new warehouse for one of their clients. The warehouse would process 13K order lines or 750 picking cartons per day. The project included the development of the best algorithm for multi-order picking. It was planned that the orders in the warehouse would be served by workers with trolleys (or fangos). Workers with trolleys would pick the goods and put them in cartons by order.
Warehouse Cluster Pick Optimization
How DHL optimized warehouse order picking and improved efficiency. Analysis using simulation-based modeling increased picking speed and reducing order completion times. The tool integrates with warehouse management systems.
Developing a Forecasting Simulation Model for Efficient Warehouse Operations
A warehouse in Thailand was encountering difficulties because of a number of complicated processes involved in their logistics and storage systems. In order to overcome these and achieve more efficient warehouse operations, EPIC InnoLabs was contracted to develop a forecasting simulation model. This model would be used to predict system behavior based on a number of inputs as well as retrieve the expected values of selected KPIs.
Large-Scale Logistics Network Planning and Optimization
For a delivery network processing 15 billion parcels annually, simulation modeling provided significant saving across key metrics in a package easily accessible to all stakeholders. Find out how in this case study and presentation from Pitney Bowes.
Creating a Workforce Optimization Model for a Micro-Fulfillment Center
Micro-fulfillment centers are small, sometimes highly automated facilities that can fulfill online orders for delivery as well as click-and-collect in-store pickups. They use a combination of automated picking technology and manual picking. Dematic wanted to create a workforce optimization model that they would be able to present to retailers. It would help them understand the staffing required to operate their micro-fulfillment centers and how different scenarios could impact their ability to fulfill orders.
Evaluating Introduction of Warehouse Automation Systems
Symbotic is a warehouse automation solutions provider. Its systems are based on mobile robots that can travel freely throughout a dense storage structure, accessing products in all locations and handling them at a very high throughput rate. The company needed a tool to help their customers learn the impact of warehouse reorganization and compare capital investments against expected operational savings before the actual introduction of automation systems.
Cold Store Warehouse Operations Optimization
Phoenix Analytics is a Turkish consulting company and provider of simulation solutions for various industries. They were involved in developing a warehouse optimization project for one of the biggest ice-cream and frozen desserts manufacturers in Europe and Asia.
Get a brochure with industry case studies
- Back to Blog
5 Case Studies on Warehouse Management System (WMS) Implementations
Commonly, we study the success stories of others to get inspiration and find new ideas for improving our business or personal efficiency. As a custom WMS development partner, we at HQSofware, also follow best practices and trends to deliver top-notch solutions to our clients. However, based on our WMS development experience, we can already share our own examples of winning warehouse management systems.
In this article, we’ll take a look at 5 successful examples of WMS software to understand how to implement such a system to enhance warehouse productivity.
What is a Custom WMS?
Developing an e-3pl system for warehouse automation, implementing predictive analytics for smart inventory management, providing warehouse navigation to speed up order picking, improving supply management with a wms, developing a wms module to boost marketplace operations, how to maximize wms efficiency.
A warehouse management system (WMS) is a powerful tool that optimizes and streamlines warehouse operations, including inventory management, picking and packing processes, shipping management, etc. A custom WMS, designed according to your unique workflow, eliminates unnecessary features and offers a user-friendly interface. With custom WMS development , you can prioritize factors that are crucial for your organization, ensuring that the system aligns perfectly with your unique business needs.
Let’s take a look at some custom WMS examples and how they’ve helped to overcome warehouse challenges for their respective owners.
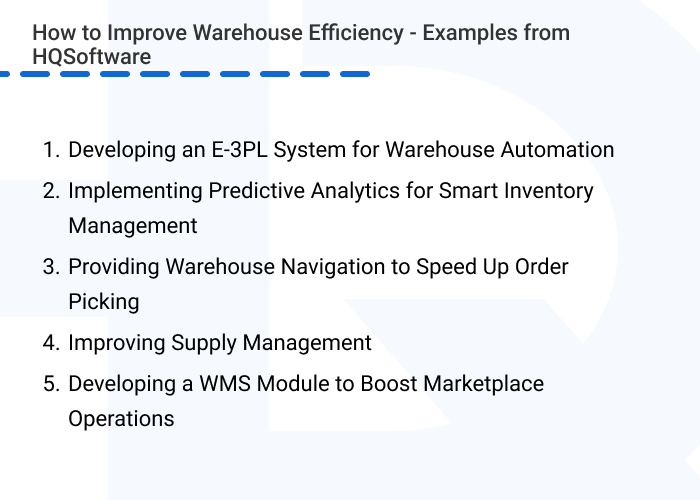
It’s no longer enough for a modern warehouse management system to merely provide inventory visibility and assist in order picking and packing. Companies are now striving to maximize operational efficiency by choosing smart systems with advanced features that can simultaneously address a wide range of issues.
In line with this trend, a US-based startup embarked on the development of comprehensive WMS software that adheres to modern requirements. A large international team of developers, including HQSoftware specialists, was involved in the project.
The main goal was to create an advanced system that can automate and optimize many logistics processes and perform some of them autonomously. For example: automatically generate replenishment orders based on customer demand forecasts, or update goods availability and price for buyers in real-time.
In addition, the system facilitates warehouse audits, provides enhanced navigation, integrates with numerous third-party systems, and enables express picking and receiving. With all its innovative features, the E-3PL platform boasts an impressive 99.9% order accuracy and 99.4% same-day order delivery.
This WMS implementation case study highlights the potential for comprehensive software to enhance virtually any warehouse operation. Achieving this requires a thorough analysis of every process within your warehouse and careful consideration of how advanced technology can drive improvements. This is especially beneficial if you decide to turn to custom WMS software development , as this allows you to build a system that meets your business needs in the best possible way.
Not wasting financial resources and being able to meet changing customer demand are deeply desired by every business and a must-have feature of modern WMS software.
Our client approached us with just such a request. They needed to upgrade a legacy WMS and implement predictive analytics capabilities to optimize warehouse inventory.
To accomplish this, our development team carefully selected the most suitable Machine Learning models capable of analyzing both historical and real-time operational data. The system provides data-driven replenishment recommendations tailored to specific parameters such as supplier delivery terms and minimum stock quantities. As a result, the client was able to reduce inventory costs by 15%.
The power of predictive analytics lies in its ability to learn and adapt to your unique business characteristics, offering personalized recommendations on how to improve it. So, you can benefit from optimal stock levels, excess-cost elimination, efficient space utilization, and a proactive response to customer needs, gaining a strong competitive edge in the market.
Since goods in a warehouse are not arranged as in a supermarket but are stored in boxes with numerical location identifiers, finding the right item can be a daunting task for pickers.
To address this WMS challenge and streamline order picking, our client — a retail company from Germany — decided to implement enhanced warehouse navigation . The feature creates optimized picking routes according to the picker and other items’ location and warehouse configuration.
The solution is delivered as a cross-platform mobile app that provides a map with a picking route and offers voice and visual guidance. With the app, pickers now spend 25% less time on order picking .
Even if you have many large warehouses with different layouts, this is no reason to overlook such a feature. Our developers can create an intuitive graphical interface that allows you to create any warehouse layout, as was implemented in this WMS case study.
Want to create a WMS solution to improve your warehouse operations? We’re ready to help! HQSoftware has a team of skilled professionals ready to tackle the project. Let’s talk! Anna Halias Business Development Manager Get a Free Quote
In an ideal world, all suppliers would have compatible systems that seamlessly integrate with your WMS. However, in reality, you may encounter scenarios where a vendor relies on Google Spreadsheets for inventory tracking or where having a large number of suppliers makes collaboration within a single WMS challenging.
Well, we know several examples of WMSs that include a separate platform for onboarding and communicating with suppliers. We’ve developed such a platform as well . It enables a US retailer to connect with all suppliers in a single interface. Here, suppliers can upload product catalogs, manage item availability, and set prices, while the customer can place purchase orders and establish collaborative agreements.
An important feature of this platform is its ability to handle various data formats, enabling suppliers to post catalogs in their preferred format, which was quite a challenge for our development team. We also ensured system scalability, enabling the customer to expand their network of suppliers.
With this platform, the customer now enjoys seamless order placement, improved supply management, and a 37% reduction in product delivery delays.
The process of publishing and updating items on a single marketplace is relatively straightforward. You fill out the product details, add images, and configure display settings. This is true for several products or catalogs hosted on a single platform. But when you’re a 3PL provider responsible for hosting hundreds of clients with thousands of items on multiple marketplaces, it’s more like a nightmare.
Therefore, for one of the 3PL providers, the HQSoftware team has developed a module for the company’s custom supply chain software system that can automatically publish and update catalogs on several marketplaces and allows for manual item updates within one interface. By synchronizing with the customer’s system, the module ensures consistent and accurate data across platforms.
Within the module, the customer can also customize the display of different products according to specific parameters, such as particular display times, different prices for different times of the day, etc. With robust data exchange mechanisms implemented by our team, the module seamlessly uploads files with all data, speeding up product management tasks by 30%.
Even if you’re not a 3PL provider, such a feature can greatly simplify marketplace management. You no longer have to manually navigate through each product listing on every platform to make changes. All this can be done with a few clicks through a user-friendly interface.
Based on the expertise we’ve gained from our WMS implementation case studies, we understand that leveraging the advantages of WMS software takes more than simply finding or developing a suitable system. It’s also important to focus on proper WMS implementation . Consider the following actions.
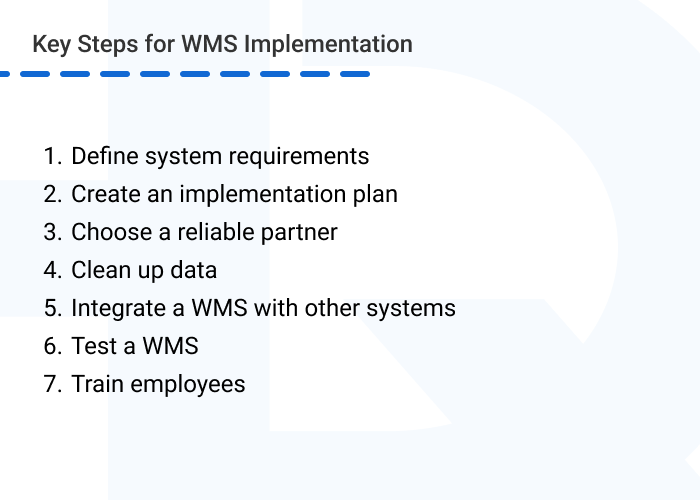
- Define system requirements . Conduct a thorough analysis of your warehouse operations to understand how a new system can automate and improve established processes. This analysis will help you define the specific requirements for your WMS.
- Create an implementation plan. The step-by-step plan will help you overview the whole cycle of WMS implementation and control the progress. A common WMS implementation project plan example includes several key phases, starting with planning, then analysis, then implementation, testing, training, and finally, deployment.
- Clean up data. It’s a good idea to get rid of outdated or duplicate information that can lead to errors and slow down the process of migrating data to the new WMS.
- Integrate a WMS with other systems. This greatly enriches WMS functionality and allows you to get valuable insights from both internal and external platforms.
- Test a WMS. Verify that the system can process all your data smoothly without any interruptions or delays. It is important to test the system’s interaction with third-party systems and ensure it meets the needs of end-users.
- Train employees. Comprehensive training ensures that your employees know how to use the system effectively and helps overcome potential resistance to change. Create visual and interactive manuals and step-by-step tutorials that employees can refer to when they encounter difficulties.
But one of the most important factors in successfully implementing a WMS is choosing a reliable and trusted WMS provider, especially if you opt for a custom WMS. The capabilities of your system and its successful implementation will depend directly on the expertise of your development partner.
At HQSoftware, we have extensive experience not only in creating comprehensive WMS systems but also in working with cutting-edge technologies that can enhance WMS functionality, such as Artificial Intelligence , Machine Learning , IoT , etc. Contact us to learn more about our WMS development services.
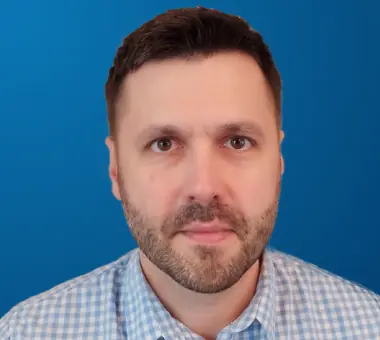
Head of Production
To ensure the outstanding quality of HQSoftware’s solutions and services, I took the position of Head of Production and manager of the Quality Assurance department. Turn to me with any questions regarding our tech expertise.
Related Posts
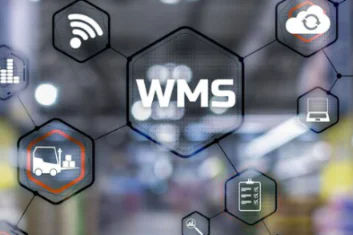
Your Name *
Your Email *
How Can We Help You? *
* Required Fields
Attach File
NDA required
I accept your privacy policy *
We are open to seeing your business needs and determining the best solution. Complete this form, and receive a free personalized proposal from your dedicated manager.
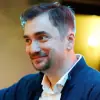
Sergei Vardomatski
We use cookies to analyze traffic, personalize site content, and for social media features. We share this data with our ad and social media partners. You can change your cookie settings and learn more here. By browsing the website you consent to our rules.

Facilities Management Advisor
Practical Facilities Tips, News & Advice.
Design and Construction, Human Resources, Sustainability/Business Continuity
Amazon: a case study in how strategic warehouse placement can drastically reduce shipping times.
Updated: Apr 27, 2022
Few businesses can compete with Amazon—not just as a retailer, but also in shipping, data management, and even warehousing. To become the juggernaut it is today, Amazon has evolved to provide many of its necessary service needs.
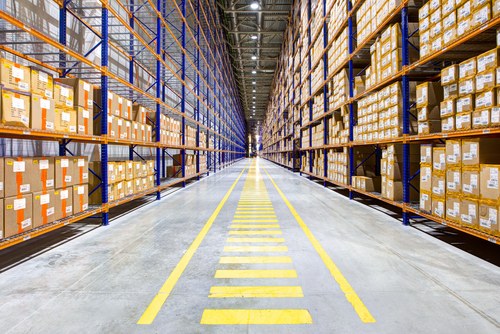
For its warehousing needs alone, for example, Amazon reportedly owns nearly 319 million square feet of fulfillment center floor space in the United States. Though that is a massive number, consider that Amazon’s warehouse placement is designed to keep shipping times as low as possible. In other words, Amazon warehouses have been strategically placed all over the country.
Strategic warehousing allows Amazon to ensure that goods are already nearby when a customer places an order. It also enables the company to focus on efficiency and cost-effectiveness for shipping. This is how Amazon can offer free next-day or two-day shipping.
With these facts in mind, let’s look at how strategic warehouse placement can help other companies reduce their shipping times.
Less Time on the Road
Transportation occupations are some of the most dangerous jobs . In 2018 alone, workers’ injuries and illnesses in transportation and material moving accounted for 20% of all injuries. These statistics also include related transportation roles, such as mechanics and transport-related warehouse jobs.
Strategic warehouse placement reduces the time that trucks and other transport options need to be used. Shorter travel periods can also decrease the time that vehicles are on the road and, thus, can help with driver fatigue. Furthermore, using strategic warehouse placement in high-volume areas will:
- Ensure the fastest shipping times by decreasing the hindrance of supply bottlenecks.
- Keep high-volume items well-stocked, eliminating unplanned shipments.
- Benefit from courier usage to deliver goods where larger delivery options may struggle (such as residential or historic areas).
Additionally, warehouses built in strategic locations can reduce the load of other warehouses. Not only does this decrease shipping times in the area, but it also increases the efficiency of the once-beleaguered warehouse.
Optimization In, Optimization Out
A strategically placed warehouse is optimized inside and out. Shipping costs and speeds are affected by more than the distance. Without optimized functions and employees, warehouses and shipping will suffer.
No matter the industry, however, warehouse safety is essential. Injured workers won’t be working, and could be costing money. Perhaps more importantly, a poorly managed warehouse will drag down morale, handling speeds, and efficiency. Mistakes will pile up, just like the hazards that surround the workers.
To achieve an optimized and safe warehouse, the following guidelines must be followed:
- Rigid daily protocols, especially around safety, awareness, and internal assistance.
- Incentivize safe efficiency, not bottom-line numbers. Breakneck speed is only temporarily sustainable.
- Storage and organization pipelines must always be adhered to.
- Use optimized scheduling to keep shipping and receiving on different shifts.
Each of the above-mentioned tips not only ensures smooth operations, but also keeps the employees and their safety in mind. Unless the warehouse is entirely automated, optimization must consider the humans within.
Technology and automation should still be used, but focus on systems that work with the human element in mind. Use machine learning and logic-oriented technologies to study your warehouse statistics. Optimize how the team at hand works, instead of forcing them into a “pre-optimized mold.”
In short, if the warehouse and its employees are optimized, then shipping times too will be optimized.
Strategic Location Keeps the Goods Close By
Today’s supply chain management goals are meant to ensure customer satisfaction . Two-day or next-day shipping is no longer a leg up over other services. Rapid shipping is now the expected offering. Larger fleets or faster processing lines alone won’t speed up shipping times if the warehouse is located across the country.
Therefore, strategically placing warehouses ensures that goods are always within your customers’ desired shipping times. Amazon’s vast number of warehouses allow for same-day shipping in some areas. Often, within hours of an online order, the purchased item is at the customer’s door. It doesn’t get much faster than that. This is achieved by the vast amount of strategic square footage Amazon devotes to customer satisfaction.
Of course, not every business can afford millions of feet of storage space. Still, a company can decide where best to locate the storage it can afford. For example, warehouses next to major shipping hubs can take better advantage of increased shipping options. Major metropolitan areas benefit from having warehouses nearby, especially in high-volume areas.
Large metropolitan areas also provide other strategic benefits, including:
- Better access to existing infrastructure.
- A more significant potential labor pool.
- A greater area of serviceable customers, plus the ability to offer reduced shipping times to a major section of customers.
Keeping warehouses close to the manufacturing locations can reduce shipping times on the back end. However, strategically located warehouses next to major shipping hubs can benefit from nearly the same back-end fulfillment, and provide customers with even quicker delivery times.
Final Thoughts
Warehouses use massive amounts of capital, both in start-up mode and during normal operations. They can be dangerous, especially with a high-velocity mix of employees and machinery. Warehouse use and placement must therefore be strategic to maximize efficiency at all levels. From employee safety to customer satisfaction, where you place a warehouse has long-existing ramifications.
Companies have found success working backward with the customer as the end goal. Strategically located warehouses allow logistics to focus on the fastest route to the customer. Be it extra stock for a high-volume item, or simply shorter shipping times from the warehouse to the customer’s door, warehouse placement is critical.
Rachel Perez is an Outreach Associate with North Star Inbound and wrote this piece working in tandem with BigRentz . An honors graduate of New York University, she is passionate about writing about business, e-commerce, construction, and travel. When not writing, she enjoys spending time in the Florida sunshine.
Leave a Reply Cancel reply
Your email address will not be published. Required fields are marked *
Save my name, email, and website in this browser for the next time I comment.
- Tech Insights
- Careers Insights
- Careers @ Zenkins
- Careers Portal
- Custom Software Development
- Web Application Development
- Mobile App Development
- SaaS Product Development
- Enterprise Software Development
- Software Testing and Quality Assurance
- Cloud Integration
- API Development and Integration
- DevOps and CI/CD
- UI/UX Design
- AI and ML Integration
- IoT Software Development
- Digital Transformation
- IT Staff Augmentation
- Data Engineering
- Product Engineering
- IT Consulting
- Platform And Infrastructure
- Manufacturing
- Professional Services
- Transportation & Logistics
- Telecommunications
- Construction
- Travel & Hospitality
- Industry 4.0
- Capital Markets
- Consumer Goods & Distribution
- Communications, Media & Information Services
- Energy, Resources & Utilities
- Life Sciences
- Public Services
- Frontend Development
- Backend Development
- Full-Stack Development
- Cloud & DevOps
- UI/UX & Design
- Quality Assurance & Testing
- Enterprise Solutions
- Specialized Roles
- ASP.NET Developers
- Blazor Developers
- C# Developers
- WPF Developers
- WinForms Developers
- VB.NET Developers
- Angular Developers
- React.js Developers
- Vue.js Developers
- HTML CSS Developers
- .NET Developers
- .NET Core Developers
- Azure Developers
- SQL Server Developers
- SharePoint Developers
- Entity Framework Developers
- WCF Developers
- Umbraco CMS Developers
- Full-Stack Developers
- MEAN Stack Developers
- MERN Stack Developers
- Xamarin Developers
- MAUI Developers
- UWP Developers
- Azure DevOps Engineers
- Microsoft Azure Engineers
- Microsoft Cloud Engineers
- Azure Solutions Architects
- Azure Security Engineers
- Azure Data Engineers
- Data Engineers (Microsoft Stack)
- Data Analysts (Microsoft Stack)
- Power BI Consultants
- Machine Learning Engineers (Microsoft Stack)
- AI Developers
- UI/UX Developers
- XAML Developers
- QA Engineers
- Automation Testers
- TestComplete Engineers
- MS Dynamics 365 Developers
- BizTalk Developers
- ServiceNow Developers
- Office 365 Developers
- Microsoft 365 Developers
- RPA Developers (Microsoft Power Automate)
- Azure AI Engineers
- Azure IoT Developers
- .NET Frameworks
- Programming Languages
- Front-End Technologies
- Data & Analytics
- AI & Machine Learning
- API & Integration
- .NET Framework
- ASP.NET Core
- ASP.NET MVC
- ASP.NET Web API
- Entity Framework (EF Core)
- WCF (Windows Communication Foundation)
- WPF (Windows Presentation Foundation)
- WinForms (Windows Forms)
- VB.NET (Visual Basic .NET)
- Microsoft Azure
- Azure DevOps
- Azure Functions
- Azure Logic Apps
- Azure App Services
- Azure Kubernetes Service (AKS)
- Azure Active Directory (AAD)
- Azure Cosmos DB
- Azure SQL Database
- Azure Virtual Machines
- Azure Service Bus
- Azure Key Vault
- Amazon Web Services (AWS)
- AWS EC2 (Elastic Compute Cloud)
- AWS S3 (Simple Storage Service)
- AWS RDS (Relational Database Service)
- AWS DynamoDB
- AWS CloudFormation
- AWS ECS (Elastic Container Service)
- AWS EKS (Elastic Kubernetes Service)
- AWS IAM (Identity and Access Management)
- AWS API Gateway
- AWS Route 53
- Google Cloud Platform (GCP)
- GCP Compute Engine
- GCP App Engine
- GCP Cloud Functions
- GCP Cloud Storage
- GCP BigQuery
- GCP Kubernetes Engine (GKE)
- GCP Cloud Pub/Sub
- GCP Cloud SQL
- GCP Cloud Spanner
- GCP Identity and Access Management (IAM)
- GCP Cloud Run
- JavaScript (ES6+)
- Blazor WebAssembly
- Razor Pages
- SSRS (SQL Server Reporting Services)
- SSIS (SQL Server Integration Services)
- SSAS (SQL Server Analysis Services)
- Azure Synapse Analytics
- Azure Data Lake
- Azure Data Factory
- Apache Hadoop
- Apache Spark
- Apache Kafka
- QlikView/Qlik Sense
- D3.js (Data-Driven Documents)
- Azure Machine Learning
- Azure Cognitive Services
- Azure Bot Service
- RESTful Services
- Azure API Management
- Customized Products
- Case Studies
- Manufacturing Execution System
- Enterprise Resource Planning System
- Deviation Management System
- Customized Product Lifecycle Management (PLM) System
- Customized Work Permit System
- Supervisory Control and Data Acquisition Application: A Case Study
- Product Lifecycle Management System Case Study
- Research Project Management Software: A Case Study
Employee Training Management Software: A Case Study
- Nonprofit Donor Management Software: A Case Study
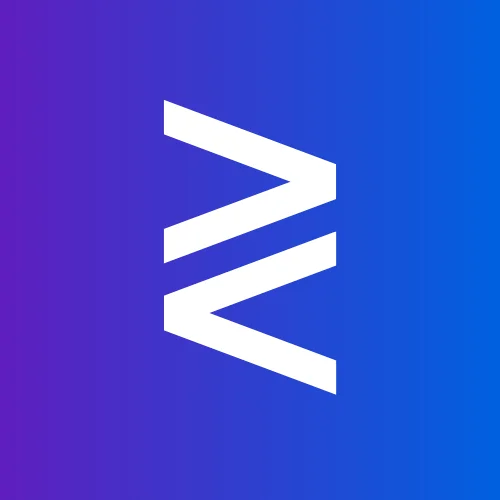
Warehouse Management Software: A Case Study
- Post author: Maryliya M J
- Post published: January 11, 2024
- Reading time: 12 mins read
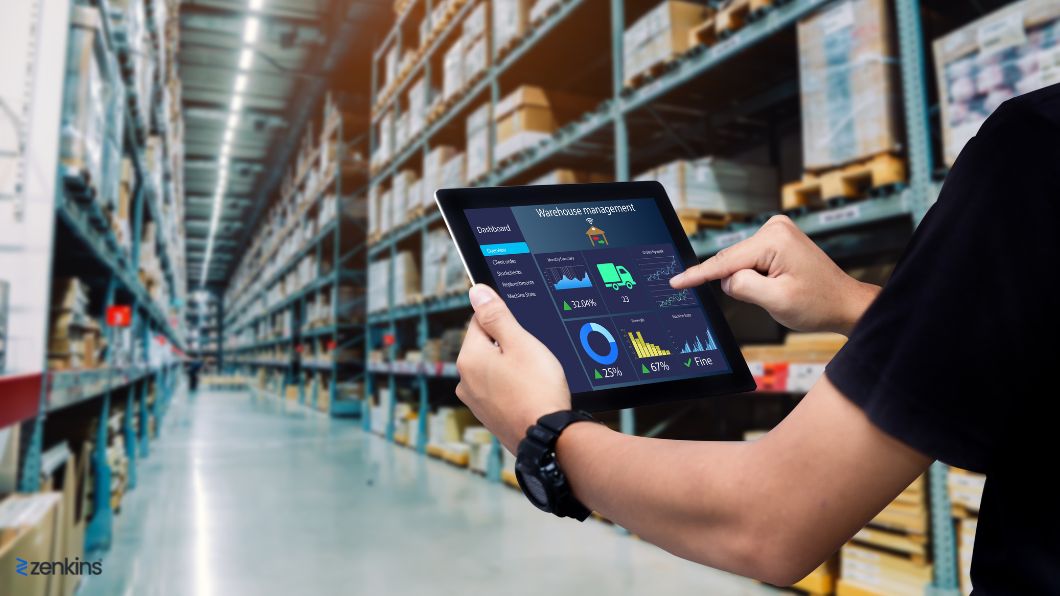
Warehouse Management Software (WMS): A Case Study
Table of contents.
Warehouse management software (WMS) has become an integral tool for modern businesses seeking to optimize their supply chain operations. With the ever-increasing complexity of managing inventory, orders, and logistics, implementing an effective WMS solution can provide significant advantages.
Introduction to Warehouse Management Software (WMS)
Understanding warehouse management systems (wms).
Warehouse Management Software ( WMS ) is like your personal assistant for managing the chaos of a warehouse. It’s a fancy computer program that helps keep track of inventory, streamline processes, and make your life a whole lot easier. Think of it as the Hermione Granger of your warehouse – organized, efficient, and always on top of things.
Evolution and Advancements in WMS
Gone are the days of scribbling inventory numbers on a piece of paper and playing detective to find that missing box of widgets. WMS has come a long way since then. It has evolved from simple spreadsheets to sophisticated systems that can handle complex tasks like inventory tracking, order processing, and even automated picking and packing. It’s like upgrading from a flip phone to the latest iPhone – everything just works better.
Benefits of Implementing WMS
Implementing a WMS might sound like a hassle, but trust me, the benefits are totally worth it. With a WMS by your side, you can say goodbye to inventory nightmares, reduce errors, and improve overall efficiency. It’s like having a superpower that makes your warehouse run smoother than a freshly oiled machine. From enhanced inventory visibility to streamlined order fulfillment, WMS has your back.
About the Client
Our client, a prominent e-commerce company, faced challenges in efficiently managing its warehouse operations. With a growing inventory and increasing order volume, they recognized the need for a robust Warehouse Management Software (WMS) to streamline inventory tracking, order fulfillment, and overall warehouse efficiency.
Project Overview
The project involved developing a .NET-based Warehouse Management Software that seamlessly integrated with the client’s existing systems. The primary objectives were to provide real-time visibility into stock levels, automate order processing, and optimize the warehouse layout for improved picking and packing processes.
The Challenges
- Inefficient Inventory Tracking: The existing systems lacked real-time visibility, leading to inaccuracies in inventory tracking.
- Manual Order Processing: Order fulfillment processes were time-consuming and prone to errors due to manual interventions.
- Suboptimal Warehouse Layout: The warehouse layout needed optimization to enhance picking and packing efficiency.
The Solution
Our team, comprising skilled developers and project managers, collaborated to design and implement a comprehensive Warehouse Management Software. Technologies such as .NET, SQL Server, and REST APIs were employed to ensure a robust and scalable solution.
Key Features of the WMS
- Real-time Stock Visibility: The WMS provided instant visibility into stock levels, reducing the risk of stockouts and overstock situations.
- Automated Order Processing: Orders were processed seamlessly, minimizing errors and accelerating the fulfillment process.
- Optimized Warehouse Layout: The software employed intelligent algorithms to optimize the warehouse layout, resulting in improved picking and packing efficiency.
The Outcome
The Warehouse Management Software was successfully deployed, leading to significant improvements in warehouse operations. The client reported enhanced efficiency in inventory management, reduced order processing times, and improved overall warehouse productivity.
By leveraging the benefits of WMS, such as enhanced inventory visibility, streamlined order fulfillment processes, and improved accuracy and efficiency, the company was able to overcome their warehouse management challenges and achieve remarkable results. The lessons learned from this case study provide valuable insights for businesses considering the adoption of WMS, emphasizing the importance of careful selection, thorough implementation planning, and seamless integration with existing systems. Ultimately, the successful implementation of WMS opens doors to increased productivity, cost savings, and improved customer satisfaction, making it a strategic investment for any organization looking to optimize their warehouse operations.
Our team’s expertise in developing a tailored Warehouse Management Software using cutting-edge technologies resulted in a solution that addressed the client’s challenges effectively. The implementation of real-time visibility, automated order processing, and warehouse layout optimization contributed to a more streamlined and efficient warehouse operation.
Are you facing similar challenges in warehouse management? Contact us today to explore how our expertise in WMS development can transform your warehouse operations and drive efficiency.
What is Warehouse Management Software (WMS) and why is it important?
Warehouse Management Software (WMS) is a software solution designed to efficiently manage and control various aspects of warehouse operations, including inventory management, order fulfillment, and logistics. It is important because it helps businesses optimize their warehouse processes, improve inventory accuracy, streamline operations, enhance productivity, and ultimately deliver better customer service.
How does a WMS solution benefit businesses?
A WMS solution offers numerous benefits to businesses. It provides real-time visibility into inventory levels and locations, enabling effective inventory management and reducing stockouts. It automates and streamlines order fulfillment processes, improving speed and accuracy while reducing errors. WMS also optimizes warehouse layout, resource allocation, and workflow, leading to increased operational efficiency, productivity, and cost savings.
What considerations should businesses keep in mind when selecting a WMS solution?
When selecting a WMS solution, businesses should consider factors such as scalability, ease of integration with existing systems, customization options, vendor support, and cost. It is crucial to assess specific business requirements, evaluate the software’s functionality, and determine whether it aligns with the organization’s long-term goals. Conducting thorough research, seeking recommendations, and requesting demos or trials can help make an informed decision.
Is it challenging to integrate WMS with existing systems and processes?
Integrating WMS with existing systems and processes can present challenges, mainly due to differences in data structures, formats, and compatibility. It requires careful planning, data migration, and coordination between the WMS provider and internal IT teams. However, with proper communication, collaboration, and expert guidance, businesses can overcome integration challenges and achieve seamless connectivity between WMS and other enterprise systems.
You Might Also Like
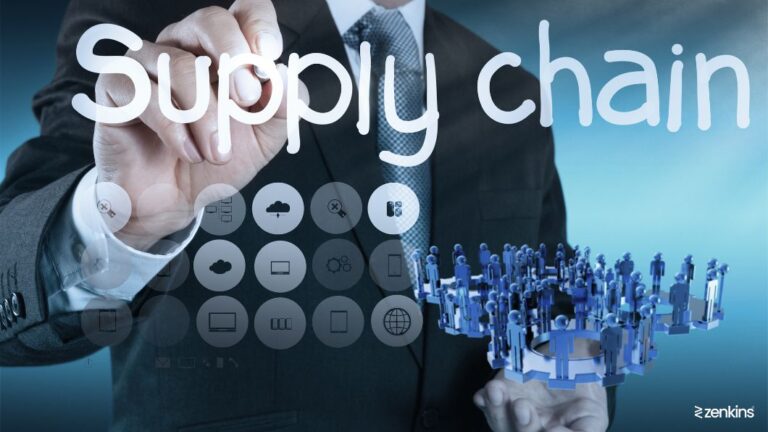
Supply Chain Management Software: A Case Study

Environmental Sustainability Management Software: A Case Study
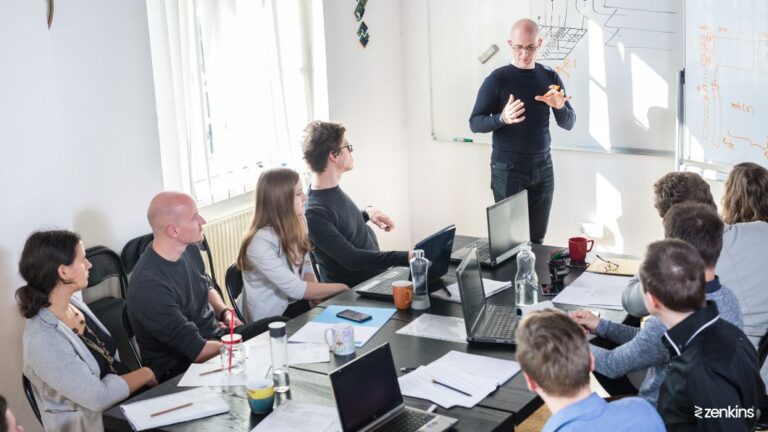
Book A Free Consultation
Tailored Solutions, Expert Advice, and Project Estimates Await.
Expect a Prompt Call from one of our Account Managers.
- Elite IT Professionals
- Time Zone Aligned
- Experienced Team
At Zenkins, we bring together a curated network of elite IT professionals ready to elevate your projects to new heights. From seasoned developers to innovative designers, our handpicked talent pool is here to turn your visions into reality. Experience unparalleled expertise, reliability, and dedication to excellence with our team of Elite IT Professionals.
At Zenkins, we understand the importance of global collaboration. That’s why our team is strategically aligned across time zones, ensuring seamless communication and productivity no matter where you are. From brainstorming sessions to project updates, our time zone-aligned approach guarantees that deadlines are met and progress never stalls. Experience the convenience of working with a team that’s always in sync.
At Zenkins, we pride ourselves on our experienced team of professionals who bring years of industry knowledge and skill to every project. From seasoned developers to seasoned project managers, our team has the expertise to tackle even the most complex challenges. With a proven track record of success, we deliver results that exceed expectations.
+91 70690 18504
[email protected]
Zenkins is a leading software development company based in India, specializing in SAAS Product Development, Digital Transformation, and Product Engineering. With a dedicated team of professionals and a commitment to excellence, we deliver innovative solutions that drive business growth and success. Partner with Zenkins for all your software development needs and experience the difference firsthand.
- Methodologies
- Technologies
- Our Services
- IT Staffing Services
- Software Outsourcing
- .NET Development
- Careers @Zenkins
- Current Openings
- Technology Insights
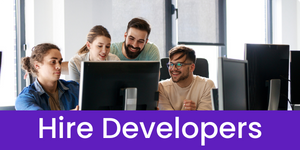
Privacy Overview
Cookie | Duration | Description |
---|---|---|
cookielawinfo-checkbox-analytics | 11 months | This cookie is set by GDPR Cookie Consent plugin. The cookie is used to store the user consent for the cookies in the category "Analytics". |
cookielawinfo-checkbox-functional | 11 months | The cookie is set by GDPR cookie consent to record the user consent for the cookies in the category "Functional". |
cookielawinfo-checkbox-necessary | 11 months | This cookie is set by GDPR Cookie Consent plugin. The cookies is used to store the user consent for the cookies in the category "Necessary". |
cookielawinfo-checkbox-others | 11 months | This cookie is set by GDPR Cookie Consent plugin. The cookie is used to store the user consent for the cookies in the category "Other. |
cookielawinfo-checkbox-performance | 11 months | This cookie is set by GDPR Cookie Consent plugin. The cookie is used to store the user consent for the cookies in the category "Performance". |
viewed_cookie_policy | 11 months | The cookie is set by the GDPR Cookie Consent plugin and is used to store whether or not user has consented to the use of cookies. It does not store any personal data. |
This site uses cookies to improve your experience. By viewing our content, you are accepting the use of cookies. To help us insure we adhere to various privacy regulations, please select your country/region of residence. If you do not select a country we will assume you are from the United States. View our privacy policy and terms of use.
- Materials Handling
- Tracking and Tracing

Flexible Warehousing with Flexe CEO Karl Siebrecht
The Logistics of Logistics
MARCH 24, 2023
Karl Siebrecht and Joe Lynch discuss flexible warehousing , which is exactly what Karl and the Flexe team provides to their customers. Key Takeaways: Flexible Warehousing Karl Siebrecht is the Co-Founder and CEO of Flexe, a company that solves the hardest omnichannel logistics problems for the world’s largest retailers and brands.

Flexible Warehousing Solutions: A Public Goods Case Study
Amware Logistics and Fulfillment
SEPTEMBER 22, 2020
In this article, we’ll showcase Amware's flexible warehousing solutions in helping Public Goods respond to a 500% spike in orders. This is certainly true within the world of logistics, where order volumes – especially those for essential household products – have increased dramatically since March.
This site is protected by reCAPTCHA and the Google Privacy Policy and Terms of Service apply.
- How To Set Up Innovation So That It Aligns With And Enables Corporate Strategy
MORE WEBINARS
Trending Sources
- Supply Chain and Logistics

Warehousing Case Study: JD.COM 3PL Warehouse
Supply Chain Brain
JULY 14, 2024
As the largest retailer in China, JD.COM serves 99% of the country, providing unparalleled same-day and next-day delivery. With approximately 600 million active customers, JD.COM faces costly, inefficient, and labor-intensive operations, compounded by high turnover rates. To address these pain points, JD.COM partnered with ForwardX Robotics.

Case Study: High Ridge Brands Sees 20% Cost Reduction with Integrated Supply Chain Solution
JUNE 30, 2024
HRB looked to ODW Logistics for a supply chain solution, aiming to integrate warehousing and transportation management.
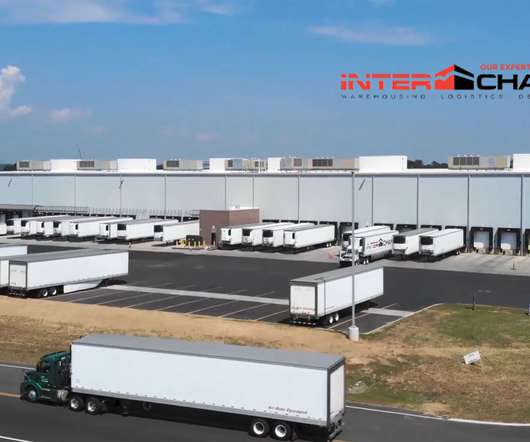
Case Study: InterChange Group
Camelot 3PL Software
NOVEMBER 13, 2020
Background: InterChange Group in Harrisonburg, VA performs cold-storage warehousing and distribution for major U.S. The post Case Study : InterChange Group appeared first on Camelot 3PL Software. food producers and other suppliers around the world.
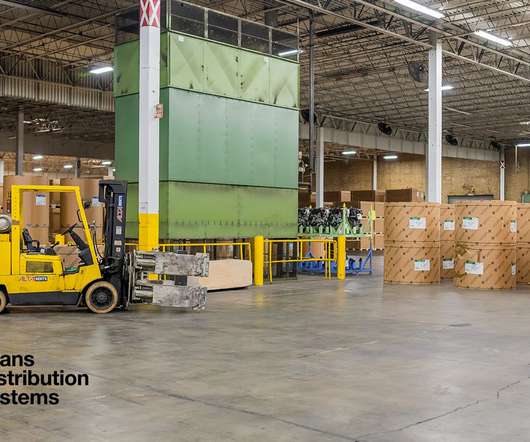
Case Study: Paper Made Easy
3PL Insights
FEBRUARY 23, 2021
Currently, Evans services five paper mill and manufacturers in our warehousing and transportation divisions. The post Case Study : Paper Made Easy appeared first on Evans Distribution Systems. This growth is largely due to rising demand in the pharmaceutical, fast-moving consumer goods and hospitality industries.
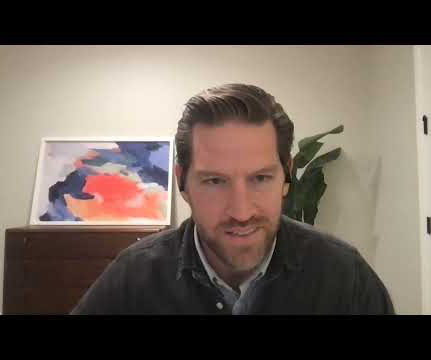
Why Packaging Matters with Phillip Akhzar
FEBRUARY 27, 2023
Arka works with both shippers and warehousing companies. For warehousing companies: Arka automates the packaging ordering process by connecting Arka’s API to the warehouse management system (WMS).
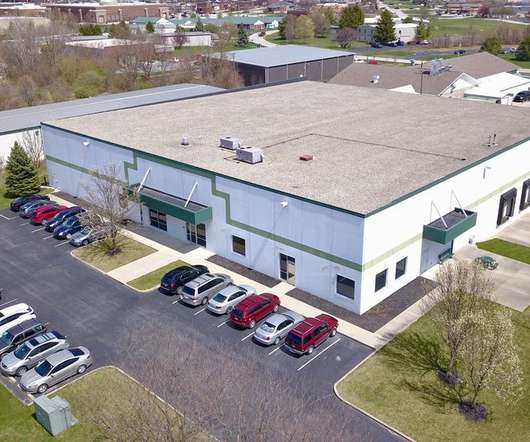
Case Study: The Order Fulfillment Group
AUGUST 12, 2021
Known for its efficiency and quick turnarounds, the third-party logistics provider (3PL) offers comprehensive fulfillment and distribution services that include order entry, accounting, warehousing , and returns receiving to organizations nationwide. The Order Fulfillment Group.
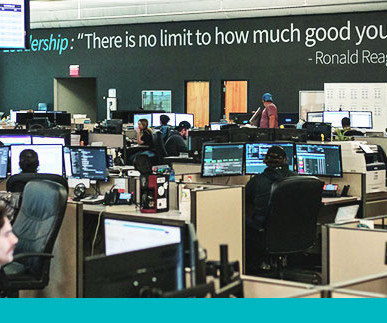
Trinity Logistics Named an Ideal 3PL Partner for Companies Preparing for Growth
Trinity Logistics
JULY 18, 2023
Trinity Logistics has a long history of providing innovative and customer-focused solutions, offering a wide range of services , including warehousing , multiple modes of transportation, technology, and transportation management. Learn how Trinity Logistics helped these companies grow their business.
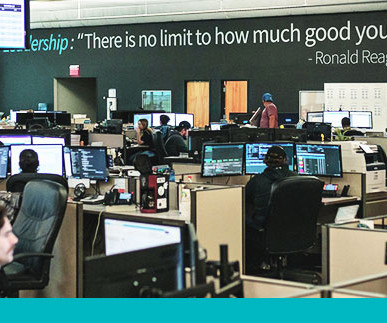
Case Study: The Building of NHS Nightingale
Logistics Business Magazine
APRIL 6, 2020
The post Case Study : The Building of NHS Nightingale appeared first on Logistics Business® Magazine. We’ve all been pushed to the extreme but when the coronavirus pandemic is over, and it will be over at some point, the memory of what was achieved with NHS Nightingale will live on.’.
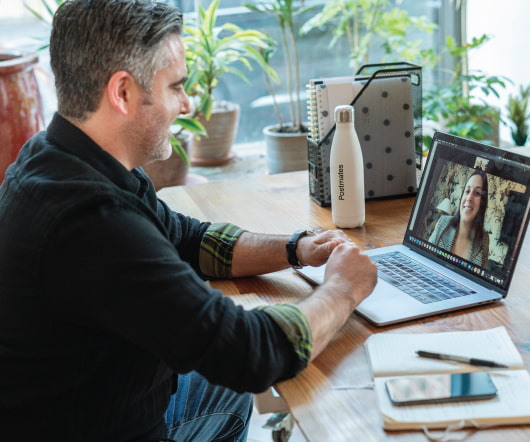
Growing With Hawktree – An Ottawa Logistics Case Study
Ottawa Logistics
NOVEMBER 11, 2016
As a new company with a major retails client with sea container importing requirements and the need for warehousing that is site licensed for medical devices, Hawktree knew they needed a competent and scaleable third party to handle logistics while they focused on sales.
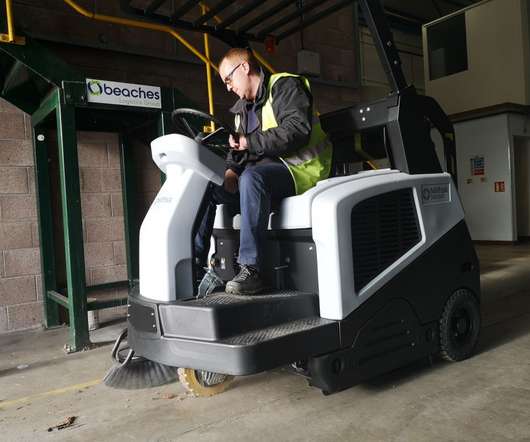
Case Study: How to Keep Your Warehouse Pristine
DECEMBER 9, 2019
The post Case Study : How to Keep Your Warehouse Pristine appeared first on Logistics Business® Magazine. Nilfisk are one of the world’s largest manufacturers of commercial and industrial cleaning equipment. Nilfisk offers a complete and affordable solution to all cleaning challenges.
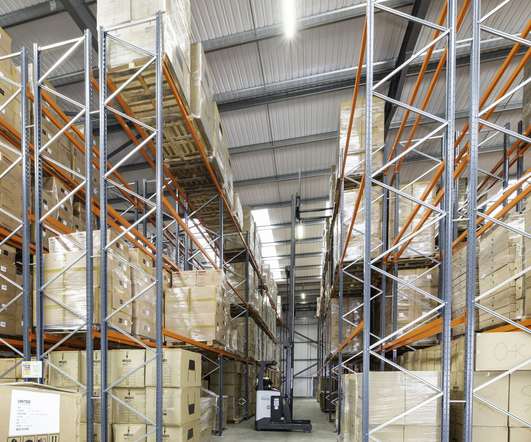
Case Study: Good Day at the Office for System Store Solutions
DECEMBER 11, 2019
This growth has meant change within the business and in July it relocated its warehousing and distribution operation to a brand-new facility in Kempston, Bedfordshire. The post Case Study : Good Day at the Office for System Store Solutions appeared first on Logistics Business® Magazine.
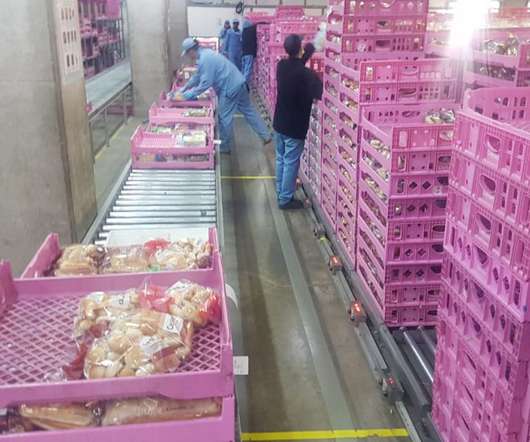
Case Study: From Pick to Shout to Pick to Light
NOVEMBER 26, 2019
“ The post Case Study : From Pick to Shout to Pick to Light appeared first on Logistics Business® Magazine. This does not mean that we have time left over when distributing fresh products, but that we have more time after each wave to prepare for the next wave. As a result, we now have more control over the process.
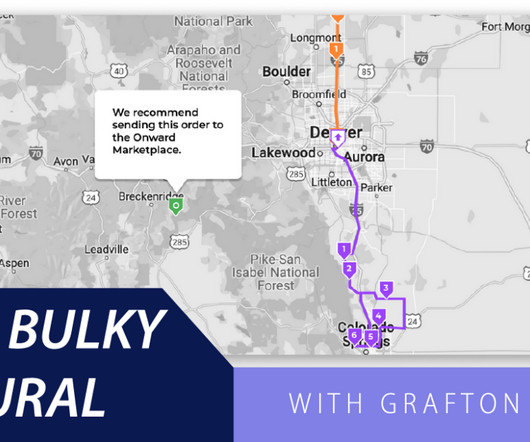
Big, Bulky & Rural with Grafton Elliot
JANUARY 19, 2024
During his time at CDS, Grafton had the opportunity to open and run several final mile warehousing + delivery operations, where he learned from a grassroots level how tough it is to run a big + bulky final mile operation. A nationwide big and bulky brokerage based in Maryland.

Case Study: Helly Hansen opts for UniCarriers once more
OCTOBER 1, 2019
Workwear stocks were warehoused at a separate distribution centre in Sweden until 2011, but they are now stored together with sports clothing at the Born EDC. The post Case Study : Helly Hansen opts for UniCarriers once more appeared first on Logistics Business® Magazine.
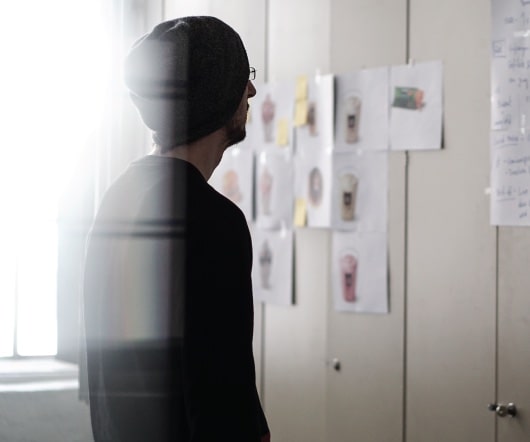
September 2024
AUGUST 16, 2024
The September ’24 issue of Logistics Business magazine : 76 pages of exclusive content spanning the international supply chain and warehousing sector. Plus hard-hitting interviews, site visits and case studies with ABP, Panattoni, Samsara, Dematic, Clark, Goodman, Colliers, Panasonic, Knapp, Mecalux, Daifuku and more.
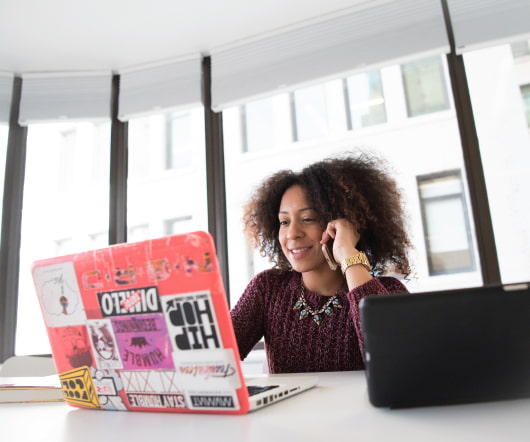
Case Study: Viennese Brewery Uses Fronius Battery Charging
JULY 31, 2019
Back in the summer of 2015, Ottakringer kitted out its subsidiary Trinkservice GmbH (which specialises in warehousing and transport services) with Fronius battery charging systems. The post Case Study : Viennese Brewery Uses Fronius Battery Charging appeared first on Logistics Business® Magazine.
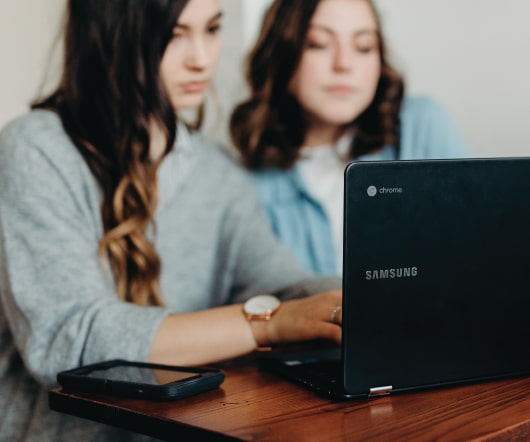
Case Study: New Forklift Generation For Poland Appliance Maker
OCTOBER 17, 2018
We decided on a comprehensive solution which did not focus solely on engineering technology and production related issues, but also on warehousing and logistics,” says Tomas Dohnal, Head of the Investment Department for Mora Moravia. “We are going through a change of production and we are introducing a new generation of products.
MAY 13, 2024
The May ’24 issue of Logistics Business magazine: 76 pages of exclusive content spanning the international supply chain and warehousing sector.
February 2024
FEBRUARY 12, 2024
The February ’24 issue of Logistics Business magazine: 84 pages of exclusive content spanning the international supply chain and warehousing sector. Plus hard-hitting interviews, site visits and case studies with Doddle, FedEx, Red Bull, Koerber, Joloda, Sick, Kardex, Dematic, Inform, Mitsubishi, CMC and Jungheinrich.
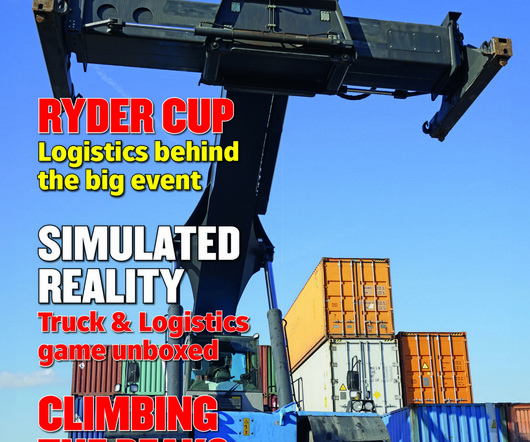
November 2023
NOVEMBER 9, 2023
The November ’23 issue of Logistics Business magazine: 76 pages of exclusive content spanning the international supply chain and warehousing sector.
Case Study: Loading Bay Technology at High-Spec Business Park
DECEMBER 13, 2018
The post Case Study : Loading Bay Technology at High-Spec Business Park appeared first on Logistics Business® Magazine.
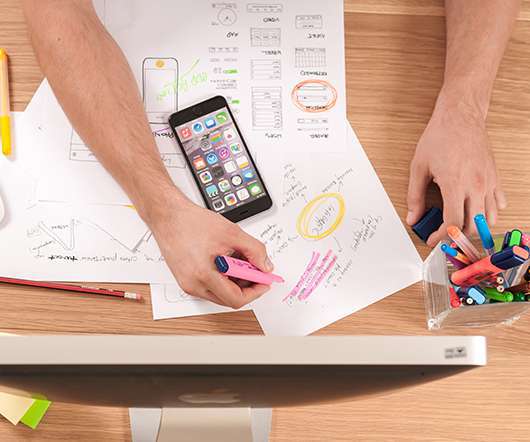
Case Study: Yale and Forkway Enable Stelrad to Radiate Success
JUNE 18, 2018
Forkway is our sole supplier for materials handling equipment and has played a significant role in the development of our warehousing and distribution operation,” said Paul Schofield, Warehouse and Distribution Manager for Stelrad. “At At Stelrad, we have specific needs that require the supply of equipment across a wide range of types.”.
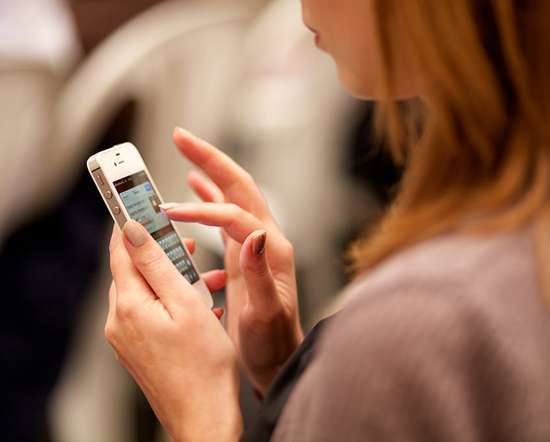
Warehouse Robots Enable a Digital Transformation
Logistics Viewpoints
AUGUST 13, 2018
Because about half of this company’s 2017 revenues are related to warehousing services, several of their digital projects have been related to improving efficiency in their warehouses. This case study describes their approach to testing out mobile logistics robots. A leading MRO began a digital transformation three years ago.
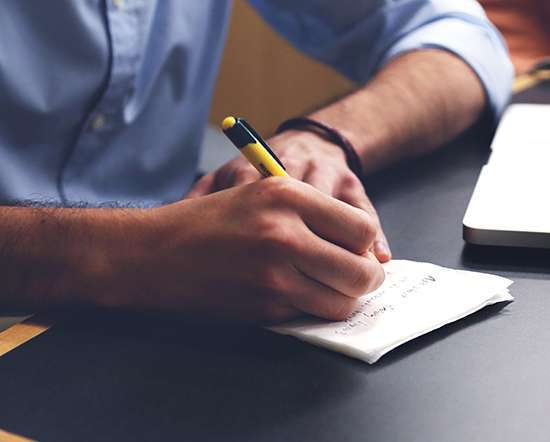
Case Study: Handling the Tough Wood Supply Chain
AUGUST 21, 2018
The post Case Study : Handling the Tough Wood Supply Chain appeared first on Logistics Business® Magazine. “However, by choosing the right trucks and attachments to meet specific needs, wood applications can reduce damage, increase efficiency and achieve a low total cost of ownership.”.
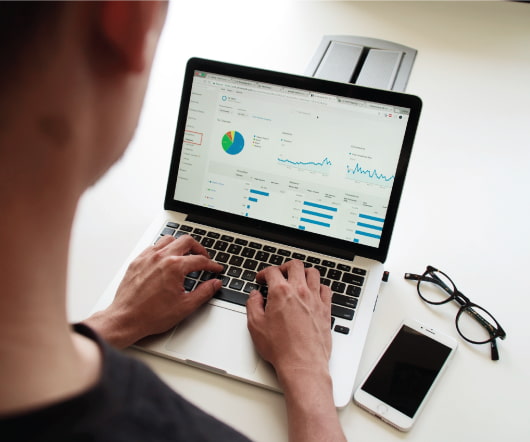
Case Study: It’s a Shoe-in at Skechers EDC
AUGUST 30, 2018
The post Case Study : It’s a Shoe-in at Skechers EDC appeared first on Logistics Business® Magazine. UniCarriers knows our business right down to the tiniest detail and is able to provide us with solid advice on optimising logistics processes.
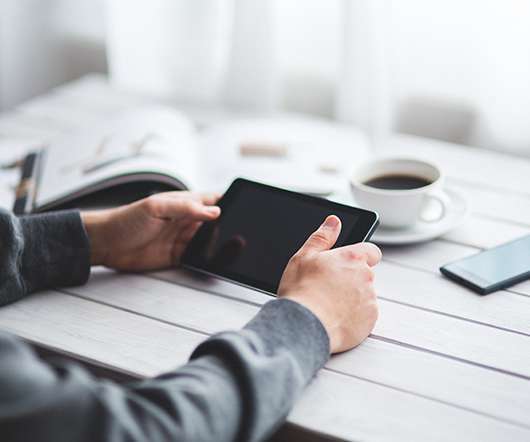
September 2023
AUGUST 21, 2023
The September ’23 issue of Logistics Business magazine: 76 pages of exclusive content spanning the international supply chain and warehousing sector. Big interviews with Directors of Dematic, Transporeon, Fortna, Blue Yonder, Leonardo, Blume, Manhattan Associates, Bowe Group, FATH and Bots&Us.
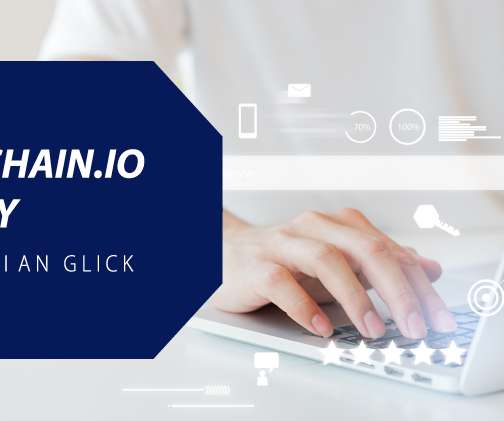
The Chain.io Story with Brian Glick
NOVEMBER 30, 2022
Case Studies . Chain.io’s cloud-based platform solves one of the most challenging puzzles for logistics services providers: rapid integration with thousands of digital tools used by shippers, carriers, and software vendors. Learn More About The Chain.io Brian Glick on LinkedIn. on LinkedIn. on Twitter.
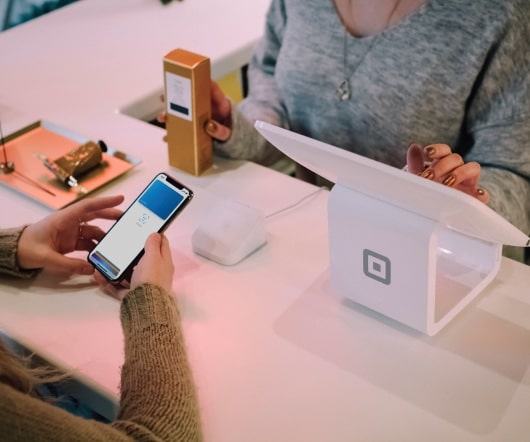
MAY 3, 2023
The May ’23 issue of Logistics Business magazine: 76 pages of exclusive content spanning the international supply chain and warehousing sector. Big interviews with CEOs of Combilift, Honeywell, Redkik insurance, Deposco and stow.
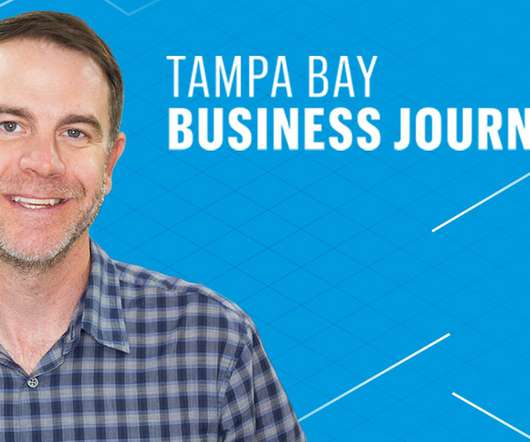
Demand for Goods and Services Remains High In Florida
Blue Grace Logistics
JANUARY 27, 2023
Demand for Goods and Services Remains High In Florida Show Submenu Resources The Logistics Blog® News Press Whitepaper Case Study Webinars Indexes Search Search BlueGrace Logistics Shippers’ demand for trucks may bounce back this year according to a Bank of America.
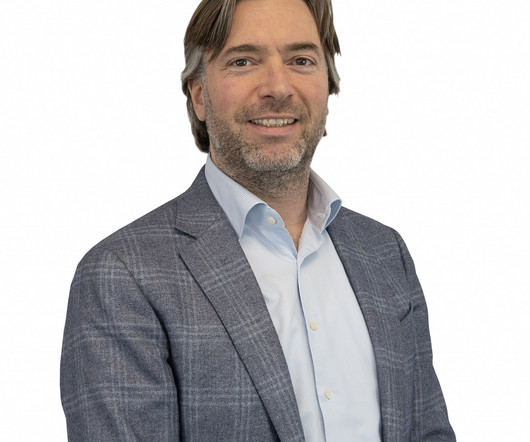
Navigating the Loading Bay’s Hidden Risks
APRIL 26, 2024
When new employees are recruited, warehousing and logistics businesses seem to experience higher than average levels of staff turnover. But a drop in staff numbers combined with higher velocity fulfilment and the resulting demand for larger warehousing and logistics facilities is creating an unsustainable situation. from 2023 to 2030.
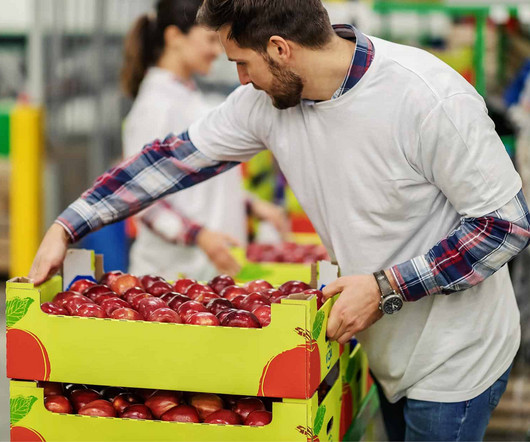
How to Find a Food-Grade Warehouse in Indiana
FW Logsitcs
MAY 25, 2023
For businesses searching for food-grade warehousing specifically, it’s essential to understand the factors that go into finding the perfect facility for their needs, products, and customers. When it comes to choosing a warehouse in Indianapolis, many considerations come into play.
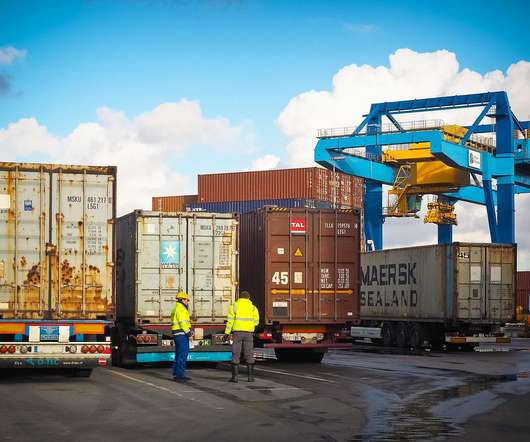
Transloading: A Comprehensive Guide With Client Examples
Dedola Global Logistics
JANUARY 14, 2023
Case Studies : DGL’s Successful Transloading Strategies for Clients in Various Industries. This case study will delve into some of our most notable transloading success stories. This involved taking the container from the port by truck to our nearby warehousing facility, where we loaded the products onto domestic dry vans.
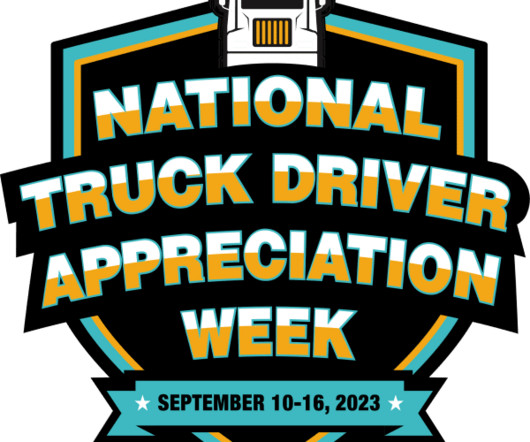
Celebrating North America’s Truck Drivers, One Delivery at a Time
SEPTEMBER 12, 2023
National Truck Driver Appreciation Week Show Submenu Resources The Logistics Blog® Newsroom Whitepaper Case Study Webinars Indexes Search Search Raddy Velkov - September 12, 2023 Celebrating North America’s Truck Drivers, One Delivery at a Time As we celebrate National Truck Driver Appreciation Week Sept.
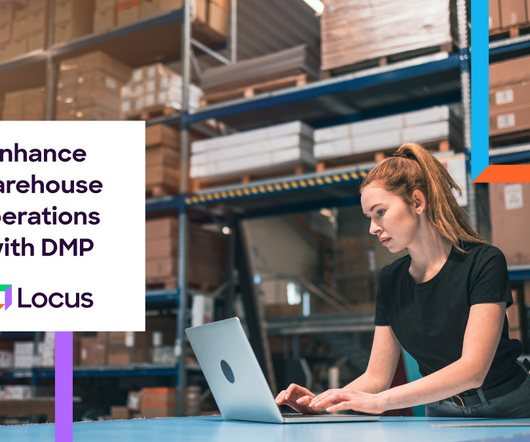
How E-commerce Warehouse Operations can be Optimized with Dispatch Management Software
FEBRUARY 16, 2023
Shipping and logistics are the final steps in warehousing that can be a significant challenge for e-commerce companies, particularly those that sell products internationally. Businesses need to ensure that their warehouses are well-organized, efficient, and well-stocked to meet customer demands.

Driving Growth with Supply Chain Sustainability
Penske Move Ahead
AUGUST 22, 2024
Rethinking Logistics Network Design Before getting into obvious areas such as transportation and warehousing , let’s start at the often-overlooked fundamental: network design. When it comes to supply chains, we think the answer is a resounding yes, and here are a few thoughts on a roadmap to get there. By Andy Moses
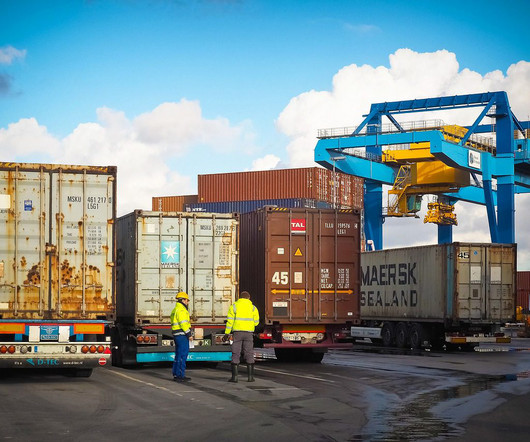
Case Studies : DGL’s Successful Transloading Strategies for Clients in Various Industries As a leading logistics provider, DGL has a wealth of experience in the field of transloading and has helped numerous clients successfully transport their cargo from one mode of transportation to another.
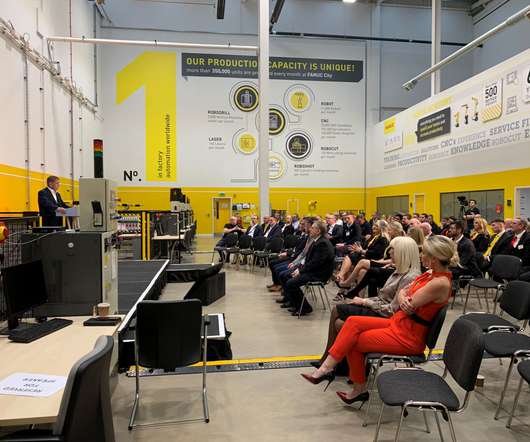
FANUC unveils speakers for Open House event
OCTOBER 28, 2022
and the future of manufacturing, the power of partnerships and the route to net zero in a series of panel discussions, keynote speeches and in-depth case studies across the three-day event aimed at showcasing the benefits of automation to UK manufacturers. Day 1 – The power of partnerships.
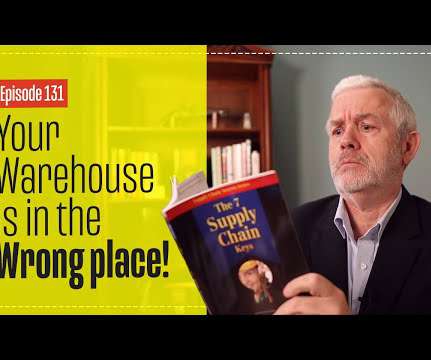
Your Warehouse is in the Wrong Place
Logistics Bureau
OCTOBER 5, 2021
Insource or Outsource Your Warehousing : What Makes Most Sense? Related articles on this topic have appeared throughout our website, check them out: 10 Proven Principles for Best Warehouse Design and Operation. 4 Tips to Help You Choose Distribution Centre Locations. Key Factors to Consider When Planning and Designing Warehouses.

National Forklift Safety Day 2024
JUNE 5, 2024
We will be releasing various resources to support this part of the campaign, including compliance checklists, animation videos, and real-world case studies . The first stage, Prepare, delves into the preparatory steps that should be taken to minimise the chance of a forklift incident becoming a forklift accident.
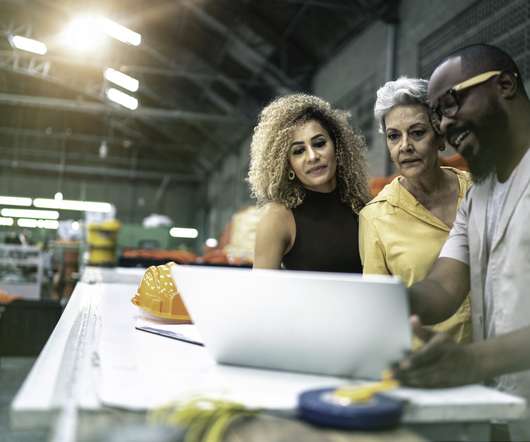
6 Things to Look for in a Third-Party Logistics (3PL) Partner
Now, That's Logistics
NOVEMBER 30, 2021
Integrated with an organization’s warehousing , fulfillment and transportation activities, third-party logistics providers (3PLs) support a wide range of logistics activities for companies across all industries. Can it provide case studies with example success stories working with companies similar to your own, and in your regions of interest?
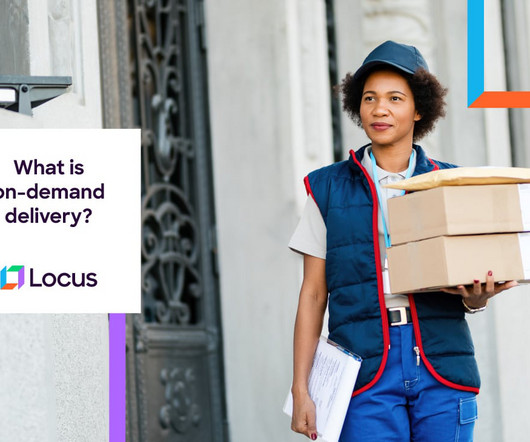
The Ins and Outs of On-Demand Delivery: What It Is and How It Operates
MAY 10, 2023
Read the case study on how to increase visibility for on-demand pharma companies? Download the Case Study Why do logistics providers and consumers prefer on-demand deliveries? After the delivery, customers can provide feedback and rate their experience through the on-demand delivery platform.
Stay Connected
Join 84,000+ Insiders by signing up for our newsletter
- Participate in Logistics Brief
- Add a Source
- Add a Resource
- See All
- 2019 Logistics Brief MVP Awards
- 2020 Logistics Brief MVP Awards
- 2021 Logistics Brief MVP Awards
- 2022 Logistics Brief MVP Awards
- Thu. Sep 12
- Wed. Sep 11
- Tue. Sep 10
- Mon. Sep 09
- Aug 31 - Sep 06
- Supply Chains
- Distribution
- Transportation
- More Topics

Input your email to sign up, or if you already have an account, log in here!
Enter your email address to reset your password. a temporary password will be e‑mailed to you., be in the know on, logistics brief.
Expert insights. Personalized for you.
We organize all of the trending information in your field so you don't have to. Join 84,000+ users and stay up to date on the latest articles your peers are reading.

Get the good stuff
Subscribe to the following Logistics Brief newsletters:
You must accept the Privacy Policy and Terms & Conditions to proceed.

You know about us, now we want to get to know you!
Check your mail, we've sent an email to . please verify that you have received the email..
We have resent the email to
Let's personalize your content
Use social media to find articles.
We can use your profile and the content you share to understand your interests and provide content that is just for you.
Turn this off at any time. Your social media activity always remains private.
Let's get even more personalized
Choose topics that interest you., so, what do you do.
Are you sure you want to cancel your subscriptions?
Cancel my subscriptions
Don't cancel my subscriptions
Changing Country?
Accept terms & conditions.
It looks like you are changing your country/region of residence. In order to receive our emails, you must expressly agree. You can unsubscribe at any time by clicking the unsubscribe link at the bottom of our emails.
You appear to have previously removed your acceptance of the Terms & Conditions.

We noticed that you changed your country/region of residence; congratulations! In order to make this change, you must accept the Aggregage Terms and Conditions and Privacy Policy. Once you've accepted, then you will be able to choose which emails to receive from each site .
You must choose one option
Please choose which emails to receive from each site .
- Update All Sites
- Update Each Site
Please verify your previous choices for all sites
Sites have been updated - click Submit All Changes below to save your changes.
We recognize your account from another site in our network , please click 'Send Email' below to continue with verifying your account and setting a password.
You must accept the Privacy Policy and Terms & Conditions to proceed.
This is not me
Case Studies
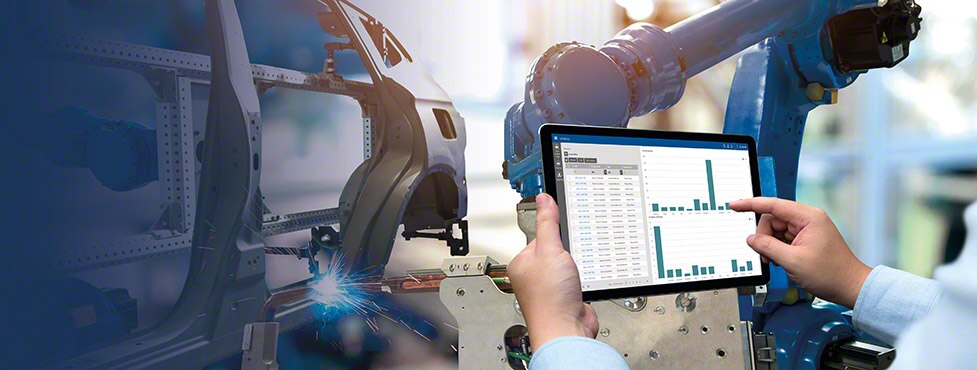
The automotive maker Renault has installed the Easy WMS warehouse management system by Mecalux in its production warehouse in Seville (Spain). The manufacturing centre in this city focuses on the assembly of transmissions and the warehouse supplies manufacturing ...
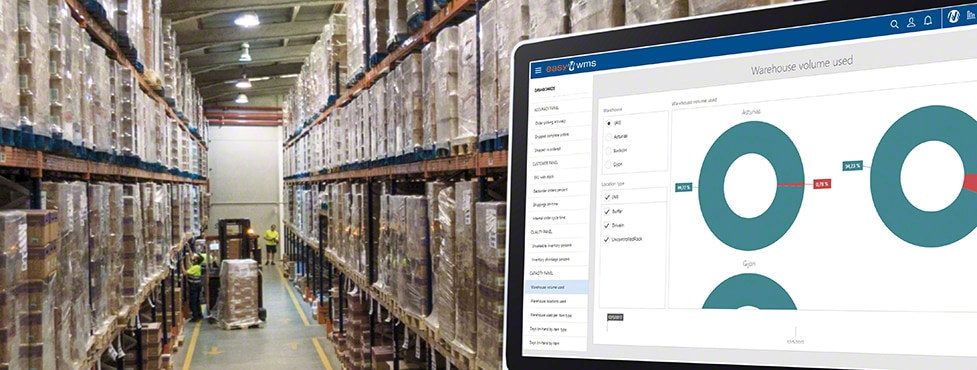
Danone’s distribution centre in Valdemoro (Spain) must cope with a very high-paced daily work rhythm: managing between 500 and 600 SKUs and preparing up to 700 orders. It is an all-in-one omnichannel warehouse, i.e. orders are sent to retailers, wholesalers and c...
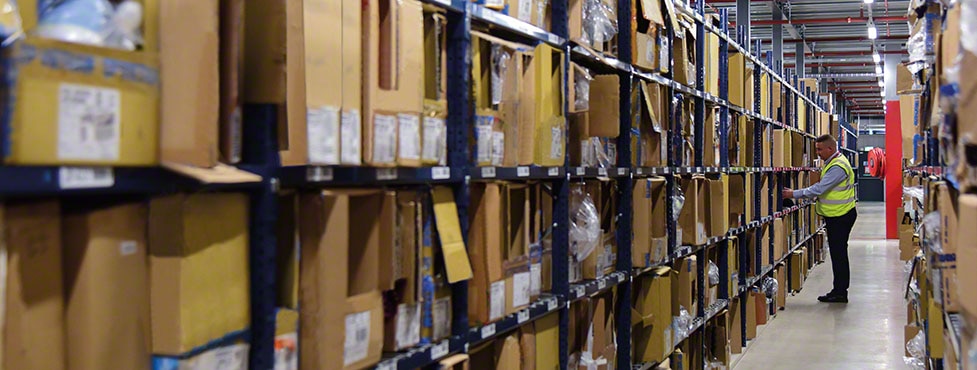
Decathlon has chosen Mecalux’s shelving for picking once again to manage its omnichannel logistics. After equipping its warehouses in France, Germany, Italy and Poland, it is Northampton’s (UK) turn. With 35,000 SKUs, the warehouse preps and ships out 3,000 order...
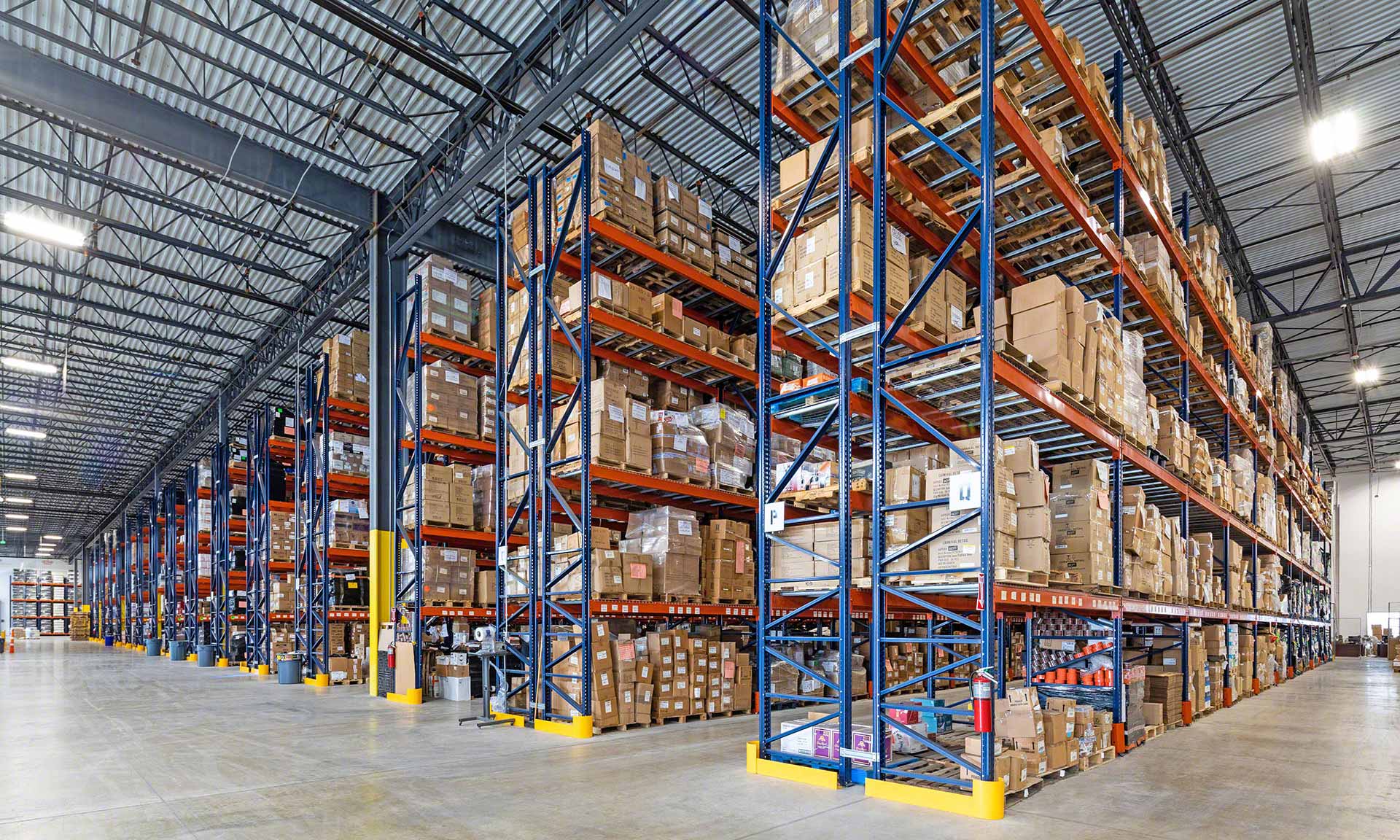
Interlake Mecalux and partner Andersen Material Handling have equipped a 13,935 m 2 warehouse in Miami, Florida, for Dufry, a travel retailer. The project includes adjustable pallet racks and the high-density push-back racking system. Overall, the syste...
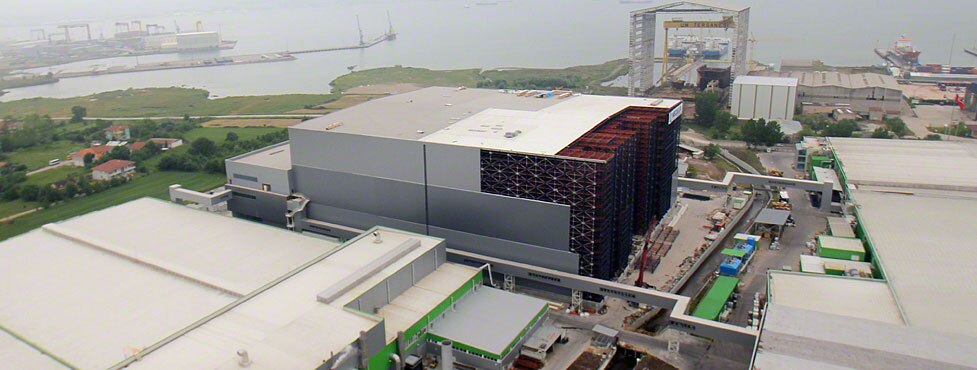
Hayat Kimya
Hayat Kimya is a leading manufacturer in the Eurasian fast-moving consumer goods market, specifically in the sector for hygiene and cleaning products. Founded in 1937, with its headquarters in Turkey, the company currently has 5,200 employees and exports to 101 c...
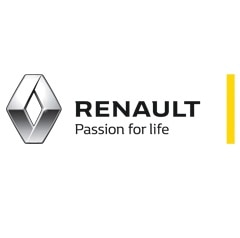
Here you can see some real solutions that Mecalux has developed. Contact us so we can assess the ideal solution for your company.
See our case studies for:
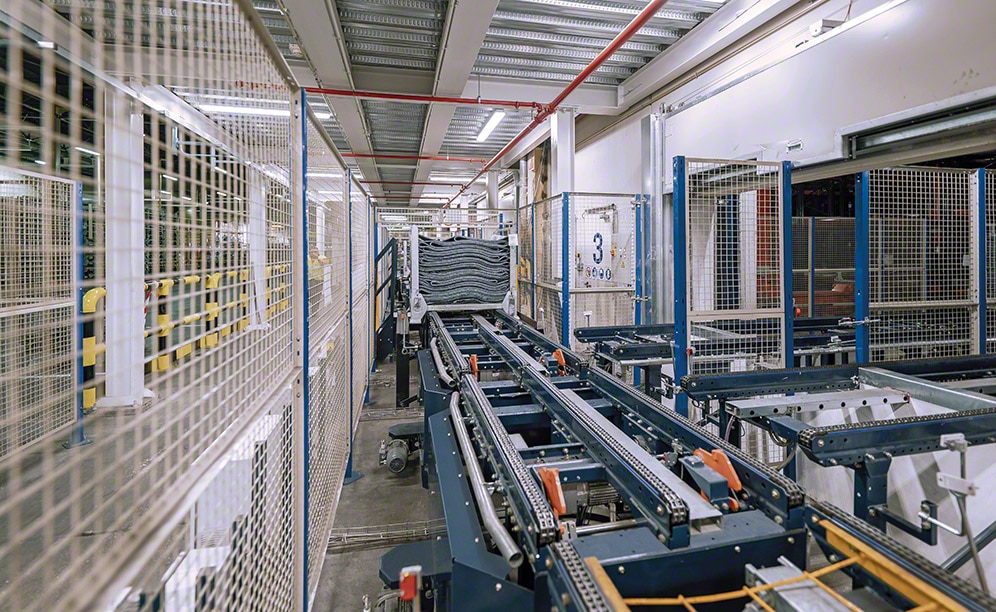
Automated clad-rack warehouse of Michelin integrated with manufacturing
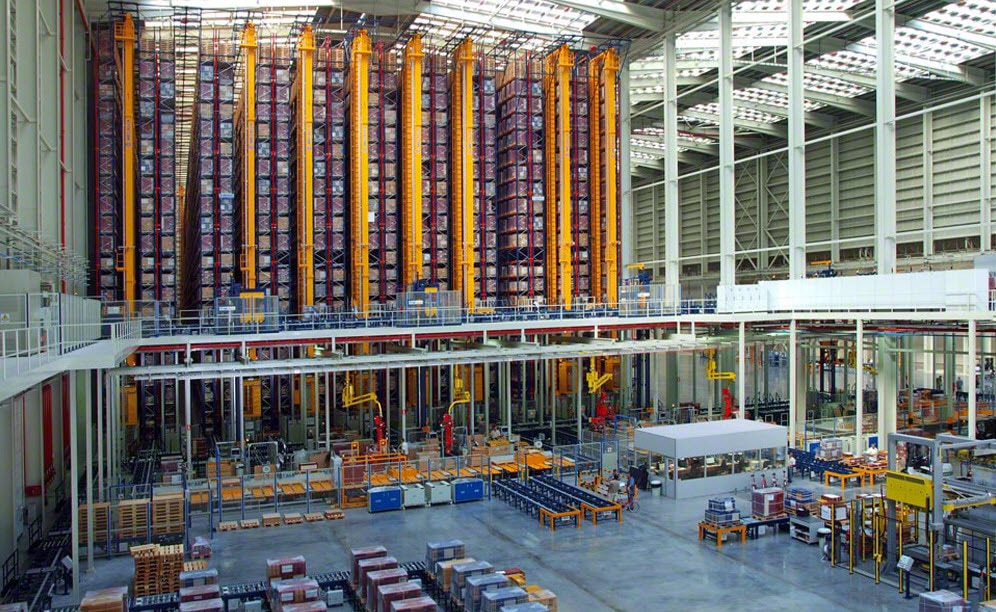
Porcelanosa
Mecalux completes the process of automating the porcelanosa group’s warehouses in castellón, spain.
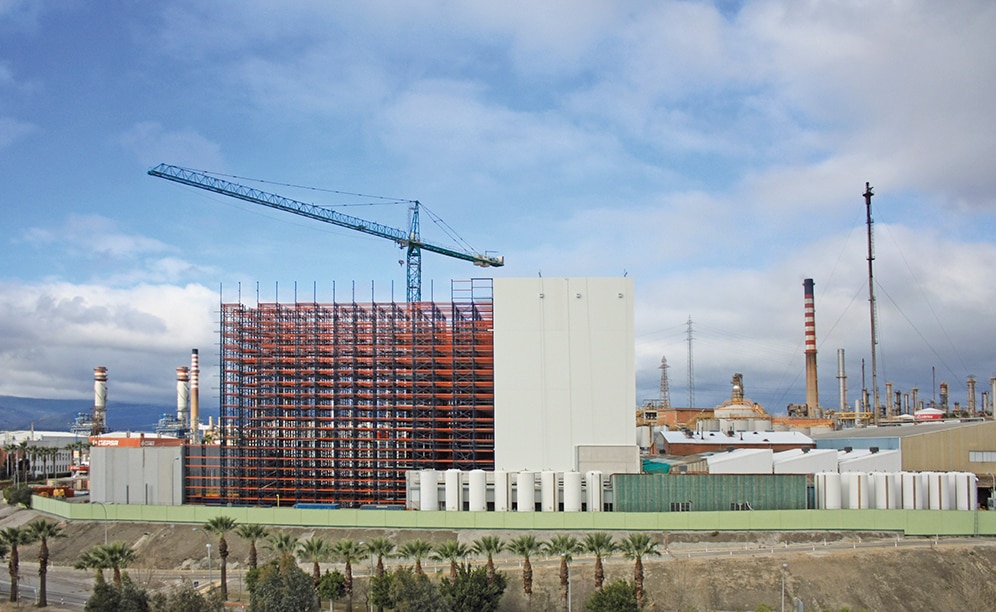
Next-generation automated clad-rack warehouse: a sure bet to streamline of logistics processes at Cepsa
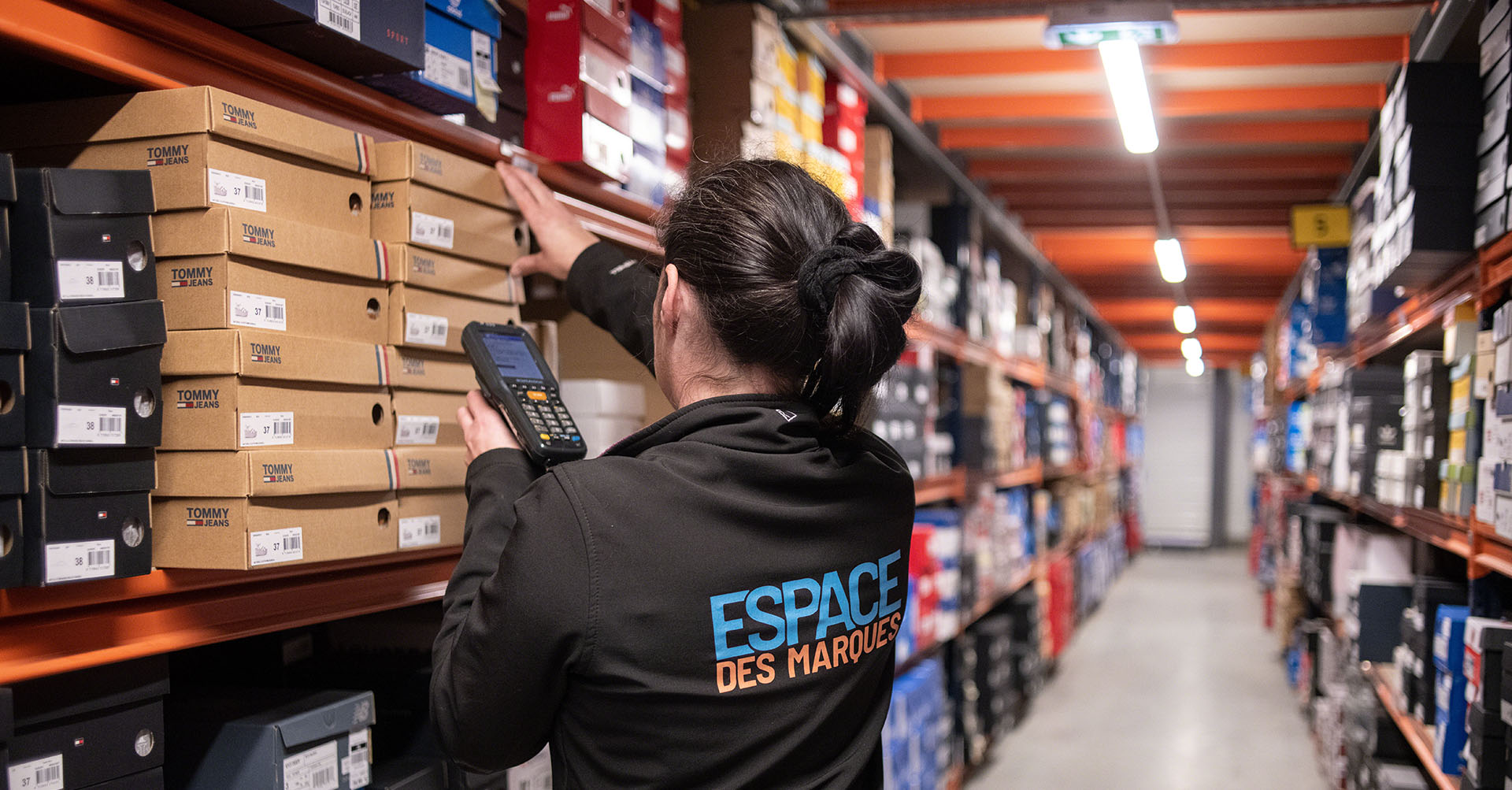
Espace des Marques
Omnichannel warehouses with 70,000 skus.
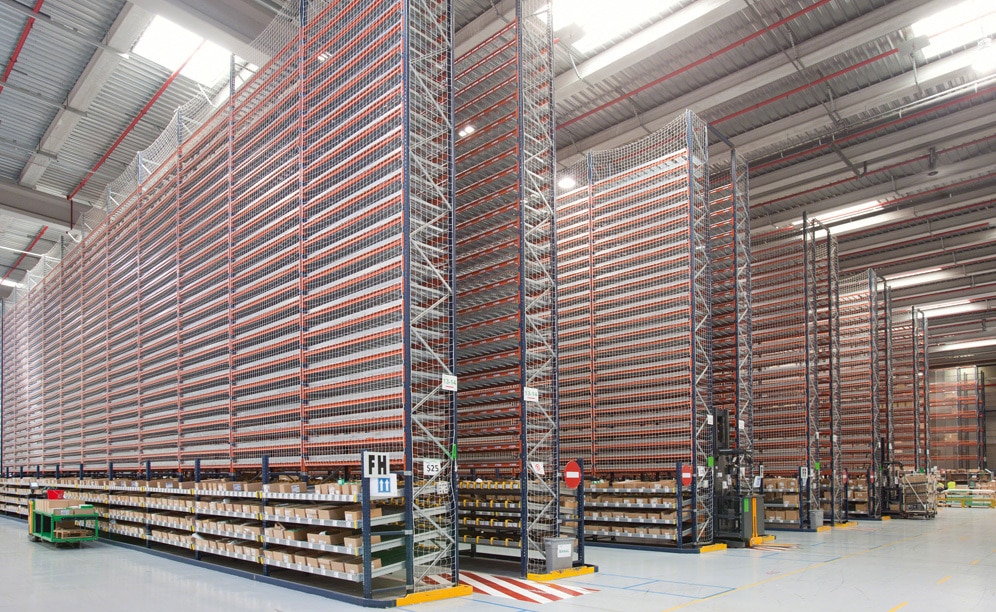
Schneider Electric
How to achieve the ideal balance between speedy picking and storage capacity.
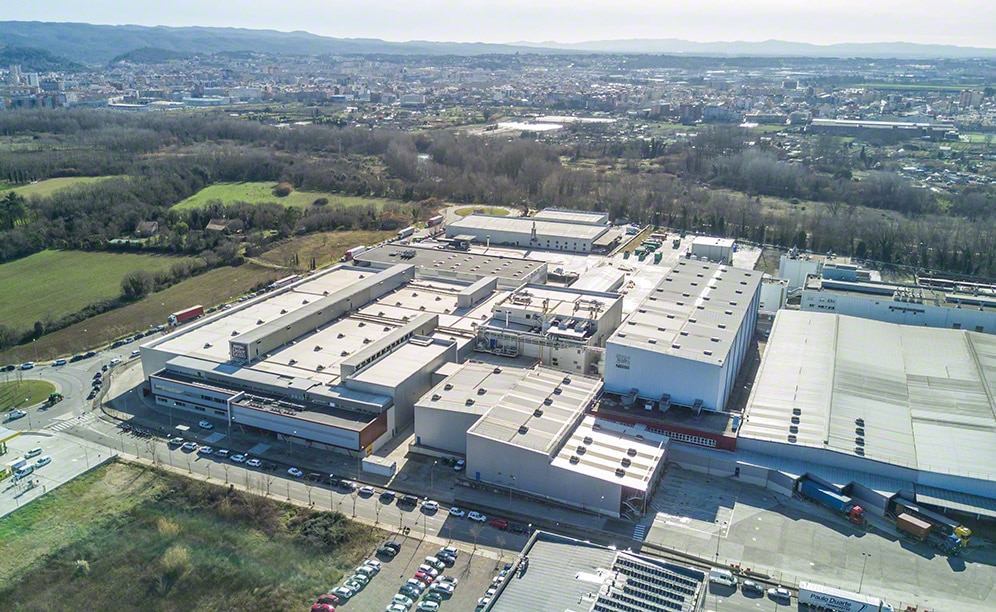
Efficient conveyors improve storage at Nestlé in Girona
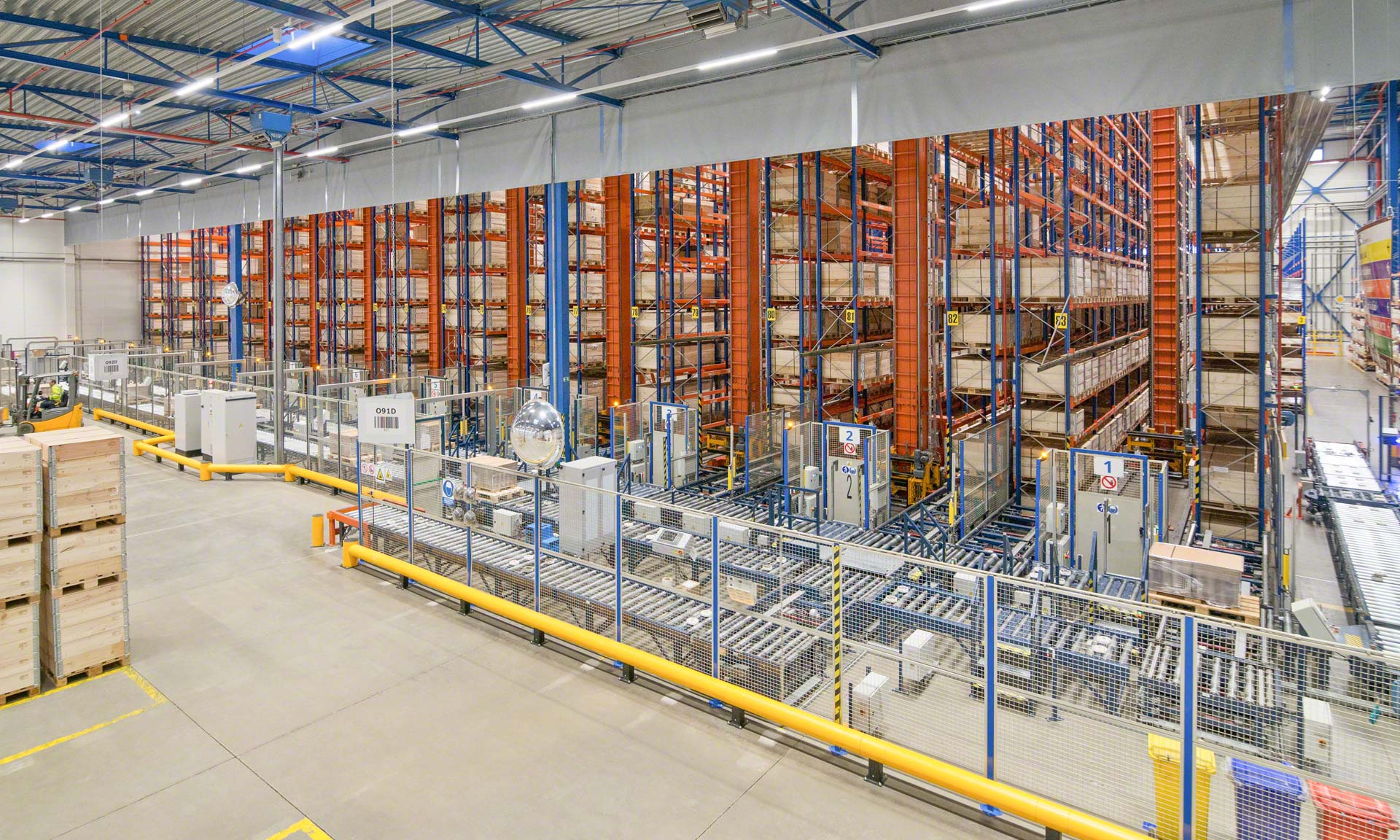
IKEA Components
Ikea components automates its warehouse in malacky without disrupting operations.
A 100% automated, turnkey warehouse for Würth in La Rioja
Easy WMS of Mecalux runs the warehouse of the car maker Renault
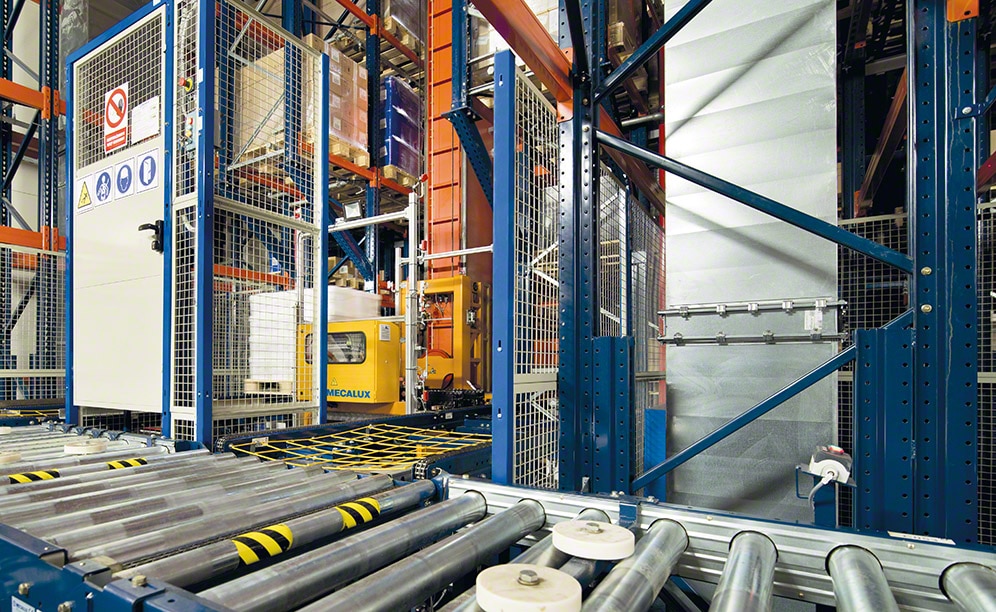
Novartis automates its supply chain in Poland
Coca-Cola Refrescos Bandeirantes
Warehouse with coca-cola soft drinks of refrescos bandeirantes in brazil.
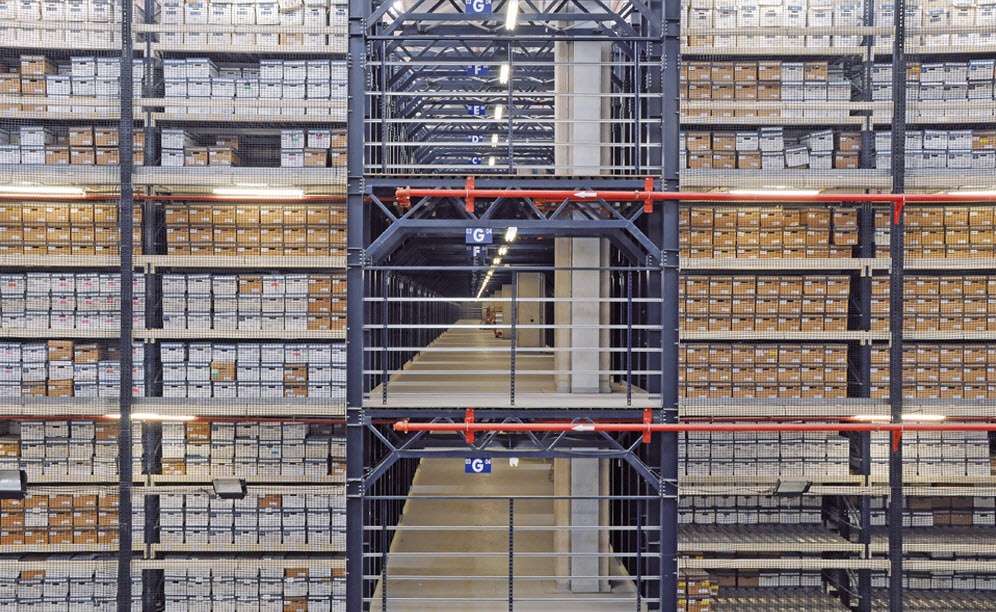
Iron Mountain
Earthquake-proof racking: warehouse with mecalux conventional racking on the pacific rim.
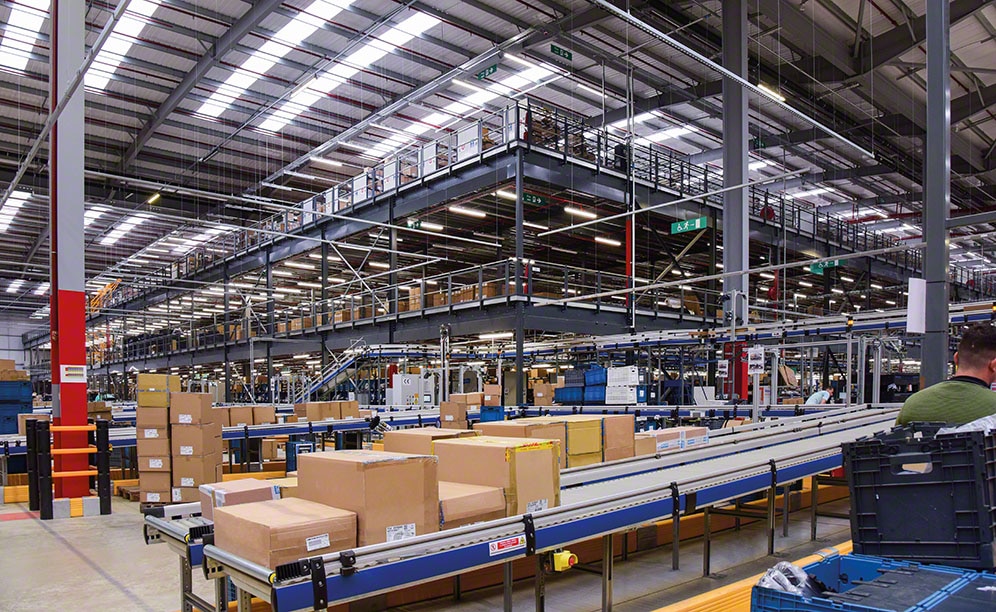
Decathlon has opened a new omnichannel warehouse in Northampton (United Kingdom)
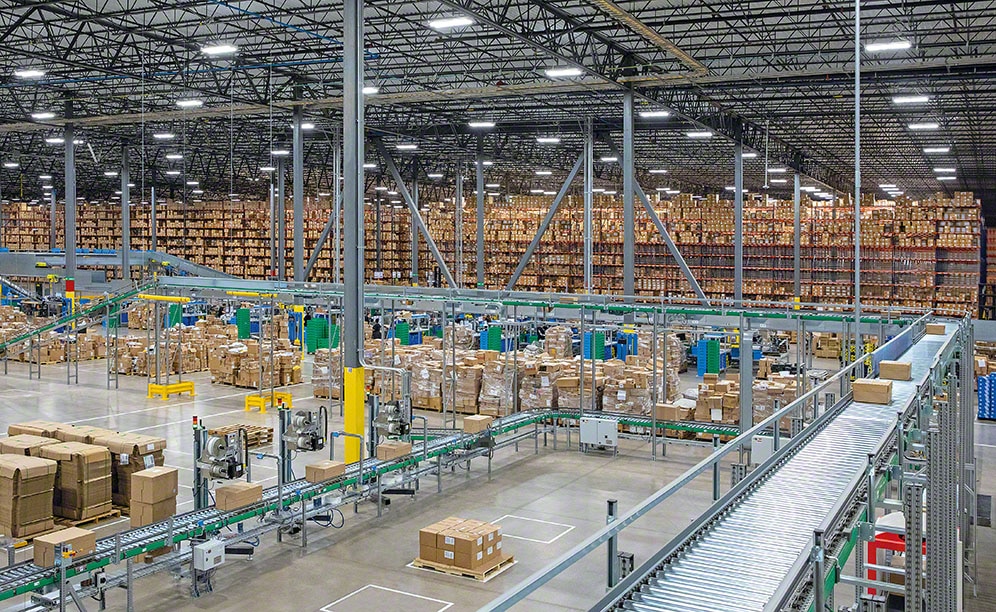
The Adidas sportswear and footwear store in Pennsylvania, USA
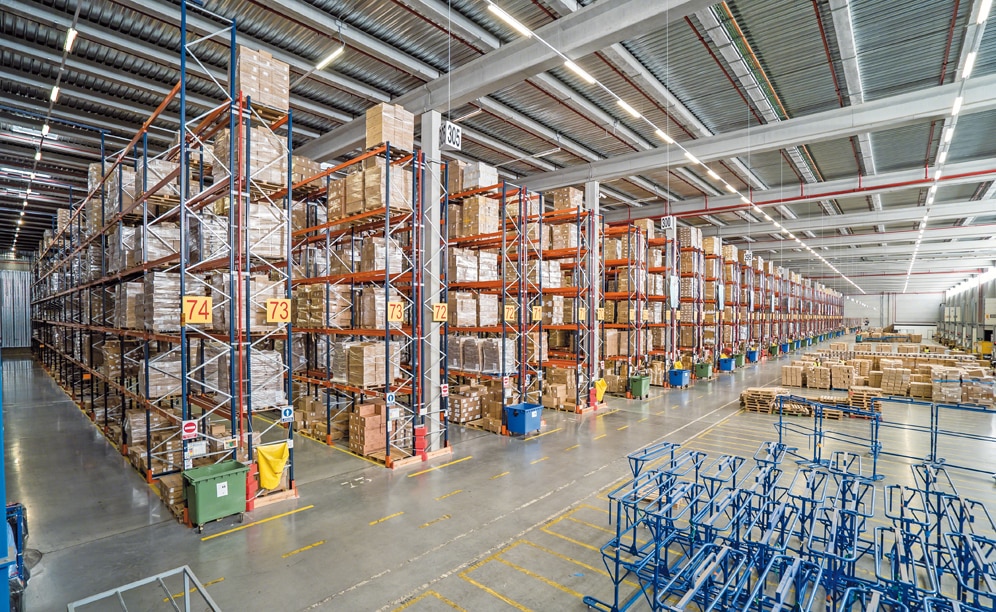
Mecalux installs a new logistics centre for DHL on the outskirts of Madrid
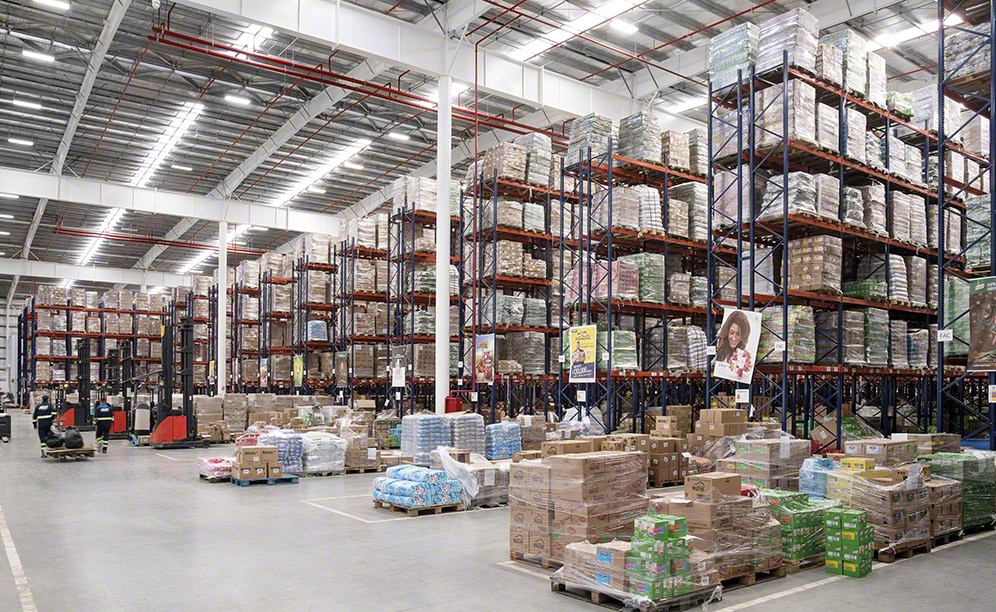
Mecalux has equipped the new Unilever distribution centre with pallet racking
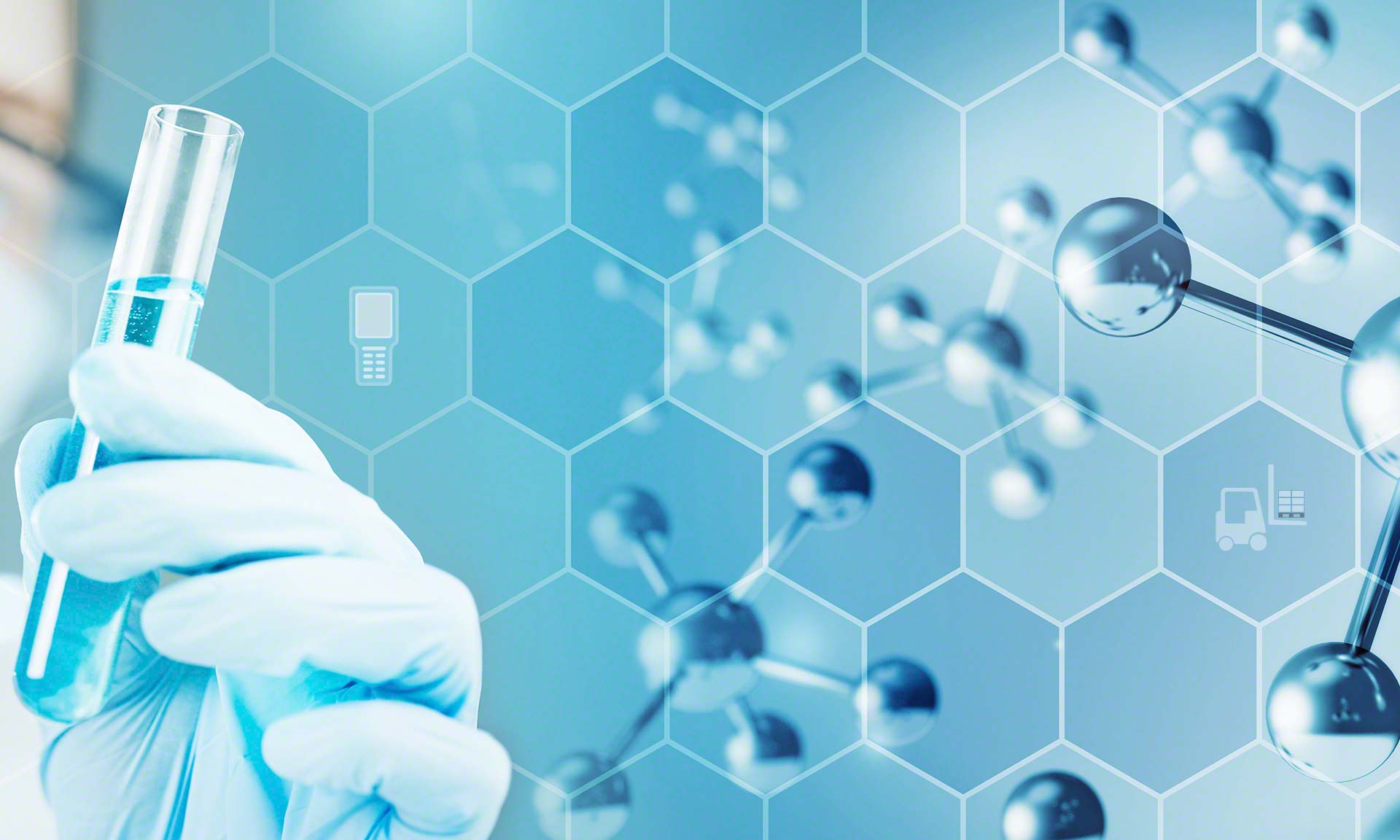
BASF: digitisation for just-in-time production
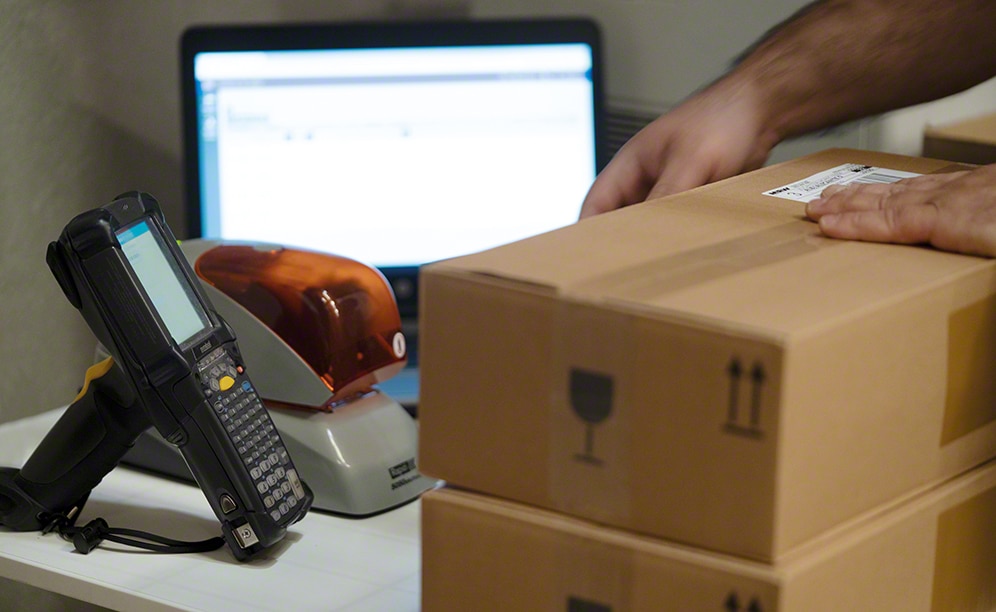
Danone’s warehouse for the infant and medical nutrition product line in Madrid
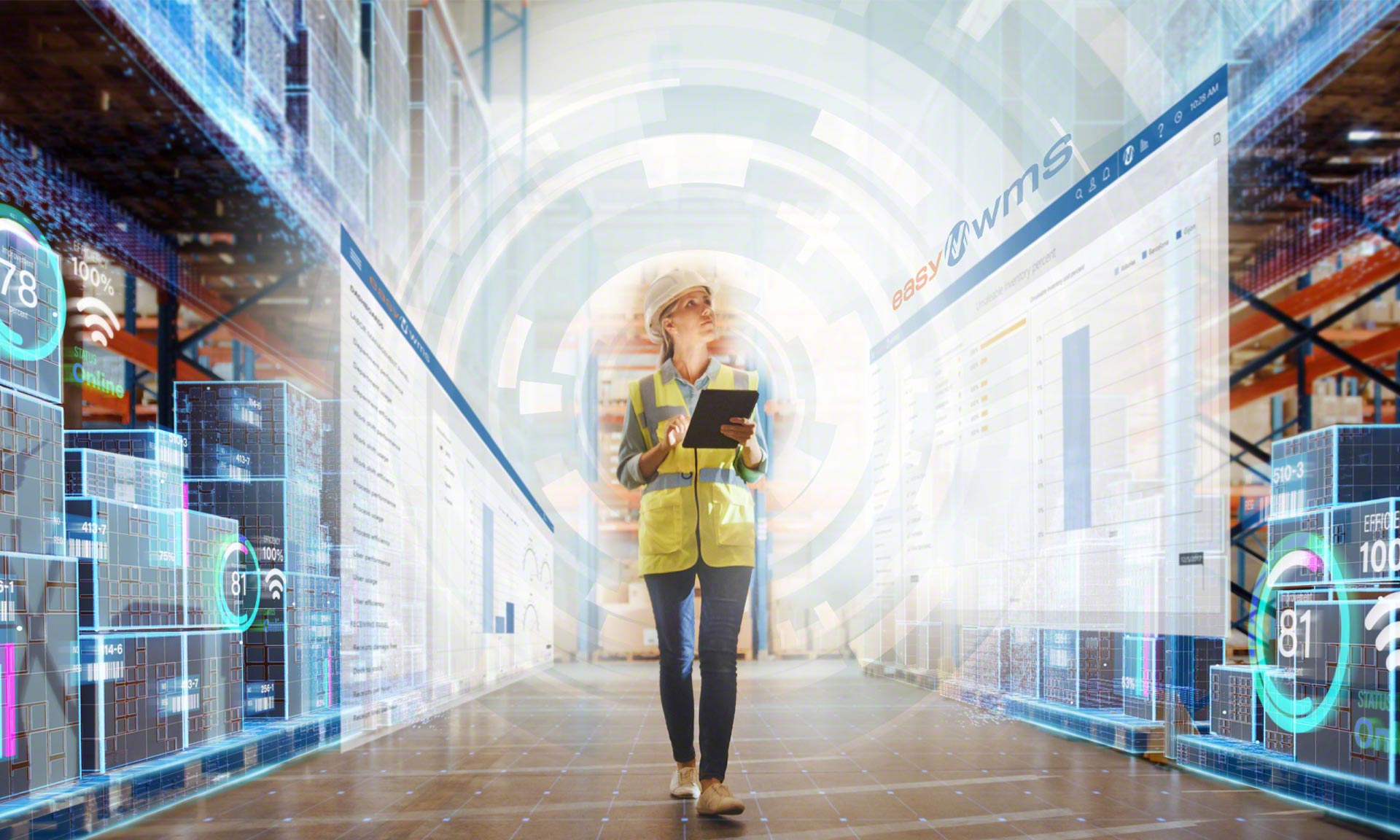
Digitisation transforms the supply chain
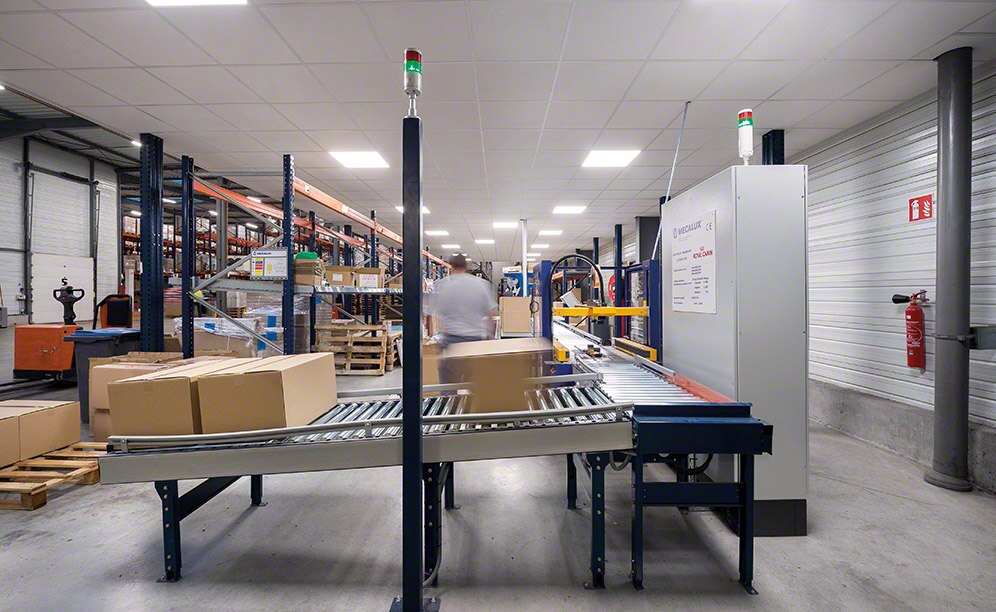
Royal Canin
Multiple solutions to manage pet food products, {{reference.name}}, {{reference.pcase.name}}.
This site uses cookies to improve your experience. By viewing our content, you are accepting the use of cookies. To help us insure we adhere to various privacy regulations, please select your country/region of residence. If you do not select a country we will assume you are from the United States. View our privacy policy and terms of use.
- Inventory Management Software
- Forecasting
- Sustainability
- Supply Chain Visibility

Pricing Optimization at Delly’s: A Case Study in Successful AI Enablement
Talking Logistics
SEPTEMBER 27, 2023
This includes implementing Enterprise Resource Planning (ERP), Customer Relationship Management (CRM), Demand Planning, Inventory Management, Transportation Management, and Warehouse Management applications. After capturing many of.

AI in the Retail Industry: Benefits, Case Studies & Examples
MARCH 27, 2024
Real-time visibility was lacking, be it in warehousing or transportation, due to which delivery delays were common. Besides, AI is helping retailers optimize inventory, warehouse and pricing. Intelligent Warehousing with AI Analytics AI-driven analytics optimizes warehousing operations helping improve storage space and efficiency.
This site is protected by reCAPTCHA and the Google Privacy Policy and Terms of Service apply.
- How To Set Up Innovation So That It Aligns With And Enables Corporate Strategy
MORE WEBINARS
Trending Sources
- SCM Research
- Enchange Supply Chain Consultancy
Logistics Viewpoints
- Enterra Insights
The Logistics of Logistics
- Techgistics
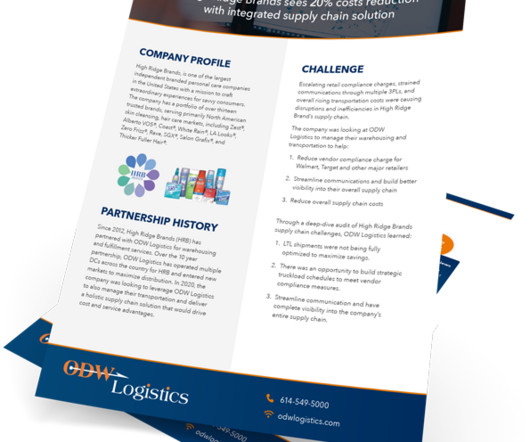
Case Study: High Ridge Brands Sees 20% Cost Reduction with Integrated Supply Chain Solution
Supply Chain Brain
JUNE 30, 2024
HRB looked to ODW Logistics for a supply chain solution, aiming to integrate warehousing and transportation management.
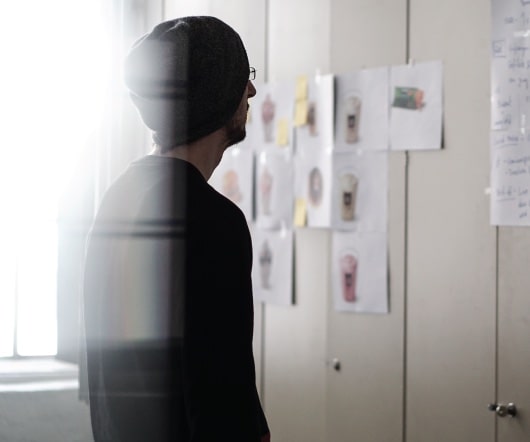
Supply Chain Case Study: the Executive's Guide
Supply Chain Opz
JUNE 1, 2014
Analysis of case study is certainly one of the most popular methods for people from business management background. In order to accelerate the learning, this article has gathered 20+ most sought-after supply chain case studies , analyzed/categorized them by industry and the findings are presented.
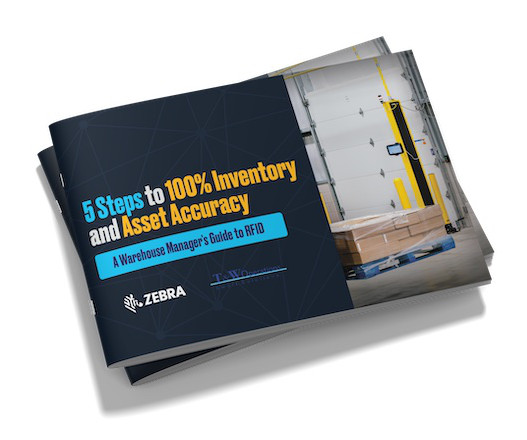
5 Steps to 100% Inventory & Asset Accuracy: A Warehouse Manager’s Guide to RFID
Advertisement
It highlights the use cases , benefits, and challenges of implementing RFID into your warehouse and supply chain operations and finding the right partner to get you there. Barcodes vs. RFID 5 ways to deploy RFID in your warehouse How to find the ideal RFID solution Who can help? What's inside the eBook?
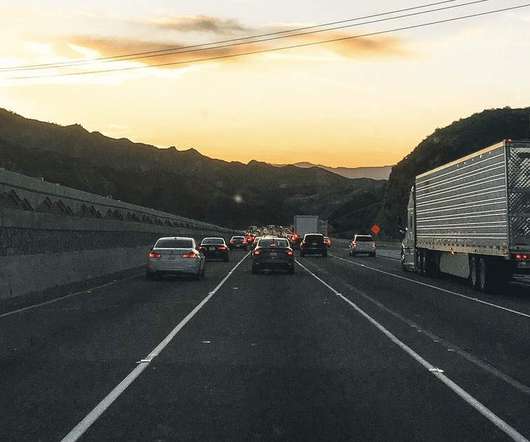
Cross Docking 101: What, Why and How? [with case studies]
SEPTEMBER 23, 2021
This removes the ‘storage’ element of warehousing logistics, and saves on costs, warehousing space, time and labour. In a cross docking system, goods are not stored onsite – making it different from warehousing Cross docking vs warehousing – what’s the difference? Why is cross docking used?
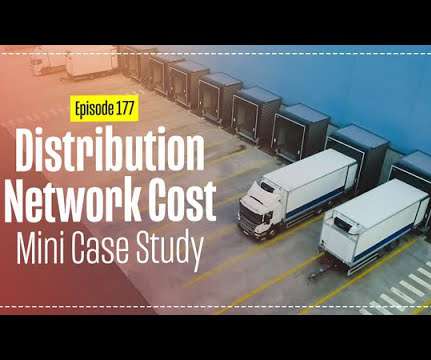
Distribution Network Cost- A Mini Case Study
Logistics Bureau
SEPTEMBER 7, 2022
Related articles on this topic have appeared throughout our website, check them out: The 7 Principles of Warehouse and Distribution Centre Design. Spotlight on Triadic Distribution Centres Making Triadic, Dyadic and Monadic Sense of your Warehouse . The Long and Short of Designing a Distribution Network.
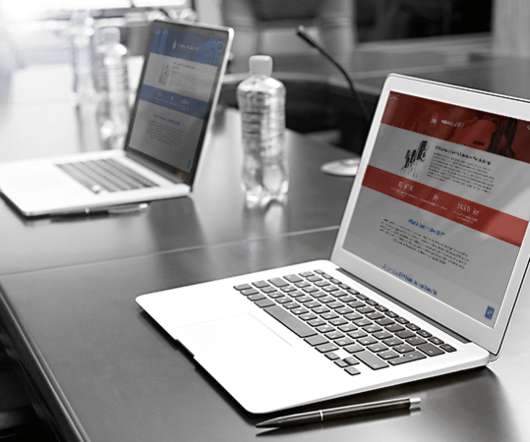
Companies Using ERP: Case Studies
SEPTEMBER 22, 2021
Case Study #1: Noble Biomaterials. Read the full Noble Biomaterials case study to learn more. . Case Study #2: Veoneer. The company operates multiple sites in different locations, as well as four warehouses in different districts. Read the full Veoneer case study to learn more.
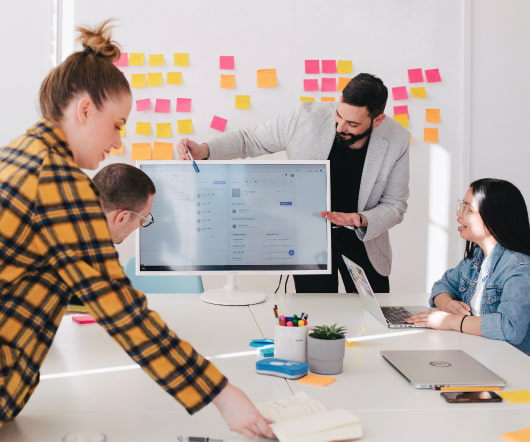
AutoStore and the Rise of Flexible Automation: The Parts Town Case Study
MAY 7, 2018
Historically, we talked about warehouses as being manual or highly automated. Manual warehouses are more flexible. Highly automated warehouses have much higher throughput, but their lack of flexibility adds risk.
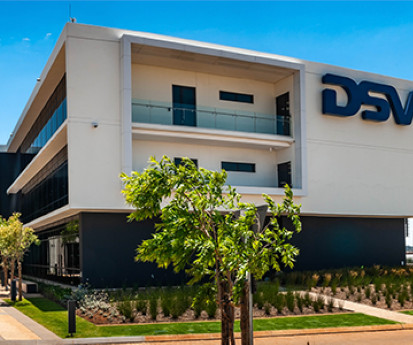
Case Study: DSV Implements a Single-Instance Control Tower with a Global Footprint
After having opened a new warehouse in Johannesburg - the largest integrated logistics center on the continent - a multi-national FMCG Healthcare company approached DSV South Africa (SA) for services across the end-to-end supply chain.
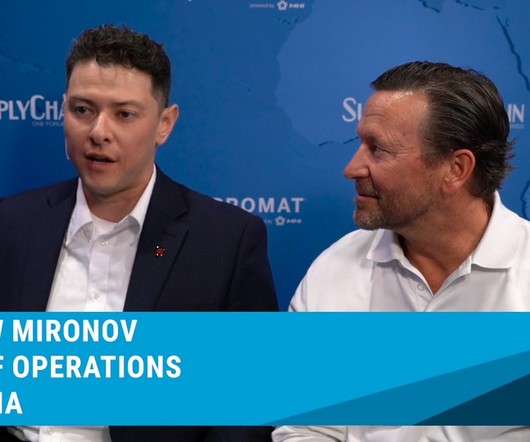
Watch: Alpine Supply Chain Solutions & Ecentria: A Case Study
APRIL 27, 2023
Huge growth in sales led to the need to optimize inventory, fulfillment and warehouse operations at Ecentria, say Michael Wohlwend, managing principal of Alpine Supply Chain Solutions, and Andrew Mironov, head of operations at Ecentria.

AutoSchedler.AI is Named Sponsor of the Supply Chain Matters Blog
Supply Chain Matters
AUGUST 29, 2024
As Founder and Managing Editor I am pleased to announce to our global-wide Supply Chain Matters readership that Cloud based warehouse management orchestration provider AutoScheduler.AI This deployment has since expanded to this customer’s other warehousing facilities. AutoScheduler Overview AutoScheduler.AI
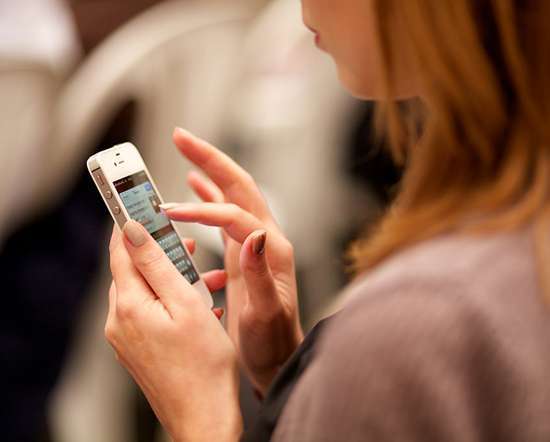
Warehouse Robots Enable a Digital Transformation
AUGUST 13, 2018
Because about half of this company’s 2017 revenues are related to warehousing services, several of their digital projects have been related to improving efficiency in their warehouses . This case study describes their approach to testing out mobile logistics robots.
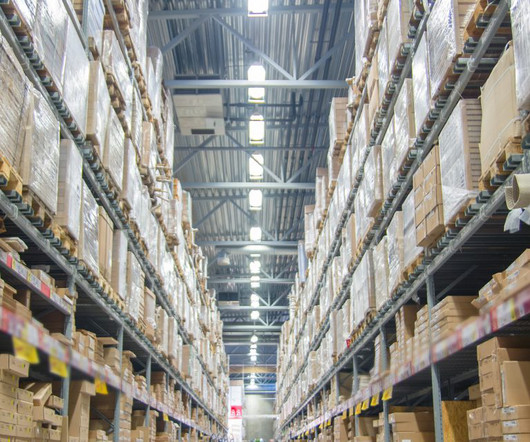
Primer for Control Layer Technology Platforms Applied to Warehousing and Customer Fulfillment Processes
MARCH 14, 2023
Supply Chain Matters provides a first installment in a four-part technology market education series where we address the evolving use of Cloud based control layer technology platforms applied to warehousing and customer fulfillment processes. This initial posting provides readers with an overview and primer for this type of technology.
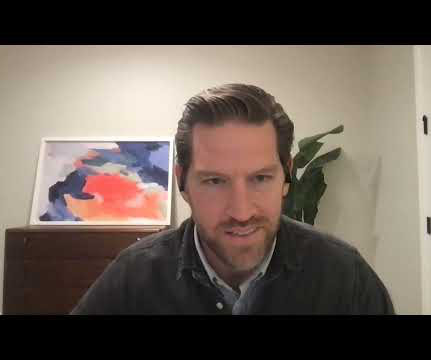
Why Packaging Matters with Phillip Akhzar
FEBRUARY 27, 2023
Arka’s API uses AI to auto-replenish packaging inventory for warehouses and 3PLs. Arka works with both shippers and warehousing companies. For warehousing companies: Arka automates the packaging ordering process by connecting Arka’s API to the warehouse management system (WMS).
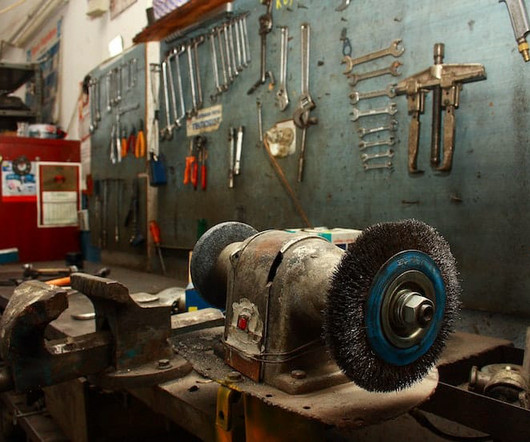
Machine Learning in Supply Chain: Definition, Uses, Case Studies
APRIL 4, 2023
We also break down several case studies of companies currently using machine learning in their supply chain processes. Machine learning can improve the supply chain in numerous ways, from tracking and predicting warehousing needs to delivery optimisation, and customer demand forecasting. What is machine learning?
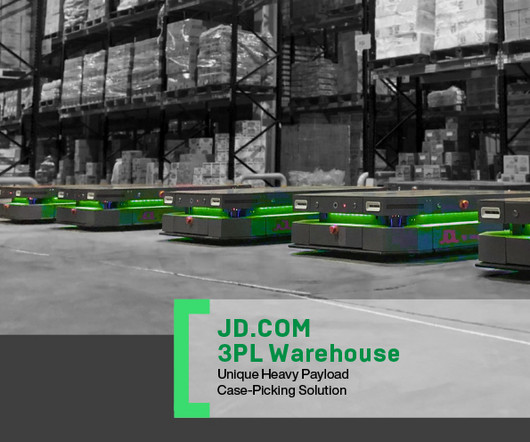
Warehousing Case Study: JD.COM 3PL Warehouse
JULY 14, 2024
As the largest retailer in China, JD.COM serves 99% of the country, providing unparalleled same-day and next-day delivery. With approximately 600 million active customers, JD.COM faces costly, inefficient, and labor-intensive operations, compounded by high turnover rates. To address these pain points, JD.COM partnered with ForwardX Robotics.
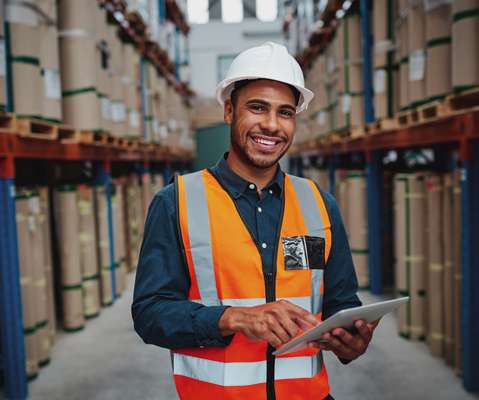
Top Mobile Barcoding Case Studies for Oracle’s JD Edwards
OCTOBER 14, 2020
In this article, we’ll explore top case studies illustrating how companies added mobile barcoding technology to get more out of their JD Edwards ERP investment. It relies on 32 warehouses situated strategically around the country, each with extensive inventory volume, to accomplish this.
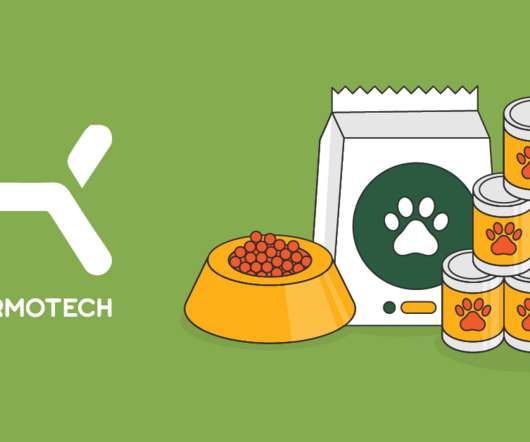
Case Study: Reducing Excess Inventory
Demand Driven Technologies
JANUARY 11, 2022
But when the inventory piles up in your warehouse because you don’t have the other materials you need to manufacture your products? It’s hard to pass up a good deal from one of your preferred suppliers. That good deal starts to seem less attractive. Frustrated by inventory inefficiencies, supply chain leaders at Ukrainian pet food.
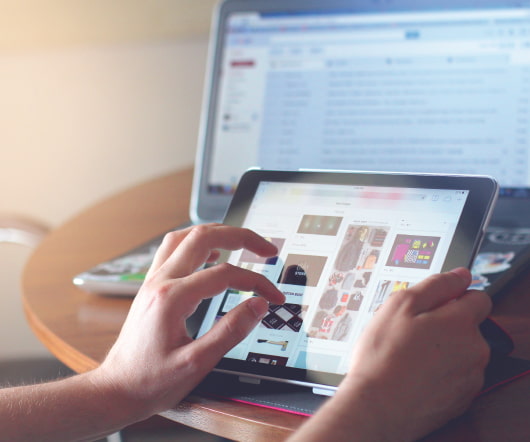
TMS for SMB: A Case Study with Carhartt
OCTOBER 19, 2016
Rapid growth, coupled with new market segments and channels (including ecommerce), prompted Carhartt to embark on a multi-million dollar upgrade of its distribution center, which included investments in warehouse management and transportation management solutions.
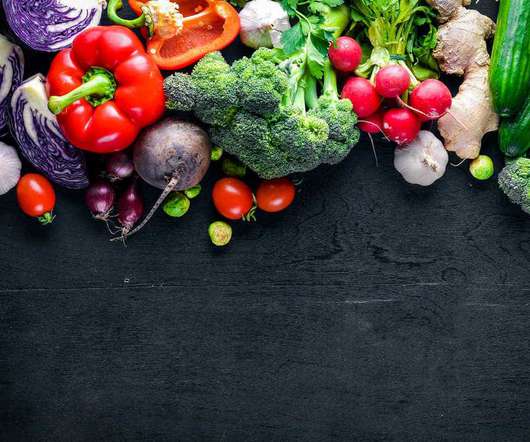
How Food Manufacturing Software Drives Profit [w Case Studies]
AUGUST 11, 2020
The right software will also improve operational processes, boost warehouse efficiency and reduce waste. For example Stock Age by Stock Keeping Unit (SKU) can be cross-referenced with warehouse location to see which ingredients are sitting on the shelf and need to be moved (perhaps with a local promotion or price change).
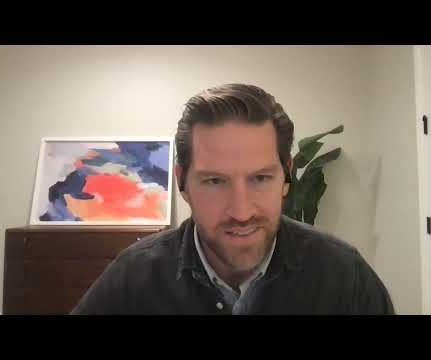

Flexible Warehousing with Flexe CEO Karl Siebrecht
MARCH 24, 2023
Karl Siebrecht and Joe Lynch discuss flexible warehousing , which is exactly what Karl and the Flexe team provides to their customers. Key Takeaways: Flexible Warehousing Karl Siebrecht is the Co-Founder and CEO of Flexe, a company that solves the hardest omnichannel logistics problems for the world’s largest retailers and brands.
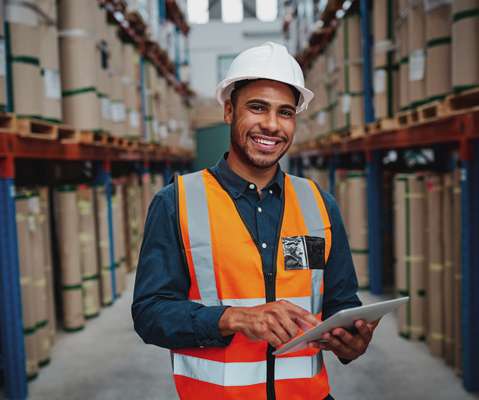
Understanding the Profitability of Omnichannel Retail is a Problem
NOVEMBER 20, 2023
But one thing you notice as you go to omnichannel software vendor’s web sites and examine customer case studies , the case studies may talk about retailers growing their revenues by 100% or more, but none talk about how much profitability grew. These new order fulfillment paths allowed retailers to rapidly grow sales.
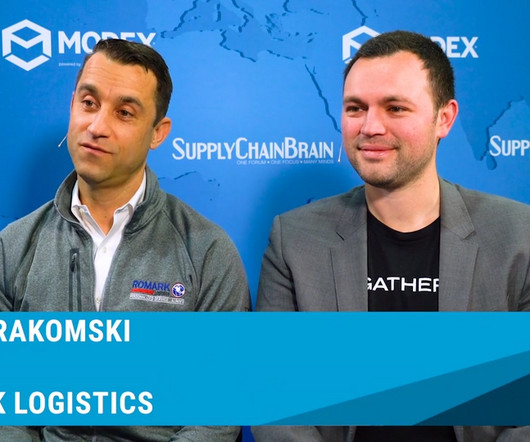
Watch: Romark Logistics and Gather AI: A Case Study
APRIL 9, 2024
A case study about the application of drones employing artificial intelligence to the warehouse operations of Romark Logistics.
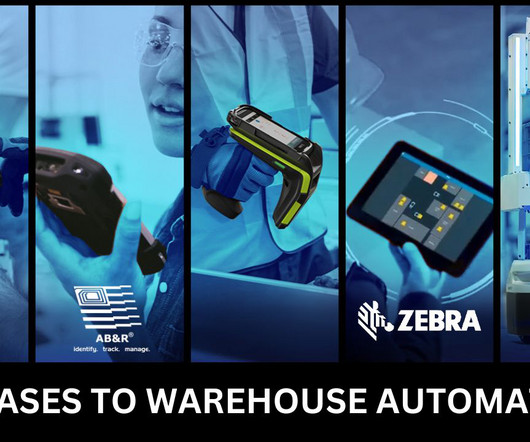
Find Your Warehouse Maturity Phase
Find Your Warehouse Maturity Phase Every day, we hear, read, and talk about warehouse automation. Our partner Zebra Technologies designed a five-phase warehouse maturity model to help businesses identify where they fall in the automation race and how to reach the next phase. Download the Warehouse Maturity Model Checklist.
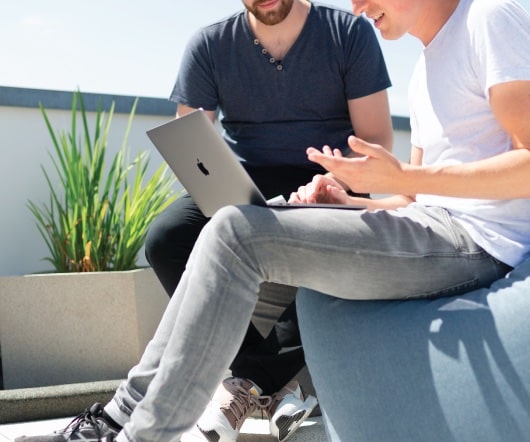
7 Traits of Great Supply Chain Leader: A Case Study of Tim Cook
OCTOBER 3, 2013
Cook reduced number of warehouses , from 19 to 9 and slashed inventory level from 2 months to 1 month. So he reduced number of key suppliers, from 100 down to 24. Cook also asked them to consider the price discount and relocate closer to Apple''s factory. By September of 1998, inventory level was down to 6 days.
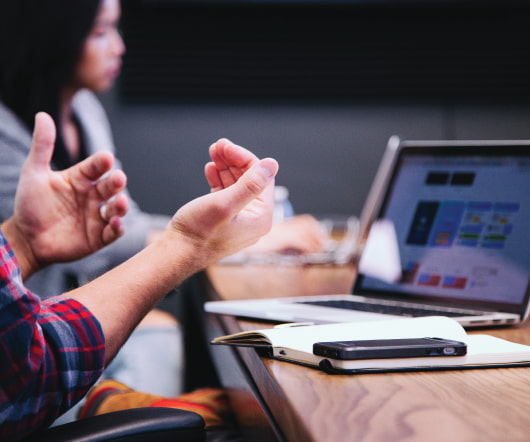
Physician Office Case Study: Hybrent provides supply chain efficiency at multi-site locations
FEBRUARY 6, 2019
And, because Village Podiatry locations are scattered around the region and it does not have a warehouse that supplies can be delivered to, it is important for the accounts payable department to know immediately when a product is delivered. The old system didn’t provide this option. Ross is satisfied with the changeover to Hybrent.
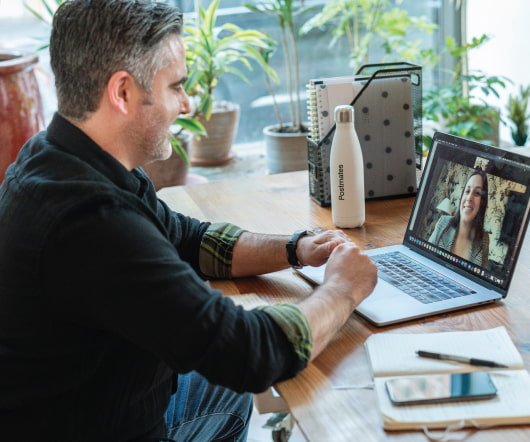
Implementing RFID for Manufacturing Visibility: A Case Study
DECEMBER 8, 2014
Likewise, maintenance personnel will be equipped with a mobile RFID reader to read and log maintenance work done on a stillage and maintain historical data.
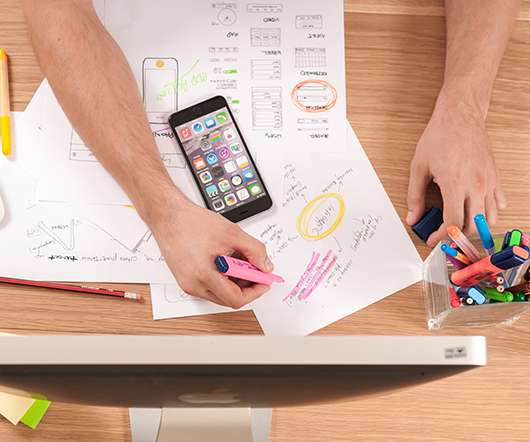
A Case Study in Reverse Logistics Optimization!
Supply Chain Game Changer
NOVEMBER 23, 2018
Inadequate planning and execution resulted in excess and obsolete inventory and poor utilization of warehouse space. The post A Case Study in Reverse Logistics Optimization! Difficulties forecasting demand in a high-volume repair environment caused inventory costs to skyrocket. The Solution. Learn more at [link].
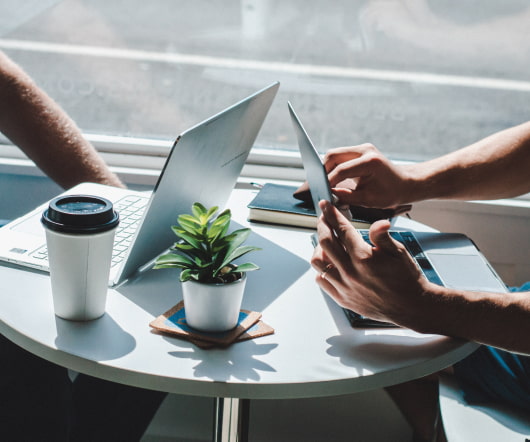
Delivering Green: Three Case Studies in Low-Carbon Logistics
MIT Supply Chain
APRIL 29, 2013
Caterpillar is the subject of one of three case studies that show how supply chain management can support both environmental and financial goals. Here are three case studies that offer clear, irrefutable evidence that sustainability and profitability can be compatible in the supply chain domain.

Adexa is Recipient of 2024 Top Supply Chain Projects Award
JUNE 17, 2024
About Supply & Demand Chain Executive Supply & Demand Chain Executive is the only supply chain publication covering the entire global supply chain, focusing on trucking, warehousing , packaging, procurement, risk management, professional development and more. Food Logistics also operates SCN Summit and Women in Supply Chain Forum.
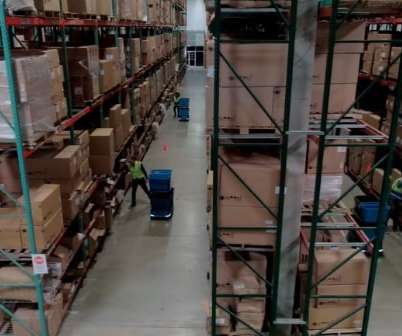
What is picking in a warehouse?
6 River Systems
DECEMBER 13, 2019
Warehouse picking refers to the process where individual items are picked from a fulfillment facility to satisfy customers’ orders. It’s an essential aspect of order fulfillment and is considered one of the most expensive and labor-intensive activities for warehouses .
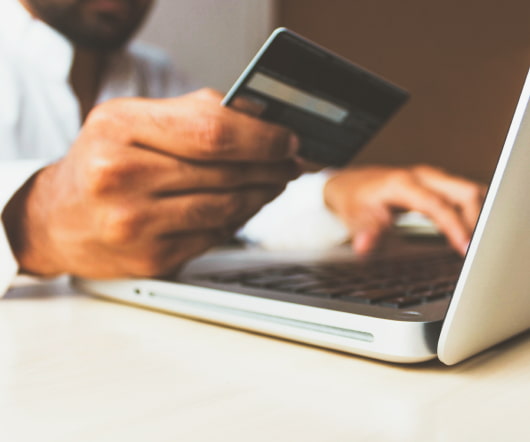
Case Study: People and Processes Drive Supply Chain Improvements at Honeywell
MAY 8, 2019
Create a load plan for the warehouse and daily share files. To solve the issue of missed pickups, warehouse dock clutter, and rolled bookings, we shifted more volume toward an incumbent carrier that had a drop yard near our warehouse . Send rebooking advice to our Freight Forwarder. Wednesday, May 15 in Grand Sonoran E.
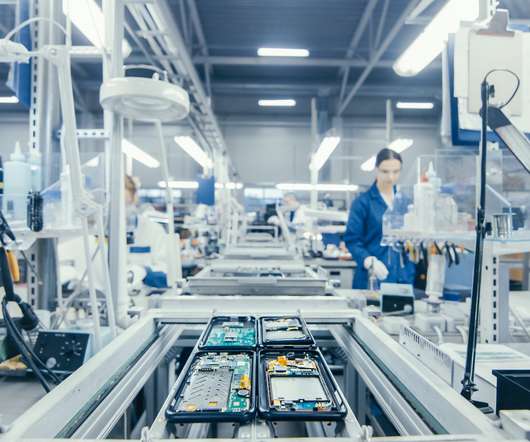
Optimization and Execution: How Manufacturing can lead the Industry Renaissance
DELMIA Quintiq
JUNE 9, 2020
They also must be working together in harmony to achieve maximum benefit from their capabilities: MOM Specifics: Visibility, synchronization and control over ALL operations: production, quality, warehousing , maintenance and field operations. Each solution has inherent value but are less effective when implemented in isolation.
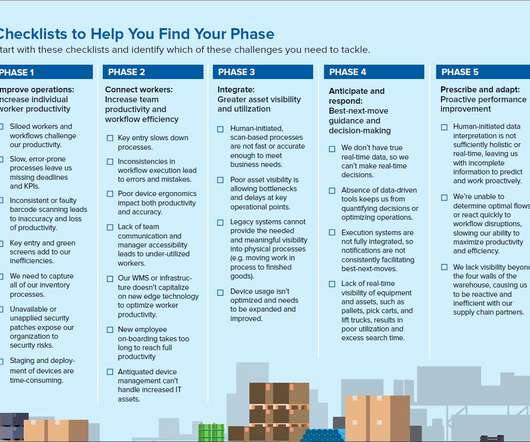
NOVEMBER 8, 2022
Find Your Warehouse Maturity Phase. Every day, we hear, read, and talk about warehouse automation. Our partner Zebra Technologies designed a five-phase warehouse maturity model to help businesses identify where they fall in the automation race and how to reach the next phase. Download the Warehouse Maturity Model Checklist.
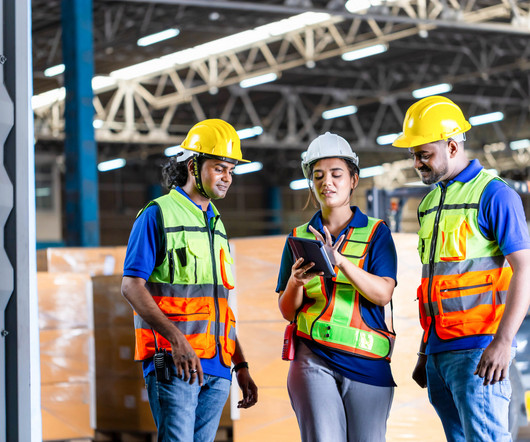
Efficiently Picking Your Way to Success: Best Practices for Improving Order Picking Speed and Accuracy in Warehouse Management
MARCH 10, 2023
Order picking is a critical process in warehouse management that involves selecting items from inventory and assembling them into customer orders. The accuracy and speed of this process have a significant impact on warehouse efficiency, customer satisfaction, and ultimately, business profitability. My Warehouse is a Mess!
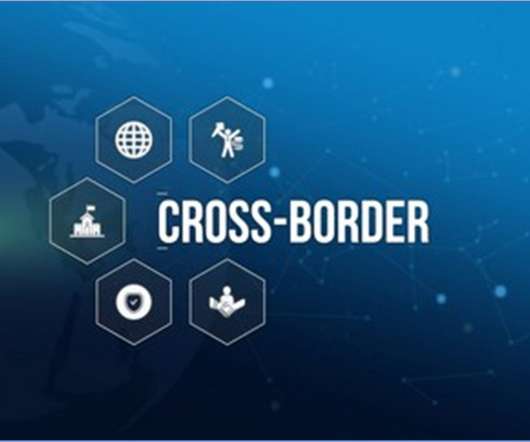
Free Trade Zone – Is Your 3PL Giving You All the Warehouse and Distribution Cost Savings You Deserve?
ModusLink Corporation
FEBRUARY 8, 2023
Fulfillment Free trade zones, or FTZs, are controlled places in a country that offer warehouse and distribution services for goods from foreign markets, excluding them from paying taxes on those goods. These include: People and staffing requirements include skilled workers and managers that will do the daily warehouse operations.
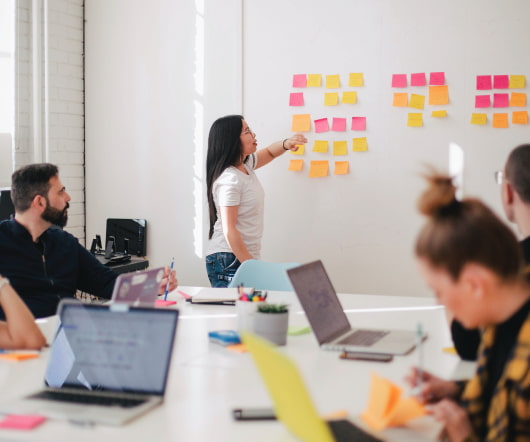
Lull Case Study: Order Fulfillment that Doesn’t Keep You Up at Night
OCTOBER 11, 2018
Get the PDF of Lull’s case study >> Challenges to Order Fulfillment. The FLEXE Supply team sourced additional warehouse providers in the FLEXE network—all of which were already running on the FLEXE software platform. Blog and video: 2018 D3: Future-Proof Your Warehouse Strategy. 30% reduction in FedEx costs.
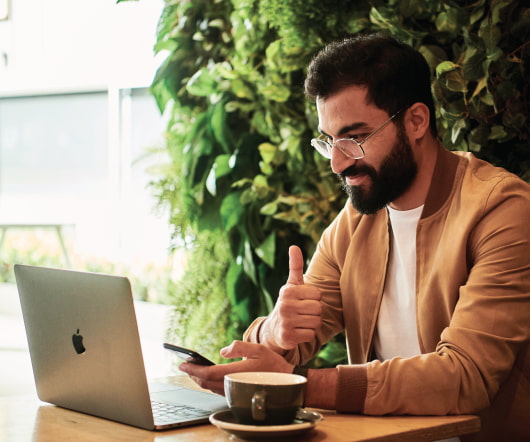
Unlocking the Value of Global Supply Chain: the Case Studies
JULY 7, 2014
In order to control its supply chain, they use a central warehouse to Germany to receive and ship products to local distribution centers in different countries. They don''t invest in production facility at all because they utilize a network of nearly 700 suppliers located in Asia and Europe.
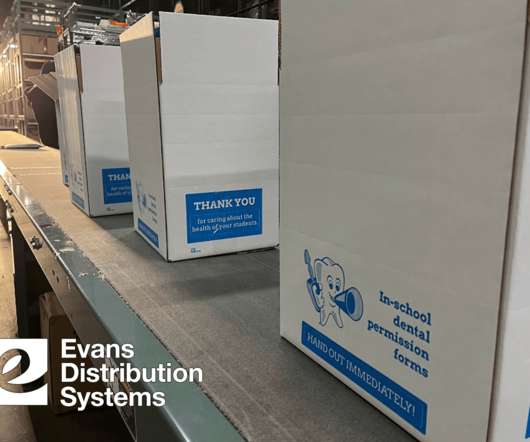
Fulfillment That Makes You Smile: Smile America Partners Case Study
3PL Insights
FEBRUARY 2, 2023
The portal was integrated with Evans’ warehouse management system (WMS). Evans associates designed a unique pick and pack process in the warehouse using barcodes to trace inventory in the WMS. Download the case study here. This integration allows for faster order processing and inventory visibility.
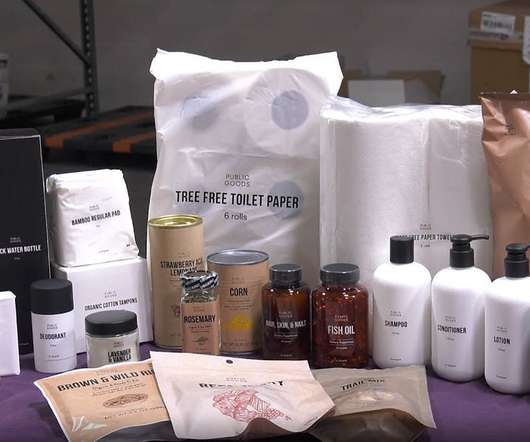
Flexible Warehousing Solutions: A Public Goods Case Study
Amware Logistics and Fulfillment
SEPTEMBER 22, 2020
In this article, we’ll showcase Amware's flexible warehousing solutions in helping Public Goods respond to a 500% spike in orders. This is certainly true within the world of logistics, where order volumes – especially those for essential household products – have increased dramatically since March.
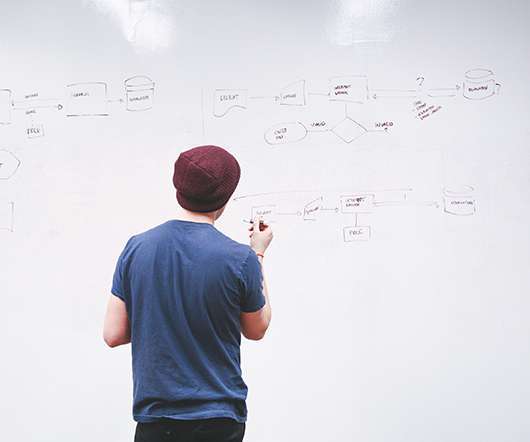
Case Study: How Generac Power Systems Cut Millions from Its Global Transportation Spend
CH Robinson Transportfolio
MARCH 28, 2018
Alan’s team can see the 40’ containers arriving at the port and they can track the freight as it is moved to a warehouse and is consolidated onto 53’ intermodal containers. The post Case Study : How Generac Power Systems Cut Millions from Its Global Transportation Spend appeared first on Transportfolio.
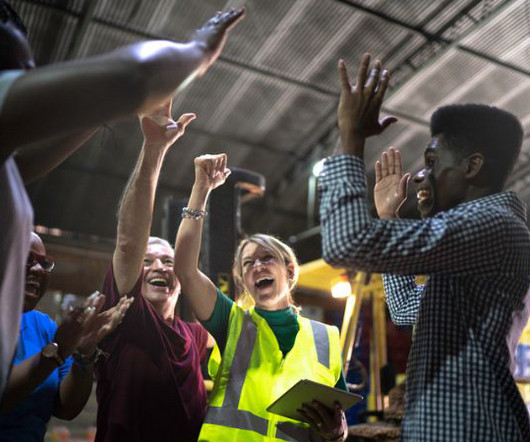
Warehouse Wins: Leveraging Software to Transform Inventory Challenges into Inventory Triumphs
JUNE 2, 2023
A common “slow zone” in the warehouse . Even though new warehouse software may require an initial investment, the efficiencies gained quickly pay off, providing a return on investment, better known as ROI. When it comes to warehouse optimization, relying on smart, innovative software solutions is hard to beat.
Stay Connected
Join 136,000+ Insiders by signing up for our newsletter
- Participate in Supply Chain Brief
- How to achieve six-figure benefits from digitizing paper-based supply chain operation
- 2019 Supply Chain Brief Summer Reading List
- Stay At Home Reading List
- Add a Source
- Add a Resource
- See All
- 2018 Supply Chain Brief MVP Awards
- 2019 Supply Chain Brief MVP Awards
- 2020 Supply Chain Brief MVP Awards
- 2021 Supply Chain Brief MVP Awards
- 2022 Supply Chain Brief MVP Awards
- Thu. Sep 12
- Wed. Sep 11
- Tue. Sep 10
- Mon. Sep 09
- Aug 31 - Sep 06
- Warehousing
- Procurement
- Transportation
- Supply Chain
- More Topics

Input your email to sign up, or if you already have an account, log in here!
Enter your email address to reset your password. a temporary password will be e‑mailed to you., be in the know on.
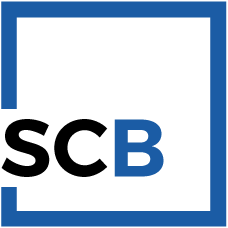
Supply Chain Brief
Expert insights. Personalized for you.
We organize all of the trending information in your field so you don't have to. Join 136,000+ users and stay up to date on the latest articles your peers are reading.

Get the good stuff
Subscribe to the following Supply Chain Brief newsletters:
You must accept the Privacy Policy and Terms & Conditions to proceed.

You know about us, now we want to get to know you!
Check your mail, we've sent an email to . please verify that you have received the email..
We have resent the email to
Let's personalize your content
Use social media to find articles.
We can use your profile and the content you share to understand your interests and provide content that is just for you.
Turn this off at any time. Your social media activity always remains private.
Let's get even more personalized
Choose topics that interest you., so, what do you do.
Are you sure you want to cancel your subscriptions?
Cancel my subscriptions
Don't cancel my subscriptions
Changing Country?
Accept terms & conditions.
It looks like you are changing your country/region of residence. In order to receive our emails, you must expressly agree. You can unsubscribe at any time by clicking the unsubscribe link at the bottom of our emails.
You appear to have previously removed your acceptance of the Terms & Conditions.

We noticed that you changed your country/region of residence; congratulations! In order to make this change, you must accept the Aggregage Terms and Conditions and Privacy Policy. Once you've accepted, then you will be able to choose which emails to receive from each site .
You must choose one option
Please choose which emails to receive from each site .
- Update All Sites
- Update Each Site
Please verify your previous choices for all sites
Sites have been updated - click Submit All Changes below to save your changes.
We recognize your account from another site in our network , please click 'Send Email' below to continue with verifying your account and setting a password.
You must accept the Privacy Policy and Terms & Conditions to proceed.
This is not me
Logistics and Supply Chain Case Studies
Review our case studies to see how we’ve helped major corporations turn logistical ideas into a reality., leading beverage distributor, penske logistics helps beverage distributor rapidly establish new warehousing operations.
When this distributor had to expand its operation quickly to counter a competitor, they turned to Penske to deploy a customized solution.
Baby2Baby Donation Transportation
Coordination and planning lead to successful transport of $3 million clothing donation.
Penske Logistics worked with Baby2Baby, a nonprofit that provides basic essentials to impoverished children, and Old Navy to transport $3M of clothing donations.
Luxury Product Manufacturer
Penske logistics reduces inventory shrinkage, improves overall inventory management.
A leading producer of fine luxury products required a partner who could improve their warehouse and distribution operations and reduce the theft.
Poultry Supplier
Transporting food items requires extra care and expertise.
Poultry producers, navigate a complex array of supply and delivery challenges to ensure their food arrives fresh, wholesome, and on-time.
Building Products Manufacturer
Customized fleet technology solution.
A leading building products manufacturer sought to streamline its supply chain operations and expand its fleet while improving visibility through the implementation of fleet management technology.
National Wholesale Distributor
A national wholesale distributor case study.
A national wholesale distributor of heating and air conditioning supplies was struggling to manage its complex supply chain and maintain high levels of customer service, which is a top priority.
Looping Process Ensures Continuous Production
Penske collaborated with Novelis to create a closed-loop recycling network that moves finished aluminum coils and transports scrap for new production.
A Global Manufacturer
Optimizing activities in the distribution center.
Penske worked with this global manufacturer to optimize its inventory routing and mode selection and to improve visibility to its supply chain.
Quick Service Restaurant
Food and beverage in-store delivery and warehousing.
Penske helped this restaurant chain get its supply chain fundamentals in place with the right logistics tools, truck driver training and warehousing solutions.
Tier 1 Automotive Component Supplier
Managing the inbound supply chain.
Penske helped this supplier minimize supply chain disruptions by designing a network that optimized mode selection, routing and analysis.
- Supply Chain Management
- Lead Logistics Provider
- Consulting Services
- Network Design
- Dedicated Contract Carriage
- Shared Dedicated Transportation
- Freight Management
- ClearChain ® Control
- Transportation Services
- Transportation Management Solutions
- Truckload Shipping Services
- Warehousing and Distribution
- Warehouse Design
- Warehouse Operations
- Multi-Client Warehousing
- Freight Brokerage
- Freight Forwarding
- Become a Carrier for Penske
Contact Penske Logistics about our services.
Improving warehouse operations—digitally
Warehouse operations are increasing in complexity with time. The growth of e-commerce has led to a proliferation of SKUs, and there’s an ever-growing need to delight customers by offering super-fast fulfillment. Technology is a factor as well: as new automation systems come onto the market, operations leaders must face the challenge of keeping pace and understanding which technologies apply and what kind of impact they can generate.
Worldwide, companies spend an estimated $350 billion a year on warehousing, and that number grows each year as pick sizes shrink and costs balloon, raising pressure not just on margins but also on service levels.
The need to improve both sides of the equation may be obvious, but the question is how. Trial-and-error is not an option: companies cannot simply shut down a warehouse so they can tinker with new layouts and workflows to see what works best.
But the better news is that they don’t have to. A few companies are already able to design and visualize their warehouse operations virtually via “digital twin” simulations. The simulations allow companies to create virtual models of their existing facilities, and then test different scenarios—no shutdowns required.
This digital warehouse-design approach lets companies experiment with different floor plans, workflows, and other variables to assess the overall impact virtually. Operations leaders can see the impact of changes in a wide range of factors, including the SKU mix, order and shipment profiles, seasonal demand spikes, productivity initiatives, automation options, and a host of other issues that impact warehouse performance. This level of detail allows warehouse designs to be optimized in advance, before anyone starts moving physical assets.
The process typically takes six to ten weeks. The revamped warehouse designs that result can help companies improve efficiency by 20 to 25 percent, before spending the money to test or pilot the changes (exhibit).
Would you like to learn more about our Operations Practice ?
The power of digital simulations.
Digital warehouse design has a wide range of applications, from productivity initiatives at existing facilities to mergers, warehouse consolidations, and new warehouse construction. Across all applications, however, the benefits are reasonably consistent: sizable savings in operating expenses from productivity improvement, as well as in capital expenses from optimizing the deployment of material-handling equipment, storage assets, and targeted, right-sized automation systems.
The approach removes bottlenecks to improve efficiency and effectiveness, and enables optimal slotting and product flows to meet service requirements at the lowest possible cost. Most important, digital warehouse design identifies the full potential of a given facility, rather than forcing companies to settle for incremental improvements to the as-is layout.
Critically, the process also enables companies to gauge the potential impact of mechanization and automation options across the entire spectrum of vendors and products on the market. These technologies can be powerful tools to reduce space and increase efficiency. But in some cases, incorrect or inappropriate automation can actually create more problems than it solves. Digital modeling lets companies see what is possible from a range of technologies and applications, before they make any investment decisions.
Transcending traditional improvements
Of course, most companies know they need to improve their warehouse operations. But they struggle to identify and make the needed upgrades, due to limited data and internal expertise. Quite simply, many companies lack the full set of capabilities needed to assess various warehouse improvement options and create a business case that incorporates capex investments and running costs.
Some rely on third-party logistics providers, but even those vendors often lack the breadth of expertise to see what is truly possible with alternative warehouse designs and operations. A related problem is that most traditional methods to design or revamp warehouses use computer-aided design software (CAD)—which is resource-heavy and time-consuming, and doesn’t allow companies to calculate the impact of new changes or anticipate second-order effects. Digital warehouse design, by contrast, offers a low-risk way to visualize and optimize layouts, allowing companies to rapidly identify real, feasible solutions that deliver quick impact.
For example, a North American manufacturer decided to consolidate several regional manufacturing and warehouse locations into a single campus, with separate buildings dedicated to manufacturing and warehousing. However, it faced several challenges, including capital constraints, insufficient warehouse space, and a need to move fast.
Instead of relying on traditional tools, the company used a digital warehouse-design approach to simulate various options across warehousing, kitting (assembly of related items into a single “kit” for shipment), and value-added operations. The digital tools allowed the company to develop detailed OPEX and CAPEX estimates for both manual and automated solutions, making it far easier to evaluate various business cases. In all, the company reduced planned capex by approximately 10 percent and operating expenses by more than 30 percent.
Digital warehouse design can also help companies rethink existing facilities. For example, another company deployed digital warehouse-design and simulation tools to optimize and revamp its operations in a warehouse currently in operation. It built models to test various layouts, material-handling-flow scenarios, picking methods, and targeted automation solutions.
Starting from an optimized slotting design, the digital twin analyzed historical orders to estimate the exact labor and equipment requirements by day of the week and by hour of the day. With accurate labor-staffing models, the company was able to choose the most optimal, modular design to implement during the transition. In addition, the company could define precise, engineered standards for each operation of the warehouse, and it could monitor daily labor and equipment performance once the new system was in place. This enabled the company to reduce annual operating expenses by 18 percent.
Similarly, one business had a central regional warehouse in Eastern Europe, with annual costs of several million dollars. By constructing a digital twin, the company analyzed the potential improvements from a proposed layout change (specifically, a picking zone that enabled one-step picking). Looking at both high-season and low-season volume, the company determined that it could reduce input costs by more than 25 percent.

Supply chain risk management is back
Foundational capabilities.
As with most technology, digital warehouse design is not a turnkey solution. To capture its full potential, companies must understand their strategy not only for today and tomorrow, but also well into the future—in terms of product portfolio, customer-order profiles, and other factors. Leadership teams must assess the implications of design changes on the supply-chain network as well. And success requires new capabilities in warehouse design—typically engineers who understand the range of variations and permutations for a space. Most organizations do not yet have internal people ready for these roles, and thus need to source that expertise externally.
As a practical matter, the simulation process must involve operations and warehouse managers—those with the deep day-to-day knowledge and real-world insights that can only come from direct experience. Because these experts will be tasked with implementing any changes to the warehouse after the simulation ends, their buy-in will be essential. The more they contribute during the early stages of the process, the more willing they are likely to be to forego old habits and work in new ways.
Last, companies need to plan for repeated changes over time. Optimizing warehouse performance is a process without a finish line—it must happen again and again, as market forces, technology, and consumer preferences continue to evolve. In fact, digital warehouse-simulation tools could become a new way of setting performance expectations, with the tools embedded as part of the day-to-day management of each distribution center. Estimating daily performance targets based on daily volume, mix, and staffing can help warehouse managers manage the shift’s performance more precisely than any other traditional, static approach to setting goals.
Companies face a growing need to improve their warehouse operations. Digital warehouse design is one clear means to help them do so. The process may be virtual, but the results generate a real impact on performance, providing an edge in an ever-more-complex warehousing landscape.
Stay current on your favorite topics
Felipe Bustamante is a consultant in McKinsey’s Miami office, Ashutosh Dekhne is a partner in the Dallas office, Jörn Herrmann is a senior expert in the Zürich office, and Vedang Singh is a consultant in the New Jersey office.
The authors wish to thank Aditi Brodie for her contribution to this article.
Explore a career with us
Related articles.

Digital supply-chain transformation with a human face
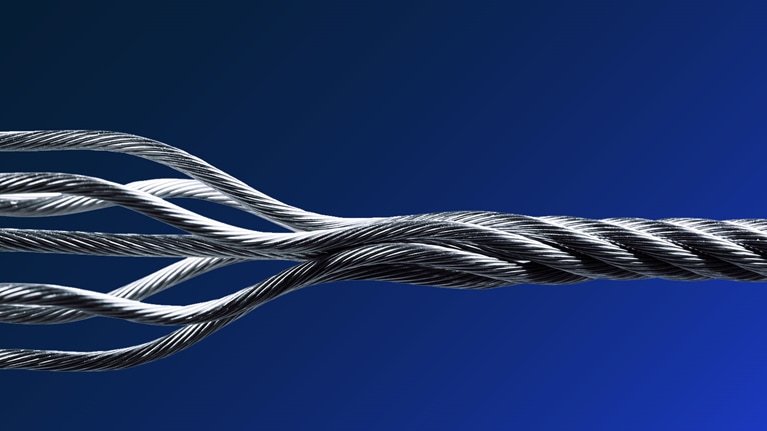
Industry’s fast-mover advantage: Enterprise value from digital factories
Warehouse Optimization Improves Efficiency 44%
Merchandise Warehouses takes its operations to the next level with high-density, deep lane racking and a pallet shuttle system
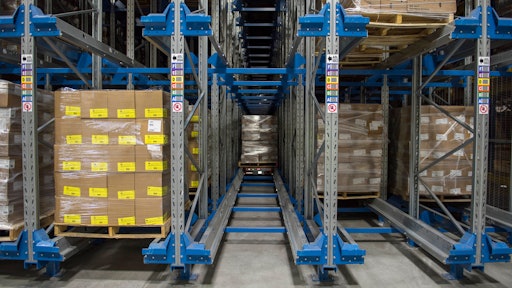
Merchandise Warehouse, a logistics provider of multi-temperature warehouse services, hasn’t stopped growing since its beginning as a 50,000-square-foot dry warehouse. An industry-wide shortage of cold storage facilities led the company to invest in cooler and freezer rooms in 1959, and now today the third-generation, family-owned warehouse has increased its facility size by eight times, with more than 400,000-square-feet of cooler and freezer space.
Consumer Demand Fuels Continued Cold Storage Growth
Yet while the company continued to excel, for years they relied on common warehouse operations. Traditional pallet racking was working, and as the old saying goes, “if it isn’t broke, don’t fix it.” However, continued growth was already pushing Merchandise Warehouse to its limit. The facility was busting at its seams with product, and the company’s customers were demanding even more room.
That growth, along with Merchandise Warehouse’s more aggressive pursuit of the latest technologies, presented the perfect opportunity to act on the company’s motto: “Take it to the next level.”
The Warehouse As A Competitive Advantage
“We’re always trying to be bigger, faster and stronger, and are looking for the latest and greatest tools that will help us achieve that,” says Seth Hamman, warehouse manager at Merchandise Warehouse. “When we were facing even more rapid growth, we saw it as an opportunity to find and implement those latest solutions that were revolutionary in the industry.”
Next Level, Efficient Solutions
Merchandise Warehouse knew what it needed: practical and affordable solutions that would help them be more efficient for their customers. The company started their search with who they knew and trusted: Raymond and Associated, an authorized Raymond Sales and Service Center.
“Associated and Raymond have always been leaders in the industry, so we knew we could trust them with this project,” explains Scott Whiting, vice president and general manager at Merchandising Warehouse. “ Plus, we have a lot of loyal Raymond fans in our warehouse, so we already had a great foundation for getting our team on board with new technologies.”
Merchandise Warehouse worked with Associated to assess the current operations and technologies and determine the best options for upgrading. They landed on high-density, deep lane racking and a pallet shuttle system from Raymond called Radioshuttle, which are both especially suited for cold storage.
Radioshuttle allows additional capacity and pallet positions, while also helping store and pick product faster with its pallet shuttle system. It’s efficient, yet has fewer opportunities for product damage on account of fewer touches required to move product. While Radioshuttle moves pallets through racking, the operator—typically using a reach truck—is free to do other work.
The Rise of High-Tech Cold Storage
Most importantly, Radioshuttle allowed for maximum storage utilization. By using the full height of the warehouse and high-density, deep lane racking, Merchandise Warehouse could better fill the facility with product.
The reduction in product touches was furthered with the integration of three conveyor systems: one moves product from the blast freezer through a de-spacing operation on to staging for lift truck put-away in the RadioShuttle system, and two others take product from the RadioShuttle storage freezer and stage it for truck loading.
Efficient Solutions with Immediate Results
The collaboration between Merchandise Warehouse, Associated and Raymond didn’t just work—it thrived.
“The companies worked together through the entire process, and in doing so, we were able to optimize our entire warehouse,” says Whiting. “We started seeing results faster than we even expected. We were seeing results in the first two months after implementing Radioshuttle and the racking.”
Merchandise Warehouse added more than 14,000 more pallet positions with the new solutions, and in doing so, was able to keep staffing levels the same. “Overall, the warehouse was more efficient—44 percent more efficient,” says Whiting. “What used to take seven man-hours to move product through the warehouse now takes about four. And what used to take 12 touches from receiving to shipping now only takes six. Fewer required touches means less opportunity for product damage.”
The Warehouse Manager’s Handbook
Outside of the storage, Merchandise Warehouse was also able to update its spacer removal process, cutting the time in half. Removing spacers from pallets used to take four hours, but now only takes two.
“Four or five years ago, I was dreaming of this kind of process improvement and upgrade. I was scribbling this stuff on napkins,” says Hamman. “It’s remarkable to see it come to life with the help of Radioshuttle and the new racking. We couldn’t have asked for a better experience or results.”
The Raymond Corporation

2024 Top Software & Tech Award: Nominations Open
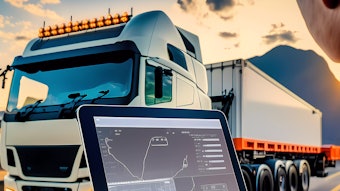
Emerging Technologies Bring New Opportunities to Freight Management
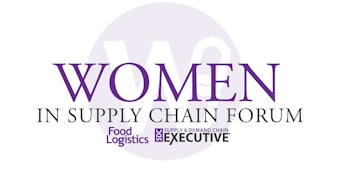
Women in Supply Chain Forum: Ulta Beauty, Uber Freight, Coca-Cola to Lead Content Sessions
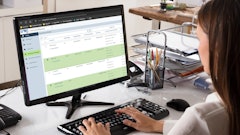
Carrier Transicold’s Lynx Fleet Expands Maintenance Dashboard for Refrigerated Fleets
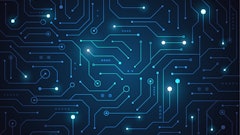
Wiliot Launches GenAI Tool for Insights into End-to-End Supply Chains
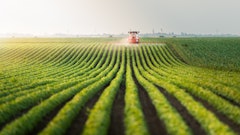
PHT Growth Fund to Acquire and Invest in Post-Harvest Cold Chain
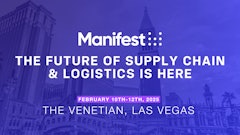
Manifest 2025 to See 150 Thought Leaders Take the Stage to Discuss End-to-End Supply Chain
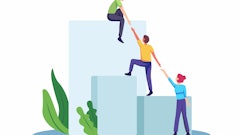
Turvo Appoints Vilas Madapurmath as Chief Technology Officer
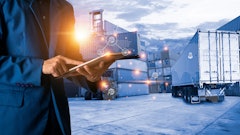
3 Theft Prevention Strategies to Catch a Cargo Thief
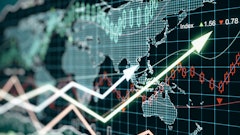
5 Ways 3PLs Impact Shortages and Disruptions in the Cold Chain
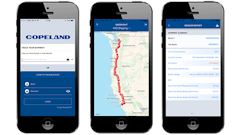
Real-Time Cargo Tracker for Better Cold Chain Connectivity
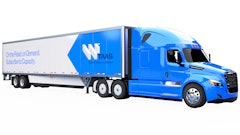
How Trailers-as-a-Service Can Reduce Complexity in Food Logistics
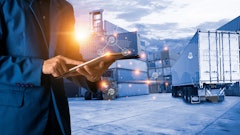
Cold Food Chain Track-and-Trace Revenues to Surpass $7B: Study
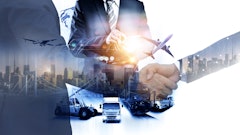
SCN Summit: Future of the Supply Chain
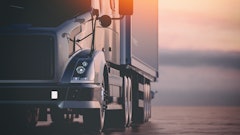
Truckload Volumes Slipped in June: Study
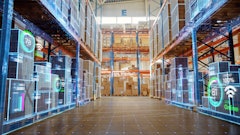
Aptean Acquires Principal Logistics Technologies, Expands Warehouse Management Capabilities
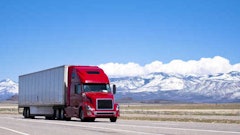
Trucker Tools’ Cold Chain Load Tracking Solutions Monitors Temperature-Sensitive Products
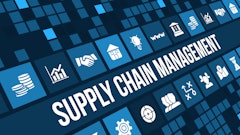
How Cold Chain Data Can Improve Supply Chain Performance
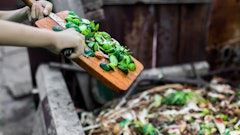
Fully Refrigerated Food Supply Chains Can Significantly Reduce Global Food Waste and Emissions: University of Michigan Study
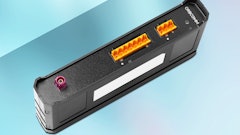
ORBCOMM Launches Next-Generation Reefer Container Monitoring Device
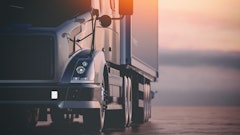
The Impact and Opportunities of SNAP Rule 26
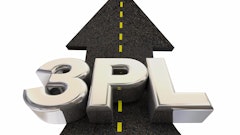
UPS to Sell Coyote Logistics to RXO, Inc.
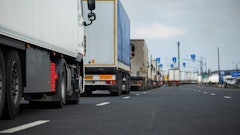
Streamlined Practices for Cross-Border Logistics
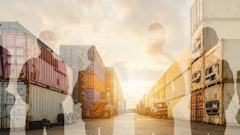
PCS Software Promotes CFO from Within
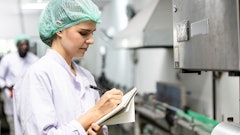
Prioritizing Sanitization in Cold Food Processing

Efficiency Equals Profitability in Cold Food Chain
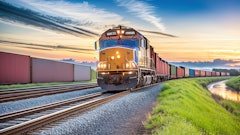
The Role of Rail Transport in Food Shipments
Build fully managed real-time data pipelines in minutes.
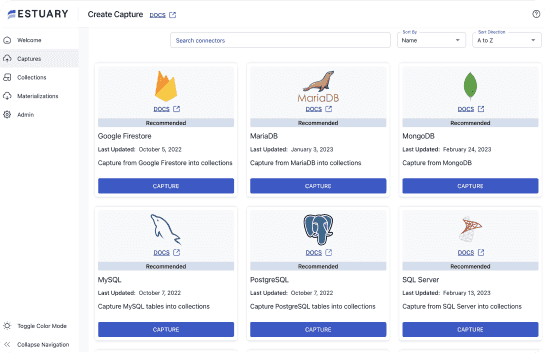
Replaced Fivetran with trouble-free CDC
Streaming CDC to Snowflake
Streaming CDC to BigQuery built 6x faster
Reliable CDC & outstanding support
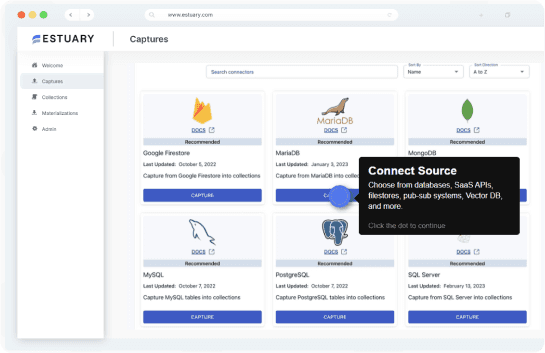
Real-Time Data Warehouse Examples (Real World Applications)
Discover how businesses are leveraging real-time data warehouses to gain actionable insights, make informed decisions, and drive growth..

Gone are the days when organizations had to rely on stale, outdated data for their strategic planning and operational processes. Now, real-time data warehouses process and analyze data as it is generated, helping overcome the limitations of their traditional counterparts. The impact of real-time data warehousing is far-reaching. From eCommerce businesses to healthcare providers, real-time data warehouse examples and applications span various sectors.
The significance of real-time data warehousing becomes even more evident when we consider the sheer volume of data being generated today. The global data sphere is projected to reach a staggering 180 zettabytes by 2025 .
With these numbers, it’s no wonder every company is looking for solutions like real-time data warehousing for managing their data efficiently. However, getting the concept of a real-time data warehouse, particularly when compared with a traditional data warehouse, can be quite intimidating, even for the best of us.
In this guide, with the help of a range of examples and real-life applications, we will explore how real-time data warehousing can help organizations across different sectors overcome the data overload challenge.
What Is A Real-Time Data Warehouse?
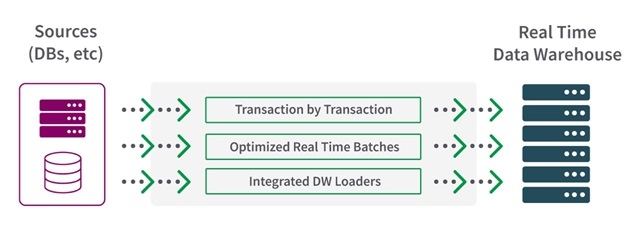
Image Source
A Real-Time Data Warehouse (RTDW) is a modern tool for data processing that provides immediate access to the most recent data. RTDWs use real-time data pipelines to transport and collate data from multiple data sources to one central hub, eliminating the need for batch processing or outdated information.
Despite similarities with traditional data warehouses, RTDWs are capable of faster data ingestion and processing speeds . They can detect and rectify errors instantly before storing the data, providing consistent data for an effective decision-making process.
- Real-Time Data Warehouse Vs Traditional Data Warehouse
Traditional data warehouses act as storage centers for accumulating an organization’s historical data from diverse sources. They combine this varied data into a unified view and provide comprehensive insights into the past activities of the organization. However, these insights are often outdated by the time they are put to use , as the data could be days, weeks, or even months old.
On the other hand, real-time data warehousing brings a significant enhancement to this model by continuously updating the data they house. This dynamic process provides a current snapshot of the organization’s activities at any given time, enabling immediate analysis and action.
Let’s look at some of the major differences between the two.
Complexity & Cost
RTDWs are more complex and costly to implement and maintain than traditional data warehouses. This is because they require more advanced technology and infrastructure to handle real-time data processing.
Decision-Making Relevance
Traditional data warehouses predominantly assist in long-term strategic planning. However, the real-time data updates in RTDWs make them suitable for both immediate, tactical decisions and long-term strategic planning.
Correlation To Business Results
Because of fresher data availability, RTDWs make it easier to connect data-driven insights with real business results and provide immediate feedback.
Operational Requirements
RTDWs demand constant data updates, a process that can be carried out without causing downtime in the data warehouse operations . Typically, traditional warehouses don't need this feature but it becomes crucial when dealing with data updates happening every week.
Data Update Frequency
While the lines between traditional data warehouses and real-time data warehouses are now blurred due to some data warehouses adopting streaming methods to load data, traditionally, the former updated their data in batches on a daily, weekly, or monthly schedule. As a result, the data some of these data warehouses hold may not reflect the most recent state of the business. In contrast, real-time data warehouses update their data almost immediately as new data arrives.
- 3 Major Types Of Data Warehouses
Let's take a closer look at different types of data warehouses and explore how they integrate real-time capabilities.
Enterprise Data Warehouse (EDW)
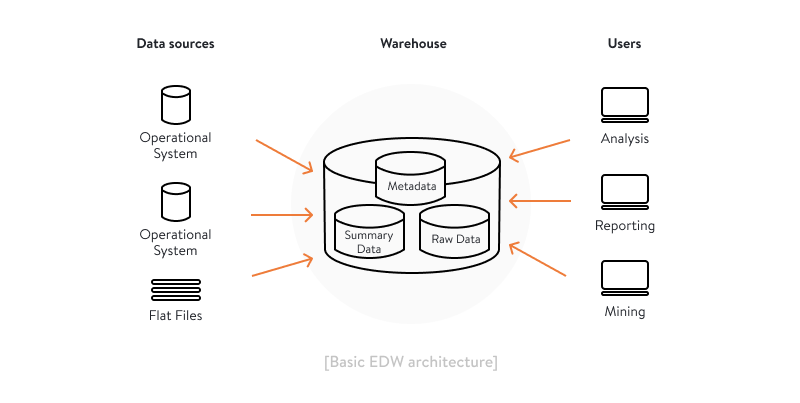
An Enterprise Data Warehouse (EDW) is a centralized repository that stores and manages large volumes of structured and sometimes unstructured data from various sources within an organization. It serves as a comprehensive and unified data source for business intelligence, analytics, and reporting purposes. The EDW consolidates data from multiple operational systems and transforms it into a consistent and standardized format.
The EDW is designed to handle and scale with large volumes of data . As the organization's data grows over time, the EDW can accommodate the increasing storage requirements and processing capabilities. It also acts as a hub for integrating data from diverse sources across the organization . It gathers information from operational systems, data warehouses, external sources, cloud-based platforms, and more.
Operational Data Store (ODS)
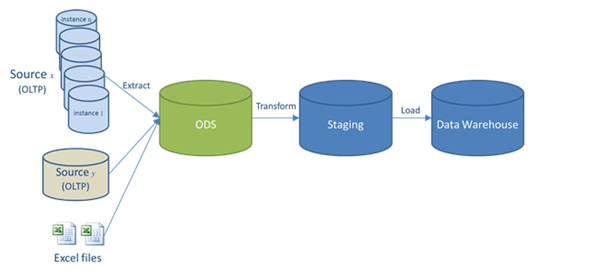
An Operational Data Store (ODS) is designed to support operational processes and provide real-time or near-real-time access to current and frequently changing data. The primary purpose of an ODS is to facilitate operational reporting, data integration, and data consistency across different systems.
ODS collects data from various sources, like transactional databases and external feeds, and consolidates it in a more user-friendly and business-oriented format. It typically stores detailed and granular data that reflects the most current state of the operational environment.
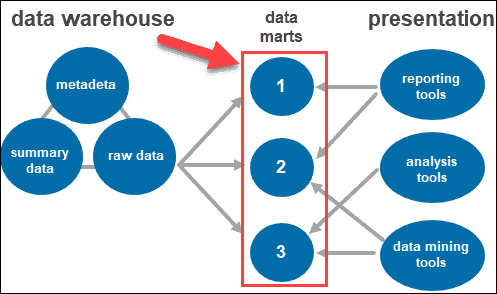
A Data Mart is a specialized version of a data warehouse that is designed to meet the specific analytical and reporting needs of a particular business unit , like sales, marketing, finance, or human resources.
Data Marts provide a more targeted and simplified view of data. It contains a subset of data that is relevant to the specific business area , organized in a way that facilitates easy access and analysis.
Data Marts are created by extracting, transforming, and loading (ETL) data from the data warehouse or other data sources and structuring it to support analytical needs. They can include pre-calculated metrics, aggregated data, and specific dimensions or attributes that are relevant to the subject area.
11 Applications Of Real-Time Data Warehouses Across Different Sectors
The use of RTDWs is now common across many sectors. The rapid access to information they provide significantly improves the operations of many businesses, from online retail to healthcare.
Let’s take a look at some major sectors that benefit from these warehouses for getting up-to-the-minute data.
In the dynamic eCommerce industry, RTDWs facilitate immediate data processing that is used to get insights into customer behavior, purchase patterns, and website interactions. This enables marketers to deliver personalized content, targeted product recommendations, and swift customer service . Additionally, real-time inventory updates help maintain optimal stock levels, minimizing overstock or stock-out scenarios.
RTDWs empower AI/ML algorithms with new, up-to-date data. This ensures models make predictions and decisions based on the most current state of affairs. For instance, in automated trading systems, real-time data is critical for making split-second buying and selling decisions.
Manufacturing & Supply Chain
RTDWs support advanced manufacturing processes such as real-time inventory management, quality control, and predictive maintenance . It provides crucial support for business intelligence operations. You can make swift adjustments in production schedules based on instantaneous demand and supply data to optimize resource allocation and reduce downtime.
RTDWs in healthcare help improve care coordination. It provides instant access to patient records, laboratory results, and treatment plans, improving care coordination . They also support real-time monitoring of patient vitals and provide immediate responses to critical changes in patient conditions.
Banking & Finance
In banking and finance, RTDWs give you the latest updates on customer transactions, market fluctuations, and risk factors . This real-time financial data analysis helps with immediate fraud detection, instantaneous credit decisions, and real-time risk management.
- Financial Auditing
RTDWs enable continuous auditing and monitoring to give auditors real-time visibility into financial transactions . It helps identify discrepancies and anomalies immediately to enhance the accuracy of audits and financial reports.
- Emergency Services
RTDWs can keep track of critical data like the location of incidents, available resources, and emergency personnel status . This ensures an efficient deployment of resources and faster response times, potentially saving lives in critical situations.
- Telecommunications
RTDWs play a vital role in enabling efficient network management and enhancing overall customer satisfaction. They provide immediate analysis of network performance, customer usage patterns, and potential system issues . This improves service quality, optimizes resource utilization, and proactive problem resolution.
- Online Gaming
RTDWs provide analytics on player behaviors, game performance, and in-game purchases to support online gaming platforms. This enables game developers to promptly adjust game dynamics, improve player engagement, and optimize revenue generation.
- Energy Management
In the energy sector, RTDWs provide instantaneous data on energy consumption, grid performance, and outage situations. This enables efficient energy distribution, quick response to power outages, and optimized load balancing.
- Cybersecurity
RTDWs are crucial for cybersecurity as they provide real-time monitoring of network activities and immediate detection of security threats. This supports swift countermeasures, minimizes damage, and enhances the overall security posture.
Real-Time Data Warehouse: 3 Real-Life Examples For Enhanced Business Analytics
To truly highlight the importance of real-time data warehouses, let’s discuss some real-life case studies.
- Case Study 1: Beyerdynamic
Beyerdynamic , an audio product manufacturer from Germany, was facing difficulties with its previous method of analyzing sales data . In this process, they extracted data from their legacy systems into a spreadsheet and then compiled reports, all manually. It was time-consuming and often caused inaccurate reports.
To overcome these challenges, Beyerdynamic developed a data warehouse that automatically extracted transactions from its existing ERP and financial accounting systems. This data warehouse was carefully designed to store standard information for each transaction, like product codes, country codes, customers, and regions.
They also implemented a web-based reporting solution that helped managers create their standard and ad-hoc reports based on the data held in the warehouse.
Supported by an optimized data model, the new system allowed the company to perform detailed sales data analyses and identify trends in different products or markets.
- Production plans could be adjusted quickly based on changing demand , ensuring the company neither produced excessive inventory nor missed out on opportunities to capitalize on increased demand.
- With the new system, the company could use real-time data for performance measurement and appraisal . Managers compared actual sales with targets by region, assessed the success of promotions, and quickly responded to any adverse variances.
- Sales and distribution strategies could be quickly adapted according to changing demands in the market. For instance, when gaming headphone sales started increasing in Japan, the company promptly responded with tailored promotions and advertising campaigns.
- Case Study 2: Continental Airlines
Continental Airlines is a major player in the aviation world. It faced significant issues because of old, manual systems. Their outdated approach slowed down decision-making and blocked easy access to useful data from departments like customer service, flight operations, and financials. Also, the lack of real-time data meant that decisions were often based on outdated information.
They devised a robust plan that hinged on 2 key changes: the ‘Go Forward’ strategy and a ‘real-time data warehouse’
- Go Forward Strategy: This initiative focused on tailoring the airline’s services according to the customer’s preferences. The concept was simple but powerful – understand what the customer wants and adapt services to fit that mold . In an industry where customer loyalty can swing on a single flight experience, this strategy aims to ensure satisfaction and foster brand loyalty.
- Real-Time Data Warehouse: In tandem with the new strategy, Continental also implemented an RTDW. This technological upgrade gave the airline quick access to current and historical data. The ability to extract insights from this data served as a vital reference point for strategic decision-making, optimizing operations, and enhancing customer experiences.
The new strategy and technology led to critical improvements:
- The airline could offer a personalized touch by understanding and acting on customer preferences. This raised customer satisfaction and made the airline a preferred choice for many.
- The introduction of the RTDW brought simplicity and efficiency to the company’s operations. It facilitated quicker access to valuable data which was instrumental in reducing the time spent on managing various systems. This, in turn, resulted in significant cost savings and increased profitability.
- Case Study 3: D Steel
D Steel, a prominent steel production company, was facing a unique set of challenges when they aimed to set up a real-time data warehouse to analyze their operations. While they tried to use their existing streams package for synchronization operations, several obstacles emerged.
The system was near real-time but it couldn't achieve complete real-time functionality. The load on the source server was significantly high and synchronization tasks required manual intervention.
More so, it lacked automation for Data Definition Language (DDL) , compatibility with newer technologies, and had difficulties with data consistency verification, recovery, and maintenance . These challenges pushed the steel company to seek a new solution.
The Solution
D Steel decided to implement real-time data warehouse solutions that enabled instant data access and analysis.
The new RTDWs system proved to be extremely successful as it resolved all previous problems. It provided:
- Real-time synchronization
- Implementing DDL automation
- Automated synchronization tasks
- Reduced the load on the source server
The system also introduced a unique function that compared current year data with that of the previous year and helped the company in annual comparison analysis.
- Enhancing Real-Time Data Warehousing: The Role of Estuary Flow
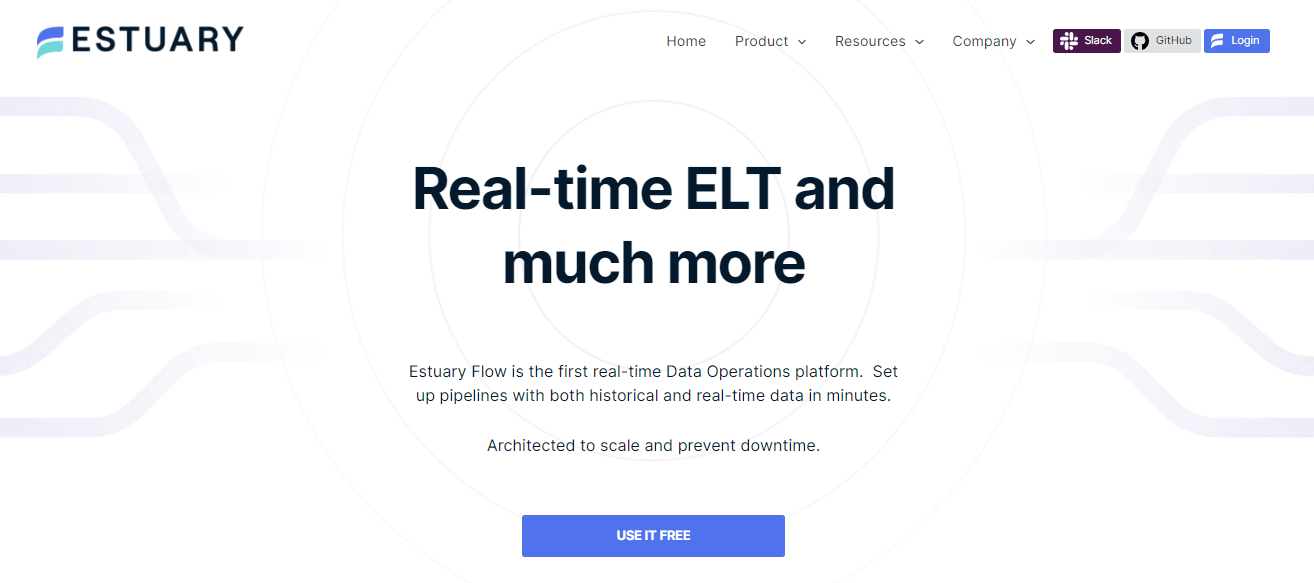
Estuary’s Flow is our data operations platform that binds various systems by a central data pipeline . With Flow, you get diverse systems for storage and analysis, like databases and data warehouses. Flow is pivotal in maintaining synchronization amongst these systems, ensuring that new data feeds into them continuously.
Flow utilizes real-time data lakes as an integral part of its data pipeline. This serves dual roles.
First, it works as a transit route for data and facilitates an easy flow and swift redirection to distinct storage endpoints. This feature also helps in backfilling data from these storage points.
The secondary role of the data lake in Flow is to serve as a reliable storage backbone . You can lean on this backbone without the fear of turning into a chaotic ‘data swamp.’
Flow assures automatic organization and management of the data lake . As data collections move through the pipeline, Flow applies different schemas to them as per the need.
Remember that the data lake in Flow doesn’t replace your ultimate storage solution. Instead, it aims to synchronize and enhance other storage systems crucial for powering key workflows , whether they're analytical or transactional.
As we have seen with real-time data warehouse examples, this solution transcends industry boundaries. Only those organizations that embrace real-time data warehousing to its fullest can unlock the true potential of their data assets.
While it can be a little tough to implement, the benefits of real-time data warehousing far outweigh the initial complexities, and the long-term advantages it offers are indispensable in today's data-driven world.
If you’re considering setting up a real-time data warehouse, investing in a top-notch real-time data ingestion pipeline like Estuary Flow should be your first step. Designed specifically for building real-time data management, Flow provides a no-code solution to synchronize your many data sources and integrate fresh data seamlessly. Signup for Estuary Flow for free and seize the opportunity today.
Start streaming your data for free
Table of Contents
- Manufacturing & Supply Chain
- Banking & Finance

Popular Articles
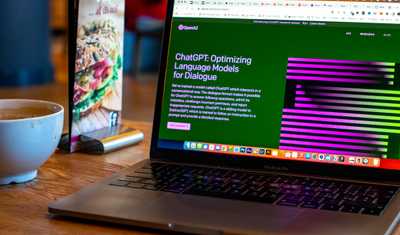
ChatGPT for Sales Conversations: Building a Smart Dashboard
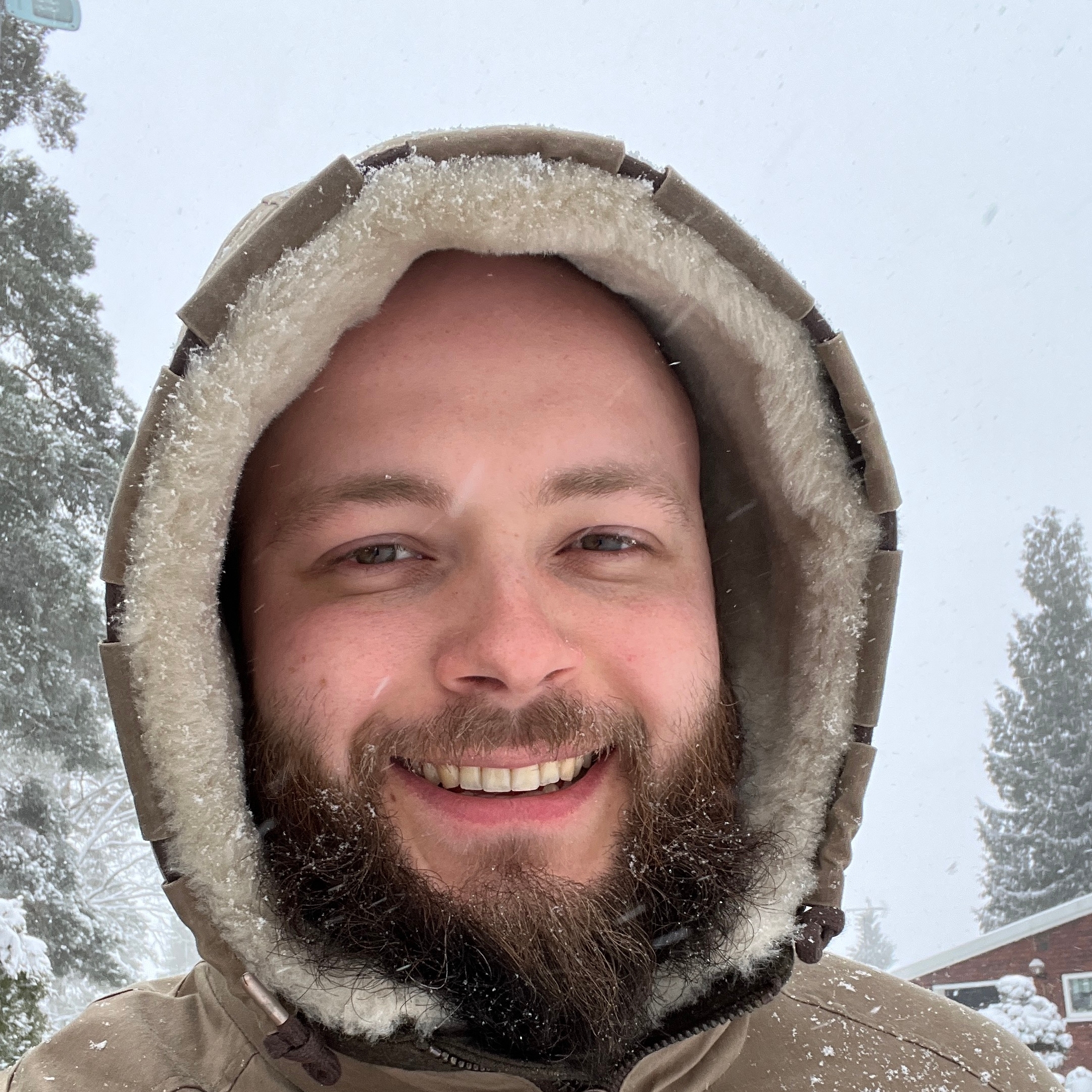
Why You Should Reconsider Debezium: Challenges and Alternatives
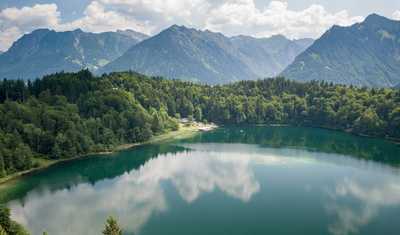
Don't Use Kafka as a Data Lake. Do This Instead.
Streaming pipelines., simple to deploy., simply priced..
Academia.edu no longer supports Internet Explorer.
To browse Academia.edu and the wider internet faster and more securely, please take a few seconds to upgrade your browser .
Enter the email address you signed up with and we'll email you a reset link.
- We're Hiring!
- Help Center
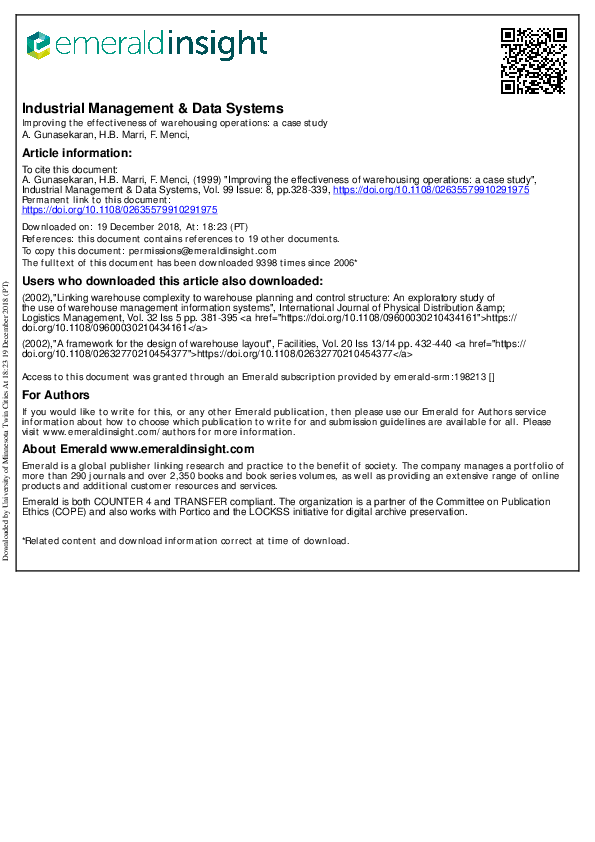
Improving the effectiveness of warehousing operations: a case study

Related Papers
adam mohd saifudin
Due to the globalization, warehousing activities ar e now becoming significantly crucial to ensure its effectiveness and efficiency of receiving, storing and handling of goods and materials in the manufact uring firms. Thus it creates the pivotal roles of logistics supp ort in exporting the goods to other destination and also as an excellent hub with accurate information of timely d elivery, receiving of materials and goods through e fficient MIS networking. The objectives of this paper are to see whether there is any relationship between the warehousing operation (WO) and warehouse efficiency (WE), to examine the mediating effect of warehousi ng MIS (WM) in the relationship between warehousing operations and warehouse efficiency and to determine whether there is any relationship between the wareh ousing operations and warehousing MIS. This paper would focus only on Small and Medium Enterprise (SMEs) Manufacturing sector in Peninsular Malaysia, register ed under the Small and Medium...
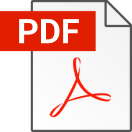
Arniel Ramos
This study investigates the relationship between the influential warehouse efficiency and warehousing operations, applied by the Small-Medium Enterprises (SMEs) manufacturing firms in Malaysia. These perspective research objectives are to determine whether there is any relationship between the warehousing operations, and warehousing Management Information System (MIS). It also examines the mediating effect of warehousing MIS in the relationship between warehousing attributes and warehouse efficiency. A quantitative method approach is applied in this research methodology. Three hypotheses have been proposed for the research with data collected from the survey of 182 SME manufacturing firm owners in Malaysia as listed in the SME Directory (2009). The findings indicate that the warehousing MIS significantly mediates and has an effect on the warehousing operations and their relationship with warehouse efficiency in the SME manufacturing firms. Theoretically, the research contributes to ...
Anna Corinna Cagliano , Alberto De Marco , Carlo Rafele
Purpose – To present an analysis of how different sourcing policies and resource usage affect the operational performance dynamics of warehouse processes. Design/methodology/approach – The System Dynamics methodology is used to model warehouse operations at the distribution centre of a leading fast-fashion vertical retailer. This case study includes a detailed analysis of the relationships between the flow of items through the warehouse, the assignment of staff, the inventory management policy, and the order processing tasks. Findings – Case scenario simulations are provided to define warehouse policies enabling increased efficiency, cost savings, reduced inventory, and shorter lead-times. Practical implications – The case study reaffirms that a flexible usage of human resources, outsourcing of selected warehouse operations, and sourcing from reliable manufacturers may result in important performance improvements for centralised warehousing. Originality/value – It is proved that System Dynamics is a valuable tool in the field of operations management not only to support strategic evaluations but also to execute a detailed analysis of logistical processes and make scenario-based dynamic decisions at the operational level. To cite this document: Anna Corinna Cagliano Alberto De Marco Carlo Rafele Sergio Volpe, (2011),"Using system dynamics in warehouse management: a fast-fashion case study", Journal of Manufacturing Technology Management, Vol. 22 Iss 2 pp. 171 - 188
mahmud abdurahman
As the supply chains get more complex, the variety of indicators and tools to measure warehouse performance has also increased. Furthermore, the metrics that are used for performance evaluation are assessed in different manners and hence there is not clear definition for some of these metrics. To address these issues, this literature review focuses on operational warehouse performance measurement, for which the warehouse managers need to carry out periodic analysis. Using the content analysis method, performance indicators are acquired from selected papers and are classified according to time, cost, quality and productivity dimensions. The contributions of this literature review are as follows: we present a synthesis of the literature on operational warehouse performance, we provide the definitions for the performance indicators and a framework to demonstrate their boundaries and, finally, based on the literature analysis, we also provide some discussions on current trends in warehouses and propose future research directions on warehouse performance evaluation.
Jerick Olpindo
Angappa Gunasekaran
Production Planning & Control
Journal of Business Strategy
Ugaraj Retna
Loading Preview
Sorry, preview is currently unavailable. You can download the paper by clicking the button above.
RELATED PAPERS
International Journal of Production Economics
Zillur Rahman
International Journal of Productivity and Quality Management
Dr. Faisal Talib
Benchmarking: An International Journal
Rajesh Singh
Alaa Aljunaidi
Ezeokwelume Obinna
International Journal of Advanced Operations Management
harwinder singh
Abate Teffera
Won Kin Chi
International Journal of Logistics Research and Applications
T. C. E. Cheng
Abhishek Jain
Management Research News
Erkan Bayraktar
Wubealie Wube
International Journal of …
Muhammad Subhan
Keshav Nandurkar
Int. J. Logistics Systems and Management
Hassan Qudrat-Ullah
Management Theory and Studies for Rural Business and Infrastructure Development
Mindaugas Samuolaitis
Gulgun Kayakutlu
Lakshika Gamini
RELATED TOPICS
- We're Hiring!
- Help Center
- Find new research papers in:
- Health Sciences
- Earth Sciences
- Cognitive Science
- Mathematics
- Computer Science
- Academia ©2024
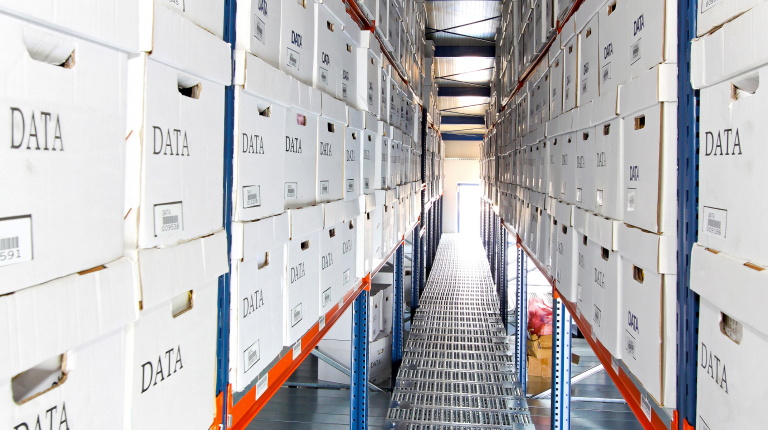
Practical Data Warehousing: Successful Cases
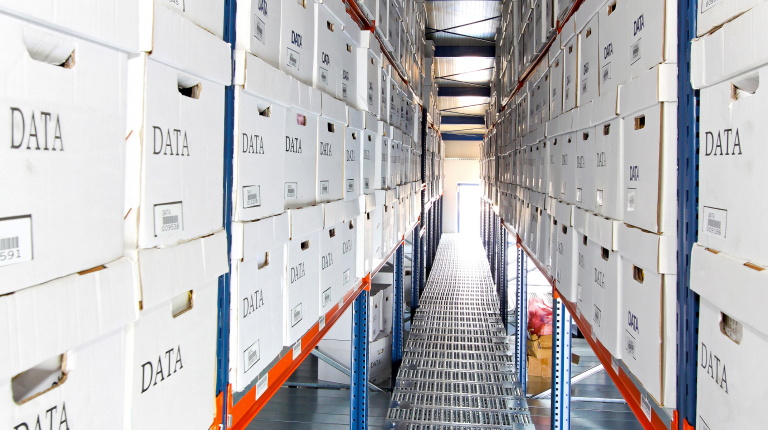
Table of contents:
No matter how smooth the plan may be in theory, practice will certainly make adjustments. Because each real case has its own characteristics, which in the general case cannot be taken into account. Let's see how the world's leading brands have adapted to their needs a well-known way of storing information — data warehousing. If you think this is your case, then arrange a call .
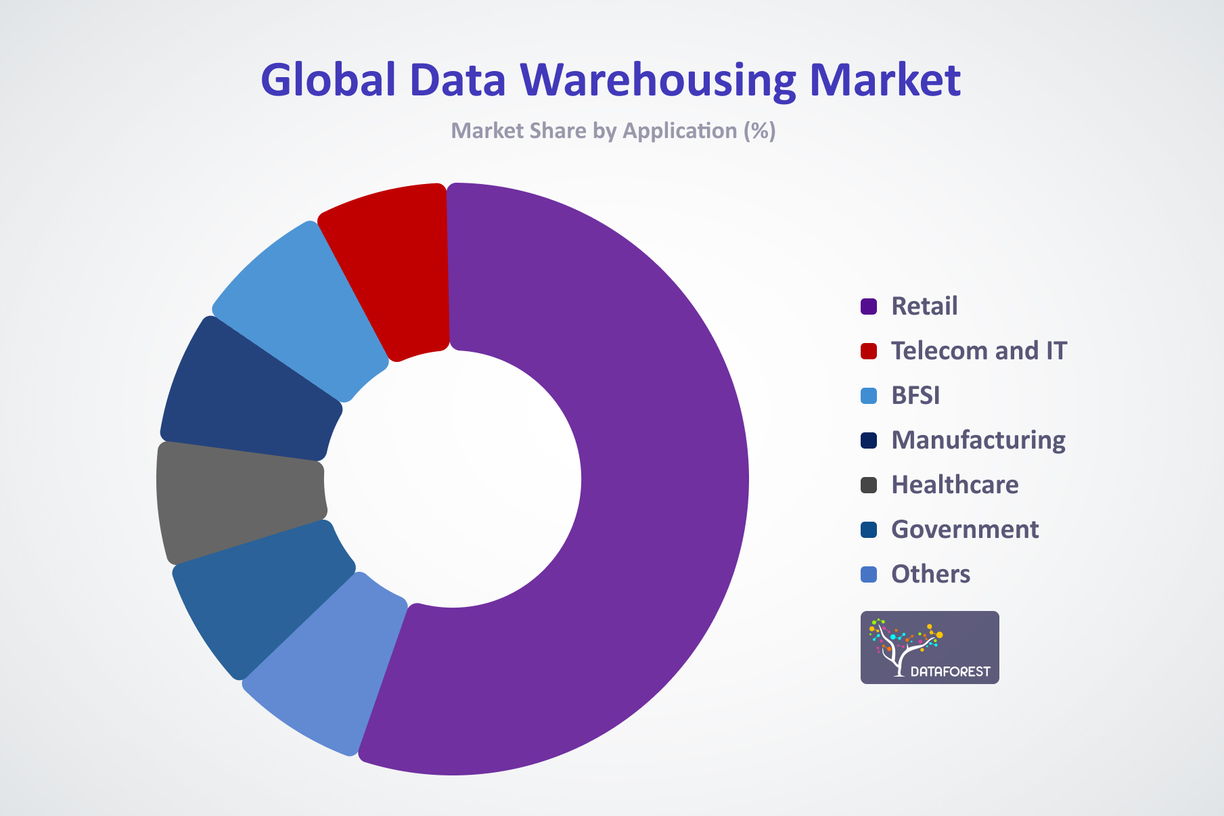
The Reason for Making Decisions
The need to make business decisions based on data analysis has long been beyond doubt. But to get this data, it needs to be collected, sorted and prepared for analytics .
Operating Supplement
supplier integrations
cost reduction
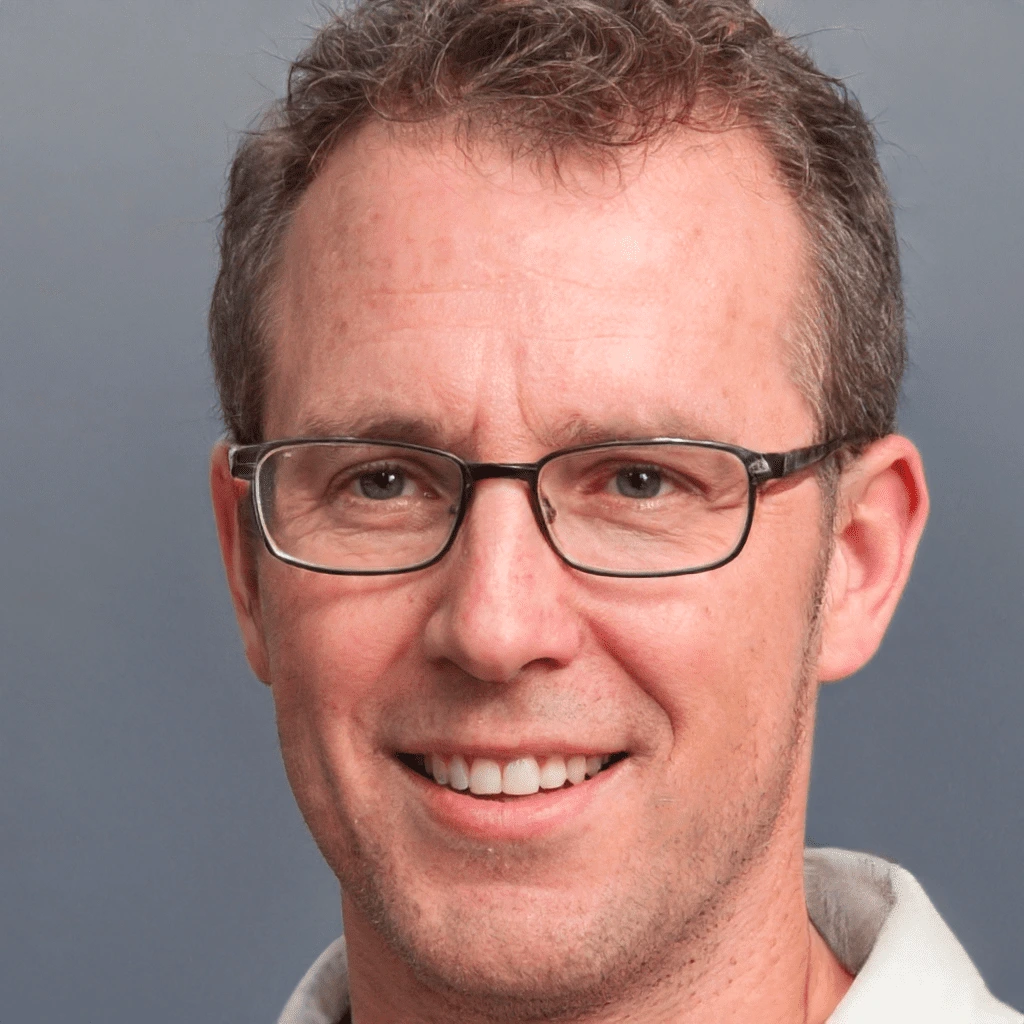
David Schwarz
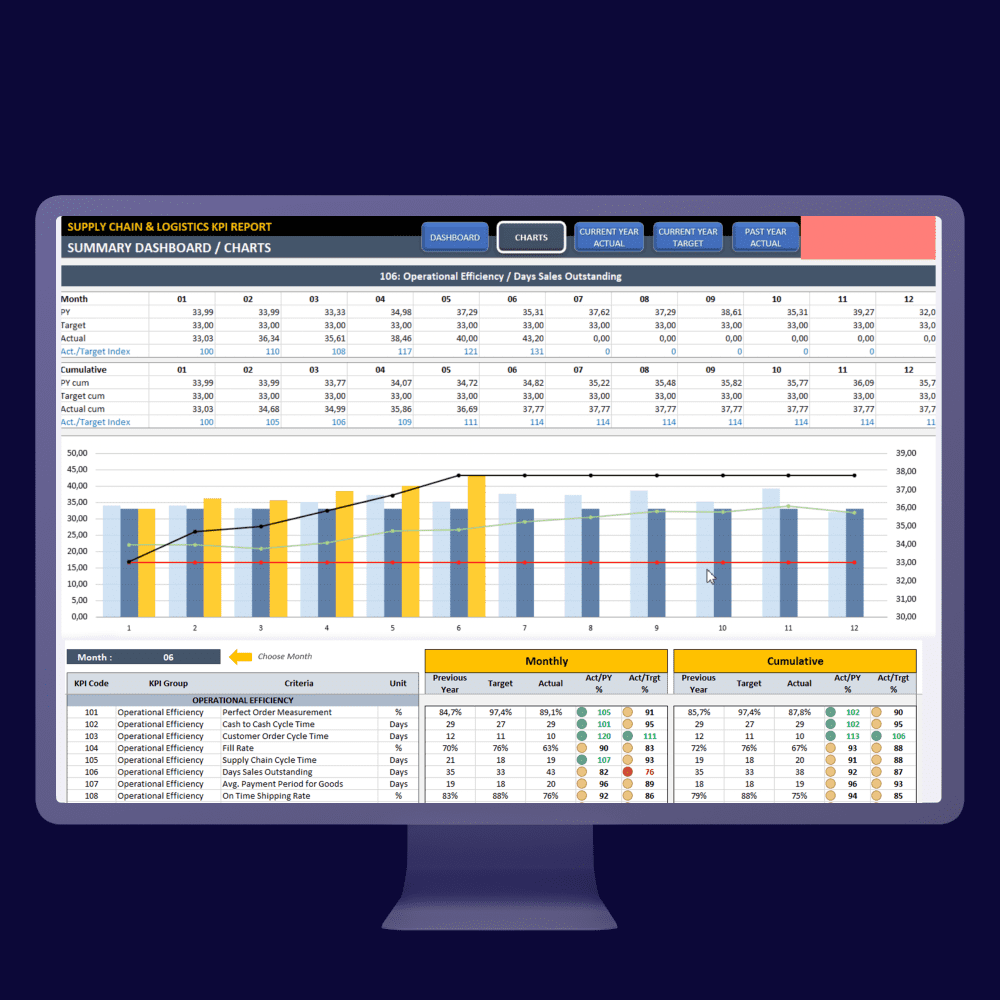
DATAFOREST has the best data engineering expertise we have seen on the market in recent years.
This is what data warehousing specialists do. To focus on the best performance, it makes sense to consider how high-quality custom assemblies came out of this constructor.
Data warehousing interacts with a huge amount of data
A data warehousing is a digital storage system that integrates and reconciles large amounts of data from different sources. It helps companies turn data into valuable information and make informed decisions based on it. Data warehousing combines current and historical data and acts as a single source of reliable information for business.
After raw data mining (extract, transform, load) info enters the warehouse from operating systems, such as an enterprise data resource planning system or a customer relationship management system. Sources also include databases, partner operational systems, IoT devices, weather apps, and social media. Infrastructure can be on-premises or cloud-based, with the latter option predominating in recent times.
Data warehousing is necessary not only for storing information, but also for processing structured and unstructured data: video, photos, sensor indicators. Some data warehousing options use built-in analytics and in-memory database data technology (info is stored in RAM rather than on a hard drive). This is necessary to access reliable data in real time.
After data is sorted, it is sent to data marts for further analysis by BI or data science .
Why consider data warehousing cases
Consideration of known options for data warehousing is necessary, first of all, in order not to keep making the same mistakes. Based on a working solution, you can improve your own performance. If you want to always be on the cutting edge of technology, book a call .
- When using data warehouses, executives access data from different sources, they do not have to decide blindly.
- Data warehousing is needed for quick retrieval and analysis. When using warehouses, you can quickly request large amounts of data without involving personnel for this.
- Before uploading to the warehouse, the system creates data cleansing tasks and puts them for further processing, ensuring converting the data into a consistent format for subsequent analyst reports.
- The warehouse contains large amounts of historical data and allows you to study past trends and issues to predict events and improve the business structure.
Blindly repeating other people's decisions is also impossible. Your case is unique and probably requires a custom approach. At best, well-known storage solutions can be taken as a basis. You can do it yourself, or you can contact DATAFOREST specialists for professional services. We have a positive experience and positive customer stories of data warehousing creating and operating.
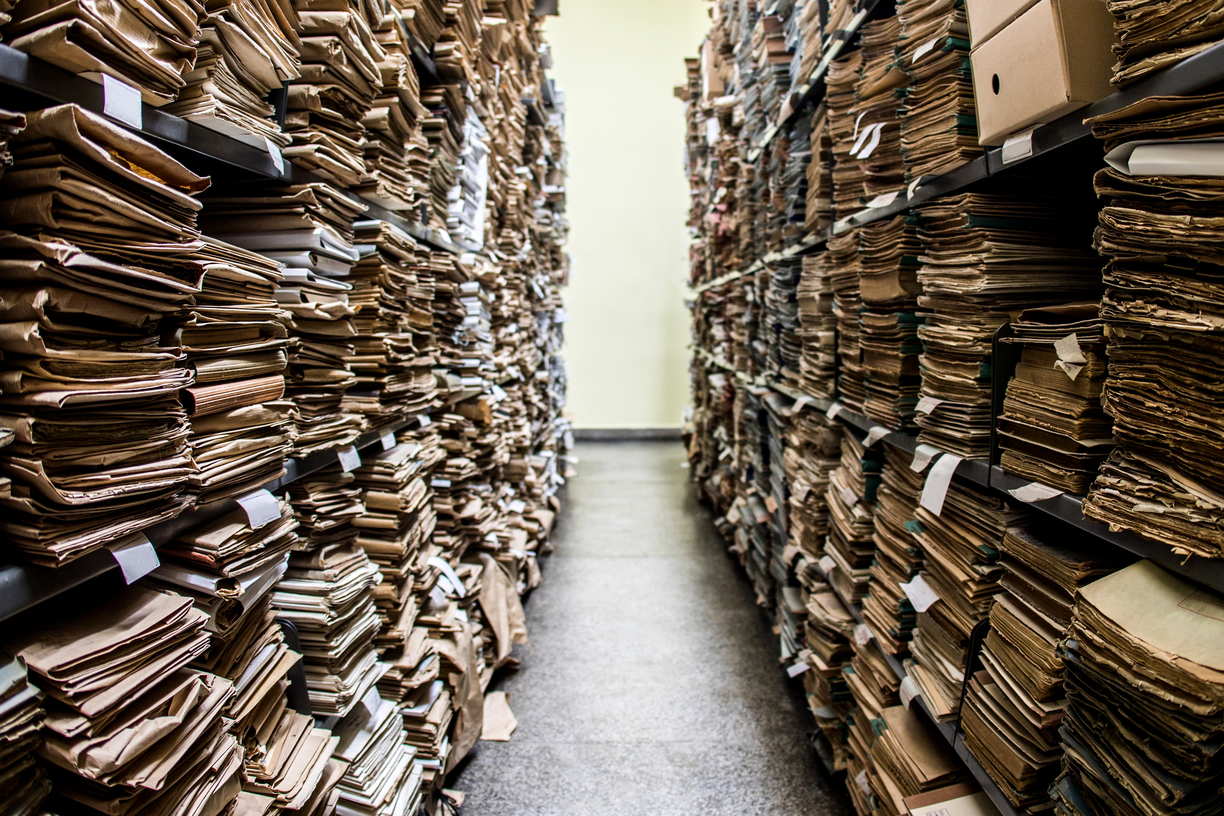
Case 1: How the Amazon Service Does Data Warehousing
Amazon is one of the world's largest and most successful companies with a diversified business: cloud computing, digital content, and more. As a company that generates vast amounts of data (including data warehousing services), Amazon needs to manage and analyze its data effectively.
Two main businesses
Amazon's data warehousing needs are driven by the company's vast and diverse data sources, which require sophisticated tools and technologies to manage and analyze effectively.
1. One of the main drivers of Amazon's business is its e-commerce platform , which allows customers to purchase a wide range of products through its website and mobile apps. Amazon's data warehousing needs in this area are focused on collecting, storing, and analyzing data related to customer behavior, purchase history, and other metrics. This data is used to optimize Amazon's product recommendations engine, personalize the shopping experience for individual customers, and identify growth strategies.
2. Amazon's other primary business unit is Amazon Web Services (AWS), which offers cloud computing managed services to businesses and individuals. AWS generates significant amounts of data from its cloud data infrastructure, including customer usage and performance data. To manage and analyze this modern data effectively, Amazon relies on data warehousing technologies like Amazon Redshift, which enables AWS to provide real-time analytics and insights to its customers.
3. Beyond these core businesses, Amazon also has significant data warehousing needs in digital content (e.g., video, music, and books). Amazon's advertising business relies on data analysis to identify key demographics and target ads more effectively to specific audiences.
By investing in data warehousing and analytics capabilities, Amazon through digital transformation can maintain its competitive edge and continue to grow and innovate in the years to come.
Do you want to streamline your data integration?
Obstacles on the way to the goal.
Amazon faced several specific implementation details and challenges in its data warehousing efforts.
• The brand needed to integrate data from various sources into a centralized data warehouse. It required the development of custom data pipelines to collect and transform data into a standard format.
• Amazon's data warehousing needs are vast and constantly growing, requiring a scalable solution. The company distributed data warehouse architecture center using technologies like Amazon Redshift, allowing petabyte-scale data storage and analysis.
• As a company that generates big data, Amazon would like to ensure that its data warehousing solution could provide real-time data analytics and insights. Achieving high performance requires optimizing data storage, indexing, and querying processes.
• Amazon stores sensitive customer data in its warehouse, prioritizing data security. To protect against security threats, the brand implements various security measures, including encryption, access controls, and threat detection.
• Building and maintaining a data warehousing solution can be expensive. Amazon leverages cloud-based data warehousing solutions (Redshift) to minimize costs, which provide a cost-effective, pay-as-you-go pricing model.
Amazon's data warehousing implementation required careful planning, significant investment in technology and infrastructure, and ongoing optimization and maintenance to ensure high performance and reliability.
Change for the better
When Amazon considered all the needs, found the right tools, and implemented a successful data warehouse, the company got the following main business outcomes:
• Improved data driven decision
• Better customer enablement
• Cost effective decision
• Improved performance
• Competitive advantage
• Scalability
Amazon's data warehousing implementation has driven the company's growth and success. Not surprisingly, a data storage service provider must understand data storage. The cobbler's children don't need to have no shoes.
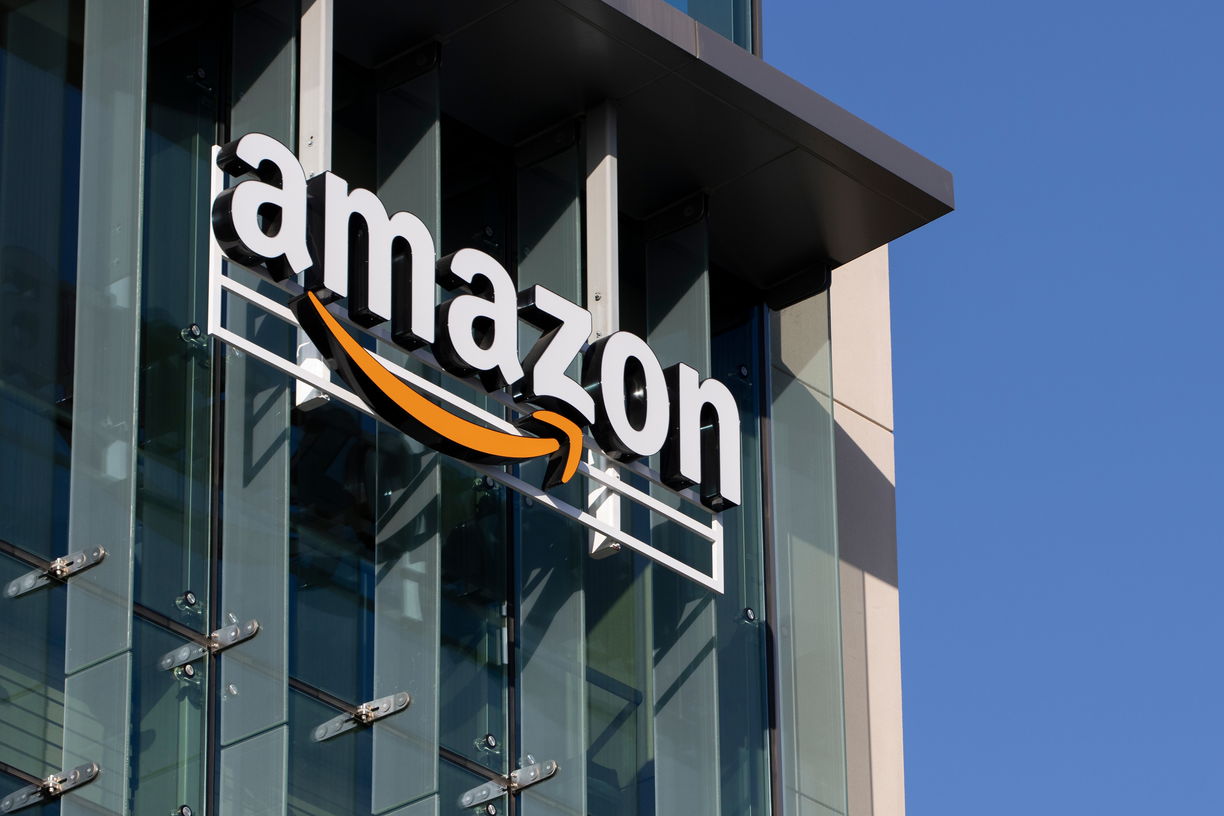
Case 2: Data Warehousing Adventure with UPS
United Parcel Services (UPS) is an American parcel delivery and supply chain management company founded in 1907 with an annual revenue of 71 billion dollars and logistics services in more than 175 countries. In addition, the brand distributes goods, customs brokerage, postal and consulting services. UPS processes approximately 300 million tracking requests daily. This effect was achieved, among others, thanks to intelligent data warehousing.
One mile for $50 million
In 2013, UPS stated that it hosted the world's largest DB2 relational database in two United States data centers for global operations. Over time, global operations began to increase, as did the amount of semi structured data. The goal was to use different forms of storage data to make better users business decisions.
One of the fundamental problems was route optimization. According to an interview with the UPS CTO, saving 1 mile a day per driver could save 1.5 million gallons of fuel per year or $50 million in total savings.
However, the data was distributed in DB2; some included repositories, some local, and some spreadsheets. UPS needed to solve the data infrastructure problem first and then optimize the route.
Four letters "V."
The big data ecosystem efficiently handles the four "Vs": volume, validity, velocity, and variety. UPS has experimented with Hadoop clusters and integrated its storage details and computing system into this ecosystem. They upgraded data warehousing and computing power to handle petabytes of data, one of UPS's most significant technological achievements.
The following Hadoop components were used:
• HDFS for storage
• Map Reduce for fast processing
• Kafka streaming
• Sqoop (SQL-to-Hadoop) for ingestion
• Hive & Pig for structured queries on unstructured data
• monitoring system for data nodes and names
But that's just speculation because, due to confidentiality, UPS didn't declassify the tools and technologies they used in their big data ecosystem.
Constellation of Orion
The result was a four-year ORION (On-Road Integrated Optimization and Navigation) route optimization project. Costs — about one billion dollars a year. ORION used the results to data stores and calculate big data and got analytics from more than 300 million data points to optimize thousands of routes per minute based on real-time information. In addition to the economic benefits, the Orion project shortened approximately 100 million shipping miles and a 100,000-ton reduction in carbon emissions.
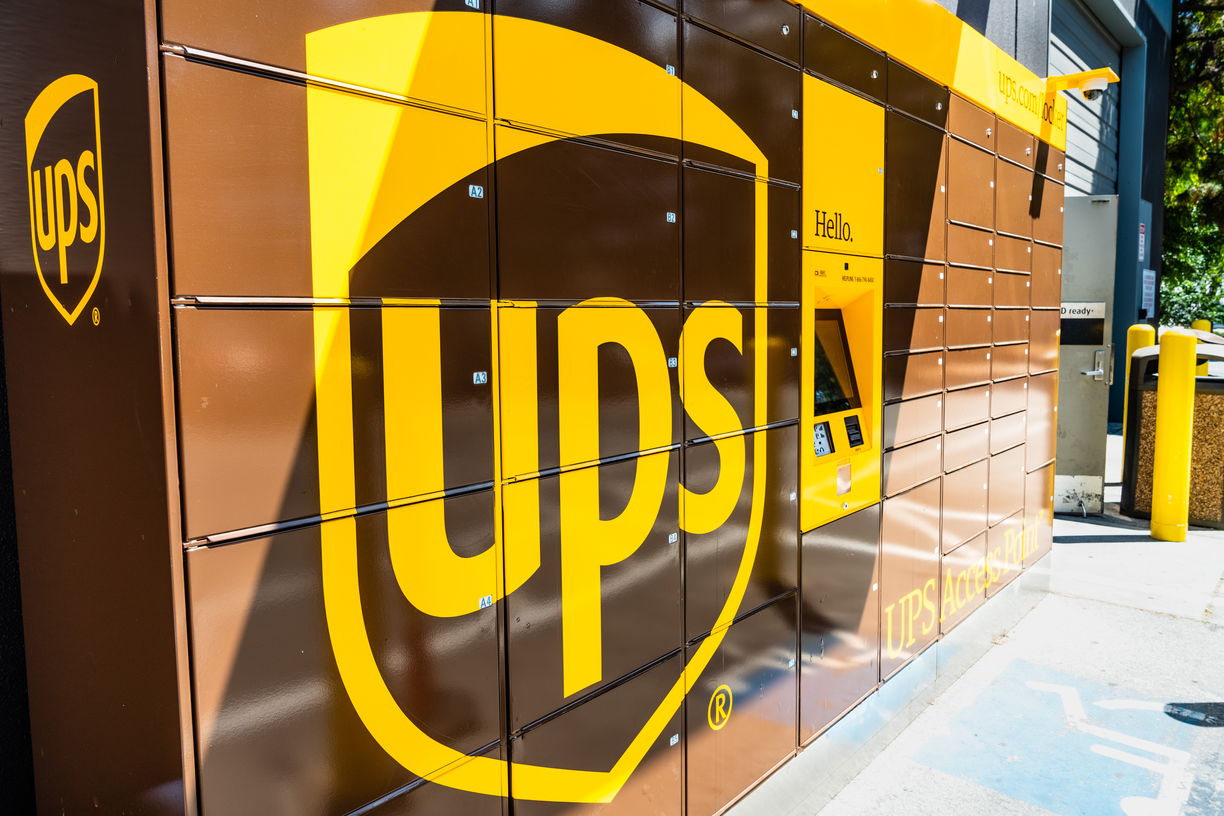
Case 3: 42 ERP Into One Data Warehouse
In general, the topic of specific cases of data warehousing implementation is sufficiently secret. There may be cases of consent and legitimate interests in the contracts. There are open-source examples of work, but the vast majority are on paid libraries. The subject is so relevant that you can earn money from it. Therefore, sometimes there are "open" cases, but the brand name is not disclosed.
Brand X needs help
World leader in industrial pumps, valves, actuators, controls, etc., needed help extracting data from disparate ERP systems. They wanted it from 42 ERP instances, standardized flat files, and collected all the information in one data warehouse. The ERP systems were from different vendors (Oracle, SAP, BAAN, Microsoft, PRMS) to complicate future matters.
The client also wanted a core set of metrics and a central dashboard to combine all the information from different locations worldwide. The project resulted from a surge in demand for corporate data from database management. The company knew its data warehousing needed a central repository for all data from its locations worldwide. Requests often came from top to bottom, and when an administrator required access to the correct data, there were logistical extracting problems. And the project gets started.
Are you interested in enhanced insights through data aggregation?
The foundation stone.
The hired third-party developer center has made a roadmap, according to which ERP data was taken from 8 major databases and placed in a corporate data warehouse. It entailed integrating 5 Oracle ERP instances with 3 SAP ERP. Rapid Marts have also been integrated into Oracle ERP systems to improve the project's progress.
One of the main challenges was the need for more standardization of fields or operational data definitions in ERP systems. To solve this problem, the contractor has developed a data service tool that allows access to the back end of the database and displays info suitably. Since then, the customer has known which fields to use and how to set them each time a new ERP instance is encountered. These data definition patterns were the project's foundation stone and completely changed how customer data is handled. It was a point to launch consent.
All roads lead to data warehousing
The company has one common and consistent way to obtain critical indicators. The long-term effect of the project is the ease of obtaining information. What was once a long and inconsistent process of getting relevant information at an aggregate level is now streamlined to store data in one central repository with one team controlling it.
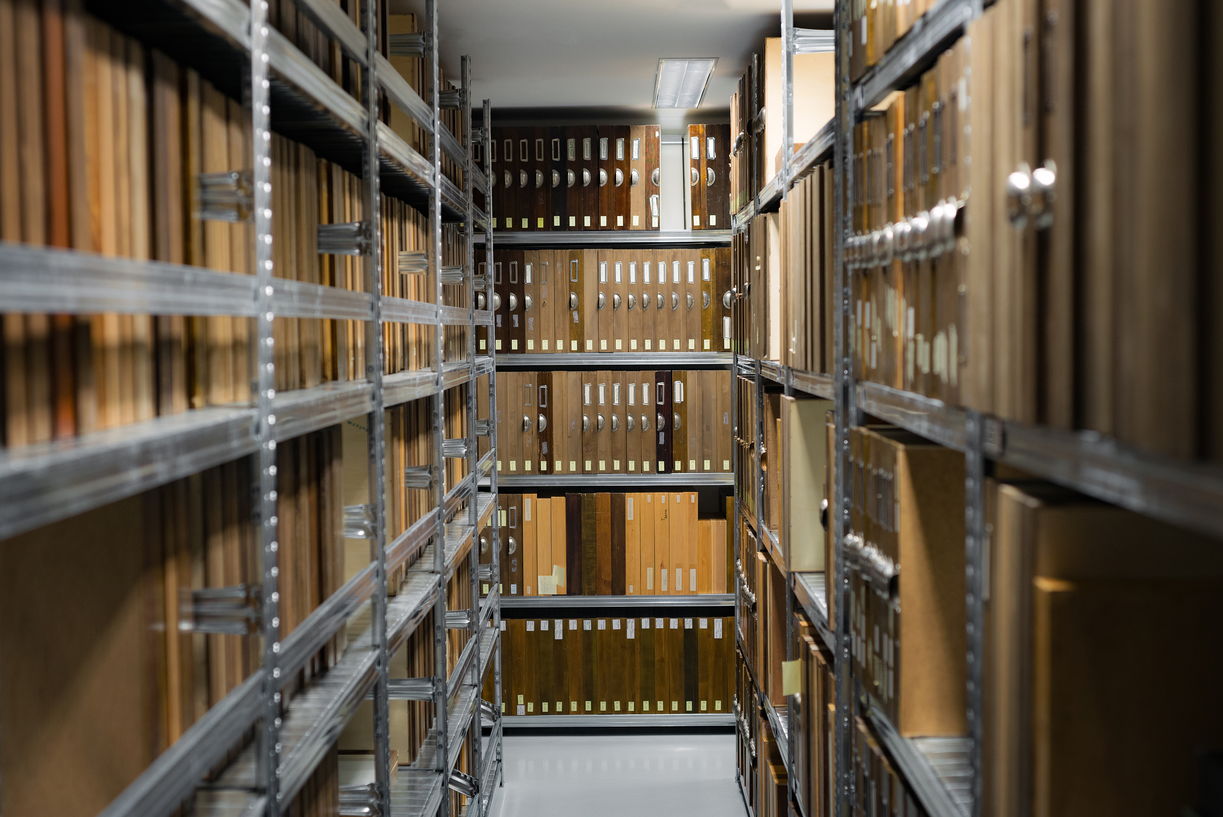
Data Warehousing: Different Cases — General Conclusions
Each data warehouse organization has unique methods and tools because business needs differ. In this case, data warehousing can be compared with a mosaic and a children's constructor. You can make different figures from the same parts, arranging the elements especially. And if one part is lost or broken, you need to make a new one or find another one and "process it with a rasp."
Generalities between different cases of data warehousing
There are several common themes and practices among successful data warehousing implementations, including:
• Successful data warehousing implementations start with clearly understanding the business objectives and how the warehouse (or data lake) can support those objectives.
• The data modeling process is critical to the success of data warehousing.
• The data warehouse is only as good as the data it contains.
• Successful data warehousing requires efficient data integration processes that can operate large volumes of data and ensure consistency and accuracy.
• Data warehousing needs ongoing performance tuning to optimize query performance.
• A critical factor in data warehousing is a user-friendly interface that makes it easy for end users to access the data and perform complex queries and analyses.
• Continuous improvement is essential to ensure the data warehouse remains relevant and valuable to the business.
Competent data warehousing implementations combine technical expertise and a deep understanding of business details and user needs.
Your case is not mentioned anywhere
When solving the problem of organizing data warehousing , one would like to find a description of the same case and do everything according to plan. But the probability of this event is negligible — you will have to adapt to the specifics of the customer's business and consider your knowledge and capabilities, as well as the technical and financial conditions of the project. Then it would help if you took a piece of the puzzle or parts of the constructor and built your data warehouse. Minus — you have to work. Plus — it will be your decision on data storage and only your implementation.
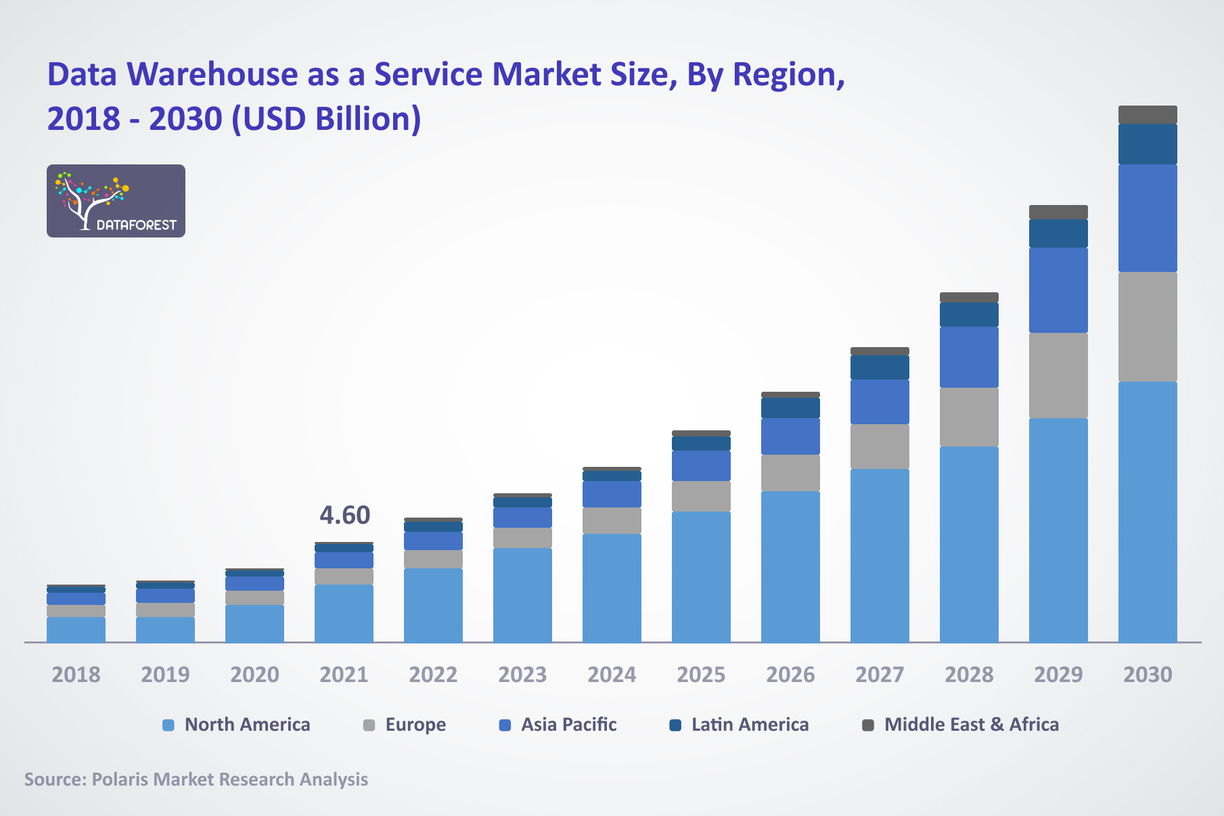
Data Warehousing Is Like a Trampoline
Changes in data warehousing , like any technological and methodological changes, are carried out to improve the data collection, storage, and analysis level. It takes the customer to a new level in his activity and the contractor — to his own. Like a jumper and a trampoline: separately, it is just a gymnast and just equipment, and in combination, they give a certain third quality — the possibility of a sharp rise.
If you are faced with the problem of organizing a new data warehousing system, or you are simply interested in what you read, let's exchange views with DATAFOREST.
What is the benefit of data warehousing for business?
A data warehouse is a centralized repository that contains integrated data from various sources and systems. Data warehousing provides several benefits for businesses: improved decision-making, increased efficiency, better customer insights, operational efficiency, and competitive advantage.
What is the definition of a successful data warehousing implementation?
The specific definition of a successful data warehouse implementation will vary depending on the goals of the organization and the particular use case for data warehousing. Some common characteristics are: meeting business requirements, high data quality, scalability, user adoption, and positive ROI.
What are the general considerations for implementing data warehousing?
Implementing data warehousing involves some general considerations: business objectives, data sources, quality and modeling, technology selection, performance tuning, user adoption, ongoing maintenance, and support.
What are the most famous examples of the implementation of data warehousing?
There are many famous examples of the implementation of data warehousing across industries:
• Walmart has one of the largest data warehousing implementations in the world
• Amazon's data warehousing solution is known as Amazon Redshift
• Netflix uses a data warehouse to store and analyze data from its streaming platform
• Coca-Cola has a warehouse to consolidate data from business units and analyze it
• Bank of America analyzes customer data by data warehousing to improve customer experience
What are the challenges while implementing data warehousing, and how to overcome them?
Based on the experiences of organizations that have implemented data warehousing, some common challenges and solutions are:
• Ensuring the quality of the data that is being stored and analyzed. You must establish data quality standards and implement data validation and cleansing by data types.
• Integrating from disparate data sources. Establishing a clear data integration strategy that considers the different data sources, formats, and protocols involved is vital.
• As the amount of data stored in a data warehouse grows, performance issues may arise. A brand should regularly monitor query performance and optimize the data warehouse to ensure that it remains efficient and effective.
• To ensure that sensitive data stored in the data warehouse is secure. It involves implementing appropriate measures such as access controls, encryption, and regular security audits. They are details of privacy security.
• Significant changes to existing processes and workflows. Solved by establishing a transparent change management process that involves decision-makers and users at all levels.
What is an example of how successful data warehousing has affected a business?
An example of how successful data warehousing has affected Amazon is its recommendation engine. It suggests products to customers based on their browsing and purchasing history. By using artificial intelligence and machine learning algorithms to analyze customer data, Amazon has improved the fully managed accuracy of its recommendations, resulting in increased sales and customer satisfaction.
What role does data integration play in data warehousing?
Data integration is critical to data warehousing, enabling businesses to consolidate and standardize data from multiple sources, ensure data quality, and establish effective data governance practices.
How are data quality and governance tracked in data warehousing?
Data quality and governance are tracked in data warehousing through a combination of data profiling, monitoring, and management processes and establishing data governance frameworks that define policies and procedures for managing data quality and governance. So, businesses can ensure that their data is accurate, consistent, and compliant with regulations, enabling effective decision-making and driving business applications' success.
Are there any measures to the benefits of data warehousing?
The benefits of business data warehousing can be measured through improvements in data quality, efficiency, decision-making, revenue and profitability, and customer satisfaction. By tracking these metrics, businesses can assess the effectiveness of their data warehousing initiatives and make informed decisions about future investments in data management and analytics with cloud services.
How to avoid blunders when warehousing data?
By following the best practices, businesses can avoid common mistakes, minimize the risk of blunders when warehousing data, and ensure their data warehousing initiatives are successful and practical to be analyzed with business intelligence.
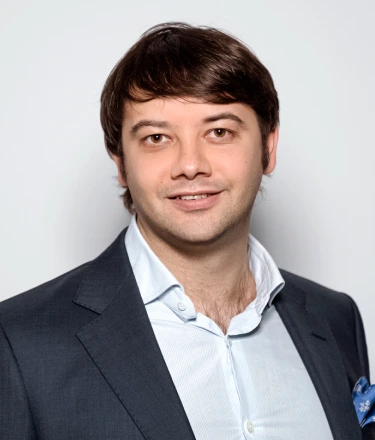
Aleksandr Sheremeta
Get More Value!
You will get from us best tailored content that will help your business grow.
Thanks for your submission!
latest posts
Openai o1: train ai to act and respond, traditional bi vs. self-service bi: a clash of approaches, marketing, sales and customer service: harness for generative ai, media about us, when it comes to automation, choosing the right partner has never been more important, 15 most innovative database startups & companies, 10 best web development companies you should consider in 2022, try to trying.
Never give up
We love you to
People like this
Success stories
Web app for dropshippers.
hourly users
Shopify stores
Financial Intermediation Platform
model accuracy
timely development
E-commerce scraping
manual work reduced
pages processed daily
DevOps Experience
QPS performance
Supply chain dashboard
system integrations
More publications
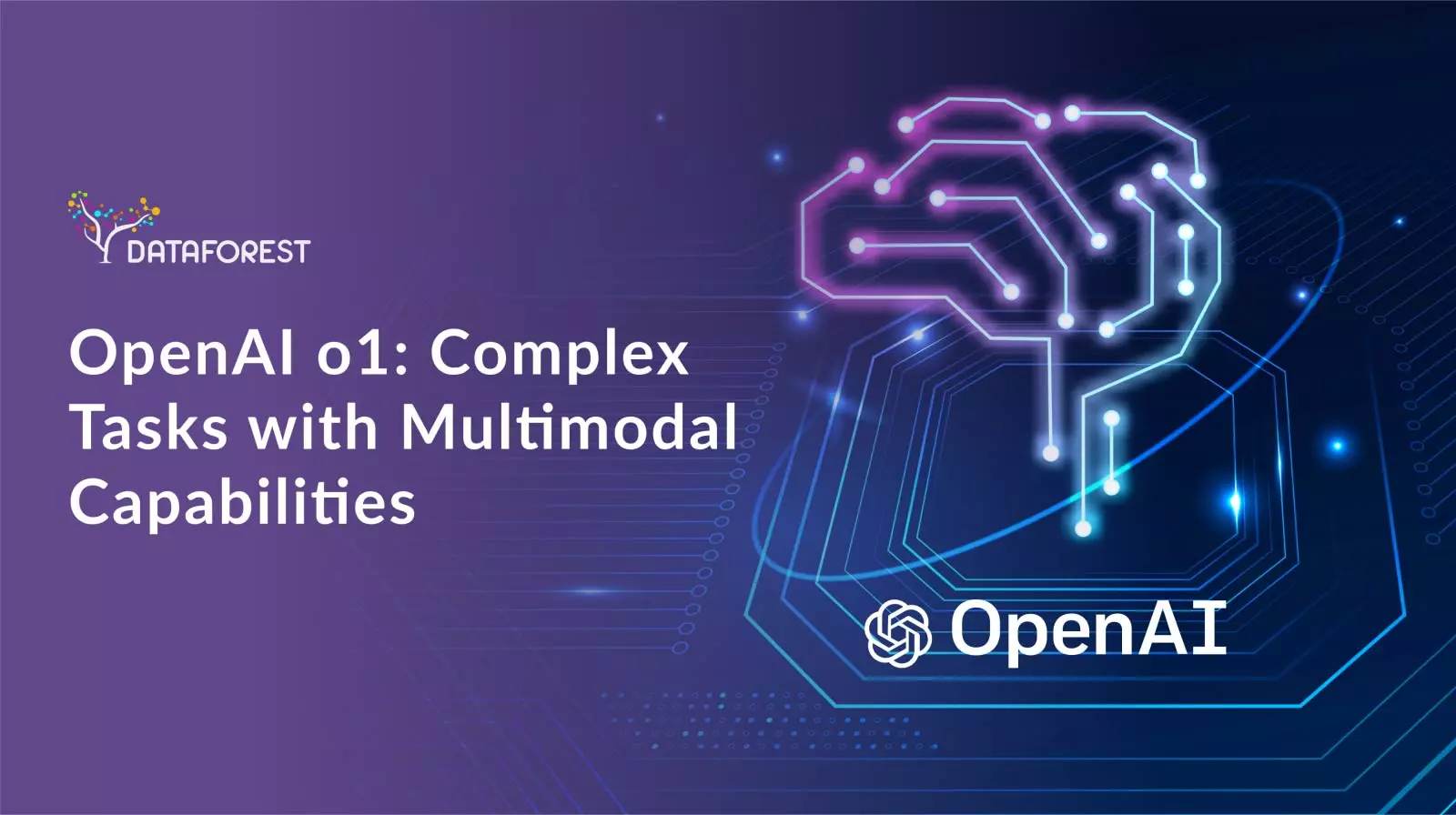
Let data make value
We’d love to hear from you.
Share the project details – like scope, mockups, or business challenges. We will carefully check and get back to you with the next steps.
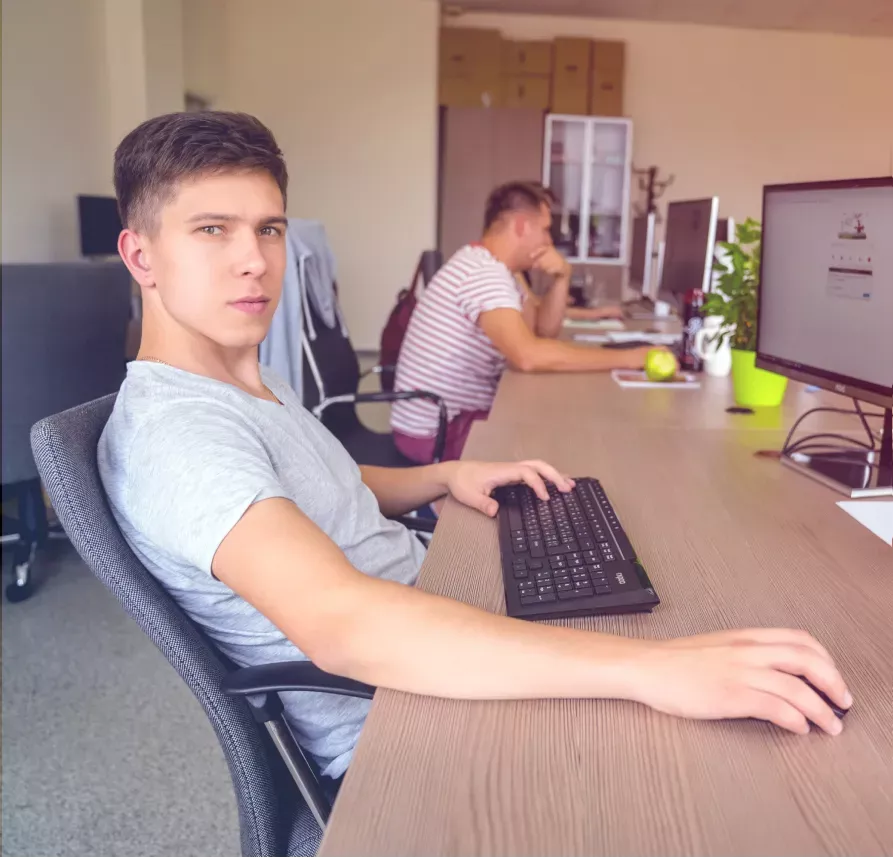
Stay a little longer and explore what we have to offer!
Information
- Author Services
Initiatives
You are accessing a machine-readable page. In order to be human-readable, please install an RSS reader.
All articles published by MDPI are made immediately available worldwide under an open access license. No special permission is required to reuse all or part of the article published by MDPI, including figures and tables. For articles published under an open access Creative Common CC BY license, any part of the article may be reused without permission provided that the original article is clearly cited. For more information, please refer to https://www.mdpi.com/openaccess .
Feature papers represent the most advanced research with significant potential for high impact in the field. A Feature Paper should be a substantial original Article that involves several techniques or approaches, provides an outlook for future research directions and describes possible research applications.
Feature papers are submitted upon individual invitation or recommendation by the scientific editors and must receive positive feedback from the reviewers.
Editor’s Choice articles are based on recommendations by the scientific editors of MDPI journals from around the world. Editors select a small number of articles recently published in the journal that they believe will be particularly interesting to readers, or important in the respective research area. The aim is to provide a snapshot of some of the most exciting work published in the various research areas of the journal.
Original Submission Date Received: .
- Active Journals
- Find a Journal
- Proceedings Series
- For Authors
- For Reviewers
- For Editors
- For Librarians
- For Publishers
- For Societies
- For Conference Organizers
- Open Access Policy
- Institutional Open Access Program
- Special Issues Guidelines
- Editorial Process
- Research and Publication Ethics
- Article Processing Charges
- Testimonials
- Preprints.org
- SciProfiles
- Encyclopedia
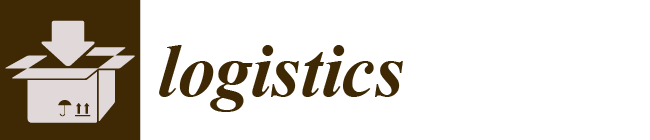
Article Menu

- Subscribe SciFeed
- Recommended Articles
- Author Biographies
- Google Scholar
- on Google Scholar
- Table of Contents
Find support for a specific problem in the support section of our website.
Please let us know what you think of our products and services.
Visit our dedicated information section to learn more about MDPI.
JSmol Viewer
Factory logistics improvement: a case study analysis of companies in northern thailand, 2022–2024.
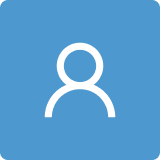
1. Introduction
2. background, 2.1. industries in thailand, 2.2. logistics in thailand, 2.3. industries in northern thailand, 3. methodology, 4. results and case study, 4.1. transportation management, 4.1.1. vehicle routing solution, 4.1.2. transportation management system (tms), 4.2. warehouse and inventory management, 4.2.1. inventory model application.
- Analysis of order history.
- Implementation of Pareto/ABC classification to categorize materials based on their value, volume, and frequency of use [ 37 ].
- Application of inventory models, specifically the Economic Order Quantity (EOQ) model, incorporating Reorder Point (ROP) and Safety Stock (SS) calculations [ 38 ].
4.2.2. Warehouse Layout Design
- Redesign of warehouse layout based on product category and significance using Pareto/ABC classification.
- Determination of stock levels for A-level raw materials using Safety Stock (SS) calculations.
- Introduction of visual control concepts to enhance warehouse operations (as illustrated in Figure 4 ).
4.2.3. Warehouse Management System (WMS)
4.2.4. automation in material handing, 4.3. logistics administrative management, 4.3.1. forecasting and demand planning, 4.3.2. logistics communication, 4.3.3. outsourcing, 5. discussion and conclusions.
- Developing more adaptive and scalable logistics improvement methodologies that can accommodate businesses of varying sizes and technological readiness levels.
- Investigating the long-term sustainability of logistics improvements, particularly in the face of changing market conditions and technological advancements.
- Exploring the potential of emerging technologies, such as artificial intelligence and blockchain, in facilitating more seamless integration across logistics functions.
- Examining the role of organizational culture and change management in the successful implementation of logistics improvements.
- For policymakers, the results underscore the importance of continued support for logistics improvement initiatives, particularly in developing economies. The triple-helix model demonstrated here could serve as a blueprint for similar programs in other regions or countries.
- Industry practitioners can benefit from the practical insights and methodologies presented, adapting them to their specific contexts to achieve logistics optimization.
- Academic researchers can build upon this work to further explore the interconnections between various logistics functions and develop more integrated theoretical models of logistics performance.
- Technology providers may find opportunities to develop more tailored solutions that address the specific challenges faced by businesses in implementing logistics improvements.
Author Contributions
Data availability statement, acknowledgments, conflicts of interest.
- Banomyong, R.; Grant, D.B.; Varadejsatitwong, P.; Julagasigorn, P. Developing and validating a national logistics cost in Thailand. Transp. Policy 2022 , 124 , 5–19. [ Google Scholar ] [ CrossRef ]
- Christopher, M. Logistics & Supply Chain Management ; Pearson: London, UK, 2016. [ Google Scholar ]
- Abdirad, M.; Krishnan, K. Industry 4.0 in logistics and supply chain management: A systematic literature review. Eng. Manag. J. 2021 , 33 , 187–201. [ Google Scholar ] [ CrossRef ]
- Chaopaisarn, P.; Huynh, M. Internet of Things (IoT) and Robotics in Agriculture: Present State and Challenges. Adv. Sci. Technol. Eng. Syst. J. 2019 , 4 , 229–234. [ Google Scholar ]
- Tsolaki, K.; Vafeiadis, T.; Nizamis, A.; Ioannidis, D.; Tzovaras, D. Utilizing machine learning on freight transportation and logistics applications: A Review. ICT Express 2023 , 9 , 284–295. [ Google Scholar ] [ CrossRef ]
- Uskenbayeva, R.; Nalgozhina, N.; Berkaliyeva, M. Introduction and evaluation problem of BPM and RPA approaches in modern Logistics systems. Sci. J. Astana IT Univ. 2022 , 12 , 45–54. [ Google Scholar ] [ CrossRef ]
- de Oliveira, A.V.; Pimentel, C.M.O.; Godina, R.; Matias, J.C.D.O.; Garrido, S.M.P. Improvement of the Logistics Flows in the Receiving Process of a Warehouse. Logistics 2022 , 6 , 22. [ Google Scholar ] [ CrossRef ]
- Woschank, M.; Dallasega, P. The impact of logistics 4.0 on performance in manufacturing companies: A pilot study. Procedia Manuf. 2021 , 55 , 487–491. [ Google Scholar ] [ CrossRef ]
- Richnák, P. Current Trend of Industry 4.0 in Logistics and Transformation of Logistics Processes Using Digital Technologies: An Empirical Study in the Slovak Republic. Logistics 2022 , 6 , 79. [ Google Scholar ] [ CrossRef ]
- Khan, S.; Singh, R.; Haleem, A.; Dsilva, J.; Ali, S.S. Exploration of Critical Success Factors of Logistics 4.0: A DEMATEL Approach. Logistics 2022 , 6 , 13. [ Google Scholar ] [ CrossRef ]
- da Silva, R.M.; Frederico, G.F.; Garza-Reyes, J.A. Logistics Service Providers and Industry 4.0: A Systematic Literature Review. Logistics 2023 , 7 , 11. [ Google Scholar ] [ CrossRef ]
- Ferreira, B.; Reis, J. A Systematic Literature Review on the Application of Automation in Logistics. Logistics 2023 , 7 , 80. [ Google Scholar ] [ CrossRef ]
- Zonta, T.; Da Costa, C.A.; da Rosa Righi, R.; de Lima, M.J.; da Trindade, E.S.; Li, G.P. Predictive maintenance in the Industry 4.0: A systematic literature review. Comput. Ind. Eng. 2020 , 150 , 106889. [ Google Scholar ] [ CrossRef ]
- Abidi, M.H.; Mohammed, M.K.; Alkhalefah, H. Predictive Maintenance Planning for Industry 4.0 Using Machine Learning for Sustainable Manufacturing. Sustainability 2022 , 14 , 3387. [ Google Scholar ] [ CrossRef ]
- Pozzi, R.; Rossi, T.; Secchi, R. Industry 4.0 technologies: Critical success factors for implementation and improvements in manufacturing companies. Prod. Plan. Control 2023 , 34 , 139–158. [ Google Scholar ] [ CrossRef ]
- Punnakitikashem, P.; Buavaraporn, N. Improving inventory management performance using lean manufacturing initiatives: A case study of Thai automotive parts manufacturer. Oper. Supply Chain Manag. Int. J. 2018 , 11 , 80–87. [ Google Scholar ]
- Jefroy, N.; Azarian, M.; Yu, H. Moving from Industry 4.0 to Industry 5.0: What are the implications for smart logistics? Logistics 2022 , 6 , 26. [ Google Scholar ] [ CrossRef ]
- Banomyong, R.; Supatn, N. Developing a supply chain performance tool for SMEs in Thailand. Supply Chain Manag. Int. J. 2011 , 16 , 20–31. [ Google Scholar ] [ CrossRef ]
- Eiamkanitchat, N.; Sukhotu, V.; Tengpongsthorn, W. Achieving strategic alignment for Thai SMEs through information technology. Int. J. Bus. Inf. 2017 , 12 , 241–266. [ Google Scholar ]
- Kohpaiboon, A.; Jongwanich, J. Global production networks and host-site industrial upgrading: The case of the semiconductor industry in Thailand. World Dev. 2019 , 124 , 104624. [ Google Scholar ]
- Kritchanchai, D.; Hoeur, S.; Engelseth, P. Develop a strategy for improving healthcare logistics performance. Supply Chain Forum Int. J. 2018 , 19 , 55–69. [ Google Scholar ] [ CrossRef ]
- NESDC. Thailand’s Logistics Report 2021 ; NESDC: Bangkok, Thailand, 2022.
- Ramingwong, S.; Sopadang, A.; Tippayawong, K.Y. Factory Logistics Improvement Projects: Case Northern Thailand. Lect. Notes Electr. Eng. 2015 , 349 , 357–362. [ Google Scholar ]
- Somboonwiwat, T.; Kritchanchai, D.; Wasusri, T.; Ruktanonchai, C. Supply chain and Logistics management in Thailand SMEs. In Proceedings of the 7th Asia Pacific Industrial Engineering and Management Systems Conference, Taipei, Taiwan, 7–10 December 2006; pp. 17–20. [ Google Scholar ]
- NESDC. Gross Regional and Provincial Product Chain Volume Measure 2022 Edition ; NESDC: Bangkok, Thailand, 2024.
- OSMEP. White Paper on MSMEs 2024 ; OSMEP: Bangkok, Thailand, 2024. [ Google Scholar ]
- Intarakumnerd, P. Thailand’s middle-income trap: Firms’ technological upgrading and innovation and government policies. Seoul J. Econ. 2019 , 32 , 107–136. [ Google Scholar ]
- Warr, P.; Kphpaiboon, A. Explaining Thailand’s automotive manufacturing success. J. Southest Asian Econ. 2018 , 35 , 425–448. [ Google Scholar ] [ CrossRef ]
- Sitthidetchtamroung, N.; Khamkanya, A.; Jearsiripongkul, T.; Pattanapairoj, S. Gap analysis of current industrial technology towards the Industry 4.0 scheme: A case study of SMEs in the central region of Thailand. Eng. Appl. Sci. Res. 2013 , 50 , 26–32. [ Google Scholar ]
- The World Bank. Connecting to Compete 2023, Trade Logistics in the Global Economy ; The World Bank: Washington, DC, USA, 2023. [ Google Scholar ]
- Manopiniwes, W.; Tippayawong, K.Y.; Numkid, J.; Santiteerakul, S.; Ramingwong, S.; Dallasega, P. On logistics potential of Thai industry in identifying gap to logistics 4.0. J. Eng. Appl. Sci. 2019 , 14 , 1608–1613. [ Google Scholar ] [ CrossRef ]
- Zhou, C.; Etzkowitz, H. Triple helix twins: A framework for achieving innovation and UN sustainable development goals. Sustainability 2021 , 13 , 6535. [ Google Scholar ] [ CrossRef ]
- Suzuki, S. SCM Logistics Scorecard: A simplified benchmarking tool for supply chain operational performance. In Proceedings of the 2015 IEEE International Conference on Industrial Engineering and Engineering Management (IEEM), Singapore, 6–9 December 2015; pp. 290–294. [ Google Scholar ]
- Ministry of Industry. Industrial Logistics Performance Index (ILPI) Manual ; Ministry of Industry: Bangkok, Thailand, 2019.
- Spliet, R.; Gabor, A.F. The time window assignment vehicle routing problem. Transp. Sci. 2015 , 49 , 721–731. [ Google Scholar ] [ CrossRef ]
- Erdoğan, G. An open source spreadsheet solver for vehicle routing problems. Comput. Oper. Res. 2017 , 84 , 62–72. [ Google Scholar ] [ CrossRef ]
- Khanorkar, Y.; Kane, P.V. Selective inventory classification using ABC classification, multi-criteria decision making techniques, and machine learning techniques. Mater. Today Proc. 2023 , 72 , 1270–1274. [ Google Scholar ] [ CrossRef ]
- Irmayanti, H. November. Analysis of raw material ordering with economic order quantity method. IOP Conf. Ser. Mater. Sci. Eng. 2019 , 662 , 032011. [ Google Scholar ] [ CrossRef ]
- Kasemset, C.; Phuruan, K.; Opassuwan, T. Shallot Price Forecasting Models: Comparison among Various Techniques. Prod. Eng. Arch. 2023 , 29 , 348–355. [ Google Scholar ] [ CrossRef ]
- Tiwong, S.; Ramingwong, S. Lifecycle management model review and design for LSP. In Proceedings of the 2nd International Conference on High Performance Compilation, Computing and Communications, Hong Kong, China, 15–17 March 2018; pp. 88–92. [ Google Scholar ]
- Zsifkovits, H.; Woschank, M.; Ramingwong, S.; Wisittipanich, W. State-of-the-Art Analysis of the Usage and Potential of Automation in Logistics. In Industry 4.0 for SMEs: Challenges, Opportunities and Requirements ; Springer: Cham, Switzerland, 2020; pp. 193–212. [ Google Scholar ]
- Tiwong, S.; Ramingwong, S.; Tippayawong, K.Y. On LSP lifecycle model to re-design logistics service: Case studies of Thai LSPs. Sustainability 2020 , 12 , 2394. [ Google Scholar ] [ CrossRef ]
Click here to enlarge figure
Area 1: Corporate strategy and inter-organization alignment | 1.1 Corporate strategy regarding logistics 1.2 Supplier contract terms and degree of information sharing 1.3 Customer contract terms and degree of information sharing 1.4 System for customer satisfaction 1.5 System for employee development and evaluation |
Area 2: Planning and execution capability | 2.1 Logistics strategy implementation 2.2 Demand forecasting 2.3 Logistics planning and adaptability 2.4 Inventory management and control 2.5 Process standardization 2.6 Logistics responsibility assignment |
Area 3: Logistics performance | 3.1 Logistics activity improvement 3.2 Inventory turnover and cash-to-cash cycle time 3.3 Customer lead time and load efficiency 3.4 Delivery performance and quality 3.5 Inventory visibility and opportunity costs 3.6 Environmental activities 3.7 Logistics cost management |
Area 4: IT methods and implementation | 4.1 Data interchange coverage 4.2 Open standards and unique identification codes 4.3 Logistics and supply chain IT capacity building |
Area 5: External collaboration | 5.1 Collaboration with partners 5.2 Collaboration with R&D agencies |
Logistics Activities | Cost Dimension | Time Dimension | Reliability Dimension |
---|---|---|---|
ILPI1 Demand Forecasting and Planning | ILPI1C Forecasting Cost per Sale | ILPI1T Average Forecast Period | ILPI1R Forecast Accuracy Rate |
ILPI2 Customer Service and Support | ILPI2C Customer Service Cost per Sale | ILPI2T Average Order Cycle Time | ILPI2R Delivered In Full and On Time |
ILPI3 Logistics Communication and Order Processing | ILPI3C Information Processing Cost per Sale | ILPI3T Average Order Processing Cycle Time | ILPI3R Order Accuracy Rate |
ILPI4 Purchasing and Procurement | ILPI4C Procurement Cost per Sale | ILPI4T Average Procurement Cycle Time | ILPI4R Supplier DIFOT |
ILPI5 Material Handlings and Packaging | ILPI5C Damaged Value per Sale | ILPI5T Average Material Handling and Packaging Cycle Time | ILPI5R Damage Rate |
ILPI6 Warehousing and Storage | ILPI6C Warehousing Cost per Sale | ILPI6T Average Inventory Cycle Time | ILPI6R Inventory Accuracy |
ILPI7 Inventory Management | ILPI7C Inventory Carrying Cost per Sale | ILPI7T Average Inventory Day | ILPI7R Inventory Out of Stock Rate |
ILPI8 Transportation | ILPI8C Transportation Cost per Sale | ILPI8T Average Delivery Cycle Time | ILPI8R Transportation DIFOT |
ILPI9 Reversed Logistics | ILPI9C Returned Cost per Sale | ILPI9T Average Cycle Time for Customer Return | ILPI9R Rate of Returned Goods |
No. | Size | Industry/Product | Project Focus | Cost Impact (%) | Time Impact (%) | Reliability Impact (%) | Cost Saving/yr. (THB) | Other Benefits |
---|---|---|---|---|---|---|---|---|
1 | S | Waste Management | Transportation (ILPI8) | −15.03% | 165,300 | |||
2 | S | Food Processing | Customer service and support (ILPI2) | −23.79% | +13.57% | Sales increase: THB 1,512,000 | ||
3 | S | Food Processing | Sales forecasting (ILPI1) | +16.3% | Sales increase: THB 1,029,904 | |||
4 | S | Honey Products | Logistics communication and order processing (ILPI3) | −2.08% | −17.62% | 116,465 | ||
5 | S | Beverages | Sales forecasting (ILPI1) and inventory management (ILPI7) | Sales increase: THB 1,896,000 | ||||
6 | S | Export | Logistics communication and order processing (ILPI3) | −32.39% | 251,480 | |||
7 | S | Automotive | Transportation (ILPI8) | −25.37% | 108,000 | |||
8 | S | Cold Storage | Transportation (ILPI8) | −20.78% | 245,548 | |||
9 | S | Handicrafts | Inventory management (ILPI7) | −21.00% | −13.80% | 717,449 | ||
10 | S | Beverages | Warehouse management (ILPI6) | −55.03% | −10.30% | 336,800 | ||
11 | S | Food Processing | Inventory management (ILPI7) | −32.00% | 1,382,400 | |||
12 | S | Baby Products | Inventory management (ILPI7) | −54.50% | 621,120 | |||
13 | M | Beverages | Inventory management (ILPI7) and warehouse management (ILPI6) | −16.74% | +10.7% | 228,652 | ||
14 | M | Glass Production | Logistics communication and order processing (ILPI3) | −18.92% | 548,240 | |||
15 | M | Medical Equipment | Logistics communication and order processing (ILPI3) and transportation (ILPI8) | −25.00% | −80.00% | +27.3% | 419,577 | |
16 | M | Medical Supplies | Inventory management (ILPI7) and warehouse management (ILPI6) | −34.50% | 102,000 | Sales increase: THB 318,859 | ||
17 | M | Retail | Inventory management (ILPI7) | −51.30% | −43.70% | +31.2% | 520,000 | |
18 | M | Garments | Logistics communication and order processing (ILPI3) | −16.25% | +7.5% | 550,309 | ||
19 | L | Transportation | Transportation (ILPI8) | −24.89% | 29,586,350 | Sales increase: THB 540,691 | ||
20 | L | Retail | Transportation (ILPI8) | −18.90% | 1,415,737 | |||
21 | L | Retail | Inventory management (ILPI7) and warehouse management (ILPI6) | −7.50% | −5.60% | +22.3% | 1,779,769 | |
22 | L | Construction | Transportation (ILPI8) | −15.04% | 2,510,139 | |||
23 | L | Poultry | Logistics communication and order processing (ILPI3) and material handling and packaging (ILPI5) | −16.02% | 868,000 | Sales increase: THB 2,560,000 | ||
24 | L | Beverage | Material handling and Packaging (ILPI5) and inventory management (ILPI7) | −16.50% | −7.50% | 970,000 | ||
25 | L | Transportation | Inventory management (ILPI7) | −15.87% | +15% | 995,000 | ||
26 | L | Frozen Food | Sales forecasting (ILPI1) and logistics communication and order processing (ILPI3) | −21.12% | −13.10% | +9.65% | 1,234,000 | |
27 | L | Food Processing | Transportation (ILPI8) | −16.25% | −22.12% | 1,650,000 | ||
28 | L | Frozen Food | Warehouse management (ILPI6) | −21.67% | 2,370,551 | |||
29 | L | Dairy | Transportation (ILPI8) | −23.70% | +15% | 1,178,618 | ||
30 | L | Asphalt | Transportation (ILPI8) | −26.10% | 3,208,217 |
The statements, opinions and data contained in all publications are solely those of the individual author(s) and contributor(s) and not of MDPI and/or the editor(s). MDPI and/or the editor(s) disclaim responsibility for any injury to people or property resulting from any ideas, methods, instructions or products referred to in the content. |
Share and Cite
Ramingwong, S.; Sopadang, A.; Tippayawong, K.Y.; Jintana, J. Factory Logistics Improvement: A Case Study Analysis of Companies in Northern Thailand, 2022–2024. Logistics 2024 , 8 , 88. https://doi.org/10.3390/logistics8030088
Ramingwong S, Sopadang A, Tippayawong KY, Jintana J. Factory Logistics Improvement: A Case Study Analysis of Companies in Northern Thailand, 2022–2024. Logistics . 2024; 8(3):88. https://doi.org/10.3390/logistics8030088
Ramingwong, Sakgasem, Apichat Sopadang, Korrakot Yaibuathet Tippayawong, and Jutamat Jintana. 2024. "Factory Logistics Improvement: A Case Study Analysis of Companies in Northern Thailand, 2022–2024" Logistics 8, no. 3: 88. https://doi.org/10.3390/logistics8030088
Article Metrics
Article access statistics, further information, mdpi initiatives, follow mdpi.
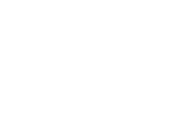
Subscribe to receive issue release notifications and newsletters from MDPI journals

IMAGES
VIDEO
COMMENTS
Learn how enVista helped four clients to implement and optimize WMS solutions for their distribution operations. See the outcomes, challenges and benefits of each case study and download the PDFs for more details.
Learn how DHL Supply Chain helped Baycrew's, a leading 'select-shop' company, to consolidate and optimize their logistics operations across four warehouses into one site. See the benefits of the warehouse management system, productivity goals and employee engagement for Baycrew's online and retail sales.
Warehousing and Logistics Case Study. tices Among States During COVID-19 In the 21st century, public organizations have increasingly shifted to an on-demand just-in-time model of pro. urement and supply chain management. This model has been useful for shrinking bud-gets by cutting out the overhead costs associated with operating a warehousing ...
Warehouse Simulation for Choosing Optimal Picking Algorithm. Kuehne+Nagel, a leading global provider of logistics solutions, was involved in planning a new warehouse for one of their clients. The warehouse would process 13K order lines or 750 picking cartons per day. The project included the development of the best algorithm for multi-order ...
This WMS implementation case study highlights the potential for comprehensive software to enhance virtually any warehouse operation. Achieving this requires a thorough analysis of every process within your warehouse and careful consideration of how advanced technology can drive improvements. This is especially beneficial if you decide to turn ...
Few businesses can compete with Amazon—not just as a retailer, but also in shipping, data management, and even warehousing. To become the juggernaut it is today, Amazon has evolved to provide many of its necessary service needs. For its warehousing needs alone, for example, Amazon reportedly owns nearly 319 million square feet of fulfillment center […]
Warehouse Management Software (WMS) is like your personal assistant for managing the chaos of a warehouse. It's a fancy computer program that helps keep track of inventory, streamline processes, and make your life a whole lot easier. Think of it as the Hermione Granger of your warehouse - organized, efficient, and always on top of things.
The post Case Study: How to Keep Your Warehouse Pristine appeared first on Logistics Business® Magazine. Nilfisk are one of the world's largest manufacturers of commercial and industrial cleaning equipment. ... Transloading: A Comprehensive Guide With Client Examples. Dedola Global Logistics. JANUARY 14, 2023. Case Studies: DGL's ...
Mecalux offers various types of warehouse systems for different sectors and needs. Browse the case studies of Renault, Danone, Decathlon, Dufry and more to see how Mecalux has optimized their logistics.
AI in the Retail Industry: Benefits, Case Studies & Examples. ThroughPut. MARCH 27, 2024. Every aspect of operations, be it managing the inventory, forecasting demand or fulfilling orders was dependent on human wisdom and intuition.Real-time visibility was lacking, be it in warehousing or transportation, due to which delivery delays were common. Besides, AI is helping retailers optimize ...
The WES is the "brain" of the system, sequencing and regulating the release and flow of orders into the facility. FlexSim's Process Flow tool was used to replicate the WES logic—Bastian Solutions created an algorithm using Process Flow activity blocks to evaluate the system's capacity against the orders sitting in the pool, and then ...
Warehouse Management Systems is one of the key Logistics and Supply Chain systems when it comes to Logistics and Supply Chain visibility. This article talks about the recent challenges and its ...
Watch: Alpine Supply Chain Solutions & Ecentria: A Case Study. Supply Chain Brain. APRIL 27, 2023. Huge growth in sales led to the need to optimize inventory, fulfillment and warehouse operations at Ecentria, say Michael Wohlwend, managing principal of Alpine Supply Chain Solutions, and Andrew Mironov, head of operations at Ecentria.
The comparative analysis of the individual warehouse processes' duration is also visible in this chapter. Finally, everything is rounded off with the observed conclusions of the research. 2. Overview of warehouse process optimization methods Logistics costs take an important part of the overall production costs.
5S is a tool to eliminate or minimize waste. 5S is often used by the industrial world, especia ly the. manufacturing industry [ 2]. The 5S concept consists of sort (seiri), set in order (seiton ...
Managing the Inbound Supply Chain. Penske helped this supplier minimize supply chain disruptions by designing a network that optimized mode selection, routing and analysis. Read supply chain case studies about our work with customers to create supply chain management solutions that support long-term growth and profitability.
Learn how digital warehouse design can help you optimize your warehouse layout, workflows, and automation options without shutting down your facility. See examples of how companies have used digital simulations to reduce costs, improve efficiency, and enhance customer service.
Learn how Merchandise Warehouse, a logistics provider of multi-temperature warehouse services, increased its storage capacity and reduced product touches with high-density racking and a pallet shuttle system. The article also features other cold storage solutions and industry news.
Real-Time Data Warehouse: 3 Real-Life Examples For Enhanced Business Analytics. To truly highlight the importance of real-time data warehouses, let's discuss some real-life case studies. Case Study 1: Beyerdynamic Beyerdynamic, an audio product manufacturer from Germany, was facing difficulties with its previous method of analyzing sales data ...
This case study includes a detailed analysis of the relationships between the flow of items through the warehouse, the assignment of staff, the inventory management policy, and the order processing tasks. ... Warehouse layouts are the perfect examples of fundamentals often neglected. Most organizations simply treat the warehouse as a place ...
The warehouse contains large amounts of historical data and allows you to study past trends and issues to predict events and improve the business structure. Blindly repeating other people's decisions is also impossible. Your case is unique and probably requires a custom approach. At best, well-known storage solutions can be taken as a basis.
Background: Thailand's logistics costs significantly exceed global averages. This study examines the novel application of a triple-helix model in factory logistics improvement projects in Northern Thailand from 2022 to 2024, addressing industrial logistics inefficiencies. Methods: The project involved 30 factories across various sectors, employing a case study methodology to analyze ...