Asking the better questions that unlock new answers to the working world's most complex issues.

Trending topics
AI insights
EY podcasts
EY webcasts
Operations leaders
Technology leaders
Marketing and growth leaders
Cybersecurity and privacy leaders
Risk leaders
EY Center for Board Matters
EY helps clients create long-term value for all stakeholders. Enabled by data and technology, our services and solutions provide trust through assurance and help clients transform, grow and operate.
- 5||See all Assurance
Artificial Intelligence (AI)
Strategy, transaction and transformation consulting
Technology transformation
Tax function operations
Climate change and sustainability services
EY Ecosystems
Supply chain and operations
EY Partner Ecosystem
Explore Services
We bring together extraordinary people, like you, to build a better working world.
- 1||More about what you can do here
- 2||More about what it's like to work here
- 3||More about how to join us
- 4||More about job search
Experienced professionals
MBA and advanced-degree students
Student and entry level programs
Contract workers
EY-Parthenon careers
Discover how EY insights and services are helping to reframe the future of your industry.
Case studies
Energy and resources
How data analytics can strengthen supply chain performance
13 Jul 2023 Ben Williams
How Takeda harnessed the power of the metaverse for positive human impact
26 Jun 2023 Edwina Fitzmaurice
Banking and Capital Markets
How cutting back infused higher quality in transaction monitoring
11 Jul 2023 Ron V. Giammarco
At EY, our purpose is building a better working world. The insights and services we provide help to create long-term value for clients, people and society, and to build trust in the capital markets.
New EY research finds AI investment is surging, with senior leaders seeing more positive ROI as hype continues to become reality
15 Jul 2024 Lizzie McWilliams
New EY Consumer Products and Retail Executive Pulse reveals perception vs. reality gap for AI maturity
09 Jul 2024 EY Americas
EY Announces Winners for the Entrepreneur Of The Year® 2024 Mid-Atlantic Award
21 Jun 2024 Victoria Kasper
No results have been found
Recent Searches

CIO Survey: will you set the GenAI agenda or follow the leaders?
Get insights on how CIOs will address the challenges and capture the full benefits of GenAI in the 2024 EY CIO Sentiment Survey.

How a flexible supply chain raised the bar for the beverage industry
The client’s goal: better accommodate future growth, predict customer demands, and add agility to inventory and production lines. Learn how we did it.

How can your business go from competitive to cutting edge?
Learn how the EY-Microsoft Alliance delivers AI driven strategies and smart business solutions using cloud technology.
Select your location
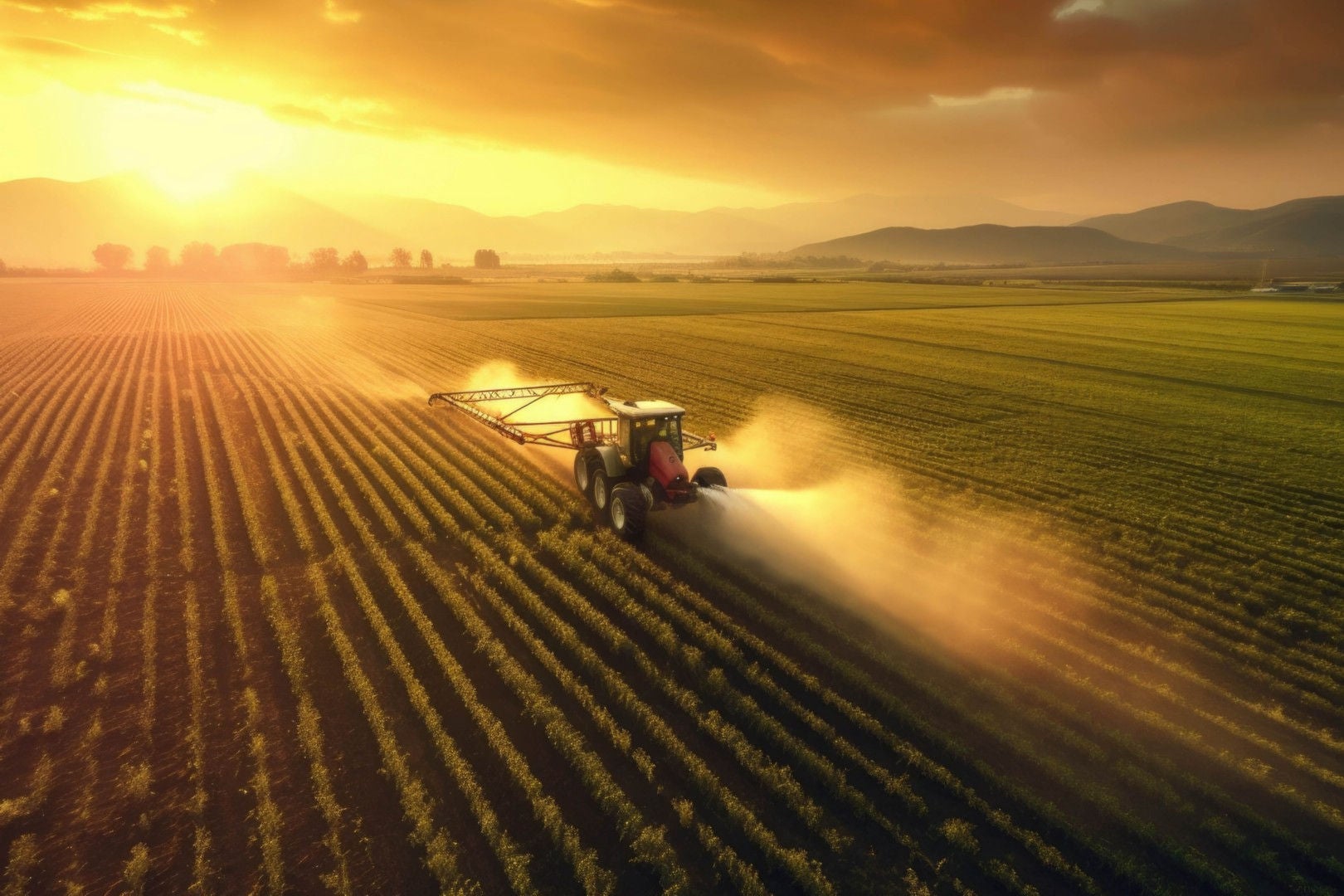
Intelligent transportation management solutions drive improvements
Global standardization improves efficiency, visibility and agility
- 1. Better question
- 2. Better answer
- 3. Better working world
How EY can help
The better the question
Rising to the challenge all around the world
EY Supply Chain Transformation solution
Discover how EY's Supply Chain Transformation solution can help your business move towards fully autonomous, connected supply chains that drive business growth.
One EY client, a global leader in innovative farming and agriculture science solutions, sought to improve its operations through implementing an advanced global TMS. Seeking to reduce overall transportation spend and increase customer on-time delivery across multiple regions, the client sought the support of the EY organization.
Conducting business in more than 70 countries, the client had difficulties streamlining and managing transportation. It used multiple systems, which provided varied logistic workflows, and unclear data and analytics.
Adding to the confusion, these disparate systems didn’t offer any capacity for collaboration or communication. In other words, the multinational client was relying on siloed data and processes.
Additionally, other issues hindered its performance:
- A lack of supply chain visibility
- Incohesive data to analyze performance
- Nonstandard transportation processes
- Inability to track and trace orders
- Unautomated operations and communications with logistics partners
Based on the client’s challenges, the EY-Blue Yonder alliance seemed the perfect fit.
The better the answer
Taking the right approach, right on time
The solution
The alliance brought deep experience and specialization in delivering transformative supply chain strategies. Engaging with the client, we identified the need for a single, end-to-end global logistics solution. This type of TMS could standardize and automate the sharing of data, metrics, workflows and leading practices across departments, regions and time zones.
The first step was onboarding the client’s legacy logistics operations to Blue Yonder’s TMS technology across the US, Latin America, EMEA and Asia-Pacific. This eventually covered more than 350 locations within the client’s global footprint.
Blue Yonder’s technology addressed not only international transportation needs but also domestic logistics. This meant managing logistics across multiple modes, such as truckload, less-than-truckload (LTL), intermodal, rail, parcel, ocean and air.
The alliance team helped the organization standardize the processes and augment its existing global design template. Helping the client transform in today’s digital age, the alliance developed and deployed a digital platform to expedite region, user and carrier onboarding.
The better the world works
Strengthening every link in the supply chain
The outcome
The EY and Blue Yonder teams successfully onboarded the organization’s logistics operations to the Blue Yonder TMS — standardizing and automating operations globally. Key to this success was identifying, consistently measuring and leveraging the appropriate KPIs across the client’s network, which facilitated tactical and strategic decision-making.
While the initial deployment of the TMS included 10 countries, it’s now utilized in more than 65. This is thanks to its enabling near-real-time transportation visibility, which improved the client’s global tracking, no matter the mode of transportation.
With the new TMS in place and deployed, the client achieved its goal of driving supply chain savings and increasing on-time performance. Because of the EY-Blue Yonder alliance, the client make progress on becoming a more data-driven organization, positioning it for further leadership all around the world.
EY-Blue Yonder Alliance: enabling your supply chain’s full potential
EY and Blue Yonder design and deliver global supply chain transformational projects and create long-term value for their customers. Learn more.
Supply Chain & Operations Consulting Services
Discover how EY's supply chain team can help your business redefine its end-to-end supply chain and operations to support your enterprise objectives.
How EY orchestrates opportunity
EY Ecosystems: orchestrating technology, data and relationships
EY Ecosystem strategies help assess ecosystem strengths, identify market opportunities and determine your role within targeted ecosystems. Learn how.
The EY Partner Ecosystem: our strategic relationships and alliances
EY teams collaborate, co-create and innovate with our category-leading organizations to drive transformation, performance and growth.
How EY alliances have helped clients navigate challenges
Explore our case studies to learn how EY alliances combine perspectives to see solutions beyond challenges.

Vivek Chhaochharia

- Connect with us
- Our locations
- Do Not Sell or Share My Personal Information
- Legal and privacy
- Accessibility
- Open Facebook profile
- Open X profile
- Open LinkedIn profile
- Open Youtube profile
EY refers to the global organization, and may refer to one or more, of the member firms of Ernst & Young Global Limited, each of which is a separate legal entity. Ernst & Young Global Limited, a UK company limited by guarantee, does not provide services to clients.
- Tech Insights
- Careers Insights
- Careers @ Zenkins
- Careers Portal
- Custom Software Development
- Web Application Development
- Mobile App Development
- SaaS Product Development
- Enterprise Software Development
- Software Testing and Quality Assurance
- Cloud Integration
- API Development and Integration
- DevOps and CI/CD
- UI/UX Design
- AI and ML Integration
- IoT Software Development
- Digital Transformation
- IT Staff Augmentation
- Data Engineering
- Product Engineering
- IT Consulting
- Platform And Infrastructure
- Manufacturing
- Professional Services
- Transportation & Logistics
- Telecommunications
- Construction
- Travel & Hospitality
- Industry 4.0
- Capital Markets
- Consumer Goods & Distribution
- Communications, Media & Information Services
- Energy, Resources & Utilities
- Life Sciences
- Public Services
- Frontend Development
- Backend Development
- Full-Stack Development
- Cloud & DevOps
- UI/UX & Design
- Quality Assurance & Testing
- Enterprise Solutions
- Specialized Roles
- ASP.NET Developers
- Blazor Developers
- C# Developers
- WPF Developers
- WinForms Developers
- VB.NET Developers
- Angular Developers
- React.js Developers
- Vue.js Developers
- HTML CSS Developers
- .NET Developers
- .NET Core Developers
- Azure Developers
- SQL Server Developers
- SharePoint Developers
- Entity Framework Developers
- WCF Developers
- Umbraco CMS Developers
- Full-Stack Developers
- MEAN Stack Developers
- MERN Stack Developers
- Xamarin Developers
- MAUI Developers
- UWP Developers
- Azure DevOps Engineers
- Microsoft Azure Engineers
- Microsoft Cloud Engineers
- Azure Solutions Architects
- Azure Security Engineers
- Azure Data Engineers
- Data Engineers (Microsoft Stack)
- Data Analysts (Microsoft Stack)
- Power BI Consultants
- Machine Learning Engineers (Microsoft Stack)
- AI Developers
- UI/UX Developers
- XAML Developers
- QA Engineers
- Automation Testers
- TestComplete Engineers
- MS Dynamics 365 Developers
- BizTalk Developers
- ServiceNow Developers
- Office 365 Developers
- Microsoft 365 Developers
- RPA Developers (Microsoft Power Automate)
- Azure AI Engineers
- Azure IoT Developers
- .NET Frameworks
- Programming Languages
- Front-End Technologies
- Data & Analytics
- AI & Machine Learning
- API & Integration
- .NET Framework
- ASP.NET Core
- ASP.NET MVC
- ASP.NET Web API
- Entity Framework (EF Core)
- WCF (Windows Communication Foundation)
- WPF (Windows Presentation Foundation)
- WinForms (Windows Forms)
- VB.NET (Visual Basic .NET)
- Microsoft Azure
- Azure DevOps
- Azure Functions
- Azure Logic Apps
- Azure App Services
- Azure Kubernetes Service (AKS)
- Azure Active Directory (AAD)
- Azure Cosmos DB
- Azure SQL Database
- Azure Virtual Machines
- Azure Service Bus
- Azure Key Vault
- Amazon Web Services (AWS)
- AWS EC2 (Elastic Compute Cloud)
- AWS S3 (Simple Storage Service)
- AWS RDS (Relational Database Service)
- AWS DynamoDB
- AWS CloudFormation
- AWS ECS (Elastic Container Service)
- AWS EKS (Elastic Kubernetes Service)
- AWS IAM (Identity and Access Management)
- AWS API Gateway
- AWS Route 53
- Google Cloud Platform (GCP)
- GCP Compute Engine
- GCP App Engine
- GCP Cloud Functions
- GCP Cloud Storage
- GCP BigQuery
- GCP Kubernetes Engine (GKE)
- GCP Cloud Pub/Sub
- GCP Cloud SQL
- GCP Cloud Spanner
- GCP Identity and Access Management (IAM)
- GCP Cloud Run
- JavaScript (ES6+)
- Blazor WebAssembly
- Razor Pages
- SSRS (SQL Server Reporting Services)
- SSIS (SQL Server Integration Services)
- SSAS (SQL Server Analysis Services)
- Azure Synapse Analytics
- Azure Data Lake
- Azure Data Factory
- Apache Hadoop
- Apache Spark
- Apache Kafka
- QlikView/Qlik Sense
- D3.js (Data-Driven Documents)
- Azure Machine Learning
- Azure Cognitive Services
- Azure Bot Service
- RESTful Services
- Azure API Management
- Customized Products
- Case Studies
- Manufacturing Execution System
- Enterprise Resource Planning System
- Deviation Management System
- Customized Product Lifecycle Management (PLM) System
- Customized Work Permit System
- Product Lifecycle Management System Case Study
- Research Project Management Software: A Case Study
- Employee Training Management Software: A Case Study
- Nonprofit Donor Management Software: A Case Study
- Environmental Sustainability Management Software: A Case Study
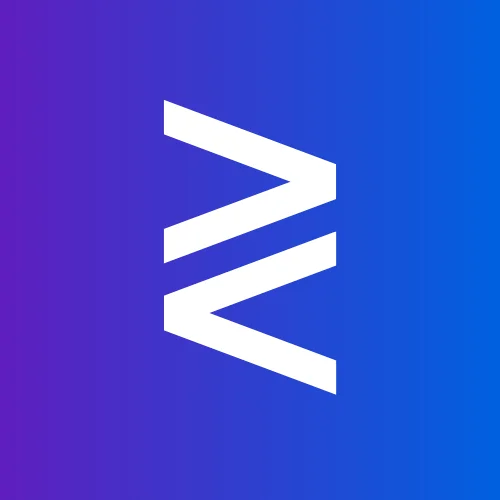
Transport Management Software: A Case Study
- Post author: Maryliya M J
- Post published: January 11, 2024
- Reading time: 14 mins read
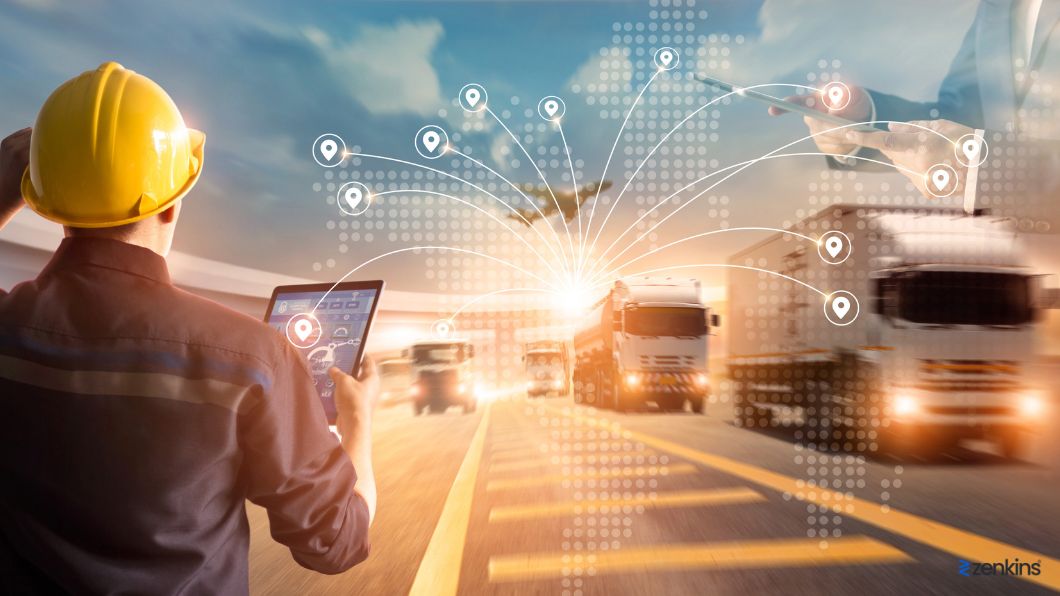
Transport Management Software (TMS): A Case Study
Table of contents.
Transportation management is a critical aspect of any logistics operation, involving the planning, execution, and optimization of freight movements. With the advancement of technology, traditional manual methods of managing transportation have given way to more efficient and automated solutions. Transport Management Software ( TMS ) is one such solution that has revolutionized the way businesses handle their transportation operations.
Introduction to Transport Management Software (TMS)
Definition and purpose of tms.
Transport Management Software, or TMS, is a powerful tool that helps businesses effectively manage their transportation operations. It is a software solution that streamlines and automates various tasks involved in transportation, such as freight management, route planning, load optimization, and documentation. TMS ensures efficient coordination between different stakeholders, including shippers, carriers, and customers, resulting in smooth and cost-effective transportation operations.
Evolution of TMS in Transportation Industry
Transportation management has come a long way from manual paperwork and endless phone calls. The evolution of TMS can be attributed to advancements in technology and the need for businesses to keep up with the growing demands of the transportation industry. In the past, companies relied heavily on spreadsheets and manual processes to manage their transportation activities. Today, TMS offers a comprehensive and automated solution that improves efficiency, reduces costs, and enhances customer satisfaction.
Key Features and Benefits of TMS
Centralized freight management.
One of the key features of TMS is its ability to centralize freight management. It provides a single platform where businesses can manage all aspects of their transportation operations, including order processing, carrier selection, freight tracking, and invoice reconciliation. This centralized approach simplifies the process, reduces errors, and increases efficiency.
Real-time Tracking and Visibility
TMS enables real-time tracking and visibility of shipments, allowing businesses to have complete visibility into their transportation operations. With GPS technology and integration with carriers, businesses can track shipments at every stage of the journey. This level of visibility helps in proactively addressing any delays or issues, improving customer service and overall supply chain efficiency.
Automated Route Planning and Optimization
Gone are the days of manually planning routes and juggling multiple factors such as delivery windows, vehicle capacities, and traffic conditions. TMS automates the route planning process and optimizes it based on various parameters, including cost, distance, and delivery time. This automation saves time, reduces fuel consumption, and improves overall route efficiency.
Efficient Load Optimization and Consolidation
TMS allows businesses to optimize and consolidate loads, maximizing the utilization of available space in trucks or containers. By analyzing shipment data and considering factors like weight, volume, and compatibility, TMS recommends the most efficient way to load goods. This optimization leads to reduced transportation costs and better asset utilization.
Streamlined Documentation and Compliance
TMS streamlines the documentation and compliance process by automating tasks such as generating shipping labels, bills of lading, and customs forms. It ensures that all necessary documentation is in place, reducing the risk of errors and delays. Additionally, TMS keeps businesses in compliance with regulatory requirements, making it easier to meet industry standards and avoid penalties.
About the Client
Our client, a leading logistics company, faced challenges in coordinating its fleet, experiencing delays, and grappling with inefficient routing. Recognizing the need for an advanced solution, they sought a Transport Management Software (TMS) to enhance route planning, monitor vehicle status, and optimize overall transportation logistics.
Project Overview
The project aimed to develop a cutting-edge Transport Management Software using .NET to address the client’s challenges. The primary objectives included real-time tracking of vehicles, dynamic route optimization, efficient communication between drivers and dispatchers, and the integration of analytics to identify areas for improvement.
The Challenges
- Coordination Issues: Lack of effective coordination led to delays and disruptions in transportation operations.
- Inefficient Routing: Existing routing strategies were suboptimal, affecting fleet efficiency and timely deliveries.
- Limited Communication: Inadequate communication channels between drivers and dispatchers hindered real-time decision-making.
The Solution
Our expert team of developers and project managers collaborated to design and implement a comprehensive .NET-based Transport Management Software (TMS). The solution incorporated features such as real-time vehicle tracking, dynamic route optimization, and communication tools to streamline operations.
Key Features of the TMS
- Real-time Vehicle Tracking: The Transport Management Software enabled real-time tracking of vehicles, providing visibility into their current status and location.
- Dynamic Route Optimization: Advanced algorithms optimized routes dynamically, considering factors like traffic, weather, and delivery schedules.
- Communication Tools: The software facilitated efficient communication between drivers and dispatchers, ensuring seamless coordination.
- Analytics Integration: Robust analytics tools were integrated to provide insights into operational efficiency and identify areas for improvement.
The Outcome
The Transport Management Software was successfully deployed, resulting in significant improvements in the client’s transportation logistics. Real-time tracking enhanced visibility, dynamic route optimization reduced delays, and improved communication streamlined operations.
Future Trends and Innovations in TMS
Integration with internet of things (iot).
In the future, Transport Management Software is expected to integrate with the Internet of Things (IoT) to enhance transport management capabilities. By leveraging IoT devices and sensors, organizations can gather real-time data on vehicles, shipments, and traffic conditions. This will enable proactive decision-making, efficient routing, and improved supply chain visibility.
Artificial Intelligence and Machine Learning
Artificial intelligence (AI) and machine learning ( ML ) are poised to revolutionize TMS by offering predictive analytics and automated decision-making. AI algorithms can analyze vast amounts of data to optimize routes, predict demand, and identify potential disruptions. ML algorithms can continuously learn from data, enabling TMS to adapt and improve over time.
Blockchain Technology for Transparency and Security
Blockchain technology holds promise for enhancing transparency and security in transport management. By using blockchain’s decentralized and immutable ledger, organizations can ensure greater visibility and traceability of goods, reducing the risk of fraud and unauthorized access. This technology also enables secure and instant transactions between stakeholders.
Sustainability and Green Initiatives
As sustainability becomes increasingly important, TMS is expected to incorporate features that support green initiatives. This includes optimizing route planning for fuel efficiency, reducing empty miles, and promoting the use of alternative fuels and eco-friendly transportation modes. By embracing sustainability, organizations can reduce their carbon footprint and contribute to a greener future.
Our team’s proficiency in developing a tailored Transport Management Software using .NET technologies addressed the client’s challenges effectively. The implementation of real-time tracking, dynamic route optimization, and communication tools contributed to a more efficient and streamlined transportation operation.
Transport Management Software (TMS) has emerged as a game-changer in the field of transportation management. Its centralized approach, real-time tracking capabilities, automation, and optimization features have revolutionized the way businesses handle their freight movements. Through the case study presented, we have witnessed the tangible benefits and positive impact that TMS brings to transportation operations, including improved efficiency, enhanced visibility, cost reduction, and increased customer satisfaction.
However, the implementation of TMS is not without its challenges, requiring careful planning, stakeholder involvement, and continuous monitoring. By following the best practices discussed, businesses can ensure a successful adoption of TMS and unlock its full potential. As we look to the future, TMS will continue to evolve, integrating with emerging technologies such as IoT and AI, further enhancing its capabilities. It is clear that TMS is here to stay, shaping the future of transportation management and driving operational excellence in the logistics industry.
Are you facing coordination issues and inefficiencies in your logistics operations? Contact us today to explore how our expertise in TMS development can transform your transportation logistics and drive efficiency.
You Might Also Like
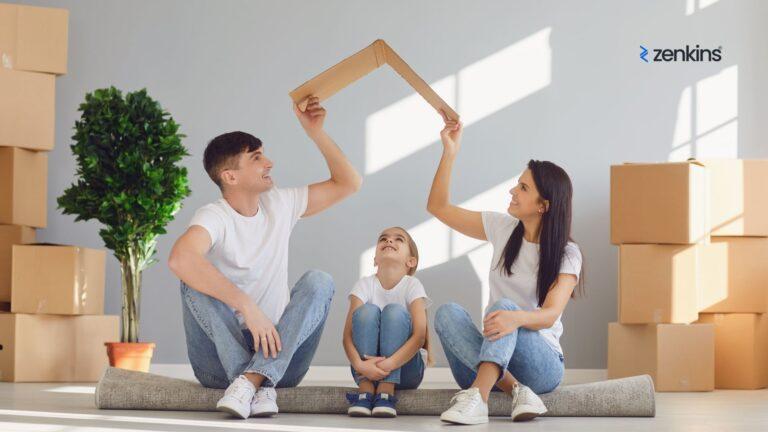
Streamlining Insurance Operations: How IT Staff Augmentation Services Revolutionized Our Client’s Business
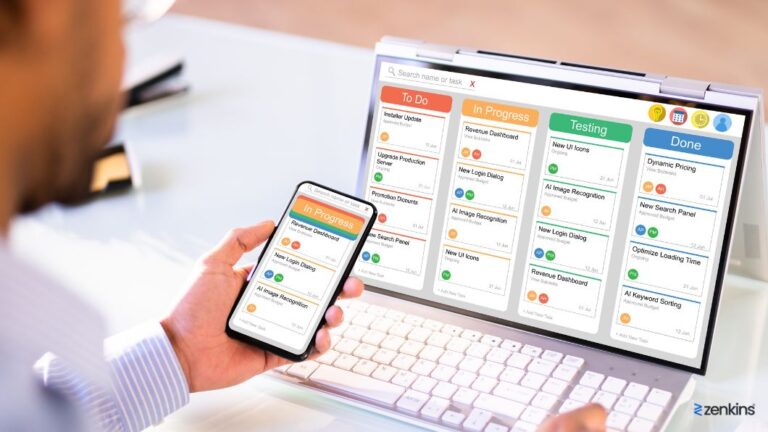
Project Management Software: A Case Study
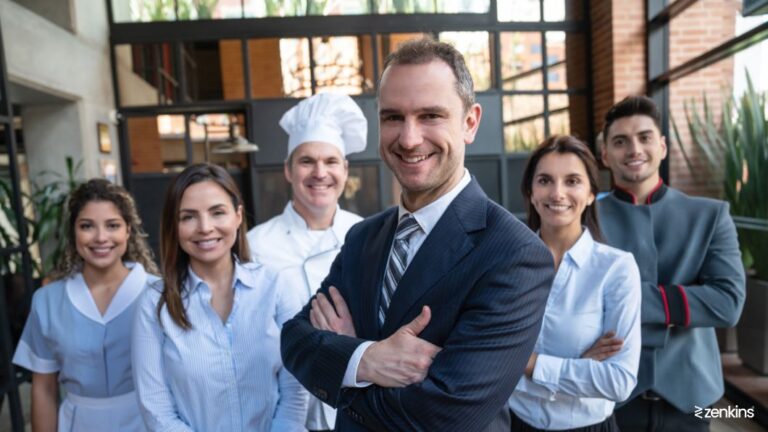
Hotel Management Software: A Case Study
Book a free consultation.
Tailored Solutions, Expert Advice, and Project Estimates Await.
Expect a Prompt Call from one of our Account Managers.
- Elite IT Professionals
- Time Zone Aligned
- Experienced Team
At Zenkins, we bring together a curated network of elite IT professionals ready to elevate your projects to new heights. From seasoned developers to innovative designers, our handpicked talent pool is here to turn your visions into reality. Experience unparalleled expertise, reliability, and dedication to excellence with our team of Elite IT Professionals.
At Zenkins, we understand the importance of global collaboration. That’s why our team is strategically aligned across time zones, ensuring seamless communication and productivity no matter where you are. From brainstorming sessions to project updates, our time zone-aligned approach guarantees that deadlines are met and progress never stalls. Experience the convenience of working with a team that’s always in sync.
At Zenkins, we pride ourselves on our experienced team of professionals who bring years of industry knowledge and skill to every project. From seasoned developers to seasoned project managers, our team has the expertise to tackle even the most complex challenges. With a proven track record of success, we deliver results that exceed expectations.
+91 70690 18504
[email protected]
Zenkins is a leading software development company based in India, specializing in SAAS Product Development, Digital Transformation, and Product Engineering. With a dedicated team of professionals and a commitment to excellence, we deliver innovative solutions that drive business growth and success. Partner with Zenkins for all your software development needs and experience the difference firsthand.
- Methodologies
- Technologies
- Our Services
- IT Staffing Services
- Software Outsourcing
- .NET Development
- Careers @Zenkins
- Current Openings
- Technology Insights
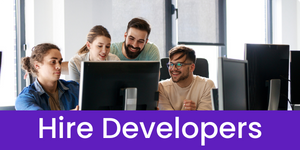
Privacy Overview
Cookie | Duration | Description |
---|---|---|
cookielawinfo-checkbox-analytics | 11 months | This cookie is set by GDPR Cookie Consent plugin. The cookie is used to store the user consent for the cookies in the category "Analytics". |
cookielawinfo-checkbox-functional | 11 months | The cookie is set by GDPR cookie consent to record the user consent for the cookies in the category "Functional". |
cookielawinfo-checkbox-necessary | 11 months | This cookie is set by GDPR Cookie Consent plugin. The cookies is used to store the user consent for the cookies in the category "Necessary". |
cookielawinfo-checkbox-others | 11 months | This cookie is set by GDPR Cookie Consent plugin. The cookie is used to store the user consent for the cookies in the category "Other. |
cookielawinfo-checkbox-performance | 11 months | This cookie is set by GDPR Cookie Consent plugin. The cookie is used to store the user consent for the cookies in the category "Performance". |
viewed_cookie_policy | 11 months | The cookie is set by the GDPR Cookie Consent plugin and is used to store whether or not user has consented to the use of cookies. It does not store any personal data. |
- Big Data, AI & ML
- Cloud & DevOps
- Internet of Things
- Mobile Development
- Processes Architecture
- Product Design
- Quality Engineering
- Renewable Energy
- Software Development
- Techstack News
- Transportation and Logistic
Choosing the Right Software for Your Transport Management System: Key Factors to Consider
Roman Slisarenko
Share this article:
Transportation management in logistics is now mainstream. Industry research predicts that the transportation management software market will grow from $5.8 billion in 2021 to over $14.4 billion by 2027. This high demand reflects the need for efficient transportation amidst global disruptions and expanding trade.
Managing logistics and shipping operations efficiently is nearly impossible without reliable transportation management system software. However, not all solutions are equal, and organizations with legacy tools often struggle to effectively coordinate freight movements, optimize routes, predict demand, and control costs.
This article provides help and guidance for those looking to implement or upgrade a transportation management system (TMS). We will explain the TMS's transformative role in a modern supply chain and highlight its key features and business advantages. Then, we will explore the key considerations when choosing a TMS provider.
Finally, we’ll guide you through the implementation process to ensure your system delivers the desired results.
How Logistics Businesses Benefit from Transportation Management Systems
A Transportation Management System (TMS) is a software tool set that simplifies the planning, tracking, and delivery of goods throughout the supply chain and across multiple regions, jurisdictions, and transport modes.
These systems are now essential tools in industries and businesses of all sizes. McKinsey’s 2023 Digital Logistics survey of over 250 global logistics providers and shippers shows that TMS solutions are now so mainstream that companies without them risk losing out to competitors.
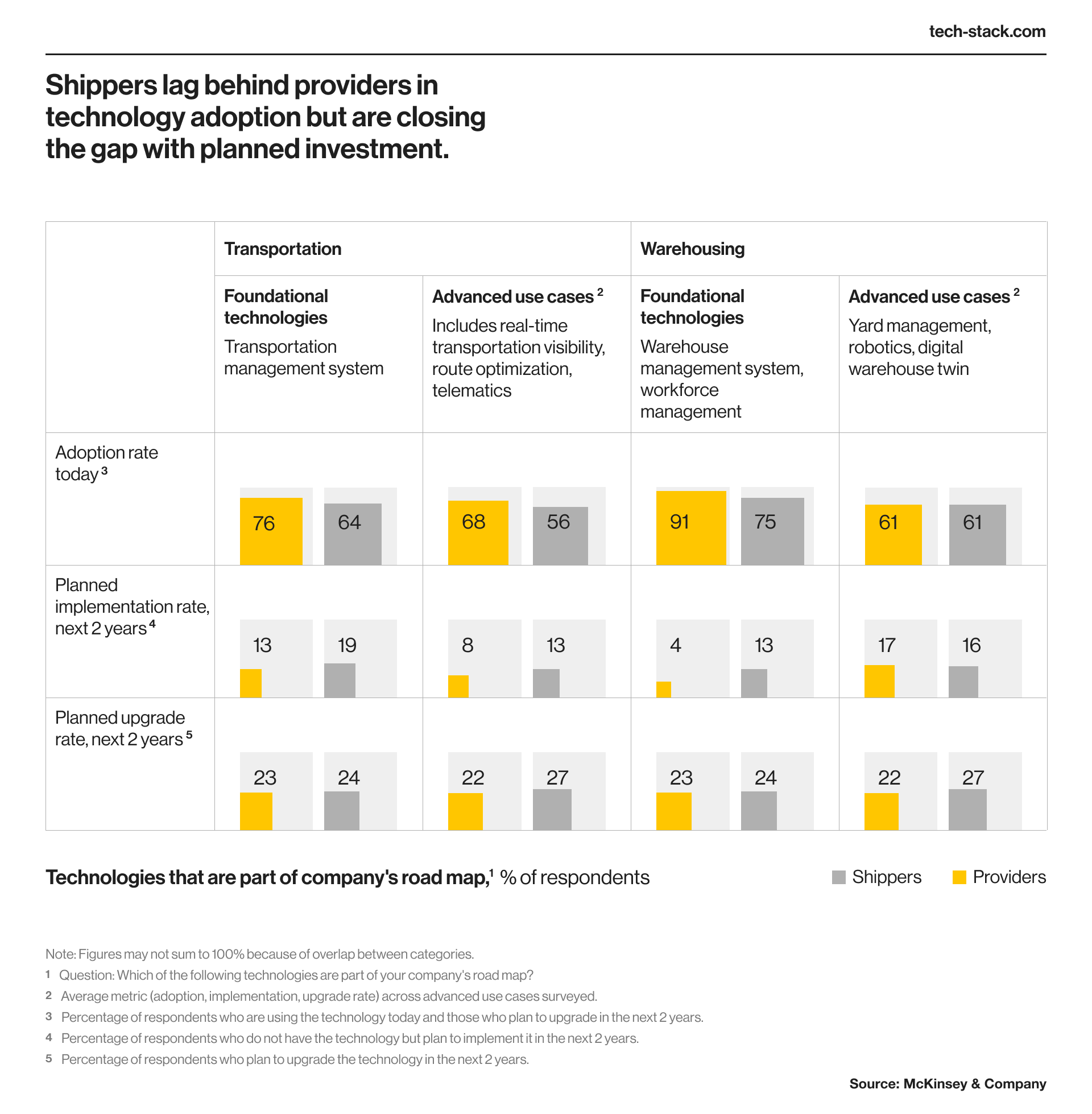
To better understand the TMS boom, just consider these transportation management system benefits:
- Minimized fuel expenditure. Organizations can identify the fastest routes and optimize fuel consumption to boost overall profitability.
- Streamlined load management. A TMS can optimize load distribution to maximize carrying capacity and travel distances. Software with these kinds of features shortens delivery schedules and reduces unnecessary operational expenses.
- Data-driven logistics optimization. Software with machine learning capabilities and business analytics can predict potential demand and supply chain disruptions, allowing companies to align their operations more tightly with market demand.
- Smarter warehouse management. IoT sensors and RFID tags help track inventory items and supply chain assets, leading to better inventory placement, warehouse movement operations, and more efficient stock control.
- Reduced costs with predictive maintenance. Thanks to AI and machine learning, a TMS can analyze visual cues, sounds, and equipment sensors to anticipate maintenance needs. This lets companies schedule maintenance proactively, which prevents breakdowns and extends vehicle life.
- Environmental sustainability. Reduced travel distances and fuel consumption lead to lower carbon emissions and a smaller environmental footprint.
- Elevated customer experience. Real-time tracking and delivery updates make a transportation service feel more reliable for customers. This improvement in the service contributes to customer satisfaction, repeat business, and referrals.
- Real-time operational visibility. A 2023 Gartner survey reports that 74% of organizations invest in TMS to improve operational visibility, for example, with IoT-enabled real-time tracking and actionable insights . Greater visibility allows for swift decision-making and helps anticipate and address disruptions.
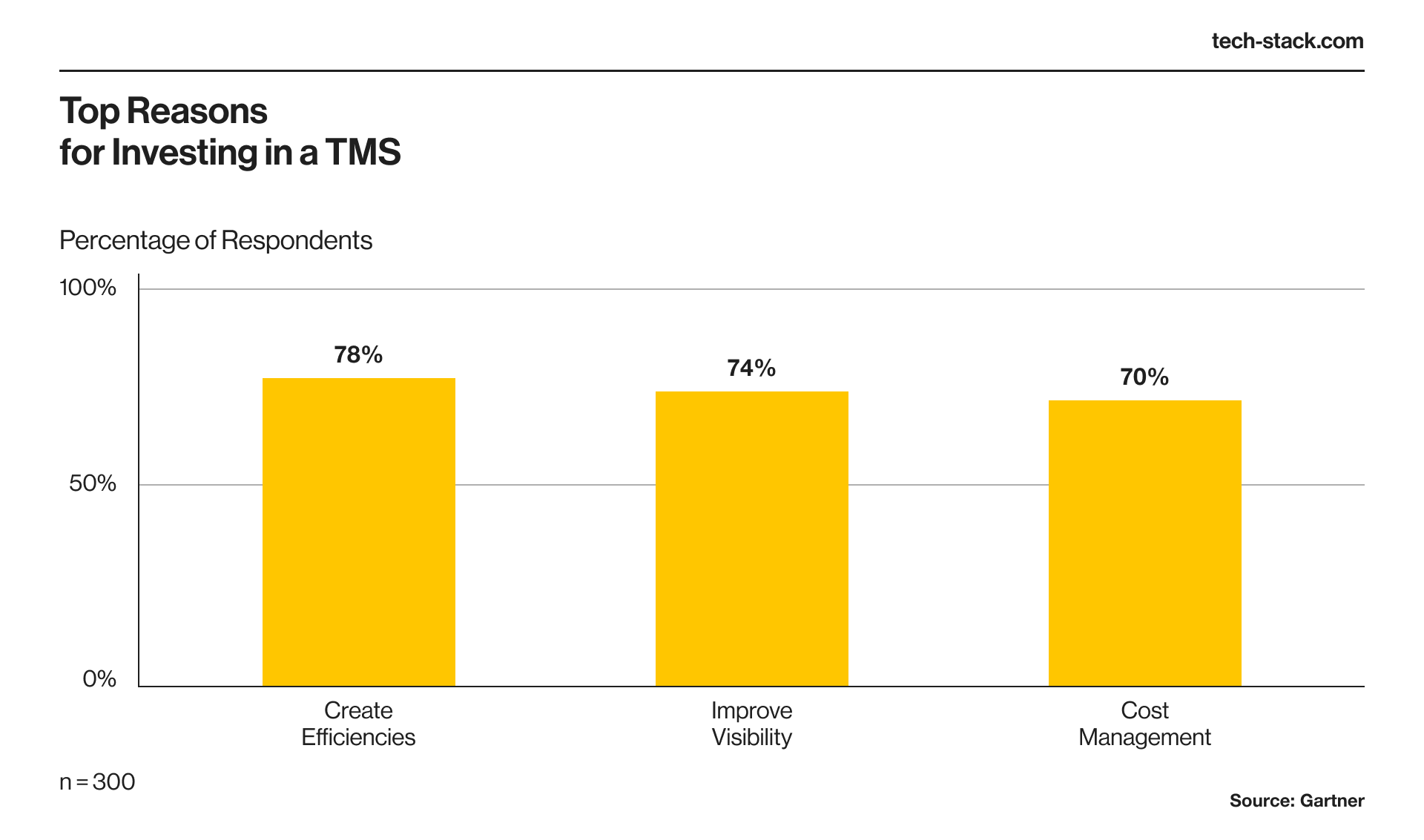
- Regulatory compliance. Automated document generation and regulatory checks allow organizations to produce accurate paperwork for delivery routes that span several jurisdictions, reducing the risk of violations.
In short, the right TMS software brings significant benefits ranging from operational efficiency and cost reduction to environmental sustainability. All these things contribute to your business growth. They also show the importance of selecting a system that meets your organizational needs.
What to Look for In Software for a Transport Management System
Your complete requirements for TMS software will be based on your transportation networks, processes, and regional units, but should generally include the following considerations.
Functionality
To begin with, what operating features should you look for? Gartner’s 2023 Magic Quadrant for Transportation Management Systems highlights the critical capabilities of the most effective systems. Here, we’ll focus on what we consider to be the core features of logistics, transportation, and shipping organizations.
- Freight sourcing (procurement management) allows businesses to compare freight options based on carriers' historical performance, routes, rates, and contract terms.
- Shipment rate management tools monitor and analyze changes in fuel prices, carrier rates, and market conditions to suggest the most economical shipping methods.
- Dock scheduling helps manage the allocation of trucks to loading docks at warehouses or distribution centers. You can schedule and track arrivals and departures to avoid dock congestion and shipment delays.
- Order planning streamlines order entry and tendering by automatically filling out details in documents for the corresponding orders. Many systems allow you to specify rules for tendering, so the TMS will automatically pick the best partners based on costs, load allocation, or end-customer preferences (based on previous shipments).
- Vehicle routing uses GPS and analytics data to determine the most efficient routes for delivery. It considers factors like road conditions, delivery priorities, and real-time traffic updates to reduce travel time. For example, truckers can consult the system to check for road closures.
- Transportation forecasting analyzes historical transportation data and current market trends to forecast future transportation needs. This insight helps you budget and strategize for high demand during specific dates, such as the holiday season.
- A settlement module handles invoicing, payments, and freight auditing processes in compliance with transportation-related regulations. This simplifies document management, financial settlements, bills of lading, and claims.
- Fleet management includes tools for managing fleet vehicle status, scheduling maintenance, and tracking fuel consumption. The software for IoT devices can provide insight into vehicle driving speed, break times, and the response time to real-time alerts. It may also monitor the environmental impact of logistic processes and enable remote transportation control systems.
- Performance management analytics uses AI and ML-powered algorithms to identify areas suitable for service improvement and cost savings based on KPIs (for example, based on on-time delivery rates, cost per delivery, and fuel consumption rates for different routes).
- An event management module can warn about real-time disruptions and unexpected deviations during delivery. One example is cold chain logistics tools that notify the driver about temperature or humidity changes in cargo with perishable products so the driver can prevent spoilage.
- Carrier communication tools provide secure, encrypted communications between managers, warehouse workers, carriers, and drivers. They facilitate coordination, real-time updates, and document sharing.
- 3D load modeling helps place the cargo in vehicles based on a virtual model. The automation feature can suggest the best placement to maximize space usage and ensure cargo safety.
These built-in features are not the only things to look out for—your TMS software must also work seamlessly with your existing systems and tools.
Integration capabilities
Modern logistics and shipping companies manage several TMS-related solutions. McKinsey research shows that 34% of transportation providers have more than eight technologies in their TM stack. Smooth integration is key to bringing all these data sources together. Integration capabilities
Modern logistics and shipping companies manage several TMS-related solutions. McKinsey research shows that 34% of transportation providers have more than eight technologies in their TM stack. Smooth integration is key to bringing all these data sources together.
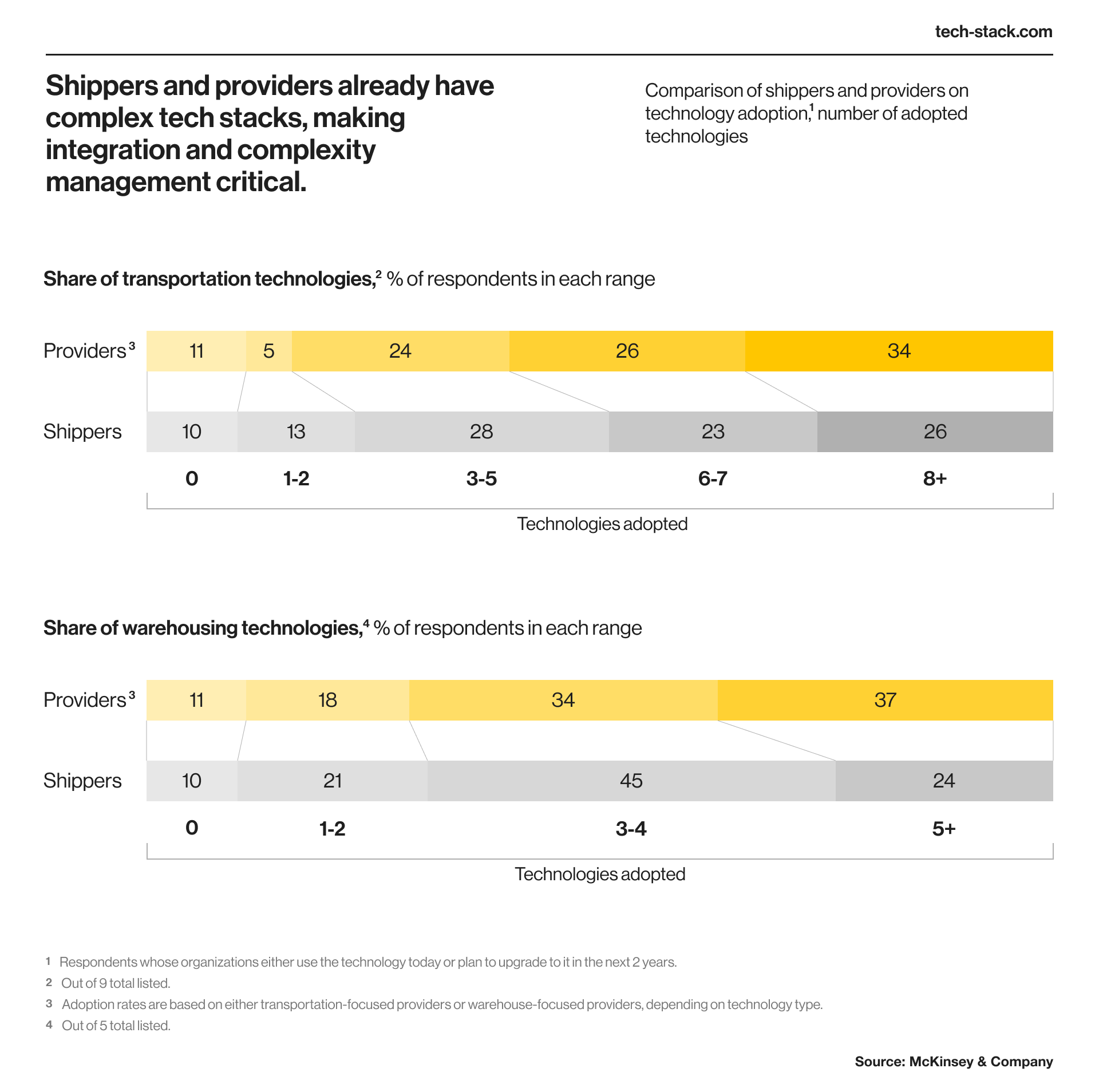
The lack of standards for data sharing between partners and vendors is a known problem among logistics and supply chain vendors. It's important to ensure that the solution converts data from other systems outside the TMS for seamless data sharing. That’s why, before committing to a TMS provider, you should check that the software integrates with your other business tools, such as:
- Enterprise Resource Planning (ERP): ERP systems should be able to integrate transportation and logistic data for more accurate resource planning and financial reporting.
- Warehouse Management System (WMS): Integrating a TMS with a WMS helps synchronize asset provisioning and inventory control to drive the efficiency of warehousing operations.
- Order Management System (OMS): OMS-TMS integration allows you to automatically capture, fulfill, and track orders across multiple eCommerce channels.
- Retail or eCommerce platform: In retail, integrating an eCommerce platform with a TMS aligns order processing and scheduling. This can allow customers to select an appropriate carrier or track their delivery.
- Business Intelligence (BI) software: The mass of TMS data should fuel your BI and data analytics software, helping you make more informed decisions and forecast trends.
- Third-Party Logistics (3PL) system: Integrating TMS with 3PL systems is essential for outsourced logistics operations, as it ensures seamless coordination during procurement and fulfillment activities.
Once you’ve checked that a TMS has the right features and integrates seamlessly with your systems, it’s time to think about your processing load.
Scalability
As your logistical activities grow, so does your data volume and system load. Your transportation management system needs to be able to handle new IoT devices and software integrations easily to maintain operational performance at peak times.
To ensure you have enough operational resources at any point in time, we recommend considering the following solutions:
- A cloud-based infrastructure: Modern solutions are primarily cloud-based subscription services that help you avoid extensive hardware installation, setup, and maintenance.
- Autoscaling: This capability allows resources in cloud applications to scale up and down based on demand, so you only pay for what you need.
- Modular architecture: TMS software built on a modular, loosely coupled architecture lets you add or modify features without disturbing existing processes.
- Mobile applications: Mobile versions ensure that all your employees, from managers to field personnel to drivers, stay connected to logistics operations.
To check that a TMS will reliably scale for you, we advise getting a free trial version from the provider and testing it under extreme conditions.
We developed an auction platform for cargo allocation and bidding that speeds up logistic operations by automatically validating the most cost-effective bids. The platform is built on scalable AWS infrastructure to ensure high performance under any load. We also designed web and mobile interfaces to allow employees to engage with the platform on the go.
After understanding what a good solution for transportation and logistics management is, you need to know how to implement it in your business operations.
How to Effectively Implement Transportation Management System Software
At Techstack, we work with both startups and enterprises. In each case, we follow a time-tested process of detailed business analysis, strategic planning, and test-driven integration. Here are the six steps you can take to ensure successful TMS integration.
1. Research your needs and opportunities
The first step is to carry out an in-depth analysis of your logistics, transportation, and supply chain needs. Review your existing processes and application portfolio to understand where your opportunities for streamlining and cost-cutting lie. Involve your employees, as their experience can provide invaluable insights.
Beyond an internal audit, analyze how your competitors use their transportation management systems. Their successes and shortcomings may inform your choice of a TMS provider.
2. Choose your TMS provider
Your research should give you specific criteria for selecting your TMS provider. As we’ve seen, the right solution will offer all required features, integrate with your workflow, and scale with your operational demands.
Software review platforms such as Capterra, Gartner, and G2 are good for comparing options. Focus on features, pricing models, and interface, and check reviews from other business users to understand any weaknesses. When you have a shortlist, contact providers for a consultation and ask about free trial or demo options.
Out-of-the-box solutions may not meet all your needs or suit the workflow that you’re used to. In that case, custom TMS solution development with a reputable software development company could be the best solution.
3. Plan the implementation
Collaborate with your TMS solution provider or software company to create a detailed technical requirements outline. Make sure you set up clear success metrics to measure the effectiveness of your operations before and after implementation.
McKinsey reports that 80% of logistics providers and 68% of shippers think costs are the biggest challenge during implementation. To keep spending on track, set operational goals, timeframes, and budgetary constraints for each distinct implementation phase. Also, draft a proactive risk mitigation strategy to cover delays or implementation failures.
Your team will need the right technical expertise and a good understanding of the nuances of transportation management in logistics. Ideally, your project manager and senior engineers will have a track record of implementing successful TMS solutions. Using Agile methodologies and DevSecOps practices can streamline development and mitigate production risks.
4. Integrate the TMS with existing systems
It’s now time to work with the provider to integrate the transportation management solution into your supply chain. The aim is to extend your technical and business capabilities while maintaining a secure environment. For this to happen, the TMS should work seamlessly with your enterprise resource and warehouse management systems, planning tools, and billing software.
McKinsey research cites change management and training as key integration challenges. That’s why your TMS provider should provide essential technical assistance and remote support for onboarding. Ideally, they should also equip your employees with the skills and practices to fully leverage the software’s potential.
5. Conduct continuous testing
Establishing a robust quality control loop and quality model is crucial for successful implementation. The testing team should cooperate with the developers to promptly address bugs, vulnerabilities, and other deviations from the requirements.
Adopt a plan-do-check-act approach for QA to ensure every change is planned, tested, reviewed, and improved upon. QA professionals should assess every aspect of the integration, including usability, stability, efficiency, and security, to make sure the TMS solution performs as expected after deployment.
6. Improve after deployment
After deploying the TMS solution, continuously monitor its behavior to check that it's operating efficiently and scaling correctly with your demand.
Your TMS provider should provide timely bug fixes and security patches to sustain the system’s health. Be sure to periodically analyze user feedback and competitor systems to ensure optimum user experience and functionality.
Now that we’ve reviewed the selection criteria and integration workflow, we’ll help you choose a reliable TMS provider.
TMS Application Provider Comparison
Which TMS platform is right for you?
To help you decide, here’s an overview of the most prominent transportation management software providers and their key differences. Most solutions are tailored to medium-sized businesses and larger enterprises, but if you’re a smaller company, some providers offer suitable subscription tiers.
Let’s take a look at some of the most popular solutions on the market today.
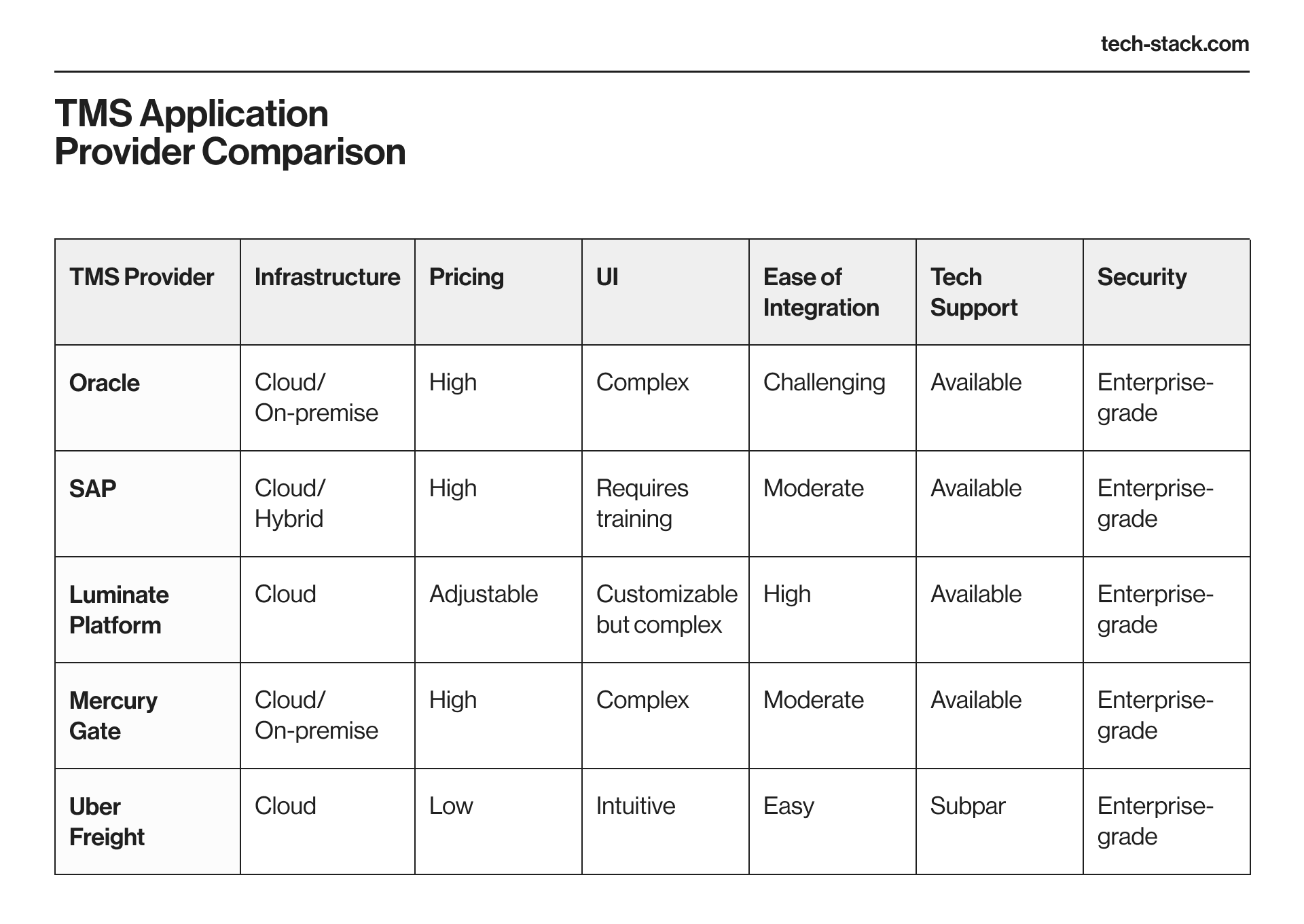
The Oracle Transportation Management (OTM) software suite helps shippers and logistics service providers manage their transportation activity on a global scale. It includes an optimization engine that identifies optimal logistics solutions and shipping routes.
With its user-friendly dashboard and customizable interface, OTM provides clear visibility of transportation data. It generates invoices and processes claims while avoiding errors and duplicates.
- Implementation requires significant effort, particularly when integrating with legacy systems.
- Lacks features like last-mile delivery and simultaneous rating of multiple shipments.
- Occasional software glitches and cloud syncing issues.
- Higher setup costs compared to other TMS solutions.
- Some updates and changes require a platform restart.
SAP’s Transportation Management (TM) solution helps standardize procedures and consolidate data for logistics decision-making. This program centralizes all logistics data and offers enhanced analysis and reporting.
With SAP TM, organizations can schedule carriers, spread load times throughout the day, and coordinate every stakeholder in the transportation process. Users benefit from Google Maps integration for routing and features for tracking mileage and expenses.
- The software has a steep learning curve.
- Accessing certain sections requires excessive authorization or approval.
- The application can be slow, which can affect productivity.
- The high cost makes it less suitable for small and medium-sized organizations.
Luminate Platform
Luminate by Blue Yonder is a highly customizable platform that caters to the needs of 3PL businesses. Its robust integration capabilities ensure smooth data handling across different systems. The platform helps with warehouse labor management, tracking transactions, and enforcing inventory rules for accuracy. What’s more, its advanced work queuing engine helps assign tasks to warehouse staff for maximum efficiency.
- The high level of customization required can make this platform overwhelming for small businesses.
- Users can find the interface cluttered and hard to navigate because of the high amount of information displayed.
- Updates can be sluggish, which creates friction for users who rely on up-to-date information.
MercuryGate
MercuryGate TMS can be deployed in the cloud or on-premise and supports multiple transport modes, including ocean, air, rail, and trucking. It features import/export options and XML visibility for custom solutions. MercuryGate's strength lies in its customizable reports and ability to sort loads efficiently.
- The software has high purchase and installation costs.
- Employees need extensive training to use it effectively.
- Limited visibility on EDI transactions and files can hinder troubleshooting.
- Some screens have notably long load times.
Uber Freight
Uber Freight is a user-friendly trucking TMS that allows for efficient load planning weeks in advance. Its affordable pricing streamlines logistics for small businesses. The platform is particularly well-designed for shippers and drivers, as it offers straightforward mobile apps and an interactive navigation map for shipment tracking.
- This is a basic TMS solution that requires additional management systems alongside it.
- Drivers may find the claims resolution process complex and unclear.
- Some users have reported functional hiccups, such as the app not allowing changes to destinations or departure locations once a driver has accepted a delivery.
- Notifications about the unavailability of drivers for a load are often received only an hour before the scheduled pickup.
In summary, each solution differs in terms of pricing, customization, and use cases. Oracle’s suite is the best for global logistics, but the pricing is too prohibitive for smaller businesses. Meanwhile, Luminate's platform is best tailored to 3PL organizations, while Uber Freight offers a user-friendly solution for startups.
Case Studies of Successful TMS Implementations
Transportation management systems are widely implemented across the industry. Here are just a few companies that have benefited from TMS integration.
- Outrider integrated its software with transportation management systems for autonomous yard operations. Their system uses a full stack of technologies and IoT devices to enhance the visibility of asset and freight locations. This solution helps dispatchers, transportation managers, and warehouse operators improve decision-making and reduce misplacements. Outrider’s CEO estimates that this TMS solution will help drivers save hours looking for trailers that often get lost in yards.
- Blue Diamond , the world's largest almond processor, uses TMS to synchronize demand and supply planning with real-time logistics. The integration gave the organization real-time tracking ability and allowed it to pinpoint delivery bottlenecks. The company states that the technology also automated invoicing and shipping cost calculations.
- SIO Logistics , a 3PL provider, saw a 212% increase in load volume after implementing a TMS with a freight management module. The company highlighted that the software integrated with all their business systems, resulting in end-to-end visibility and enhanced workflow management. The system’s customizable customer portal and automated document management also improved operational efficiency.
- SISU Energy LLC , a Texas-based carrier, adopted an open API-based TMS for transporting bulk commodities for energy exploration and production. The system's user-friendly interface and integration capabilities reduced operational overhead, while the open API allowed SISU to integrate its custom solutions and foster continuous improvement.
- Shree Cement addressed load management challenges by implementing a TMS with IoT sensors and automation tools. The company has halved its truck loading turnaround time thanks to video analytics and thermal technologies and freed up around 400 employees for other tasks. Centralized dashboards also provide real-time vehicle location and movement insights that are accessible on mobile devices.
In all these cases, the real impact comes from how a company uses the installed technology in decision-making and operations. Sometimes, off-the-shelf software lacks the necessary features or doesn’t meet your budget. A logistics software development company can help you build a TMS based on your specific needs.
Invest in a Reliable Transport Management System
In the race to secure safe and reliable transportation in an unpredictable world, organizations without TMS software simply won’t keep up. The right solution helps you maximize your operational efficiency and reduce unnecessary expenses.
Yet, not all TMSs are equal or right for you. Existing solutions may be too expensive, hard to integrate with your systems, or too complex for logistics managers or drivers. This is where the value of a custom solution shines.
At Techstack, we specialize in elevating transport management systems with cutting-edge technology. Our team can do all the hard work: connect the IoT devices, automate your logistic operations, and design intuitive mobile apps. Connect with us to find out how to transform your transportation management.
Related articles
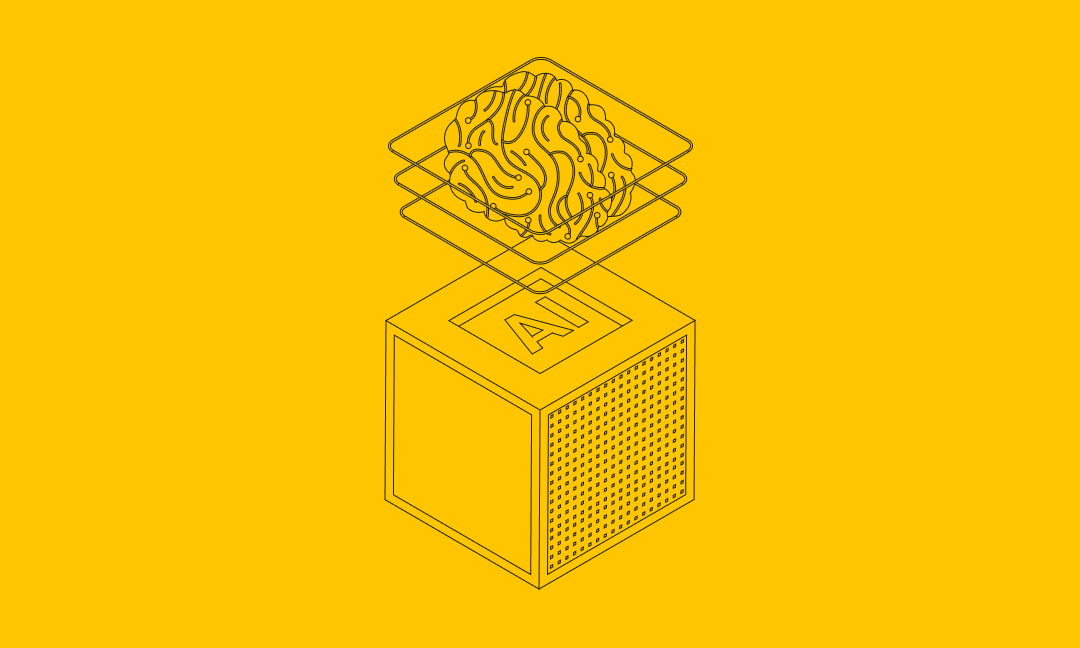
Lessons Learned from Generative AI Early Adopters
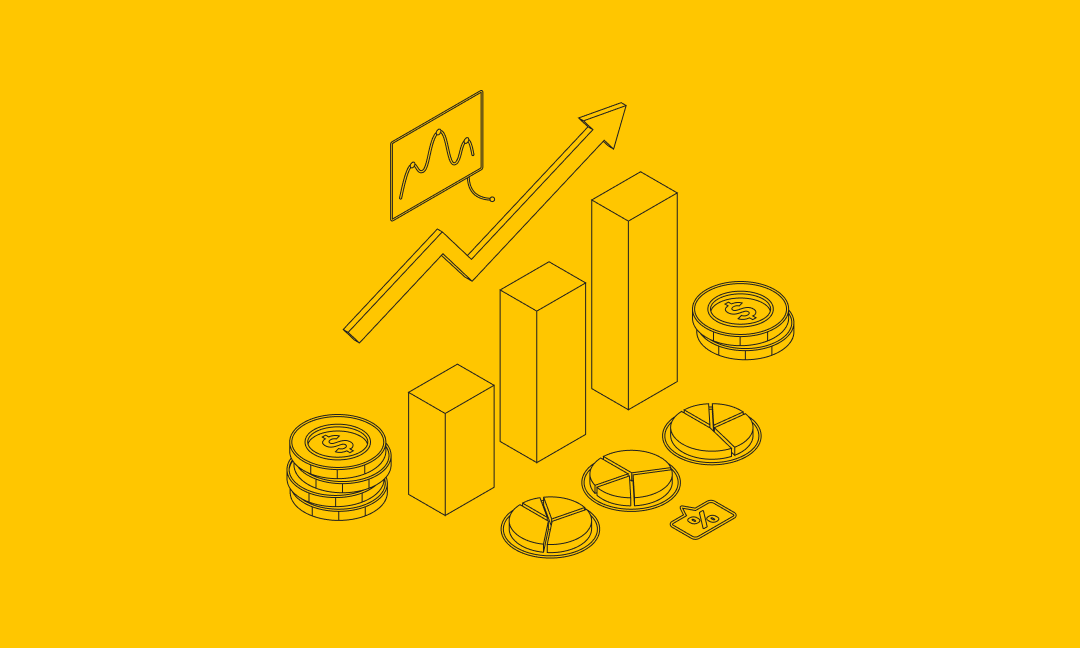
Measuring the ROI of AI: Key Metrics and Strategies
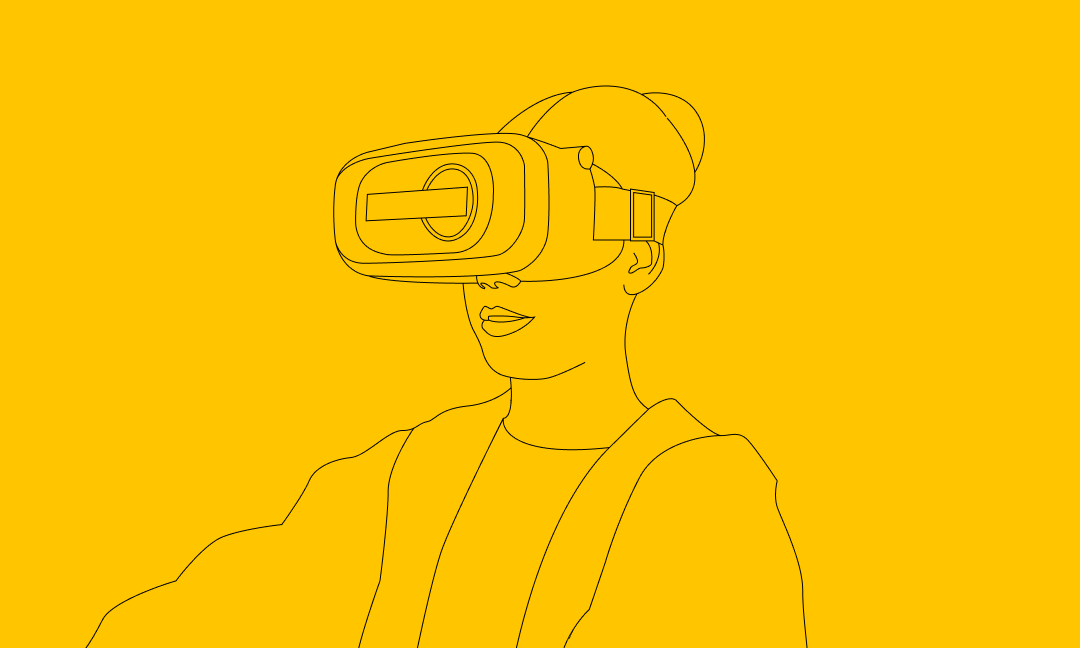
Balancing AI Adoption, Globalization, and Self-Reliance in Tech
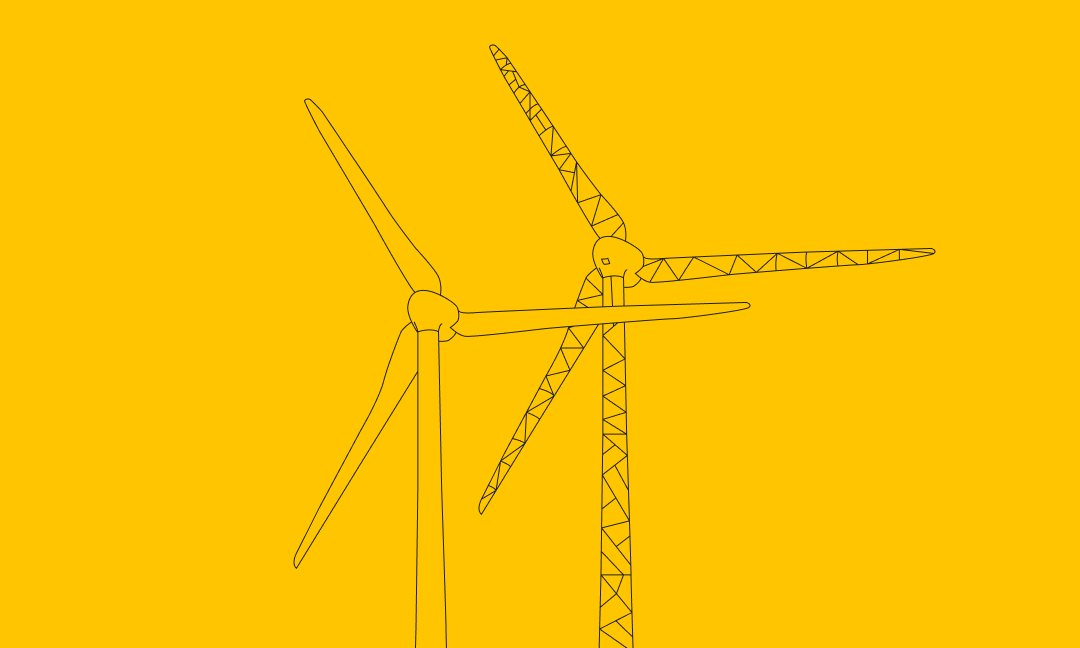
Digital Twins & IIoT for Energy Innovation & Integrated Renewables
What is a transportation management system?
A transportation management system (TMS) software helps businesses plan, execute, and optimize the physical movement of goods across a logistics network. These systems come with management, planning, and analytical features and usually integrate with other business tools for greater visibility of the supply chain.
A transportation management system (TMS) software helps businesses plan...
How does TMS software improve logistics operations?
TMS software streamlines logistics operations by optimizing route planning, automating freight billing, providing real-time tracking, and improving inventory management. These functionalities lead to more efficient resource utilization, cost savings, enhanced customer service, and better decision-making.
TMS software streamlines logistics operations by optimizing route planning...
Can small businesses benefit from implementing a TMS?
Absolutely. Many providers have scalable offerings with advanced customization options and flexible pricing models. Thanks to automation, document generation, tracking, and analytics, even basic software can improve operational efficiency.
Absolutely. Many providers have scalable offerings...
What are the typical costs associated with TMS software?
Expenses depend on factors like deployment type (cloud-based or on-premise), feature set, and scale of operations. Most TMS providers offer a monthly subscription fee that scales based on your user or data load. Additional costs may include customization, integration, employee training, and ongoing support.
Expenses depend on factors like deployment type (cloud-based or on-premise)...
How do I ensure the security of data within a TMS?
Choose a provider that adheres to industry-standard security measures such as user authentication, role-based access control, encrypted communications, and compliance with data privacy laws like GDPR and CCPA. The TMS provider should offer regular security updates and hotfixes. If you’re developing a custom solution, also make sure the software company adheres to ISO/IEC 27002 security standards and practices DevSecOps methodology.
Choose a provider that adheres to industry-standard security measures...
This site uses cookies to improve your experience. By viewing our content, you are accepting the use of cookies. To help us insure we adhere to various privacy regulations, please select your country/region of residence. If you do not select a country we will assume you are from the United States. View our privacy policy and terms of use.
- Inventory Management Software
- Forecasting
- Sustainability
- Supply Chain Visibility

Pricing Optimization at Delly’s: A Case Study in Successful AI Enablement
Talking Logistics
SEPTEMBER 27, 2023
This includes implementing Enterprise Resource Planning (ERP), Customer Relationship Management (CRM), Demand Planning, Inventory Management , Transportation Management , and Warehouse Management applications. After capturing many of.

[PODCAST] Case Study: How Freight Tech Innovation Provided Efficiency & Reduced Freight Costs
GlobalTranz
MARCH 10, 2020
Freight & Logistics Technology Resources 2020 Strategic Freight Management Trends Download White Paper An Introduction to Blockchain and Its Potential Benefits and Drawbacks in Supply Chain Management Download White Paper Revenue Growth At The Hand Of Improved Digital Supply Chains.read More.
This site is protected by reCAPTCHA and the Google Privacy Policy and Terms of Service apply.
Trending Sources
Logistics Viewpoints
- The Logistics of Logistics
- Enterra Insights
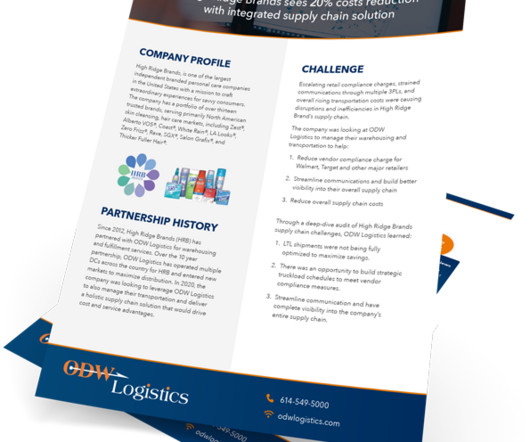
Case Study: High Ridge Brands Sees 20% Cost Reduction with Integrated Supply Chain Solution
Supply Chain Brain
JUNE 30, 2024
High Ridge Brands (HRB) was experiencing supply chain challenges and faced escalating retail compliance charges, communication issues across multiple third-party logistics providers (3PLs), and rising transportation costs, prompting a need for streamlined operations.

Profiles in Transportation Management Excellence: Molson Coors’ Success with Drop and Hook
SEPTEMBER 5, 2024
There are many ways to reduce waste and improve efficiencies in transportation management , and in our latest installment of “Profiles in Transportation Management Excellence,” Jeff Bishop, Category Manager Transportation and Logistics.
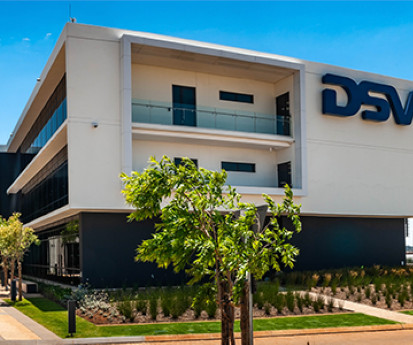
Case Study: DSV Implements a Single-Instance Control Tower with a Global Footprint
Advertisement
As a customer of Kinaxis’s end-to-end logistics and transportation management system, which is used at the DSV Solutions sites in Europe, DSV reached out to Kinaxis to develop a global supply chain control tower solution that would meet those needs in South Africa.
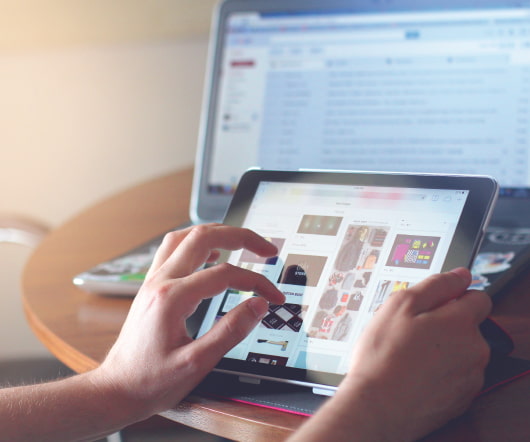
TMS for SMB: A Case Study with Carhartt
OCTOBER 19, 2016
What defines the small and mid-sized business (SMB) market for transportation management systems (TMS)?
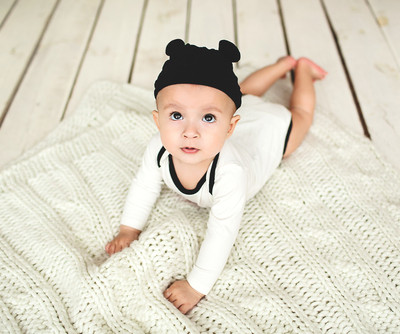
Thoughts. Selecting Supply Chain Software
Supply Chain Shaman
APRIL 29, 2024
I still hold hope that SAP could get serious about supply chain planning, but I have given up on Oracle (with the exception of transportation management .)) Then build business case studies (think back to your business school case studies ) describing the opportunity. Put your case studies in your briefcase.

BASF Video Case Study: The Value of Real-Time Freight Visibility
MAY 3, 2018
The post BASF Video Case Study : The Value of Real-Time Freight Visibility appeared first on Talking Logistics with Adrian Gonzalez. Then post a question or comment and share your perspective on this topic! For related commentary, see On-Time In-Full (OTIF) and the Growing Demand for Real-Time Freight Visibility.
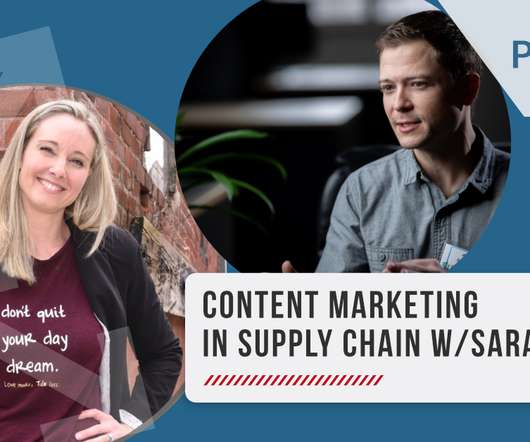
[PODCAST] The Growing “Influence” of Content Marketing in the Supply Chain
MARCH 3, 2020
Business and Marketing Resources Marketing Logistics Services: A Discussion on Getting Attention Online Listen to the Podcast Example of an Effective Transportation Management Case Study View Case Study How Industrial Companies Can Pivot to Inbound Organizations & Increase Customer Experience Listen.read More.

How Nortera Modernized Its Logistics Operations with a Transportation Management System
AUGUST 13, 2024
Read more The post How Nortera Modernized Its Logistics Operations with a Transportation Management System appeared first on Talking Logistics with Adrian Gonzalez. Additionally, burdened by insufficient visibility into logistics operations and a lack of coordinated strategy, the company was lagging behind the rest of the industry.
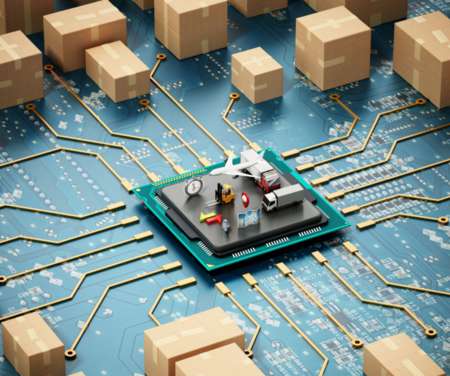
Modern Ways Technology Provides Transportation Management & Freight Spend Visibility
Intelligent Audit
AUGUST 25, 2022
This allows a company to respond to the problem and minimize spending spikes, optimizing the whole transportation management system. What Is Freight or Transportation Spend Management ? A transportation management system simplifies the process of planning out logistics. View the Case Study ) .
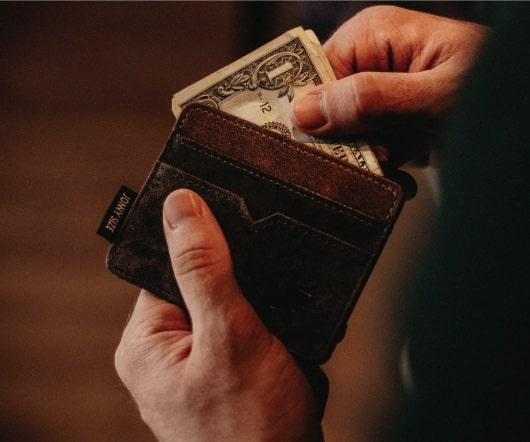
Transportation Management Case Study: Medical Supply Company Decreases Freight Claims Percentage, Improves Visibility, & Reduces Costs
NOVEMBER 15, 2017
In a first of several case studies to come out from Cerasis regarding how our solutions aid shippers in managing transportation more effectively thru our transportation technology and managed services, learn how a Medical Supply Company switched providers and increased overall results.
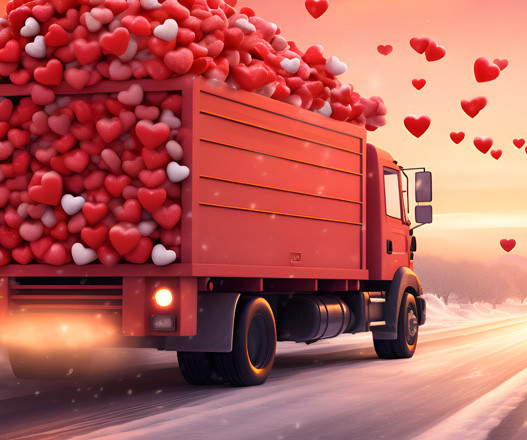
Heart of Efficiency: 3 Logistics Case Studies that Show the Love
MercuryGate
FEBRUARY 13, 2024
Transportation management professionals love the seamless integration of logistics technology and collaboration, leading to operational excellence. This article dives into three compelling logistics case studies showcasing how MercuryGate enhances transportation management for three of our clients.
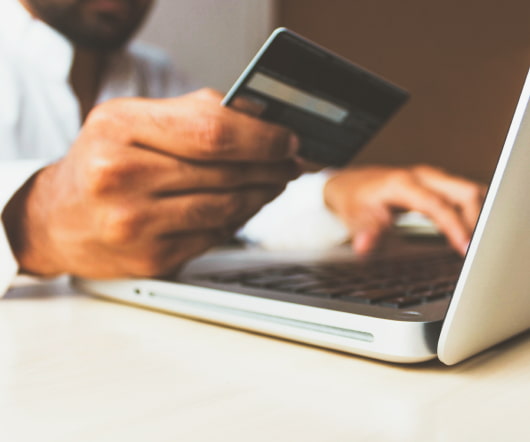
Case Study: People and Processes Drive Supply Chain Improvements at Honeywell
MAY 8, 2019
Then you’ll be able to leverage your transportation management system (TMS) to execute, automate, and optimize those processes, as well as gain visibility to business intelligence to drive continuous improvement. Wednesday, May 15 in Grand Sonoran E. Click here for more information on the session.
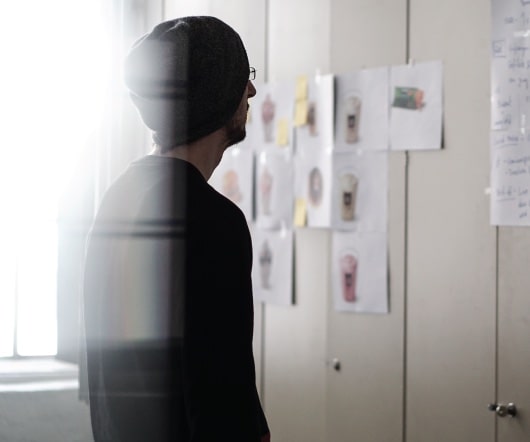
LTL Freight Class: DIM Pricing Updates & A DIM Pricing Case Study
JANUARY 29, 2020
The post LTL Freight Class: DIM Pricing Updates & A DIM Pricing Case Study appeared first on Transportation Management Company | Cerasis. Throughout the strategic freight series, we sought.read More.
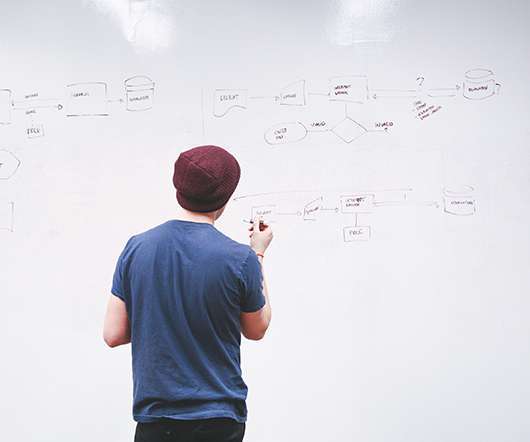
Case Study: How Generac Power Systems Cut Millions from Its Global Transportation Spend
CH Robinson Transportfolio
MARCH 28, 2018
Generac implemented our global transportation management system (TMS), Navisphere ® and integrated it with its enterprise resource planning (ERP) system. The post Case Study : How Generac Power Systems Cut Millions from Its Global Transportation Spend appeared first on Transportfolio.
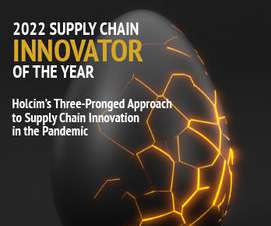
Watch: Leveling Transportation Demand at Kimberly-Clark
DECEMBER 1, 2022
Ron Sweet, senior consultant at Kimberly-Clark, describes how the CPG giant optimized transportation management , in this case study submission to the 2022 Supply Chain Innovator of the Year Award.
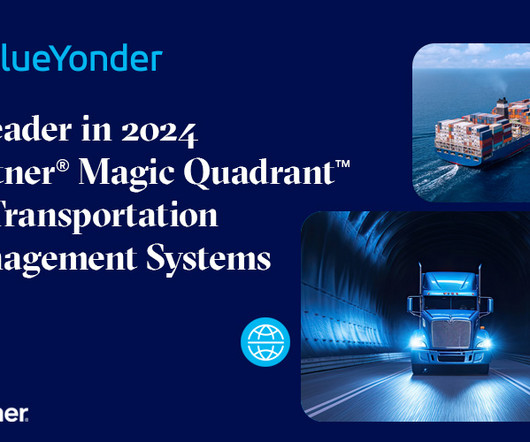
Blue Yonder is a Gartner® Magic Quadrant™ Leader 13 Years in a Row
APRIL 2, 2024
This blog was co-written by Terence Leung and Jen McQuiston Our customers depend on Blue Yonder Transportation Management to achieve customer-centricity and operational resiliency across the globe. Transportation Optimization microservice: top-tier Blue Yonder planning made available to wider audience via a standalone API.
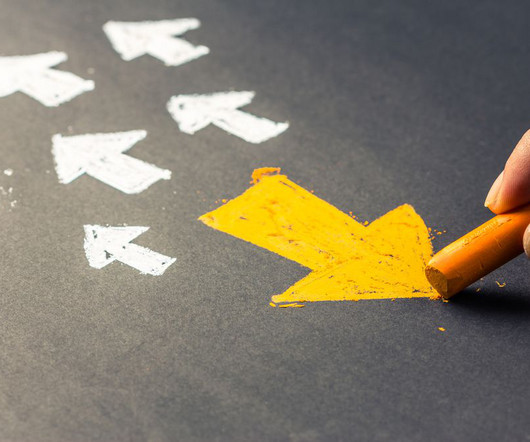
Elevating The Voice of the Supply Chain Contrarian
JUNE 21, 2023
Managing the Contrarian Deep Inside Of Me It is hard to manage the contrarian deep inside of me. Many of the case studies being presented at today’s conferences were born during the pandemic and the post-pandemic turbulence. While companies talk digital, the projects follow traditional supply-centric paths.
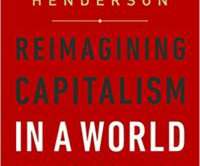
Walmart in a World on Fire
NOVEMBER 15, 2021
I’ve long argued that implementing a transportation management system (TMS) is a great way to save money while going green. Henderson sums up the Walmart case study by saying, “Walmart’s breakthrough came from focusing on the everyday operational details of the business – from a profoundly different perspective.”.
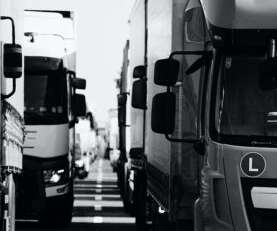
Driver Shortage, Driverless Vehicles, and Other Supply Chain Curiosities
JULY 27, 2021
An impressive case study to be sure, but alas, the cost of the technology is still prohibitive for most companies. As a Senior Director at Open Sky Group, Byron’s focus is building and growing the Transportation Management practice. Byron Davis, Senior Director, Client Services, Open Sky Group.
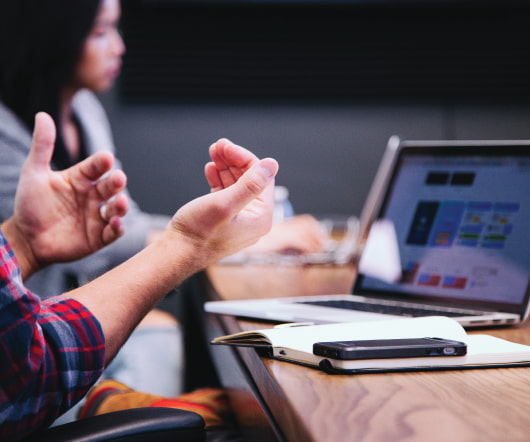
Making the Case for a Different Kind of TMS
JUNE 14, 2017
In Making the Case , we’ll explain how a modern, feature-rich and user-friendly TMS can reduce your freight spend, improve service levels, streamline your logistics functions and give you more control over your end-to-end supply chains. Download Making the Case for a Modern-Day Transportation Management System.
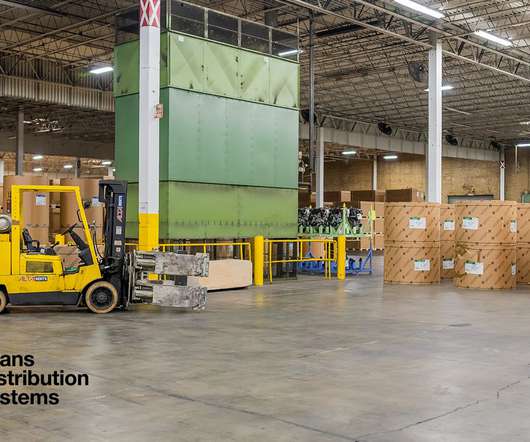
Case Study: Paper Made Easy
3PL Insights
FEBRUARY 23, 2021
transports a high daily volume of inbound and outbound paper truckloads. According to Deanna Smith, Transportation Supervisor at Evans, there are several advantages to having a full-service transportation management solution. The post Case Study : Paper Made Easy appeared first on Evans Distribution Systems.
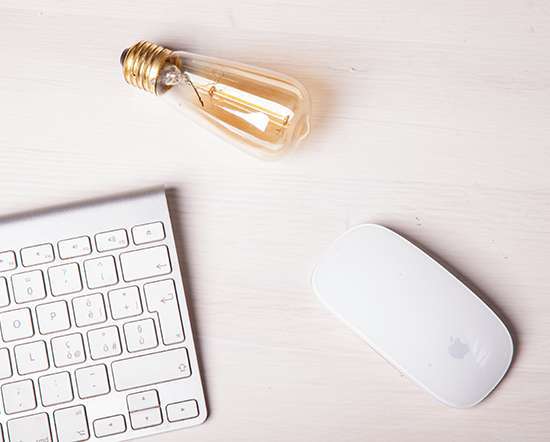
Revisiting Transportation Forecasting
MAY 20, 2013
Watch as Adrian discusses: Two key reasons why transportation forecasting has been a challenge to implement. Trends that are causing shippers, carriers, and technology providers to revisit transportation forecasting. Case studies from Unilever and Canadian Tire. Next steps to driving adoption. Be Sociable, Share!
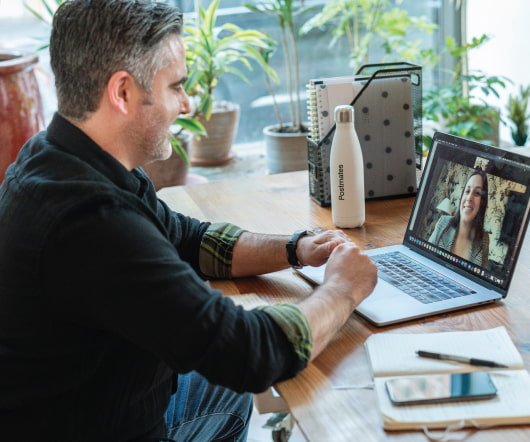
The Road to Big Data Visibility Doesn’t Run Through Your 3PL Technology
AUGUST 7, 2014
So you’re a shipper intrigued by Big Data tools and technology to improve transportation management initiatives. The 18 th Annual CapGemini Third Party Logistics Study revealed some interesting data regarding shippers’ usage of technologies, systems, and tools to leverage Big Data in their supply chain initiatives.
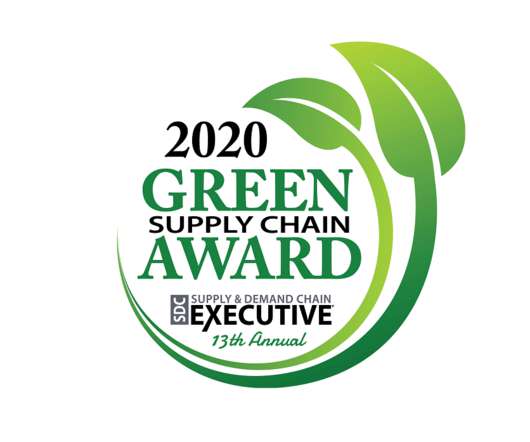
ADEXA Receives 2020 SDCE Green Supply Chain Award
DECEMBER 14, 2020
From software solutions to transportation management systems to several other initiatives designed to reduce carbon footprint and improve the re-use of materials, sustainability continues to rank as a key component to a stronger, safer and more efficient supply chain.”.

Blockchain in Supply Chain: 2 Ethereum-Based Projects That Demonstrate How Blockchain Can Improve Supply Chains
FEBRUARY 6, 2018
Provenance cites a case study with major British grocer The Co-Op: “ Provenance linked together data from the farm, factory, Co-op depot and retail branches, building a digital history that store colleagues, the food team, and shoppers can all access. Blockchain in supply chain changes that.
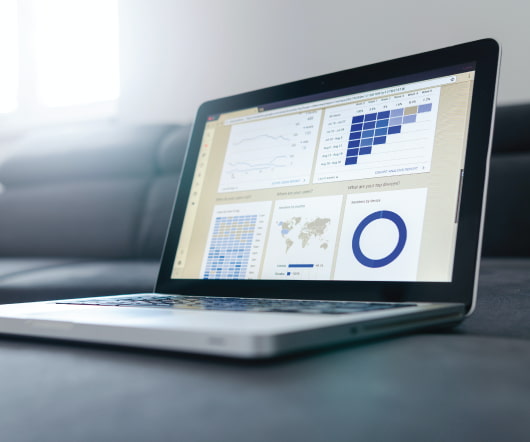
Five Reasons Why Food Shippers are Eating Up TMS Solutions
APRIL 17, 2014
Transportation Management Systems (TMS) is fast becoming a go-to tool for supply chain management professionals across every industry. Here are five reasons why TMS for transportation automation and optimization is a must-have for food shippers. Reason #1 – TMS adds shelf time.
The Google TMS?
DECEMBER 2, 2014
Then join us over the fold as we imagine what a Google TMS ( transportation management system) would look like. These and many, many more offerings from Google could be marshalled into the service of transportation management goals. See the Wall Street Journal article about its (don’t be) ‘evil’ plan.
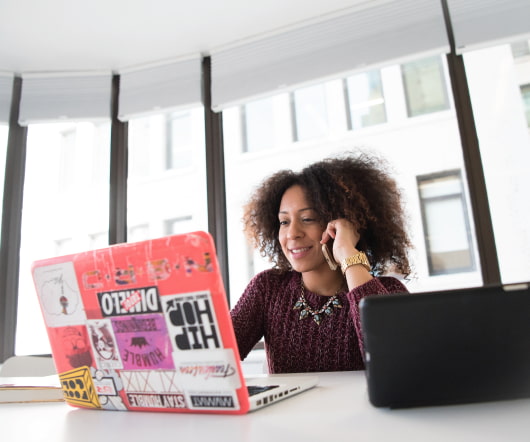
A Truth About Global Transportation: It Happens Locally
MARCH 30, 2016
As shippers of all sizes expand their global sourcing, manufacturing, and distribution operations, they have to navigate the complexities involved with global transportation management . So, how do you know if you’re a leader or laggard in global transportation management ?
Extend the Benefits of Your Transportation Management System (TMS) with an ERP Integration
OCTOBER 30, 2019
At their core, transportation management systems (TMS) help shippers perform logistics management functions like rating, booking and tracking. However, transportation management systems aren’t only limited to rating and booking. However, transportation management systems aren’t only limited to rating and booking.
Building the Business Case for a TMS
JULY 16, 2014
In a past episode of Talking Logistics , Nicholas Carretta, President at UltraShipTMS (a Talking Logistics sponsor), discussed some of the barriers companies face in implementing a transportation management system (TMS), and “building the business case ” was one of the main challenges he talked about.
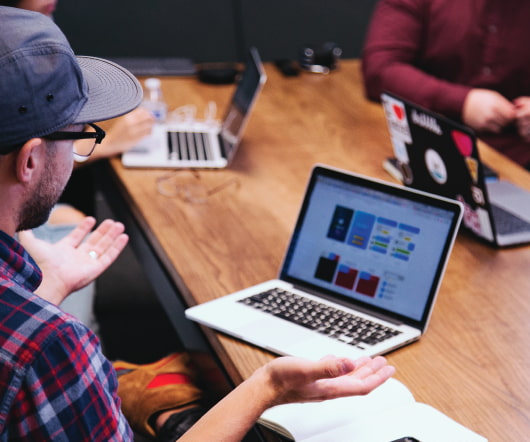
Inventory Optimization Case Study: O'Reilly Auto Parts
Supply Chain Digest
MAY 8, 2009
Supplier Management . Transportation Management Syst. Warehouse Management Systems (. Content Being Accessed: Inventory Optimization Case Study : OReilly Auto Parts. OReilly Auto Parts drives inventory management to stay in the fast lane. Supply Chain Agility/Flexibili. Supply Chain Network Design.
Bucking the Trend in Transportation – Simultaneously Cap Rate Growth and Beat Capacity Constraints
OCTOBER 30, 2018
Bucking this trend is a daunting proposition and even those large volume shippers that are already embracing powerful logistics IT solutions to more efficiently manage spend, like transportation management systems (TMS), fleet tools, optimizers and others, are still frequently overpaying greatly for spot moves.
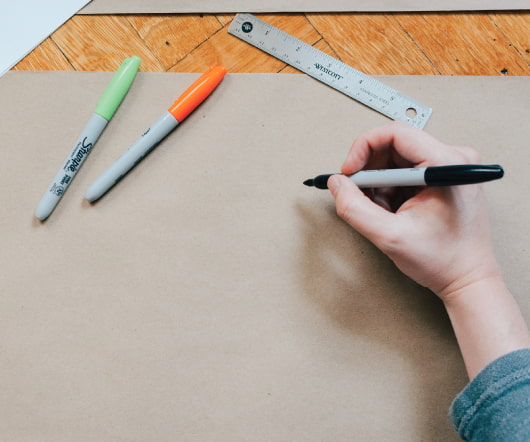
3PL Executive Insights from MercuryGate User Conference 2013
SEPTEMBER 25, 2013
While at the conference, I also had the opportunity to interview three of MercuryGate’s logistics service provider clients: Michael Bartz from ReTrans; Jeff McDermott , VP of Transportation Management at OHL ; and Phillipp Dismukes , TMS Technology Manager at Old Dominion. Be Sociable, Share!
[PODCAST] How a Shipper Cut Transportation Costs with a TMS & Managed Services
AUGUST 13, 2019
Listen to “How a Shipper Cut Transportation Costs with a TMS & Managed Services” on Spreaker. The post [PODCAST] How a Shipper Cut Transportation Costs with a TMS & Managed Services appeared first on Transportation Management Company | Cerasis.
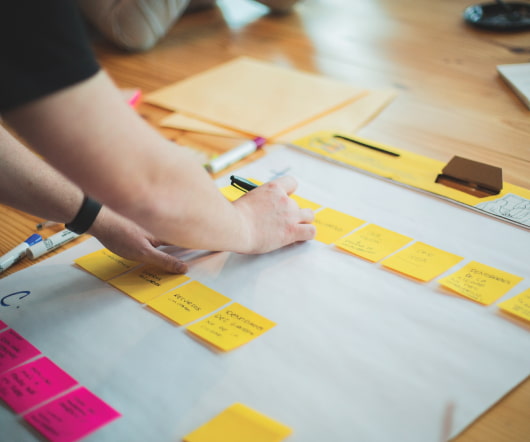
Case Study: Day & Ross Modernizes Route Management for Freight and Same-day Transportation Operations
NOVEMBER 24, 2015
The other system allows us to dispatch trucks and record where they’re going—a transportation management system as it were.” Paul has a diverse background with experience managing technology projects, solutions and companies. Paul has a Bachelor of Science in Systems Engineering and Management from the U.S.
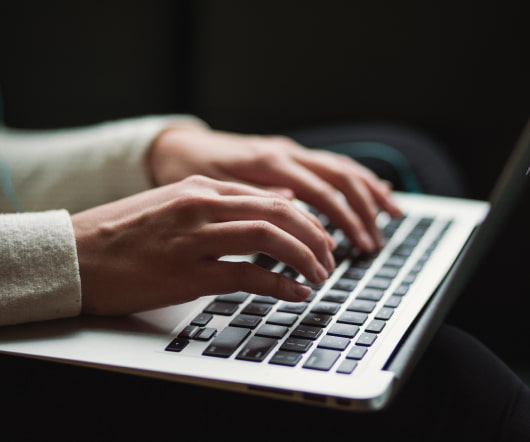
Distribution Center Robots: How Robots Continue to Power the Distribution Center
APRIL 6, 2018
While robotics have resulted in some job loss, the case studies of Amazon, as noted by The New York Times , reveal that Amazon has added more than 80,000 jobs since they began adding Kiva robots to their distribution centers.
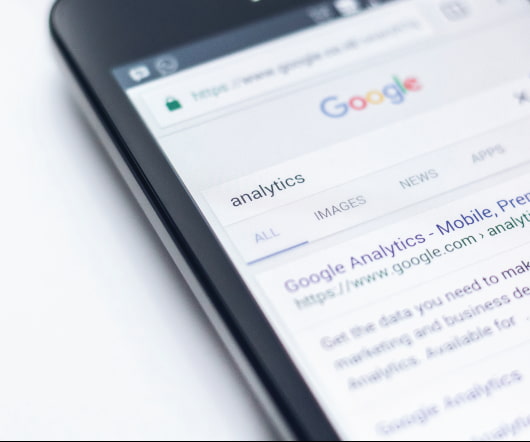
Preparing Tomorrow’s Supply Chain Leaders: The Importance of Technology Skills and Experience
MARCH 31, 2015
More than ever before, this means providing students with hands-on experience using enterprise software applications, such as transportation management systems (TMS). Students use self-paced, online training to learn the ins-and-outs of the software, and then put it to use by solving real-world examples and case studies .
[PODCAST] Improving Trucking Marketing & How to Work with Industry Influencers
NOVEMBER 12, 2019
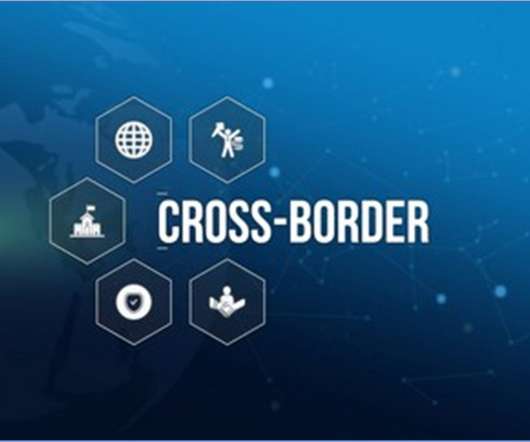
Free Trade Zone – Is Your 3PL Giving You All the Warehouse and Distribution Cost Savings You Deserve?
ModusLink Corporation
FEBRUARY 8, 2023
Asking for references and case studies from previous clients. It’s essential to use the latest technology and transportation management service providers, such as ModusLink, to maximize their value. Verifying the 3PL’s experience and expertise in FTZ setup and operations. Bibliography Forster, James.
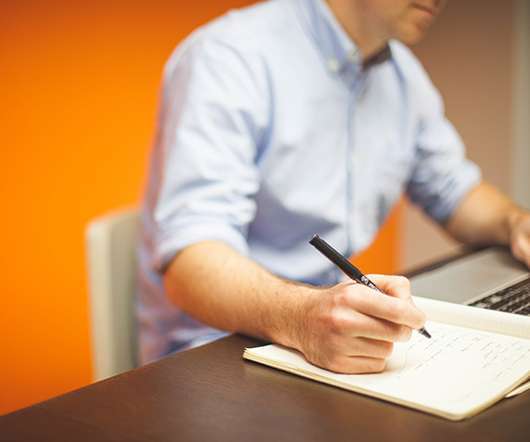
Columbia Sportswear: Peeling Back the Onion on Your Supply Chain Processes
MAY 13, 2015
Like the multi-billion dollar chemical manufacturer that had been paying market rates for ocean transportation for eight years because nobody realized that their contract, filed away in a drawer by a transportation manager who had left the company, had expired. million and net profit 45% to $137.2
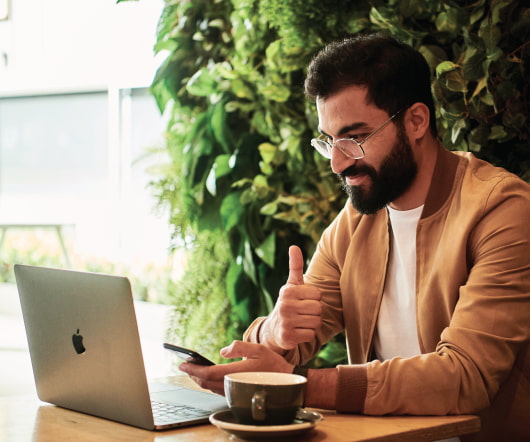
Parcel Shipping: It’s Anything But Simple
MARCH 16, 2016
So, how are leading companies leveraging parcel solutions to manage the complexities of parcel shipping? Watch the short clip below for Steve’s response, where he talks about how each carrier essentially has their own “rule book” for how to do business with them, and how those rules differ by region and are continuously changing.
Stay Connected
Join 136,000+ Insiders by signing up for our newsletter
- Participate in Supply Chain Brief
- How to achieve six-figure benefits from digitizing paper-based supply chain operation
- 2019 Supply Chain Brief Summer Reading List
- Stay At Home Reading List
- Add a Source
- Add a Resource
- 2018 Supply Chain Brief MVP Awards
- 2019 Supply Chain Brief MVP Awards
- 2020 Supply Chain Brief MVP Awards
- 2021 Supply Chain Brief MVP Awards
- 2022 Supply Chain Brief MVP Awards
- Fri. Sep 06
- Thu. Sep 05
- Wed. Sep 04
- Tue. Sep 03
- Aug 24 - Aug 30
- Warehousing
- Procurement
- Transportation
- Supply Chain
- More Topics

Input your email to sign up, or if you already have an account, log in here!
Enter your email address to reset your password. a temporary password will be e‑mailed to you., be in the know on.
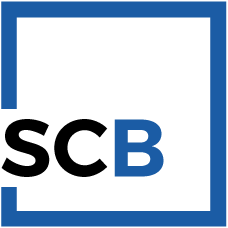
Supply Chain Brief
Expert insights. Personalized for you.
We organize all of the trending information in your field so you don't have to. Join 136,000+ users and stay up to date on the latest articles your peers are reading.

Get the good stuff
Subscribe to the following Supply Chain Brief newsletters:
You must accept the Privacy Policy and Terms & Conditions to proceed.

You know about us, now we want to get to know you!
Check your mail, we've sent an email to . please verify that you have received the email..
We have resent the email to
Let's personalize your content
Use social media to find articles.
We can use your profile and the content you share to understand your interests and provide content that is just for you.
Turn this off at any time. Your social media activity always remains private.
Let's get even more personalized
Choose topics that interest you., so, what do you do.
Are you sure you want to cancel your subscriptions?
Cancel my subscriptions
Don't cancel my subscriptions
Changing Country?
Accept terms & conditions.
It looks like you are changing your country/region of residence. In order to receive our emails, you must expressly agree. You can unsubscribe at any time by clicking the unsubscribe link at the bottom of our emails.
You appear to have previously removed your acceptance of the Terms & Conditions.

We noticed that you changed your country/region of residence; congratulations! In order to make this change, you must accept the Aggregage Terms and Conditions and Privacy Policy. Once you've accepted, then you will be able to choose which emails to receive from each site .
You must choose one option
Please choose which emails to receive from each site .
- Update All Sites
- Update Each Site
Please verify your previous choices for all sites
Sites have been updated - click Submit All Changes below to save your changes.
We recognize your account from another site in our network , please click 'Send Email' below to continue with verifying your account and setting a password.
You must accept the Privacy Policy and Terms & Conditions to proceed.
This is not me
-min.png)
SAP Transportation management implementation for a transport company
LeverX helped a large transport company to achieve transparent reporting, reduce transportation costs, and optimize routes with SAP TM.
Table of contents:
Large European transport company.
A European trucking company needed a system to enhance logistics processes, simplify data processing, and provide comprehensive reporting.
SAP TM meets all the requirements above and contributes to reducing transportation costs, streamlining carrier cooperation, and making logistics operations more transparent. The LeverX project team was responsible for the SAP TM implementation, customization, and integration with third-party solutions to provide unified infrastructure.
Project Scope
- Among the key modifications to add into the standard SAP TM product was a module responsible for ferry transportation and developed from scratch.
- Our team integrated SAP TM with a product for optimizing a truck finding process.
- The customer uses a route optimization solution that defines the detailed routing for a tour. As soon as SAP TM itself lacks this option intended for trucks, we ensured the integration of the products taking into account all particular aspects.
- Software for on-board units lets truck drivers get all info, such as the assigned tasks or predefined routes, and track their progress or inform about traffic conditions. This was also the third-party product we integrated with SAP TM in terms of the project.
- Constant tracking of a truck provided by the customer’s product was also available. Thanks to the integration of SAP TM and the third-party software, it is now easy to get informed about the truck’s geolocation and key events, including loading/unloading, shipping, or delivery, as they are being reported automatically in real time.
- We also involved SAP Event Management, an application that contributes to monitoring and managing events.
TOP SAP Company
Project Results
The SAP TM implementation allowed the European trucking company to:
- Enhance logistics management.
- Simplify transportation planning.
- Gain more detailed and easy-to-use reporting.
- Increase the visibility of all transport operations thanks to the automated event monitoring system, SAP Event Management.
- Optimize transportation resource utilization.
- Reduce transportation cost through the optimization of transportation routes.
More Case Studies
What happens next?
An expert will reach out to you to discuss your specific migration needs and requirements.
We will sign an NDA to ensure any sensitive information is kept secure and confidential.
We'll work with you to prepare a customized proposal based on the project's scope, timeline, and budget.
- Who is MD Logistics
- MD Logistics West Coast 3PL
- MD Logistics East Coast 3PL
- MD Logistics Midwest 3PL
- Meet Our Executive Team
- Strategic Partnerships
- Community Outreach
- MD Logistics’ Awards
- Join Our Team
- Life Science & Pharmaceutical Cold Chain Logistics Management
- Retail & Consumer Goods Supply Chain Management
- Freight Forwarding & Transportation Services
- e-Commerce Fulfillment and Omni-Channel Logistics
- Quality Excellence in 3PL
- Quality Certifications
- Supply Chain Sustainability
- Supply Chain Case Studies
- Logistics White Papers
- Logistics Blog
CUSTOMIZED SUPPLY CHAIN SOLUTIONS
Case Studies / Transportation Management System Case Study
Transportation Management System Case Study
Posted on February 3, 2014
Integrating with the Agile TMS, MD Logistics offers clients more efficient and effective transportation options.
BACKGROUND | Printer Friendly PDF Transportation expenses associated with shipping commodities across the world can be mitigated with strategic freight decisions. Successful companies understand the importance of freight optimization, which is the process of strategically selecting carriers based on a variety of factors, including price, service offerings and retail compliance.
CHALLENGE MD Logistics recently upgraded its Transportation Management System (TMS) as part of ongoing improvements to its supply chain support systems. The existing legacy TMS was used to manually optimize freight solutions for customers that elected for the value-added service. However, it lacked full integration to the WMS and the ability to rate shop and optimize freight spend and routing automatically
MD Logistics also noticed that other customers were opting to price carriers, negotiate rates and handle freight decisions in-house. This approach often resulted in customers securing high freight prices for carriers that weren’t the most strategic choices for their commodities.
WHY MD LOGISTICS WAS THE SOLUTION To better serve customers, MD Logistics implemented the Agile TMS and integrated it into its current Red Prairie Warehouse Management System (WMS). This integration allows MD Logistics to find customers the most strategic carrier based on a variety of factors, including price, transit times and retail compliance.
This turnkey solution requires no human intervention, such as manual entry or carrier negotiation, once rates and services are established. Instead, Agile TMS works with the WMS to automatically price shipments simultaneously amongst carriers that meet a customer’s specific delivery needs.
RESULTS MD Logistics can efficiently and cost-effectively handle freight selection and important tasks such as filing claim paperwork, auditing invoices and managing non-deliverables for customers that opt for the value-added service. The integrated TMS also removes guesswork from the equation; customers can track their shipments until final delivery through MD Logistics’ online portal, MD Net.
BENEFIT TO THE CLIENT Cost-Savings With integrated freight optimization, MD Logistics can efficiently use its significant buying power to negotiate the most advantageous shipping rates for customers.
Quality Control MD Logistics’ Agile TMS identifies the best solutions for each customer. The system shops rates based on important parameters such as delivery date, service offerings and compliance. The system also supports easy tracking for troubleshooting and problem resolution.
Flexibility The Agile TMS increases MD Logistics’ ability to offer customized service offerings. The system also seamlessly communicates with the Red Prairie WMS to ensure customers remain compliant with retailers’ carrier requirements.
Optimization The Agile TMS is able to shop different modes of transportation services, varying from postal, parcel, LTL or FTL. Custom reports are easily generated through the TMS, enabling MD Logistics and customers to analyze their supply chain to make continuous improvements.
If you are looking for a white-glove delivery provider, please tell us a little about your needs .
Case Study Categories
- Freight Forwarding & Transportation Services Case Studies
- Life Sciences & Pharmaceuticals
- Retail & Consumer Goods
Looking for a Third Party Logistics Partner?

Tell us a little about your 3pl needs
Newsletter signup, stay in the loop.
Sign up and we'll keep you updated on supply chain news!
WATCH VIDEO
20th anniversary.
MD Logistics celebrates 20 years in business, 1996-2016.
Read Our Customized Supply Chain Solutions Brochure.
© 2024 MD Logistics, LLC, A NIPPON EXPRESS Group Company. All Rights Reserved.
Privacy Policy | Sitemap
Privacy Overview
About Motifworks
At Motifworks, we are AZURESMART. We are one of the fastest-growing cloud solutions providers, specializing in Cloud Adoption, Application Innovation, and Effective Data Strategies. Our passion is to empower you to accelerate your digital transformation initiatives using the Microsoft Azure cloud. We’re here to simplify your path to explore what’s possible.
Corporate Office
200 W Townsontown Blvd, Suite 300D, Towson, MD, 21204, US
Regional Offices
Philadelphia ¦ Detroit ¦ Dallas ¦ Florida ¦ Cincinnati ¦ Ohio
Development Office
101 Specialty Business Center, Balewadi Road, Pune- 411045, Maharashtra, India
Connect with us
For the 5th Time in a Row, Motifworks Inc. Appears on the Inc. 5000 List ➜ Motifworks won Bronze Stevie® Award for Technical Innovation of the Year 2022 ➜ -->
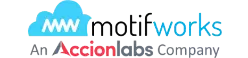
Motifworks and Atlas Oil create StormProof – A State-of-the-art Cloud Transportation Management System
StormProof: A State-of-the-Art Cloud Transportation Management System by Motifworks for Atlas Oil
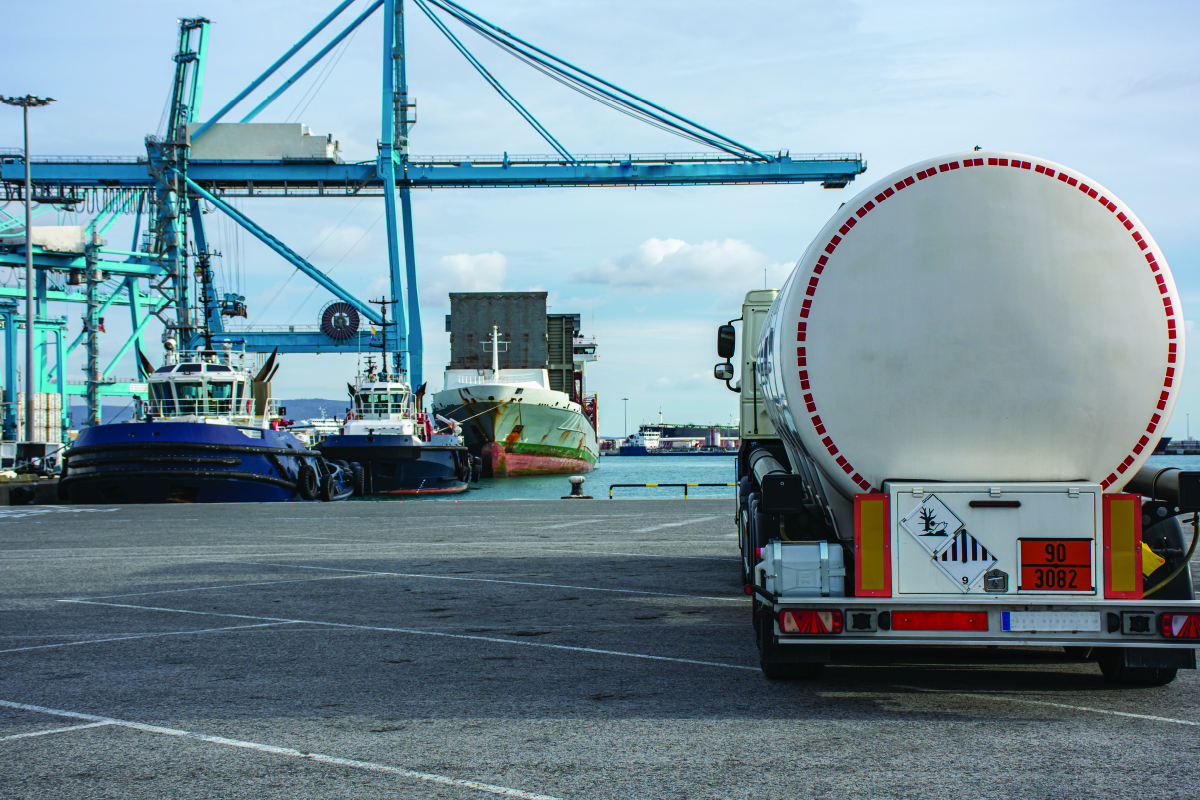
The ability to have uninterrupted power during hurricanes, storms, and other such natural disasters is essential for mission-critical and essential services like hospitals, data centers, and banking operations, among others. It is a complex process that involves fueling assets, drivers, and mobile tanks sourced from multiple places around the country, leveraging the nationwide logistics network. Being able to track vehicles and fuel inventory real-time 24x7 and support multiple variations and exceptions to the default process is the key to fortify such operations seamlessly.
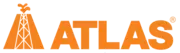
The ability to have uninterrupted power during hurricanes, storms, and other such natural disasters is essential for mission-critical and essential services like hospitals, data centers, and banking operations, among others. It is a complex process that involves fueling assets, drivers, and mobile tanks sourced from multiple places around the country, leveraging the nationwide logistics network and cloud transportation management system. Being able to track vehicles and fuel inventory real-time 24x7 and support multiple variations and exceptions to the default process is the key to fortify such operations seamlessly.
Business Challenges
We are on a digital journey as a company. We wanted to become a digital energy solution provider and we knew we couldn’t do it alone, so we turned to Motifworks to help us achieve our goals.
– Bob Kenyon, Former President, Atlas Oil
- Unpredictable weather and storms create immense problems for mission-critical (Hospitals, data centers, emergency services, etc.) businesses that need to function despite power outages caused by natural disasters.
- Atlas Oil was struggling with its current transportation management systems and effectively manage the variability of the customers service model that leverages the trucking network combined with third parties.
- They were also finding it difficult to track their fuel truck drivers, and address challenges like difficulties with understanding important information such as travel location, fuel availability, and transport options.
- The Client wanted to leverage new technology and cloud transportation management system to provide better support for their customers.
- They also needed to find and contact local carriers that could perform the work necessary for their clients in need. The information they needed to access, and gather was crucial in providing the best possible service for their clients.
- Overall, Atlas Oil was looking to efficiently execute their emergency fuel services (EFS) and modernize their current fueling processes to better manage third party partners and to better serve their customers.
Motifworks Solutions: Maximizing Efficiency, Accuracy, and Reliability with Cloud Transportation Management System
- Atlas Oil needed to work with a partner who could deliver results quickly and efficiently. More importantly, they needed a partner who they could trust to understand the importance of EFS and execute the process quickly, efficiently, and effectively
- Through application modernization service , Motifworks experts built a cloud-native platform called ‘StormProof’ for Atlas Oil to help them better manage its emergency fueling services.
- The StormProof App is a digital solution built for fuel truck drivers who are part of Atlas Oil’s National Emergency Fueling Response Team.
- The application facilitates driver’s performance in their day-to-day fuel distribution activities. Architecture to support real-time operations and high performance was just one of the many challenges.
- The main features include real time geo-location tracking, live chat with the Atlas Logistics Coordinators (ECC), order processing, submitting transactions, and daily inventory check.
- StormProof also helps fuel truck drivers locate nearby carriers so they can track, update, and effectively manage third party carriers and partners.
- This cloud transportation management system features a smart dashboard with real-time analytics, and delivery tracking across multiple sites, making it an extremely sophisticated application in its class. The dashboard also makes the order loading and processing feature extremely efficient and seamless as the entire workflow can be exercised right from the dashboard/map view.
- The Maps use Google API and records latitude and longitude of specific areas combined with satellite shots from Google to make sure the deliveries are done at the right location at the right time every single time.
Motifworks has become a trusted partner of Atlas. They have put in the time and effort to learn our business and understand our goals. We can trust that they will solve our problems to create opportunities and create valued solutions. They are an idea machine that creates innovative solutions, and we know we can rely on them.
With Motifworks’ AzureSmart approach and solutions, Atlas Oil was able to effectively managed, monitor, and track all the necessary components of the fueling process, so they can stay true to their mission of saving lives and serving communities.
Increased profitability by optimizing the use of drivers
Simplified back office processes such as data processing, increased efficiency by 85%, optimized operations, achieving 100% uptime, increased transparency internally and externally, improved order to cash process by 93%, wish to replicate such success in your business.
Choose Motifworks to build an innovative and peerless cloud-based solution on Azure
Related Posts
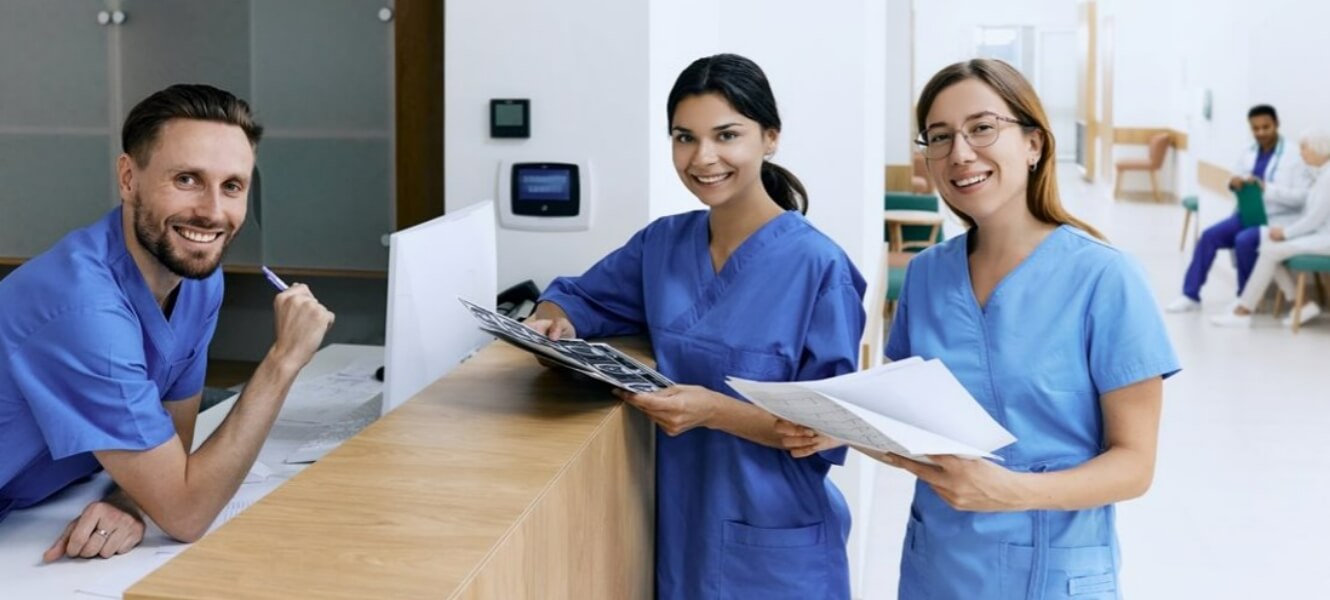
Case Study| Enabling Application Modernization Strategy to improve performance and reliability | Azure Migration Roadmap | App modernization strategy

Electric manufacturing success story that implemented modern data analytics solution
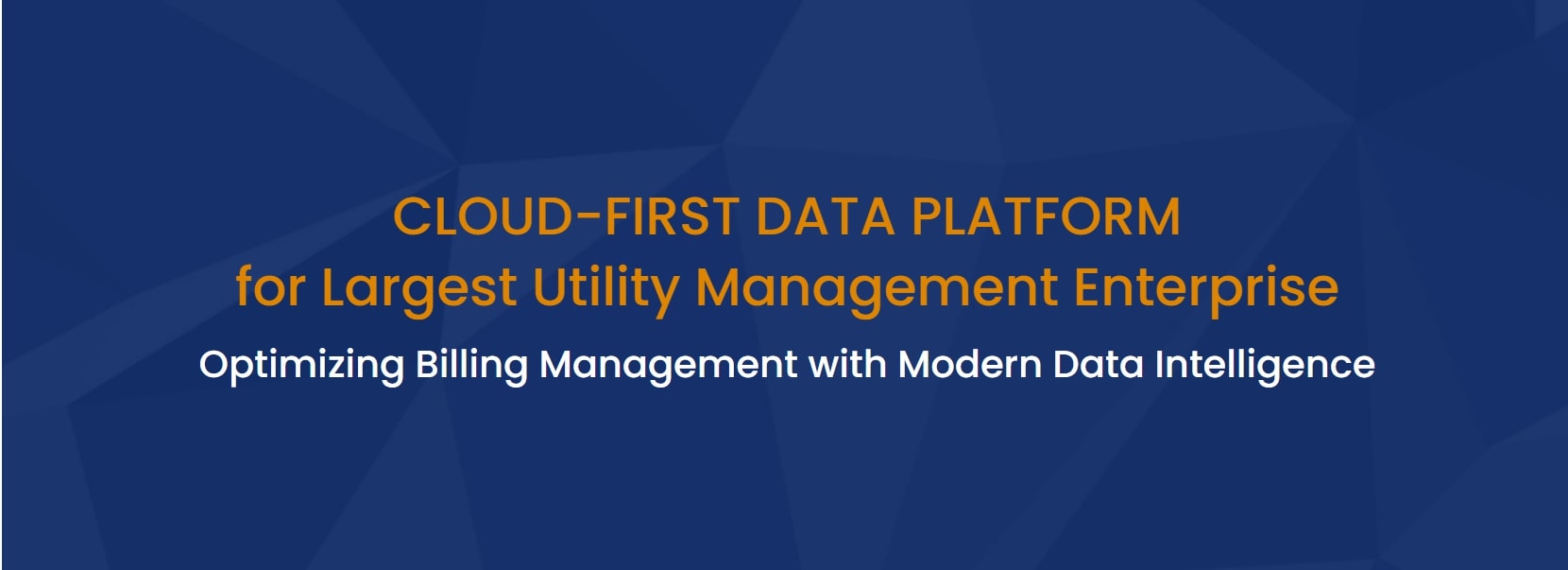
Billing Management System for Utility Management Enterprise
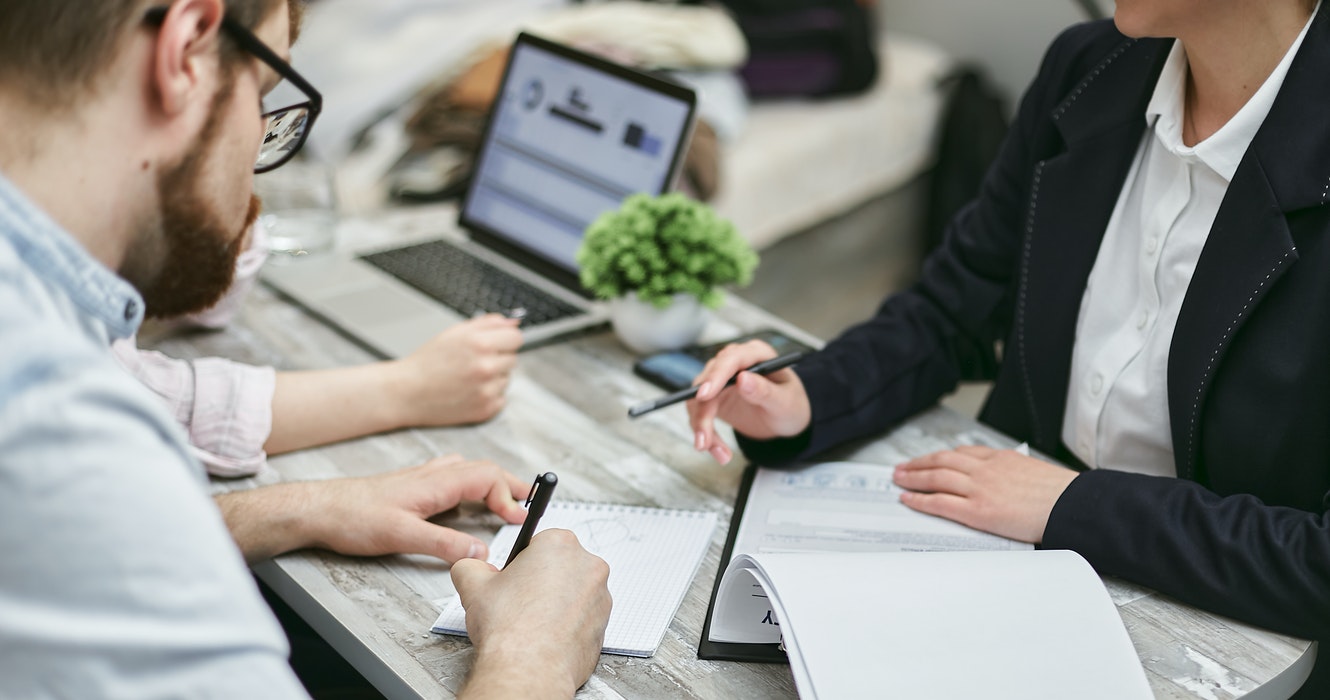
Cloud migration success stories: Insurance Software Provider
Privacy overview.
MBA Knowledge Base
Business • Management • Technology
Home » Management Case Studies » Case Study: Wal-Mart’s Distribution and Logistics System
Case Study: Wal-Mart’s Distribution and Logistics System
As the world’s largest retailer with net sales of almost $419 billion for the fiscal year 2011, Wal-Mart is considered a “best-in-class” company for its supply chain management practices . These practices are a key competitive advantage that have enabled Wal-Mart to achieve leadership in the retail industry through a focus on increasing operational efficiency and on customer needs. Wal-Mart’s corporate website calls “logistics” and “distribution” the heart of its operation, one that keeps millions of products moving to customers every day of the year.
Wal-Mart’s highly-automated distribution centers, which operate 24 hours a day and are served by Wal-Mart’s truck fleet, are the foundation of its growth strategy and supply network. In the United States alone, the company has more than 40 regional distribution centers for import flow and more than 140 distribution centers for domestic flow. When entering a new geographic arena, the company first determines if the area will be able to contain enough stores to support a distribution center. Each distribution center supports between 75 to 100 retail stores within a 250-mile area. Once a center is built, stores are gradually built around it to saturate the area and the distribution network is realigned to maximize efficiencies through a process termed “reoptimization”. The result is a “trickle-down” effect: trucks do not have to travel as far to retail stores to make deliveries, shorter distances reduce transportation costs and lead time, and shorter lead time means holding less safety inventory. If shortages do occur, replenishment can be made more quickly because stores receive daily deliveries from distribution centers.

An important feature of Wal-Mart’s logistics infrastructure was its fast and responsive transportation system. The distribution centers were serviced by more than 3,500 company owned trucks. These dedicated truck fleets allowed the company to ship goods from the distribution centers to the stores within two days and replenish the store shelves twice a week. The truck fleet was the visible link between the stores and distribution centers. Wal-Mart believed that it needed drivers who were committed and dedicated to customer service. The company hired only experienced drivers who had driven more than 300,000 accident-free miles, with no major traffic violation.
Wal-Mart truck drivers generally moved the merchandise-loaded trailers from Wal-Mart distribution centers to the retail stores serviced by each distribution center. These retail stores were considered as customers by the distribution centers. The drivers had to report their hours of service to a coordinator daily. The coordinator scheduled all dispatches depending on the available driving time and the estimated time for travel between the distribution centers and the retail stores. The coordinator informed the driver of his dispatches, either on the driver’s arrival at the distribution center or on his return to the distribution center from the retail store. The driver was usually expected to take a loaded truck trailer from the distribution center to the retail store and return back with an empty trailer. He had to dispatch a loaded truck trailer at the retail store and spend the night there. A driver had to bring the trailer at the dock of a store only at its scheduled unloading time, no matter when he arrived at the store. The drivers delivered the trailers in the afternoon and evening hours and they would be unloaded at the store at nights. There was a gap of two hours between unloading of each trailer. For instance, if a store received three trailers, the first one would be unloaded at midnight (12 AM), the second one would be unloaded at 2 AM and the third one at 4 AM. Although, the trailers were left unattended, they were secured by the drivers, until the store personnel took charge of them at night. Wal-Mart received more trailers than they had docks, due to their large volume of business.
Because Wal-Mart’s fast, responsive transportation operations are such a major part of the company’s successful logistics system, great care is taken in the hiring, training, supervising, and assigning of drivers’ schedules and job responsibilities. From the onset of his retailing career, Wal-Mart founder Sam Walton recognized the importance of hiring experienced people and of building loyalty not only in his customers but also in his employees. The company hires only experienced drivers who have driven more than 300,000 accident-free miles and whom it believes will be committed to customer service. Its retail stores are considered important “customers” of the distribution centers. As stated in the “Private Fleet Driver Handbook” that each driver is given a copy of, drivers are expected to be “polite” and “kind” when dealing with store personnel and others. In addition to containing a driver’s code of conduct, the Private Fleet Driver Handbook gives instructions and rules for following pre-planned travel routes and schedules, the responsible unloading of a truck trailer at a retail store, and the safe-guarding of Wal-Mart’s property. For example, although drivers deliver loaded trailers in the afternoon and evening hours, a trailer can be brought to the store’s docks only at its scheduled unloading time. Because unloading is done at two-hour intervals during the night, a driver is expected to spend the night, returning to the distribution center at a pre-scheduled time with an empty trailer. Coordinators closely monitor the detailed records of each driver’s activities for adherence to rules. Violations are dealt with according to handbook procedures, which include employee education to prevent future occurrences of incorrect actions. By effectively managing every aspect of its transportation operations and treating its drivers fairly, Wal-Mart gets results that are unrivaled in the logistics arena. This philosophy parallels the successful coaching style of New York Giant’s football coach Tom Coughlin who believes that rules are more than just discipline. Rules are a key to consistency, which leads to preparedness, which then leads to proper execution.
To make its distribution process more efficient, Wal-Mart also made use of a logistics technique known as ‘cross-docking.’ In this system, the finished goods were directly picked up from the manufacturing plant of a supplier, sorted out and then directly supplied to the customers. The system reduced the handling and storage of finished goods, virtually eliminating the role of the distribution centers and stores. There were five types of cross-docking.
- Opportunistic Cross docking – In this method of cross docking, the exact information about where the necessary good should be shipped and from where it should be procured and exact quantity which will be sent was necessary. This method of cross docking has allowed the company to ship directly the goods, necessary retail clients, not storing them in warehouse bins or shelves. Opportunistic cross docking could also be used when the warehouse software of management installed by the retailer, has set ready it, that the specific product was ready to moving and could be moved immediately.
- Flow-through Cross docking – In this type of cross docking, there was a constant inflow and outflow of the goods from the distribution center. This type of cross docking was mostly suitable for the perishable goods which had very short interval of time, or the goods which were difficult to be kept in warehouses. This cross docking system was mainly accompanied by supermarkets and other retail discount stores, especially for perishable items.
- Distributor Cross docking – In this type of cross docking, the manufacturer has delivered the goods to directly to retailer. No intermediaries have been involved in this process. It has allowed the retailer to save a major portion of the expenses in the form of storage. As the retailer should not support the distribution center for storage various kinds of the goods, he has helped it to save warehouse costs. The lead time for the delivery of goods from the manufacturer to the consumer was also drastically reduced. However, this method had some disadvantages too. Expenses of transportation both for the manufacturer and for the retailer tended to increase during time when the goods have been required to be transported to different locations several times. Besides, the transportation system should be very fast. Otherwise, the purpose of cross docking has been lost. The transportation system should be also highly responsive and to take the responsibility for delays in delivery of the goods. The retailer was at a greater risk. He has lost that advantage to sharing risks with the manufacturer. This type of cross docking was suitable only for those retailers who had the big distributive network and could be used in situations when goods had to be delivered in a short span of time.
- Manufacturing Cross docking – In Manufacturing cross docking, these cross docking facilities served the factories and acted as temporary and “mini warehouses.” Whenever a manufacturing company required some parts or materials for manufacturing a particular product, it was delivered by the supplier in small lots within a very short span of time, just when it was needed. This helped reduce the transportation and warehouse costs substantially.
- Pre-Allocated Cross Docking – Pre-allocated cross docking is very much like the usual cross-docking, except that in this type of cross docking, the goods are already packed and labeled by the manufacturer and it is ready for shipment to the distribution center from where it is sent to the store. The goods can be delivered by the distribution center directly to the store without opening the pack of the manufacturer and re-packing the goods. The store can then deliver the goods directly to the consumer without any further repacking. Goods received by the distribution center or the store are directly sent into the outbound shipping truck, to be delivered to the consumer, without altering the package of the good. Cross docking requires very close co-ordination and co-operation of the manufacturers, warehouse personnel and the stores personnel. Goods can be easily and quickly delivered only when accurate information is available readily. The information can be managed with the help of Electronic Data Interchange (EDI) and other general sales information.
In cross docking, requisitions received for different goods from a store were converted into purchase or procurement orders. These purchase orders were then forwarded to the manufacturers who conveyed their ability or inability to supply the goods within a particular period of time. In cases where the manufacturer agreed to supply the required goods within the specified time, the goods were directly forwarded to a place called the staging area. The goods were packed here according to the orders received from different stores and then directly sent to the respective customers. To gain maximum out of cross-docking, Wal-Mart had to make fundamental changes in its approach to managerial control . Traditionally, decisions about merchandising, pricing and promotions had been highly centralized and were generally taken at the corporate level. The crossdocking system, however, changed this practice. The system shifted the focus from “supply chain” to the “demand chain,” which meant that instead of the retailer ‘pushing’ products into the system; customers could ‘pull’ products, when and where they needed. This approach placed a premium on frequent, informal cooperation among stores, distribution centers and suppliers with far less centralized control than earlier.
Besides, if the supplier knows also, that for the company it will be incredibly difficult to make proper adjustments to guarantee smooth transition to the different supplier, then they will be less inclined to lower their price as much. It is not, how existing suppliers deal with Wal-Mart; when they see that Wal-Mart has found the supplier who will give them lower price, current suppliers lower their prices accordingly. They know that logistical system of the Wal-Mart can address with transition easily, and consequently they do not receive additional leverage, as it will not be difficult or expensive for Wal-Mart to choose other supplier.
Another reason that Wal-Mart’s prices are so competitive is because they buy in such large quantities that transportation from one end of the supply chain to another is not as expensive for additional units. This aspect of the logistical system does not come from skill or expertise it simply comes from the sheer size of the company, but this is still a factor. On the other hand, the Wal-Mart buys so many supplies from different places throughout the world, that they have the luxury of using bigger trucks and using less fuel to go back and forth. Also if by chance they have to use shipping services to transport material from one location to another, Wal-Mart will give them so much business that they will get huge discounts.
On the whole, the logistical system that Wal-Mart uses is so effective because it is so flexible. This is why Wal-Mart is able to offer things much cheaper than other companies can.
About Wal-mart Stores
Wal-Mart Stores, Inc. is the largest retailer in the world, the world’s second-largest company and the nation’s largest nongovernmental employer. Wal-Mart Stores, Inc. operates retail stores in various retailing formats in all 50 states in the United States. The Company’s mass merchandising operations serve its customers primarily through the operation of three segments. The Wal-Mart Stores segment includes its discount stores, Supercenters, and Neighborhood Markets in the United States. The Sam’s club segment includes the warehouse membership clubs in the United States. The Company’s subsidiary, McLane Company, Inc. provides products and distribution services to retail industry and institutional foodservice customers. Wal-Mart serves customers and members more than 200 million times per week at more than 8,416 retail units under 53 different banners in 15 countries. With fiscal year 2010 sales of $405 billion, Wal-Mart employs more than 2.1 million associates worldwide. Nearly 75% of its stores are in the United States (“Wal-Mart International Operations”, 2004), but Wal-Mart is expanding internationally. The Group is engaged in the operations of retail stores located in all 50 states of the United States, Argentina, Brazil, Canada, Japan, Puerto Rico and the United Kingdom, Central America, Chile, Mexico,India and China.
Related posts:
- Case Study: Wal-Marts Competitive Advantage
- Case Study: Wal-Mart’s Failure in Germany
- Case Study: Business Strategy Analysis of Wal-Mart
- Case Study: An Assessment of Wal-Mart’s Global Expansion Strategy
- Case Study of Walmart: Procurement and Distribution
- Use of Logistics Channel and Public and Private Distribution Facilities – For Material Sources
- Case Study of FedEx: Pioneer of Internet Business in the Global Transportation and Logistics Industry
- Distribution Center Decisions
- Case Study: Strategy of Ryanair
- Case Study: How Netflix Took Down Blockbuster
One thought on “ Case Study: Wal-Mart’s Distribution and Logistics System ”
Leave a reply cancel reply.
Your email address will not be published. Required fields are marked *

FreightPOP Case Studies
See how freightpop has helped companies like yours improve supply chain operations and freight management, freight management case studies.
See how FreightPOP has improved the supply chain and logistics operations for companies like yours with these case studies.
How FreightPOP Helps Odeko Achieve $45,000 In Monthly Savings
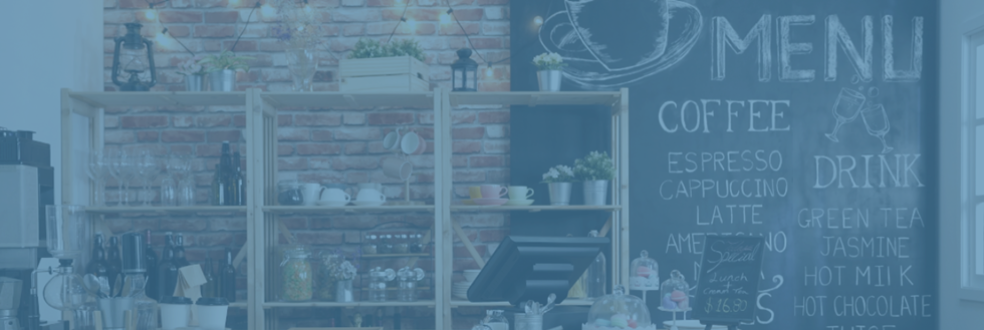
Kyocera Division Case Study - How to Negotiate Fairer Carrier Contracts
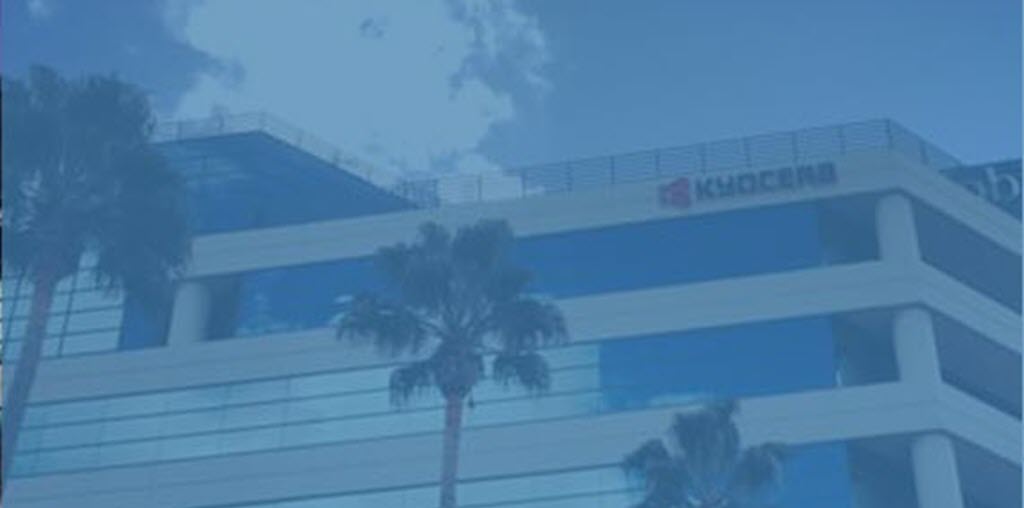
4Wall Entertainment Take Shipping To The Next Level
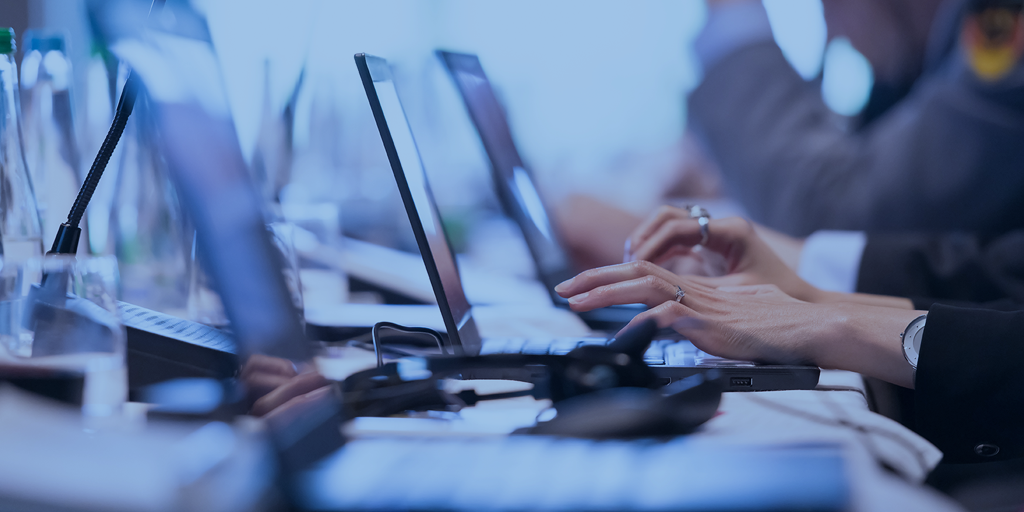
Award-Winning Global Mailer Wins Big With Shipping Software
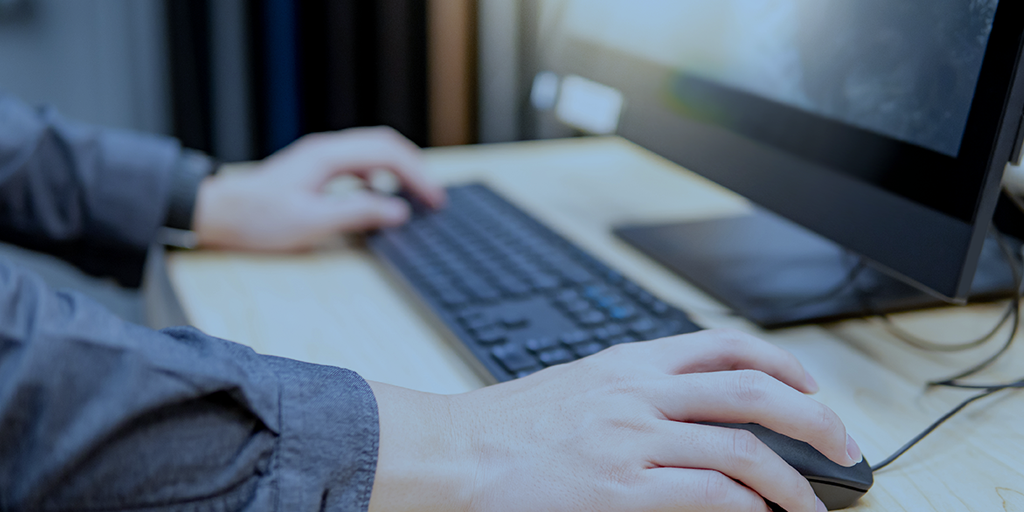
LogiQuip Counts On Shipping Software For Custom Integrations
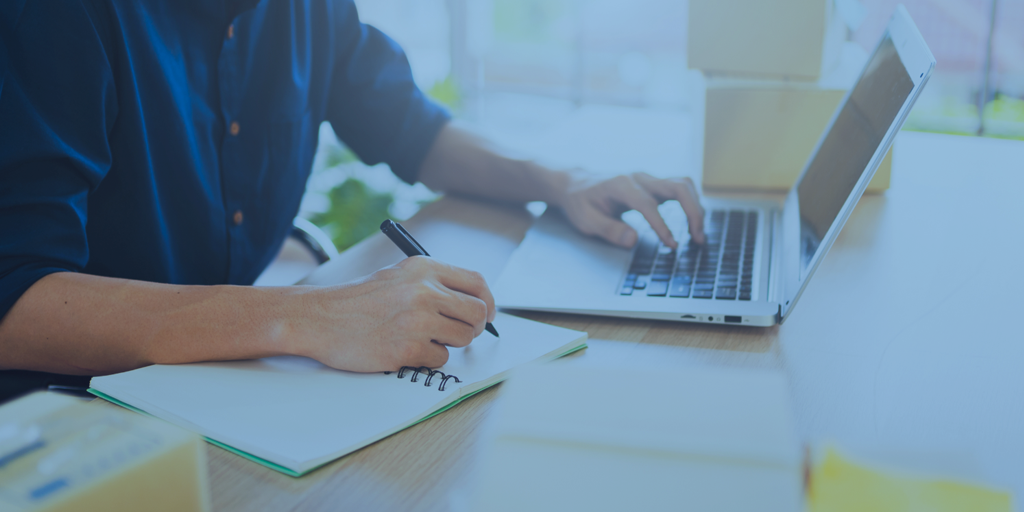
Quality Shipping Software and Carrier Insights for Manufacturers
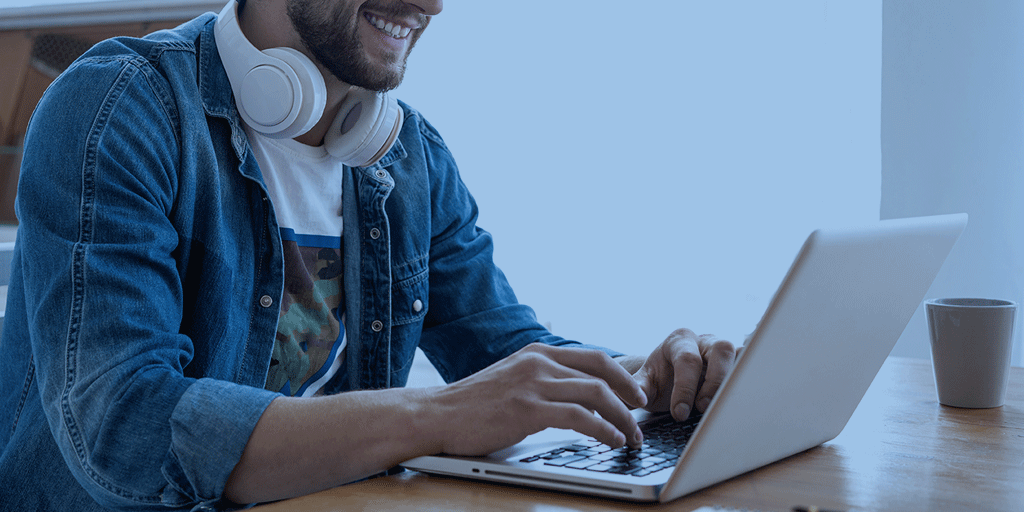
Plastics Distributor Case Study
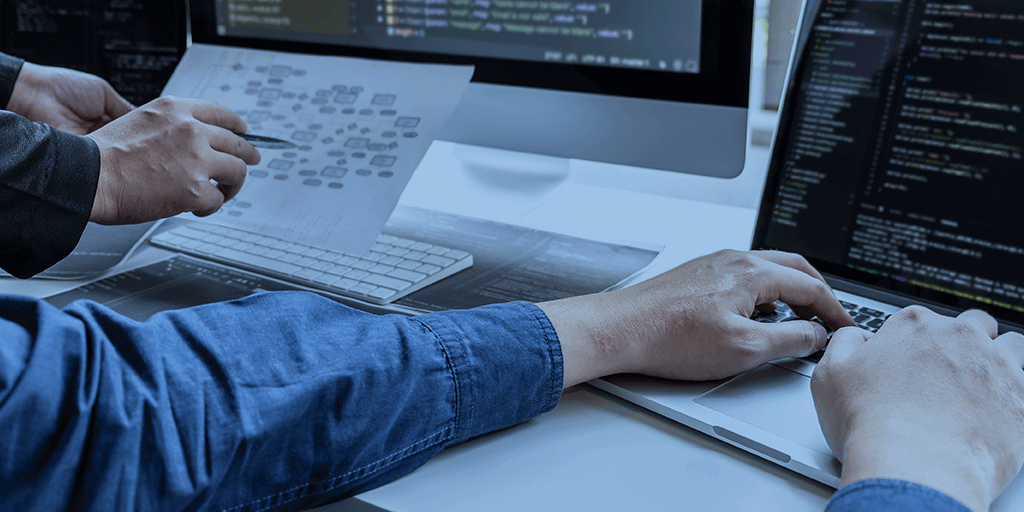
Elgen Manufacturing Sees Impressive Results
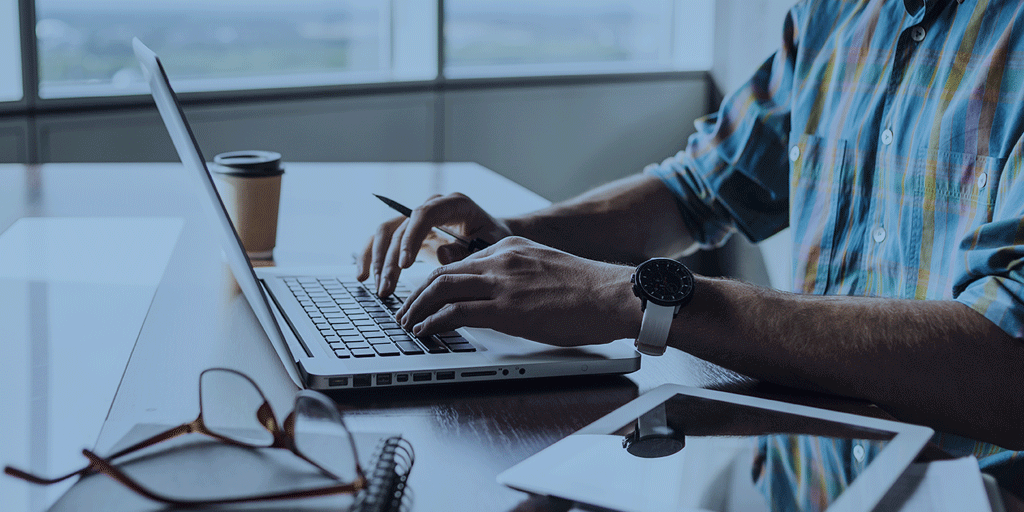
Newegg reduced the time spent on shipping
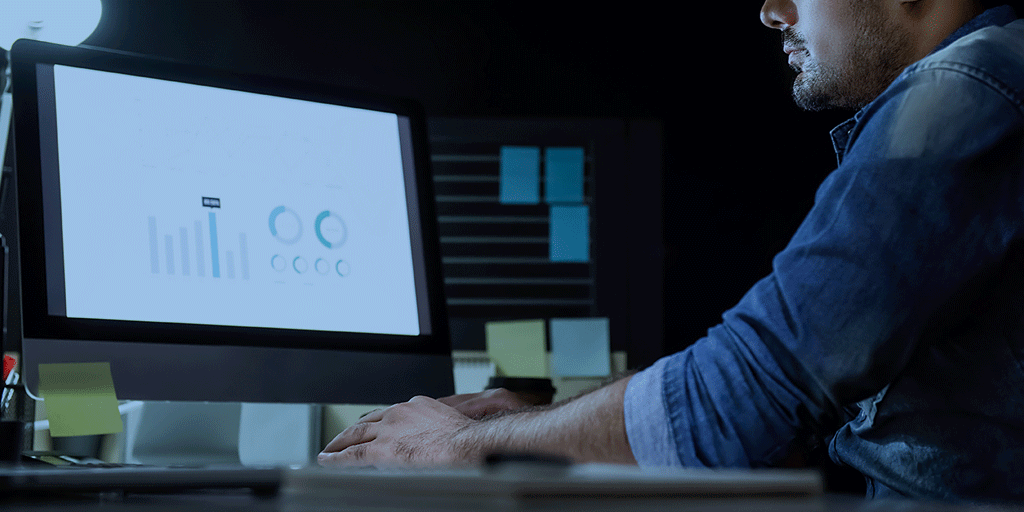
Customer Spotlights
5 freightpop tms features to discover in 2024.
The logistics and transportation management landscape is rapidly transforming, driven by innovation and the evolving...
3 Ways Logistics Managers Are Losing Money
Navigating the complexities of logistics management requires a keen eye for detail and an unwavering commitment to...
Freight Cost Calculation: How to Calculate Your Shipping Costs
Navigating the complexities of freight costs can be a daunting task for businesses aiming to streamline their logistics...
Navigating the Logistics Journey: How an Adhesive Manufacturing Leader Excelled with FreightPOP
With a 45-year legacy of producing top-quality adhesive products, our customer—a manufacturing giant in adhesive...
From Sticky Situations to Smooth Shipping: An Adhesive Leader's Transformation
For 45 years, our latest customer – a titan in adhesive solutions – has been crafting the perfect product for every...
Crafting Memories With Improved Logistics
Our latest partner is a family-owned enterprise renowned for creating exquisite glass ornaments for over 70 years....
💪Powering Growth: NetSuite Integration For HAZMAT And International Shipping
Want to find out how FreightPOP's NetSuite integration can revolutionize heavy shippers' efficiency, accuracy, and...
Retailer Upgrades Shipping With SAP S/4HANA Integration
Does your TMS fail to connect with SAP S/4HANA? This was something a new client of ours encountered when trying to...
Global Printer Fast Tracks Shipping With Powerful ERP Integration
When a pioneering print and press production supplier sought a powerful TMS solution that could easily integrate into...
How a Designer Furniture Brand is Offering Better Shipping to Customers
Today's customer spotlight is on a high-end furniture brand designing for online catalogs and IKEA home & storage...
Janitorial Distributor Cleans Up On Procurement, Orders, And HAZMAT
Learn how a major supplier and distributor with a heavy ecommerce arm relying on Magento and InsiteCommerce revamped...
Syspro ERP And Custom BOL App Integrations Give Manufacturer Peace of Mind
Industry-leading lamination manufacturer struggling to find solid logistics software to integrate into Syspro and...
When This 3PL Struggled To Scale - FreightPOP Delivered
FreightPOP empowers customers to quote, ship, and track at scale. Read how a 3PL struggling to keep up with his...
How To Improve Fragmented Shipping And Clunky Quoting Processes
"Streamlined shipping" is bandied about by TMS companies quite a bit, but what can a solid shipping platform really do...
Grocery Distributor Makes The Most Of Resources - Ships With FreightPOP
Like many businesses, you have to be clever about using your resources. See how this grocery wholesaler with limited...
How a Major Telco Streamlined International Shipping with FreightPOP
Read how a major telecom customer streamlines their international shipping through FreightPOP's currency conversion...
[Case Study] WMS Provider Uses FreightPOP APIs For Freight Shipping
Our WMS provider customer had big problems. They had an outdated TMS, couldn't provide freight shipping to their...
3PL Fulfillment Company Breaks Into LTL Market
When a 3PL fulfillment company breaking into the LTL market approached us, they had specific requirements. They needed...
Custom Wheel Company Kicks it up a Notch - Tracks Shipments Smarter
When a custom-design wheel retailer said they needed reliable tracking and streamlined shipping to free up labor and...
Case Study: Streamlined HAZMAT Shipping, NetSuite Integration
Customer Spotlight: How shipping software helped move one of America's largest non-profit agricultural advocacy...
Supporting Our Shippers With Reliable IT and Custom Configurations
CUSTOMER SPOTLIGHT: Brief overview of how we helped a manufacturer maintain their competitive advantage through ongoing...
How a fulfillment company improved their HAZMAT and International shipping
CUSTOMER SPOTLIGHT: Read how a major private label manufacturer with over 50 production lines found the perfect TMS...
Digitizing Logistics In The Face Of Major Growth During COVID
CUSTOMER SPOTLIGHT: Learn how a national supplier with 15 locations used FreightPOP's integrations and software to...
Clinical Lab Accesses Better Shipping Rates Through FreightPOP
CUSTOMER SPOTLIGHT: At FreightPOP, we solve issues that hinder shipping processes. In today's spotlight, we highlight...
"FreightPop has become part of our operating system so to speak, it brings all your carriers into one platform for quoting, tracking, and shipping with ease."
Transport Manager
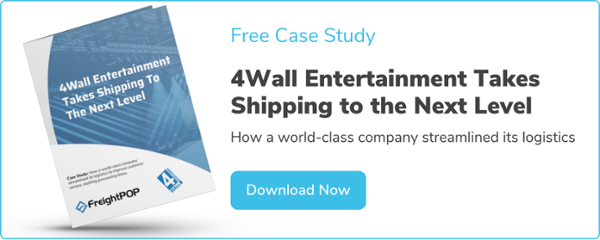

Toolkit on Intelligent Transport Systems for Urban Transport
- Technical requirements
- How to use the Toolkit
- Layout of the Toolkit
- Credits and acknowledgements
- Implementation
- Strategic Context Level
- Tactical Planning Level
- Service Delivery Level
- General Support Level
- Statistical Analysis Level
- Operations Management
- Driver Aids
- Fare Collection
- Traveller Information
- Traffic Management
- Demand Responsive Transport
- ITS-facilitated Functions
- Automatic Vehicle Monitoring
- Driver Monitoring
- Vehicle Systems Monitoring
- In-Vehicle Data Hub and Processor
- Electronic Fare Collection
- Travel Information Displays
- Surveillance Equipment
- Vehicle Identification
- Communications
- Dublin, Ireland
- Florence, Italy
- Izmir, Turkey
- Prince William County, USA
- Zurich, Switzerland
- Johannesburg, South Africa
- Mysore, India
- Accra, Ghana
- Cebu, Philippines
- Library glossary
- Library documents
Case Studies
A set of Case Studies has been prepared to illustrate how ITS is used in practice. The sites have been selected to provide diversity in environment, operator type, scale, ITS implemented, and degree of experience with ITS.
The Case Studies are presented in three clusters:
Sites where ITS is well established
Sites where ITS is currently in first deployment
Sites which are considering the use of ITS and/or carrying out some initial testing
This section provides an overview of the ten Case Studies. It presents the main points of context, ITS implemented, and lessons learned (for the sites where the ITS has been deployed).
Each Case Study is presented in detail on the Toolkit website. The information includes:
Contextual information: Regulatory environment, operator information, basis of service organization and procurement, basis of financial support
ITS: Overall ITS approach, individual ITS systems implemented, technical details, means of operations management
Implementation experience: Preparation, procurement, installation and implementation, post-implementation experience, lessons learned, benefits achieved.
It is strongly recommended that decision-takers and practitioners familiarize themselves with these Case Studies and with other sites that have implemented ITS. There is a vast array of experience which can be drawn on – not all of it pleasant, but all of it valuable. It is clear that the implementers are willing to share what they have learned with their counterparts in other cities and regions.
VBZ, Zurich, Switzerland
Public transport in Zurich is provided by VBZ, a multi-modal operator of trams, trolleybuses and buses. Trams form the backbone of the system.
Since the mid-1970’s, the City of Zurich has committed to a strongly pro-public transport policy, giving it high priority in streets and at junctions

The basic concept is that the City provides an excellent operating environment, and VBZ should operate on-time services within that frame
ITS is central to Operations Management and high-quality, on-time services. VBZ first implemented ITS in the early-1970’s.
The ITS is integral to the VBZ operation, and to the organization, business processes, operating procedures, data, and management. The approach has matured over the four decades as they gain better understanding of what they can do, embed it in the organization, and evolve the technology.

VBZ has evolved from using ITS to just know where their vehicles are, to precision operation with on-time running and transfer assurance
Passenger information is extremely well-developed, prior to the trip, at stops and in the vehicles. It provides a seamless and ubiquitous guidance.
Read the full case study
ATAF, Florence, Italy
ATAF is the Municipality-owned bus operator of the City of Florence, serving the Metropolitan Area and some hinterlands towns.
Since 2005, services are provided under Service Contract to the Province of Florence, for which ATAF joined with Li-nea and some smaller operators in a special purpose entity.
The Contract has quantitative and qualitative performance requirements, in particular in relation to volume of service and punctuality. It also places quite extensive service and event reporting requirements.

ATAF first introduced AVLC in 1984 to about 100 of its buses. The AVLC was updated in 1996 and extended to the full fleet of about 400 buses. This included GPS, trunked mobile radio, and enhanced AVLC functions.

A new procurement was launched in 2006 for a total AVLC replacement, at-stop RTPI units, and internet/mobile travel information applications. It also procured a limited amount of video-surveillance and traffic signal priority facilities, which may be extended later.
Phased deployment has commenced in 2009 with the new AVLC Control Centre already fully operational. It contains a major functionality upgrade.
Dublin Bus, Dublin, Ireland
Dublin Bus is the publicly owned operator of the bus network in Dublin. It operates 980 double-deck buses in the city and hinterland of Dublin.

Dublin Bus has a 5-year Public Service Obligation contract with the National Transport Authority. Performance measures are now linked to PSO payments, and will place increasing pressure on operational quality.
The company has implemented extensive ITS over the course of two decades. Electronic Ticket Machines were first implemented in 1989 and have provided the backbone of the on-bus intelligent network.

Vehicle location and voice/data communication capability have been added to provide the platform for a new AVLC system. This is based on a centralized Control Centre that manages services on a real-time basis.
The AVLC supports real-time passenger information on internet and at bus-stops. The RTPI server and at-stop displays are managed by the city.

The ITS has been based on the business and operational requirements.
The AVLC is in its first full year of operation, and has not yielded quantified resource or operational benefits
ESHOT, Izmir, Turkey
ESHOT is the municipal-owned operator of the bus network in Izmir and its surrounding service area. It operates a fleet of 1,560 buses, including 410 from its associate Izulas.
The bus network forms part of an integrated transport system including Metro, Rail, Ferry, and local paratransit. Integration has been developed since 2000, and suburban rail was included in 2010.

The Izmir Metropolitan Transport Co-ordination Centre was established in 2006 for the planning, co-ordination and determination of routes; ESHOT is represented on this body through its General Manager.
The company has implemented extensive ITS since 1999, when smart-card ticketing was first introduced. The ticket validators have provided the backbone of the on-bus intelligent network.
Vehicle location and voice/data communication capability have been added to provide the platform for a new AVM system. This is based on a centralized Control Centre that manages services on a real-time basis.

The AVL supports real-time passenger information on buses and at bus-stops. The communications capability is also utilized for surveillance.
AVL data is also utilized for fuel issue monitoring and bus maintenance scheduling.
Prince William County
PRTC at Prince William County, USA
PRTC is the transit commission for an area of eastern Virginia adjacent to Washington DC.
PRTC uses a fleet of 139 buses to provide commuter bus services to Washington (OmniRide) and local flexible bus services in Prince William County and the Manassas area (OmniLink). Service operation is contracted out.
OmniLink services are demand-responsive transport (DRT) operated as route deviation (flex-route) for general use including riders with disabilities. Trips are pre-booked from 2 hours to 7 days before travel and about 30 percent of demand responsive trips are standing orders.

First implementation of ITS at PRTC was to support the DRT. It included booking, routing and dispatch software, and in-vehicle data terminals.
The ITS evolved with the addition of GPS, improved communications, and new back-office software capacity. Rudimentary GPS tracking was extended to the OmniRide commuter services.
A new procurement has been launched in 2011 for significant enhancement of the ITS systems, including CAD/AVL system- and service-wide and installation of new MDTs in all vehicles.
Benefits attributed to ITS include the ability to offer DRT with short pre-booking time, better on-time performance, increased efficiency, increased ridership, improved working environment and enhanced data collection.
MCTD of KSRTC, Mysore, India
KSRTC is the State Transport Commission for the State of Karnataka, India. It operates about 7,000 buses on intra- and interstate bus services.
MCTD is a division of KSRTC, providing urban bus services in the city of Mysore, using a fleet of about 400 buses out of 3 depots and 6 bus stations
KSRTC are currently implementing an ITS system at MCTD covering all of the fleet and the services. The order has been placed and the system is scheduled to be fully operational by end-December 2011.
The ITS system consists of AVLC based on GPS, GSM/GPRS and real-time passenger information at bus stations, bus stops, and in-vehicle;

A Central Control Station (CCS) is being established at the main bus station, which will manage services along the routes and at outer terminals. Platform dispatchers will be retained at the bus stations.
KSRTC are procuring a Project Management Consultant to support the implementation process
An extensive Monitoring and Evaluation program is being procured to examine the implementation phase, the system and service performance, and the longer-term impacts. This will assist KSRTC in taking decisions about deployment of ITS elsewhere in their fleet.
Johannesburg
Rea Vaya, Johannesburg, South Africa
Rea Vaya is the BRT network in Johannesburg. Phase 1A is operational, linking the township of Soweto to the CBD. Phase 1B is under construction and expected to be operational during 2012. Rea Vaya is developed by City of Johannesburg.
The Rea Vaya network consists of Trunk Routes that operate exclusively on the BRT running way, Complementary routes that operate both on and off the BRT running way, and Feeder Routes that bring passengers to the BRT for transfer.

A new Bus Operating company (PioTrans) has been formed, whose shareholders are from the minibus taxi owners displaced by the Rea Vaya services. City of Johannesburg has entered a 12-year bus service operating contract with PioTrans, who are paid a per-kilometre fee for the provided services.
A comprehensive, integrated ITS program supports Rea Vaya BRT. This consists of GPS-based AVM, operations control centre, traveller information, CCTV for security and station management, scheduling package, traffic signal priority, and fare collection.
By end-2011, the AVM, Operations Control Centre, CCTV and scheduling systems are fully operational. The traveller information system and traffic signal priority systems are expected to come on-stream during 2012-3.
An Automatic Fare Collection (AFC) system has been procured and is currently under deployment (operational by end-February 2012). The AFC is based on EMV smart cards. Value-loading will take place at stations, vendors and banks.

The vehicle to control centre communications takes place over the local GSM network, while the stations and their devices use fibre optic cable.
ITS Support to the Private Bus Operator Sector in Sri Lanka
The private bus sector in Sri Lanka consists of 19,000 vehicles, which are independently owned, mostly by single-vehicle Owners. There is a very low level of collective organizational or operational capacity.
The National Transport Commission (NTC) regulates tariffs and service standards island-wide and regulates permits for inter-provincial bus routes. Raising standards and monitoring compliance are key functions.
NTC has already successfully launched the implementation of Electronic Ticket Machines, currently deployed on over half the Sri Lankan bus fleet.
NTC achieved this through a combination of mandating their use, preparing specifications, giving type approval to suitable suppliers, and allowing Operators to directly purchase approved models of their choice.
NTC has launched an ITS pilot project on inter-provincial bus services, involving about 70 buses. The core application is automatic provision of location data to the NTC Control Centre using GPS and GPRS units.
A similar approach to ETMs has been used whereby NTC prepared the technical specifications and invited suppliers to test compliant devices
7 suppliers have installed compliant systems. Many have exceeded the baseline requirement and installed additional functionality including fuel monitoring, driver alarms, speeding alerts, in-vehicle image capture
Subject to successful pilot phase, NTC intends to make ITS installation mandatory as part of the Permit conditions, and to make permanent their Control Centre for monitoring route and service quality compliance.
ITS Support to the Private Bus Operator Sector in Accra, Ghana
Urban passenger transport in Ghanaian cities is provided primarily by minibuses (tro-tros) which are individually owned, but are highly organized at route level through Unions. This has provides a stable system which is well understood by the customers. Nonetheless, there are limitations in vehicle and service quality that need to be addressed.
Large vehicle service provision is currently limited to the parastatal Metro Mass Transit and some bus companies with low market share.
Major sector reform is underway, primarily through the Ghana Urban Transport Project (GUTP). This includes regulatory and institutional development, a BRT corridor from the west of Greater Accra to the CBD, and improved bus routes with some bus priority on other corridors.
The local authorities (Assemblies) have taken on the regulatory role and are implementing a new Permit system; hitherto, the sector had been self-regulating. This places new management, monitoring, enforcement, administration and planning requirements on the Assemblies.

The tro-tro sector will need to develop Permit compliance capacity, both on the ground and in administrative/reporting terms. It also needs to improve the quality of its vehicles and its services
Both the BRT and the Permit Type B Routes will require the formation of new operating entities, new operating methods, and new operational capacity. In addition, a BRT Management Entity will be formed.
These are all likely to require ITS for Operations Management, Fare Collection, Passenger Information, and post-event analysis. The pressing timescale may require decisions on ITS in advance of these entities being established and in a position to define their functional requirements.
The current baseline for ITS is low, with no ITS and very little computerized systems currently deployed in UPT. There is not currently an active ITS supplier base in Ghana.
ITS Support to Governmental Organisations in Cebu, Philippines
Passenger transport in the Philippines is regulated through franchises issued by central government Department of Transport and Communications (DOTC) and its agencies.
The primary urban passenger transport mode is the Public Utility Jeepney (PUJ). This is typically an 18-seater converted US Jeep. Outside of Metro Manila this is the sole urban passenger transport mode.
The PUJ industry is fragmented consisting of a high percentage of single owner operators. Membership associations exist but are not wholly subscribed to and offer little more than administrative functions.
DOTC seeks to achieve increasing efficiency in the provision of passenger transport. Their first focus is on regional services (more often run by larger companies). Thereafter, increasing levels of control and organization would be applied to urban transport first in Metro Manila.
During 2011, regional services centred upon Manila are being fitted with GPS to enable operators to locate vehicles operating over long distances.
DOTC propose to assist Manila-based urban PUJ owners to fit GPS devices so that PUJs can be monitored. Current plans include cash incentives to owners. It is planned that information will be collected centrally by DOTC and information made available to owner/operators.
In the medium term, this information will be used to restructure the PUJ network as route franchises come up for renewal. In the longer term, this information might be linked to an area wide traffic control system.
Urban transport fares are cash based. There is no electronic information and basic static information. There is currently no fleet control.
The development of a BRT in Cebu has provided an information base from which to work and an ability to explore means by which the passenger transport network can be reorganised to achieve efficiency gains.
The Cebu BRT Pre-Feasibility Study (2010) identified the need for ITS solutions for operational management, payment and co-ordination with the City’s urban traffic control system (SCATS). It is estimated that the BRT will be operational by 2014.
The World Bank is progressing with a study (expected late-2011) that demonstrates the use of low cost mobile vehicle tracking systems in Cebu. This study will provide transport planners with a low-cost means to collect real time travel information and road condition data. This data can be used to manage road assets, mitigate traffic congestion and manage mass transport fleets.
Academia.edu no longer supports Internet Explorer.
To browse Academia.edu and the wider internet faster and more securely, please take a few seconds to upgrade your browser .
Enter the email address you signed up with and we'll email you a reset link.
- We're Hiring!
- Help Center
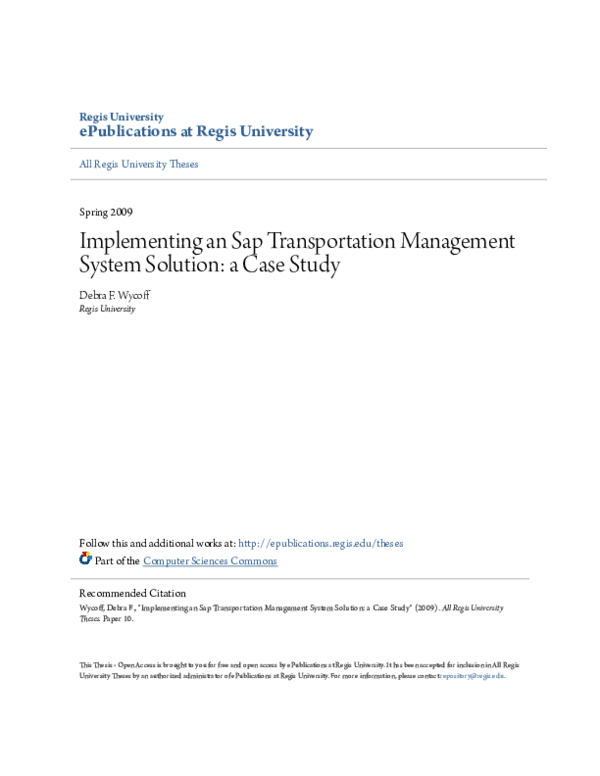
Implementing an Sap Transportation Management System Solution: a Case Study

Related Papers
Proceedings of the …
Olga Ormandjieva , Alain Abran
Abstract: This paper makes a first attempt towards improving the testing process in ERP projects by using a metric-based approach [ABU06] based on functional size measurement. The paper reports on how this approach was adapted to a ERP-package-specific project context, how it was applied to five settings in a mid-sized project, and what was learnt of doing it.
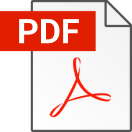
Loading Preview
Sorry, preview is currently unavailable. You can download the paper by clicking the button above.
- We're Hiring!
- Help Center
- Find new research papers in:
- Health Sciences
- Earth Sciences
- Cognitive Science
- Mathematics
- Computer Science
- Academia ©2024
- City by city
- Party Conferences 2024
- Current issues
- General election 2024
- Metro mayors
- Levelling up
- Productivity

Transport Case Studies
How different cities are improving their transport connections using our case study library
Case study library
Why improve transport?
Effective transport is vital for the economy. Good transport connections have direct benefits to people, businesses, the environment, and the economy overall. They can support innovation, help people access jobs, shape greener and healthier places, and attract new firms.
Having more control over transport can help cities make the most of their infrastructure by reducing uncertainty and short timescale of funding, improving the bus system, and ensuring integration of transport, economic development and infrastructure.
Use the table below to find out more about how and what cities in the UK and abroad have done to improve transport. These case studies highlight what the cities did and their self-reported outcomes.
To find out more about what types of transport what types of policy interventions have an impact on local economic growth from across OECD countries, as well as evidence-based policy design guides, take a look at the What Works Centre pages on Transport.
Case studies
click the case study title to find out more
Improve bus quality and services | Nottingham | UK | Nottingham City Council | |
Improve bus quality and services | Helsinki | Finland | Helsinki Region Transport | |
Improve bus quality and services | London | UK | Transport of London | |
Encourage investment in transport | Paris | France | French Government | |
Align costs and benefits of transport | Cities across the UK | UK | City Councils | |
Delivering efficient services using data | London | UK | Transport of London | |
Delivering efficient services using data | Dublin | Ireland | Dublin City Council, IBM | |
Delivering efficient services using data | Boston | US | The Mayor’s Office of New Urban Mechanics | |
Provide good links between the city centre and the wider area | Manchester | UK | CityCo Manchester | |
Provide good links between the city centre and the wider area | Montpellier | France | Montpellier Agglomeration | |
Provide good links between the city centre and the wider area | Eugene | Oregon, US | Lane Transit District, Eugene Council | |
Promote inclusive growth in transport | Nottingham | UK | Nottingham City Council | |
Promote inclusive growth in transport | London | UK | Transport for London | |
strong> | Cleaning up the air we breathe | Paris | France | National Government |
Cleaning up the air we breathe | New York City | New York, USA | New York City authority | |
Cleaning up the air we breathe | Freiburg | Germany | Freiburg City Council | |
Cleaning up the air we breathe | Copenhagen | Denmark | Copenhagen City Council | |
strong> | Cleaning up the air we breathe | Los Angeles | California, USA | Los Angeles department for transportation |
Cleaning up the air we breathe | Milan | Italy | Milan City Council | |
Cleaning up the air we breathe | Barcelona | Spain | Barcelona City Council |
More Case Studies on Housing and Transport
Delivering change: making transport work for cities.
Zach Wilcox and Nada Nohrová

Delivering change: Putting city centres at the heart of the local economy
Louise McGough and Elli Thomas

Open Data or Closed Doors?
Maire Williams

Funding and financing inclusive growth in cities
Naomi Clayton, Simon Jeffrey and Anthony Breach

How can UK cities clean up the air we breathe?
Adeline Bailly

Policy Officer
Anthony Breach
The first 100 days
Paul Swinney
Combined authorities
Thank you for visiting nature.com. You are using a browser version with limited support for CSS. To obtain the best experience, we recommend you use a more up to date browser (or turn off compatibility mode in Internet Explorer). In the meantime, to ensure continued support, we are displaying the site without styles and JavaScript.
- View all journals
- Explore content
- About the journal
- Publish with us
- Sign up for alerts
- Open access
- Published: 06 September 2024
Construction simulation and scheme optimisation of complex underground cavities
- Yu-han Ran 1 ,
- Hai-bo Li 1 , 2 ,
- Shun-tong Xu 1 ,
- Zhi-chao Yu 3 &
- Xing-guo Yang 1 , 2
Scientific Reports volume 14 , Article number: 20879 ( 2024 ) Cite this article
Metrics details
- Civil engineering
- Energy infrastructure
Underground cavities have complex spatial structures and geological settings, their arrangement is dense and crisscrossed. The construction system involves multiple work surfaces, levels, and processes. The close integration of construction simulation with actual production conditions is crucial for enhancing the guidance that simulation results provide for practical engineering. Therefore, from the perspective of optimizing construction organization and management, this article comprehensively considers various factors in the construction process, innovatively introduces the principle of production line balance and the concept of rule cycle, and combines technology and management, an underground cavities construction simulation system (UCCSS) is developed. In UCCSS, a hierarchical model is built and calculation are performed on models with different construction methods by modifying the parameters as per the actual engineering characteristics. The simulation results are comprehensively analysed to determine the optimal construction programme. An application case is proposed based on the construction organisation design of the long and parallel diversion tunnels at the CB Hydropower Station. The results show that the system has good practicality and credibility and can provide guidance for the construction organisation design of underground cavities with various features.
Similar content being viewed by others
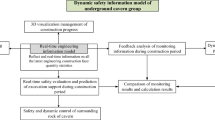
Dynamic safety information modeling of underground cavern groups in the entire construction process
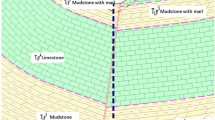
Evaluating construction parameters of HB and CD methods for super large section tunnel: a case study
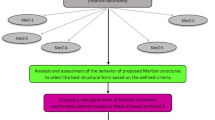
Sustainable colonization of Mars using shape optimized structures and in situ concrete
Introduction.
The construction of underground cavities in hydraulic and hydropower projects is extremely complex because the arrangement of underground cavities in such projects is dense and crisscrossed (Fig. 1 ). Accordingly, the construction system involves multiple work surfaces, levels, and processes. Further, the construction procedure is affected by many factors, such as the geological settings of the project, construction technology level, corresponding mechanical equipment configuration, traffic conditions, spatial structure of the cavities, support forms, and construction quality, these factors are often random and changeable. Therefore, accurately estimating and evaluating the construction organisation design by using only traditional methods is difficult. However, the construction of underground cavities is both repetitive and linear 1 . Therefore, on a theoretical level, conducting simulations is expected to be an effective tool for planning projects 2 .
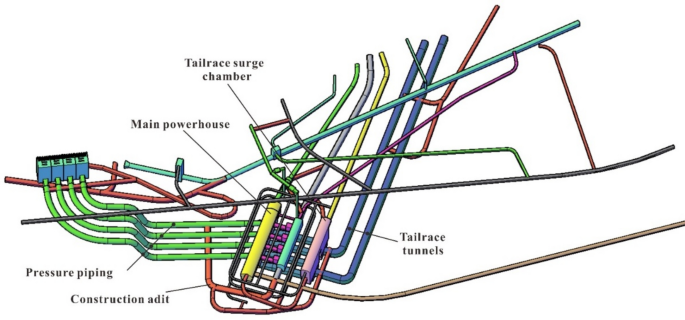
Three-dimensional representation of the underground cavities.
Owing to recent developments in computer technology, many international researchers have conducted numerous studies on construction simulation technology. The cycle operation network was first proposed by Halpin 3 , who combined queuing theory with grid technology to simulate the construction process with cyclic characteristics. Accordingly, many influential software programmes were developed, such as INSIGHT 4 , RESQUE 5 , UM-CYCLONE 6 , Micro-CYCLONE 7 , COOPS 8 DISCO 9 , STROBOSCOPE 10 , Simphony 11 , Vitascope 12 , S3 13 , COSYE 14 , and hybrid SD-DES 15 . However, these programmes are mostly used for high-rise buildings, road construction, and pipeline engineering, whose engineering characteristics are significantly different from those of hydropower station underground cavities. Therefore, a more suitable construction simulation software or systems must be developed by considering the construction characteristics of hydropower station underground cavities.
Zhong et al. 16 first used simulation technology to analyze the construction process of underground cavities, and used the cycle operation network simulation model to describe the construction process, which laid a theoretical foundation for tunnel construction simulation. Some scholars have proposed a simulation method for underground cavity construction that is more in line with engineering practive by considering different construction effects and detailed simulation of construction procedures. Liu et al. 17 considered the uncertain geologic conditions and risks and presented an adaptive cyclic operation network simulation (CYCLONE) simulation technique to predict the schedule of TBM. A.Shahim et al. 18 considered the uncertainty of tunnel construction caused by cold weather. The unit activities sensitive to climate in tunnel construction were identified and quantified, and then the simulation model tunnel construction in cold weather was established. Zhong et al. 19 proposed a robustness analysis method that involves underground powerhouse construction simulation based on the Markov Chain Monte Carlo (MCMC) method. The robustness of underground powerhouse construction was quantified, and the time buffer was introduced. The application of this methodology not only considered duration but also robustness, which effectively reduced the interference of construction uncertainty. Yu et al. 2 defined optimal probability distribution for construction activities with BestFit technology, so as to realize fine and effective analysis of ordinary risk factors at the operation level of tunnel construction. And Bayesian network is embedded into simulation program to quantitatively analyze the occurrence probalitity of potential risk events. Finally, a tunnel construction simulation model considering the impact of risks was established. Sharafat et al. 20 presented a novel risk analysis methodology based on a generic bow-tie method for systematic assessment and management of risks associated with tunnel boring machine in difficult ground conditions.
On the basis of improving the accuracy of underground cavities simulation, some studied have combined visualization technology to realize the intuitive expression and visual analysis of simulation results. Zhong et al. 21 developed a two-dimensional progress display system, combining a visualisation technology with a construction simulation technology for the first time, and then developed a three-dimensional visualisation underground cavities construction simulation system based on OpenGL, which displayed the results more vividly. Wang et al. 22 carried out parametric modelling of diversion tunnel through CATIA, which provided a visual simulation of the rapid establishment and modification of the tunnel model. Sharafat et al. 23 proposed a BIM-based multi-model tunnel information modeling (TIM) framework to visualize, manage, and simulate the drill-and-blast tunnel construction process. Moreover, new technologies such as 3D visualization modeling and artificial intelligence (AI) technology have been introduced into construction simulation. These new technologies can not only achieve visualization but also optimize construction project scheduling by considering various factors, analyze historical project data and real-time information to identify potential risks on construction and provide real-time progress tracking by analyzing data from various sources 24 , 25 .
At present, the reaserch theory and implementation of construction simulation for underground cavities have been very perfect, and visualization expression has also been achieved. Most of the above studies are devoted to obtaining more accurate simulation results by considering the influence of construction unfavorable factors on simulation and studying the optimization of simulation parameters. It fails in the perspective of innovating the concept of underground cavern construction organization and management to realize the organic combination of technology and management. It needs to be closely combined with the actual production situation, so as to improve the guiding significance of the simulation results to the actual project. Therefore, this study innovatively introduces the principle of production line balance and the concept of rule cycle, and develops a simulation system that is more suitable for the actual construction organization mode. In the system, a hierarchical model is established to meet the characteristics of complex spatial structure and crisscross of underground cavities. The system includes a variety of excavation and lining method models. Through the modification of construction equipment parameters, construction traffic parameters and engineering parameters, the simulation of different projects is completed. Finally, based on the analysis of the calculation data of construction progress, equipment resources, construction strength and traffic flow, the optimal construction scheme is established. The system was successfully applied in the construction programme design of the CB diversion tunnels.
In order to make the construction simulation of underground cavities more closely combined with the engineering practice, the simulation model can accurately and objectively reflect the actul. The principle of production line balance and rule cycle concept is proposed.
An average distribution of operations is called production line balance. The construction of underground cavities is regarded as a complex production line, and the cavities are divided into multiple unit operations through construction task allocation, such as a diversion tunnel being divided into several sections and an underground powerhouse being divided into several floors. These unit tasks can be appropriately combined into task groups, and each task group is assigned different equipment and construction procedures due to the use of different construction methods. Furthermore, when assigning tasks, efforts should be made to evenly distribute the workload among various equipment or processes. If the allocation of work is uneven, it will result in idle time for equipment or operations.
The rule cycle concept is to consider the objective fact that the natural conditions such as engineering geology and hydrogeology with a certain range of the underground cavities changed little, and the excavation or lining section is also unchanged. The same construction cycle is used to constructed, which not only conforms to the actual construction, but also improves the efficiency of simulation.
Solving process
Simulation systems are generally classified as continuous or discrete systems. The state of a continuous system changes with time, whereas that of a discrete system changes with jumps in finite time. A discrete system is more suitable for simulating underground cavities compared to a contiuous system 26 . The basic concept of discrete system is to use simulation clocks to reflect the running trajectory of simulation time, so the underground cavities construction simulation system (UCCSS) is equipped with both a global and local simulation clock, and its dynamic simulation process is shown in Fig. 2 .
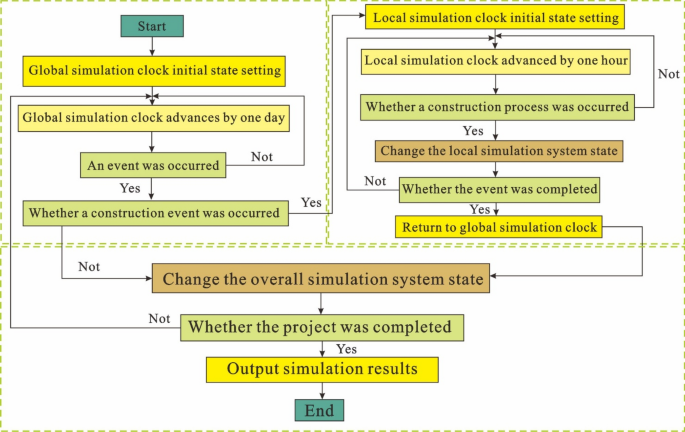
Dynamic simulation flow chart of UCCSS.
The global simulation clock is used to record the simulation trajectory of the overall simulation system, throughout which the time-step method is adopted. The time-step method is called the fixed-time incremental propulsion method, which uses \(\Delta \text{T}\) as an increment to check whether any construction events occurred. If so, the event is considered to occur at the termination of the time increment, and the system state is changed accordingly. Otherwise, the system state is not changed. When a construction event is detected, the global simulation clock retained its current state and the control power is transferred to the local simulation clock. The time-step method is also adopted throughout the local simulation clock, and the local simulation clock is used to record the simulation trajectory of the construction process. Starting time from 0 clock, the local simulation clock is advanced for \(\Delta \text{t}\) to detect whether a construction process occurred and the usage of various resources is tracked. These steps are repeated until the event is completed, then, the control power is returned to the global simulation clock, which advanced the global simulation clock until the project is completed. Subsequently, the simulation results are analysed to obtain the final results. And the construction schedule, construction intensity and resource sets etc. are output.
When the time step method is used to simulate the system, the selection of time step is a very important issue. The smaller the selected time step is, the more refined simulation results will be. However, it will increase the number of state checking and judgment in the simulation process, thereby increasing the simulation running time. On the contrary, when the time step is too large, although it can reduce the running time, it is easy to lose some information of the system behavior and lead to the distortion of the simulation state. The global simulation clock is mainly used to determine the occurrence of construction events. In actual engineering, the working time of workers is usually measured in days. Therefore, the global simulation clock selects days as the step, which not only meets the working rules of humans, but also meets the accuracy of simulation. And the use of local simulation clock is mainly oriented to all aspects of specific construction, such as cavities excavation, slag discharge, lining and other activities. Usually, similar activities are measured in hours. Therefore, taking hours as a step can not only meet the requirements of simulation accuracy, but also meet the requirements of simulation running time.
The simulation is ensured to be in line with the actual construction organisation mode regarding the entire process of underground cavities construction. There are four hierarchical structure models, namely, unit project, units project, division project, and sub-project. The hierarchical structure model construction process for the simulation system is illustrated in Fig. 3 . First, we set the system processing time and build a new project or open an existing project. Next, the unit hierarchical structure is built, and the construction parameters, equipment parameters, traffic parameters, etc. are set. After the appropriate settings were determined, a simulation calculation is performed, and then, the simulation results are viewed. If the simulation results are unsatisfactory, the corresponding parameters are reset.
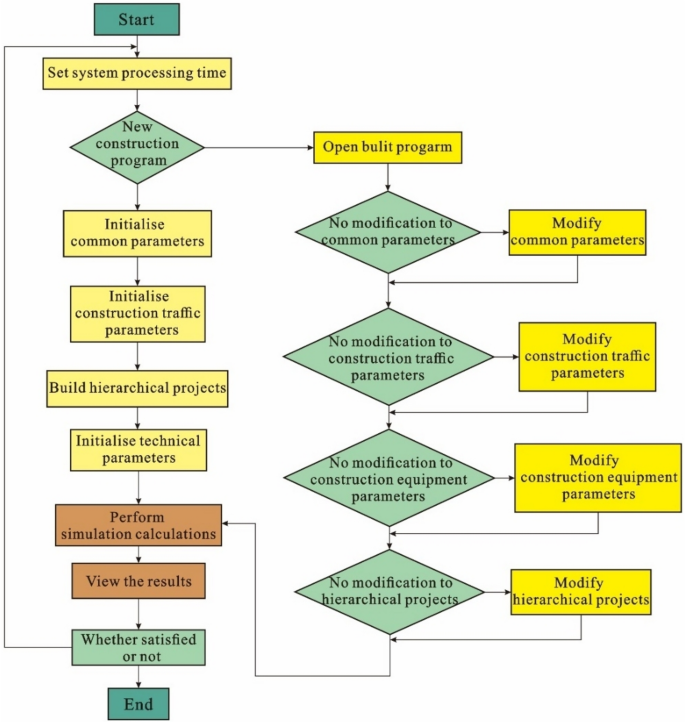
UCCSS flow chart.
Drilling-blasting excavation model
The drilling-blasting excavation model is adopted for full-section excavation, guide hole method excavation, and guide hole sidewall expansion excavation. The primary construction procedures include drilling, charging, blasting, ventilation, slag transportation, and support. The main parameters of the drill-blasting simulation model are cyclic footage, drilling time, slag transportation time, shotcrete time, daily cycle number, construction period, and cycle volume. These parameters are described as follows.
(1) Cyclic footage
Owing to the role of the rock support, the cyclic footage is generally less than the drilling depth. Because of the different blasting efficiencies, the cyclic footage is not the same as the same drilling depth.
Equation ( 1 ) defines the objective function of cyclic footage, where \({L}_{xh}(n)\) is the footage of the n th cycle, \(h\) is the drilling depth, and \({K}_{bs}(n)\) is the blasting efficiency of the nth cycle.
(2) Drilling time
There is no perfect formula for the theoretical calculation of drilling time, accordingly, it is determined mainly based on previous engineering experience.
Here, \({t}_{zk}\) is the drilling time, \(N\) is the number of designed blast holes, \({V}_{zj}\) is the speed of the drilling, \({n}_{1}\) , \({n}_{2}\) , and \(h\) are the number of drilling rigs configured for a single working face, number of drilling arms of the configured drilling rigs, and drilling depth,respectively, and \(\gamma\) is the average value of the working coefficients for multiple drilling rigs.
(3) Slag transportation time
Owing to the high concentration of dust in the cavity during slag transportation, no other operations are performed during slag removal. During the excavation of cavities, the slag output per cycle is calculated as follows:
Here, \(Z\) is the amount of slag transported in a single cycle, \(\alpha\) is the expansion coefficient of the excavation, \(\beta\) is the over- and under-excavation coefficient, \(S\) is the cavity design excavation area, and, \(d\) is the blasting cyclic footage.
The loading time of the loader is \({t}_{z}\) .
Here, \({V}_{z}\) is the productivity of the loader and \(a\) is the number of loaders.
The slag transportation time, \({t}_{y}\) , for a single dump truck is calculated using the following formula:
Here, \({L}_{1}\) and \({L}_{2}\) are the transport distances inside and outside the cavities, respectively, and \({V}_{1}\) and \({V}_{2}\) are the vehicle speeds inside and outside the cavities, respectively.
The slag transportation time, \({t}_{c}\) , for a single dump truck is calculated using the following formula:
(4) Anchoring and safe handling time.
As this process part can be constructed in parallel with other operations, the temporary support time, \({t}_{zh}\) , to ensure construction safety can be considered as the occupied linear time.
(5) Shotcrete time.
Because no other operations can be carried out during the shotcrete, it is considered an occupied linear time.
Here, \(H\) is the thickness of the shotcrete, \(L\) is the contour line after cavities excavation, \({d}_{s}\) is the upper blasting cyclic footage, \(N\) is the number of sets of shotcrete machines, \({V}_{ph}\) is the effective spraying quantity per hour of a single set of shotcrete machines, and \(\zeta\) is the average value of the working coefficient of the shotcrete machine, for \(N\) =1, \(\zeta\) =1; for \(N\) >1, \(\zeta\) <1.
(6) The single-cycle operating time, \({t}_{xh},\) is calculated using the following formula:
where \({t}_{a}\) is the time of safety inspection and treatment, \({t}_{tf}\) is the ventilation and smoke dispersion time, and \({t}_{fx}\) is the time required to measure the unreeling and hole siting.
(7) Daily cycles
When \({t}_{xh}\le {t}_{r}\) , the rule cycle criterion is used, and the single-day multiple cycles are denoted as n.
When \({t}_{xh}\) > \({t}_{r}\) , a multi-day cycle is used, and the multi-day cycles are denoted as n.
where \({t}_{r}\) is the effective daily working hours.
(8) Circulation engineering quantity.
When \({H}_{cqs}\) ≥ 0 ,
When \({H}_{cqs}\) < 0 ,
In Eqs. ( 11 ), ( 12 ) and ( 13 ) \({H}_{cqs}\) is the over- and under-excavation depth, \({V}_{cw}\) is the over-excavation quantity, \({V}_{qw}\) is the under-excavation quantity, and \(V\) is the unit project excavation quantity.
(9) Unit project construction time
In Eqs. ( 14 ) and ( 15 ), \({d}_{zx}\) is the construction period of the unit project, \({d}_{w}\left(n\right)\) is the last cycle completion time, \({d}_{s}(1)\) is the first cycle start time, \({d}_{y}\) is the entire duration of the unit project, \({d}_{q}\) is the unit project pre-processing time, and \({d}_{h}\) is the unit project post-processing time.
Layered excavation model
The layered excavation model is adopted for the second and lower layers of the layered excavation of a large section. Its construction workflow differs from that of the drilling-blasting excavation method, where, the operation of upper circulation slagging and lower circulation drilling, as well as that of anchoring and lower circulation drilling and slagging are parallel.
(1) Workflow of the layered excavation cycle.
The main processes of the construction procedures are drilling, charging, upper cycle slag transportation, upper cycle anchoring, safety evacuation, blasting, ventilation, safety inspection, slag transportation in this cycle, and lower cycle drilling and loading.
(2) Layered excavation cyclic footage.
The layered excavation method is adopted for the cavern with upper air faces, which is performed by vertical drilling with a down-hole drill, where the cyclic footage is the same as the drilling range.
(3) Layered excavation method cycle operation time.
It includes measuring the unreeling and hole-siting times, drilling time, safety inspection and processing time, slag transportation time, and smoke dispersion time. Its calculation method and shotcrete time are the same as those of the drilling-blasting excavation model. Because the upper circulation of the slag-out procedure is performed simultaneously with the lower circulation drilling, the cycle of operation time, \({t}_{xh}(n)\) , is calculated as follows.
When \(n=1\) ,
When 2 ≤ \(n\) ≤ \(N\) ,
If \({t}_{a}\left(n\right)+{t}_{zk}\left(n\right)\) < \({t}_{c}\left(n-1\right)\) , the upper circulation of the slag-out cannot be completed in the next drilling cycle.
(4) Quantity of layered excavation cycles
Because of the pre-split in the layered excavation, it is not necessary to consider the amount of over- and under-excavations.
Here, \(d\) denotes the cyclic footage, \(H\) is the step height, and \(B\) is the excavation width.
Steel trolley lining model
The steel trolley lining method is widely used in cavern engineering considering the lining sequence and different lining parts, which are divided into full section, top arch, side top arch linings, and other forms. The characteristics of this method are as follows: The lining process adopts a sequential operation, and the lining length of each cycle is the same, except for the last cycle. Its cycle operation processes include wall cleaning, keyways, measurement and placement, steel reinforcement installation, formwork placement, inspection, concrete injection, concrete maintenance, and demolding.
(1) Number of cycles per project unit
Here, L is the length of the unit project lining and L t is the length of the template.
(2) Cycle operation time
The steel trolley cycle operation time mainly includes the unreeling time, steel reinforcement installation time, formwork placement time, inspection time, concrete warehousing time, concrete maintenance time, and demolding time.
The measuring unreeling time, \({t}_{fx}\) , is generally based on an empirical input.
Steel reinforcement installation time is expressed as follows:
Here, \(G\) is the amount of reinforcing steel installed, calculated from the reinforcement ratio, \(p\) is the efficiency of the single-group steel placement, and \({N}_{gj}\) is the number of steel placement groups.
The formwork placement and inspection time, \({t}_{mb}\) , is determined based on experience.
According to construction experience, the concrete warehousing time is generally greater than the concrete loading time. Therefore, the optimal number of vehicle configurations for concrete transportation primarily depends on the transport path length, pump truck speed, and concrete warehousing time. When the last concrete pump truck arrives to the warehouse, the round trip is completed by the first concrete pump truck. The optimal number of pump truck configurations, \({N}_{bc}\) , is determined as follows:
In Eqs. ( 21 ), ( 22 ), and ( 23 ), \({t}_{x}\) is the transport time for a pump truck to complete a round trip, \({t}_{rc}\) is the concrete warehousing time, \({t}_{z}\) is the pump truck concrete loading time, \(L\) is the length of the transport path travelled by the pump truck, \({v}_{b}\) is the transport speed of the pump truck, \(V\) is the amount of concrete loaded into the pump truck, and \(\eta\) is the efficiency of the pump truck in the bin.
Concrete warehousing is considered continuous, accordingly, the total concrete warehousing time, t zr , is expressed as follows:
In Eqs. ( 24 ) and ( 25 ) , \({V}_{z}\) is the amount of concrete required for concrete entry and \(n\) is the number of times the pump truck is loaded.
In the same unit project, the concrete maintenance and demolding time, \({t}_{yh}\) , is kept constant based on engineering experience.
The cycle operation time is.
(3) The cycle time, cycle quantity, and construction period calculation methods are similar to those of the drilling-blasting excavation model, thus, these are not further described.
Sliding block lining model
The sliding block lining model is suitable for lining the bottom board of the cavern and another continuous lining. The sliding distance per hour is often used to describe the lining speed, therefore, a discrete simulation is conducted with a cycle of one hour. In the actual construction process, the lining speed is limited by the concrete supply, and the effective daily working time is set according to the overall rule cycle concept.
Here, \({S}_{z}\) is the total lining length of the unit project and \(L\) is the length of one lining cycle.
(2) Daily lining footage and concrete supply strength assessment
In Eqs. ( 28 ) and ( 29 ), \({S}_{c}\) denotes the lined concrete sectional area, \({L}_{d}\) denotes the daily lining footage, \({t}_{r}\) denotes the daily effective working time, and \({V}_{c}\) denotes the daily lining squared volume.
Concrete pump trucks and belt conveyors are used for the transportation of the sliding block lining to the workbench. When a concrete pump truck is used, the transport time is limited by the concrete condensation time and supply strength. A belt conveyor is used to satisfy the concrete supply strength requirements.
Construction transportation model
Construction traffic characteristics.
The construction traffic at underground cavities has the following characteristics:
(1) Paths are specific. Compared with urban and highway transportation, underground cavities construction transportation has unique characteristics. For a specific construction section, regardless of the number of transportation paths available, only one optimal path is selected for the material transportation path layout, which is generally composed of an open-line road outside the cavern, construction adit, and cross passage. Its road characteristics, such as slope and length, are obvious, which is conducive to a reasonable designation of vehicle speed.
(2) The vehicle type and load capacity are explicit. In general, the construction transportation at underground cavities can be carried out using various ways, such as belt conveyors, track transportation, and trackless transportation. Trackless transportation slag dump tracks are categorised into different models, such as 10t, 15t, 20t, and 25t, concrete pump trucks are categorised into different models, such as 3 m 3 and 6 m 3 , and rail transportation is classified into different models of mine trucks or railroad pump trucks. Underground cavities involve the construction of multiple work surfaces. However, for a specific construction section, to facilitate construction organisation management and maintenance, the same type of vehicle transportation is usually chosen, such that the load capacity is explicit.
(3) The starting points and destinations of transport are explicit. During the excavation of underground cavities, slag materials can be transported to sand-processing factories, waste slag storage sites, slag transfer sites, dam fillings, and other destinations. The lining concrete is typically supplied by the nearest concrete production system. For a specific section, slag utilisation is usually planned, therefore, the slag destination and concrete supply station are explicit.
(4) The concrete warehousing time is stipulated during transportation to prevent the concrete from condensing before it is placed. Regardless of whether rail or trackless transportation is used, the concrete delivery time cannot exceed the condensation time provisions.
Construction traffic flow
(1) Optimal number of vehicles on a working surface.
The number of vehicles configured requires that when the last car in the convoy leaves, the cycle in the conveyor is completed exactly by the first car. When the car is out of slag and actual number of configured vehicles is greater than the optimal, cars need to wait in line to load slag. Conversely, when the actual number of configured vehicles is less than the optimal, the loading system need to wait for cars to load slag.
In Eqs. ( 30 ) and ( 31 ), \({N}_{zj}\) is the optimal number of vehicles in a single working surface, \({t}_{d}\) is the time required for a vehicle round trip, \({t}_{x}\) is the time required for vehicle slag unloading, \({t}_{z}\) is the time required to fill a vehicle, \({t}_{o}\) is the time required for a vehicle to make an adjustment, turn, etc., \({L}_{1}\) is the length of the slag transport route through the construction adit, \({L}_{2}\) is the length of the slag transport route through the cross passage, \({L}_{3}\) is the length of the slag transport route through the open road, \({v}_{d1}\) is the construction adit vehicle speed which is on-load, \({v}_{d2}\) is the construction adit empty vehicle speed, \({v}_{h1}\) is the cross passage vehicle speed which is on-load, \({v}_{h2}\) is the cross passage empty vehicle speed, \({v}_{m1}\) is the open road vehicle speed which is on-load, and \({v}_{m2}\) is the open road empty vehicle speed.
(2) Vehicle transportation time
In Eqs. ( 32 ) and ( 33 ), \({N}_{z}\) is the loading time of a single working face slag discharge, and \({t}_{yz}\) is the slag transport time.
When the first slag transport vehicle drives out of the working face, the one-way hourly vehicle flow is counted, forming a vehicle statistical function \({q}_{t}\) with respect to time. The time node of the vehicle flow is related to the starting time of the working day, vehicle speed, loading time, and construction time before the slag transport.
Here, \({Q}_{t}\left(i,m\right)\) is the \(m\) -hour traffic flow of the \(i\) th construction support hole, and \({q}_{t}(i,j,m)\) is the \(m\) -hour traffic flow of the \(j\) th unit project carried by the \(i\) th construction adit. Similarly, we can determine the real-time traffic flow of the cross-passage and open-line road.
This section discusses the application of the proposed underground cavities construction simulation system. The construction of the diversion tunnel at the CB Hydropower Station is long with deep burial, large cross-section, and complex geological conditions.
Project overview
Engineering conditions.
The CB Hydropower Station is located in the upper gorge section of the Jinsha River, and is the 11 th stage among the planned 13 cascade hydropower stations in the Chuanzang section in the upper reaches of the Jinsha River. The two tunnels and four engines are arranged according to the diversion system of the hydropower station, most are buried at more than 400 m deep, and the maximum buried depth is approximately 1160 m. The single tunnel length of the diversion tunnels is approximately 11.17 km (from the starting point of the 1st diversion tunnel to the surge chamber) (Fig. 4 ), distance between the axes is 51 m, and longitudinal slope of the tunnel ranges between 1.39%–1.41%. The tunnel has a circular cross-section with an inner diameter of 13 m.
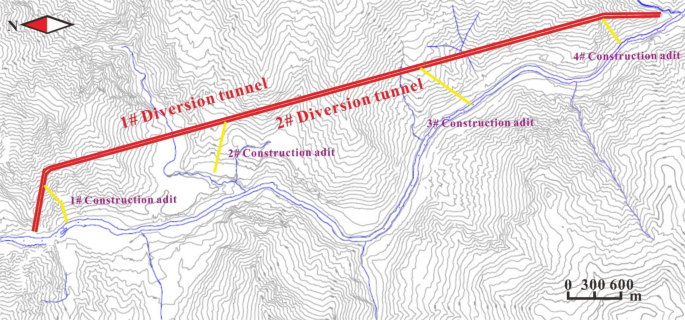
CB Hydropower Station Dam site and layout of diversion tunnels.
Based on the rock type, rock integrity, and rock structure type of the diversion tunnel area, the surrounding rock of the 1st diversion tunnel is preliminarily classified (Fig. 5 ). The Type III surrounding rock is mainly composed of medium-thick layered schist, marble and massive granite. The rock is hard, but the joints are developed and the rock mass is more complete. It accounts for approximately 40.4% of the total length of the tunnel. The Type IV surrounding rock is mainly thin layer, phyllite schist, slate, and weathering, fracture development, fault influence tunnel section. The rock is relatively weak and the structure is developed. It accounts for approximately 49.9% of the total length of the tunnel. The Type V surrounding rock is mainly a fault fracture zone, and the rock mass is in a fragmented and clastic structure. The surrounding rock is extremely unstable and the deformation and failure are serious. It accounts for approximately 9.7% of the total length of the tunnel. The specific surrounding rock types and mechanical parameters of the diversion tunnel are shown in Table. 1 .
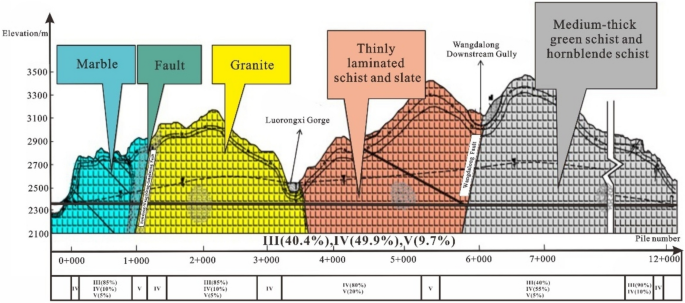
Classification of surrounding rock of 1 st diversion tunnel.
Main construction characteristics
(1) The construction section is large and cavity is long, accordingly, the project scale is extremely large.
(2) Construction safety issues are prominent. The ground stress is high. The maximum buried depth of the tunnel will reach 1100 m, the vertical stress can reach 30 MPa, and the horizontal stress can reach more than 20 MPa. It can be obtained from the strength stress ratio of surrounding rock Rb/σ m = (50 ~ 60)/(30 ~ 40MPa) = 1 ~ 2 that there is the possibility of weak rock burst. The rock mass near regional faults such as Wangdalong fault is relatively broken and has strong water permeability, which may connect river water and gully surface water and produce water inrush.
(3) The construction period is relatively short. The scale of the diversion tunnel project is large, and construction traffic, ventilation, drainage, and other related issues are relatively difficult to solve.
(4) The two diversion tunnels are parallel. There are cross-passages between the two diversion tunnels that can be used for workers to enter the 1 st diversion tunnel from the 2nd diversion tunnel. To ensure the adequate construction of the 1 st diversion tunnel and shorten the corresponding construction period, the construction work surface at the 1st diversion tunnel is increased. Then, simultaneous excavation and lining construction of multiple work surfaces can be realised.
(5) Excavation and lining procedures: The excavation of the diversion tunnel is performed by the drilling-blasting excavation method. Considering that the construction section of the diversion tunnel is large, the excavation is conducted in layers. Accordingly, the excavation of the upper layer is completed before the excavation of the lower layer. The lining is performed one month after the tunnel excavation is completed, so that the lining and excavation would not interfere with each other. Both diversion tunnels are first lined with a steel trolley for the arch lining and then for the floor lining.
(6) The single diversion tunnel of the hydropower station is approximately 11 km long with four construction adits (8 m × 7 m), which are of the city gate type. The control section is between the 2nd construction adit and 3 rd construction adit, which is 3.79 km long.
Construction simulation parameters and programme settings
The main parameters selected are the excavation model, lining model, construction machinery equipment, and related construction engineering parameters. The parameters are described as follows:
(1) Excavation model
The upper and lower halves of the diversion tunnel are excavated in layers. The drilling-blasting excavation model is adopted for the excavation of the upper half of the tunnel, whereas the layered excavation model is adopted for the lower part.
(2) Lining model.
The concrete lining of the diversion tunnel should be first applied to the upper 3/4 part of the cavern, the bottom 1/4 part of the cavern should be lined later. The arch ring of the lining should be implemented based on a steel trolley lining model, and the bottom board of the lining should be implemented based on a sliding block lining model.
(3) Selection of the machinery equipment.
The excavation of the upper half of the tunnel should be performed with a three-arm hydraulic drilling rig, whereas that of the lower part should be performed with a down-hole drill. The 20t dump truck should be selected as the slag truck, 6m 3 pump truck should be used as the concrete pump truck, 4.2 M loader should be configured as the loader, and steel trolley should be configured for the arch ring lining.
(4) Construction footage.
Because of the unique engineering, geological, and hydrogeological settings of the project diversion tunnel, the processes on key lines that affect the construction period of the tunnel excavation are listed in Table. 2 . According to the total time spent on the critical processes of different types of surrounding rock, the Type III surrounding rock can complete one cycle every day, and the Type IV and V surrounding rock can complete two cycles every day. The cyclic footage of surrounding rock of Type III, Type IV and Type V is 4m, 1.4m and 0.8m respectively. Considering 25 effective working days per month, the monthly excavation footage of Type III surrounding rock is 100 m/month, that of Type IV surrounding rock is 70 m/month, and that of Type V surrounding rock is 40 m/month.
Due to the inability to concretely consider the risks in construction simulation, this paper chooses to consider the construction risks handling time of 4 months, and allocate the delayed progress to each day.
Based on the actual project characteristics, it is proposed to use a steel trolley for the concrete lining of the arch ring, which is 12 m long. Accordingly, because of the large lining section, the average monthly lining footage is considered to be 120 m.
The bottom board lining of this project is behind the arch lining, and there is less interference in the bottom clearing construction. The speed of the concrete lining of the bottom board is considered to be 300 m/month.
Programme settings
The line of the CB diversion tunnel is long, construction scale is large, and construction term is highly uncertain. To ensure progress, the working surface area is increased by arranging construction adits and cross passages. In general, construction adits are arranged according to the terrain and geological settings along the tunnel. Therefore, the adjustment room is not large. The cross passage is relatively flexible and can be arranged accordingly. Currently, it is often set every few hundred meters, according to the experience of engineering personnel. In actual construction, there will be too much or too little investment, resulting in insufficient optimisation of the construction progress and excessive waste of resources.
Based on these characteristics, the upper and lower halves of the CB diversion tunnel are excavated in layers. To optimise the construction process, the lower half of the tunnel is excavated in advance by arranging a cross passage in the control section. As shown in Fig. 6 , the excavations of the upper half of the two diversion tunnels are conducted simultaneously, and a cross passage is arranged at an appropriate position. When the cross-passage is used, slag-out of the upper half of the 1st diversion tunnel can be carried out through the 1st cross passage—2nd diversion tunnel—construction adit. When the excavation of the lower half of the 1st diversion tunnel is completed, it can be used as a slag-out construction channel. The lower half of the 2nd diversion tunnel is excavated in advance, and slag-out of the upper half of the 2nd diversion tunnel is carried out through the 1st cross passage—1st diversion tunnel—construction adit. Thus, the cross passage can be used to optimise the construction progress of the two diversion tunnels. Setting different numbers of cross passages affects the input of equipment resources and construction process. Hence, five comparison programmes are set up to perform a more comprehensive analysis, as listed in Table 3 .
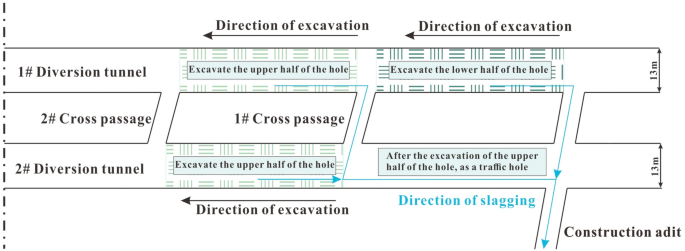
Construction simulation optimisation schematic for the diversion tunnels.
Analysis of results
The simulation results from the aspects of construction schedule, construction intensity, construction machinery, and construction traffic are analysed in this chapter.
Construction progress
The simulation results for Programmes 1–5 are listed in Table 4 . The diversion tunnel in Programme 5 is able to fulfil the conditions of power generation and water supply the earliest, whereas the diversion tunnel in Programme 1 is able to fulfil the conditions of water supply and power generation the latest. The annual construction progress of Programme 5 is shown in Fig. 7 .
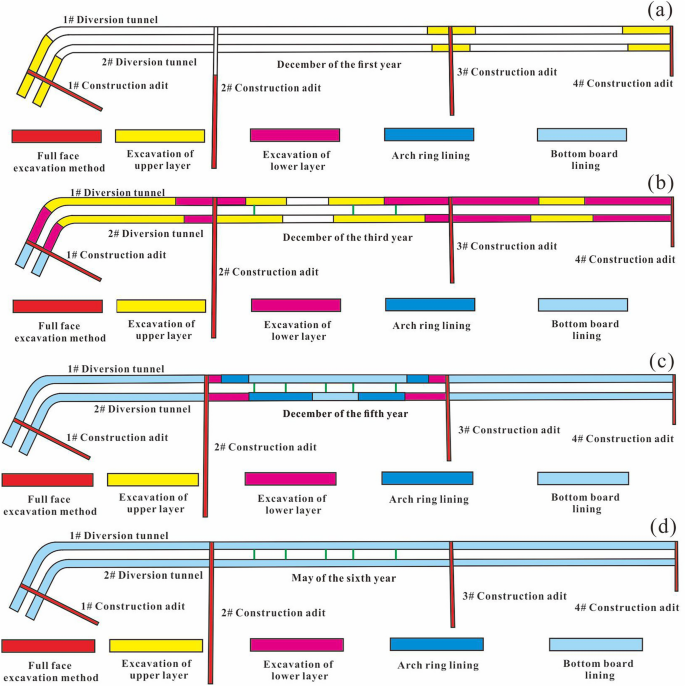
Construction simulation progress chart: ( a ) the construction node in December of the first year; ( b ) the construction node in December of the third year; ( c ) the construction node in December of the fifth year; ( d ) the construction node in May of the sixth year.
Construction traffic
The construction traffic is analysed mainly regarding the control section after the cross-passage became operational. The traffic flow and slag transportation of 2 nd and 3rd construction adits are described as follows.
In the construction simulation of the diversion tunnel, 20t dump trucks are all used for slag-out. The peak period of slag-out vehicles is mainly concentrated after the cross-passage became operational, accordignly, an increase in the construction section leads to an increase in the number of slag-out vehicles. The number of slag-out vehicles during the peak construction period of the 2 nd construction adit is shown in Fig. 8 a. The maximum vehicle flow for Programme 1 is 20 vehicles/h, and that for Programmes 2–5 is 25 vehicles/h. No sustained traffic flow in excess of the control is present.
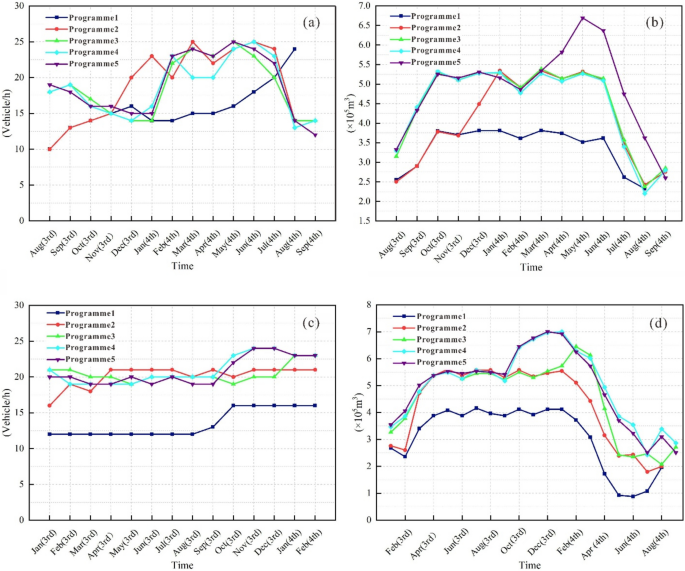
Construction traffic simulation results for the peak section of 2nd and 3rd construction adit: ( a ) the number of slag-out vehicles with 2nd construction adit; ( b ) the amount of slag-out with 2nd construction adit; ( c ) the number of slag-out vehicles with 3rd construction adit; ( d ) the amount of slag-out with 3rd construction adit.
The monthly amount of slag-out in the peak section of the 2 nd construction adit is shown in Fig. 8 b. The maximum strength of the monthly slag-out in each construction programme is 38,300 m 3 , 52,700 m 3 , 52,700 m 3 , 52,700 m 3 , and 67,200 m 3 , respectively, for Programmes 1–5.
The number of slag-out vehicles in the peak construction period of the 3rd construction adit is shown in Fig. 8 c, the maximum vehicle flows are 16, 21, 23, 24, and 24 vehicles/h for Programmes 1–5, respectively. All vehicle flows are less than 25 vehicles/h.
The monthly amount of slag-out in the peak section of the 3 rd construction adit is shown in Fig. 8 d. The maximum strength of the monthly slag-out in each construction programme is 40,800 m 3 , 55,300 m 3 , 63,800 m 3 , 69,700 m 3 , and 69,800 m 3 , respectively, for Programmes 1–5.
Construction intensity
The construction intensity of the downstream excavation surface of the 2 nd construction adit is shown in Fig. 9 . The maximum construction intensity for Programmes 1–4 is 29,000 m 3 , and that for Programme 5 is 38,200 m 3 .
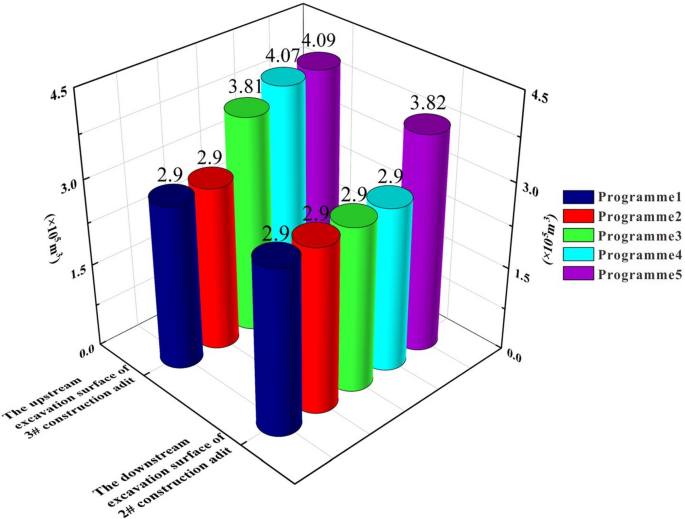
Maximum excavation intensity at the surface of the control section construction adit.
The construction intensity of the upstream excavation surface of the 3 rd construction adit is shown in Fig. 9 . The maximum construction intensity for Programmes 1–5 is 29,000 m 3 , 29,000 m 3 , 38,100 m 3 , 40,700 m 3 , and 40,800 m 3 , respectively.
Construction machinery equipment
In the construction of the diversion tunnel, a three-arm hydraulic drilling rig and down-hole drill are mainly used for the excavation. The loading equipment adopts a 4.2 M loader, 20t dump truck for slag-out, 6 m 3 pump truck to transport concrete, and steel trolley for lining, the maximum uses of mechanical equipment are reported in Table 5 .
This section focuses on the analysis of the monthly maximum demand plan for down-hole drills and 20t dump trucks.
A down-hole drill is primarily used in the lower-layer excavation. As shown in Fig. 10 a, the maximum monthly demand for Programme 1 is 16 sets for 7 months, that for Programme 2 is 20 sets for 4 months, that for Programme 3 is 22 sets for 3 months, that for Programme 4 is 22 sets for 6 months, and that for Programme 5 is 22 sets for 7 months. Programmes 1 and 5 are more reasonable in terms of resource investment and last up to 7 months, however, the duration of Programme 1 is deemed too long.
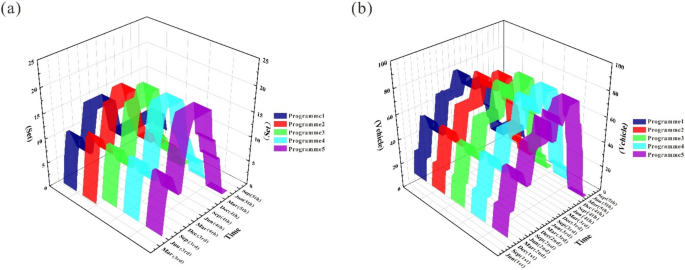
Monthly demand of the construction machinery: ( a ) usage of the down-hole drill; ( b ) usage of the 20t dump truck.
The 20t dump truck is mainly used for slag transportation during tunnel excavation. As shown in Fig. 10 b, the maximum monthly demand for Programme 1 is 84 vehicles for 3 months, that for Programme 2 is 90 vehicles for 2 months, that for Programme 3 is 90 vehicles for 6 months, that for Programme 4 is 90 vehicles for 9 months, and that for Programme 5 is 90 vehicles for 10 months. Programme 5 is more reasonable in terms of resource investment and lasts up to 10 months.
Comprehensive analysis
The construction programme design of the CB diversion tunnel group is discussed in this section, mainly based on the layout of cross-passages between the tunnels, effectively increasing the construction surface, and carrying out the excavation of the lower layer of the diversion tunnel in advance to speed up the construction progress.
In this section, a programme for laying 2–5 cross passages in the control section is proposed. Construction simulation is conducted using the UCCSS developed in this study, and comprehensive analysis of each programme is conducted by considering the aspects of construction intensity, construction traffic, machinery and equipment, construction progress, etc.. In terms of construction intensity, the maximum excavation intensity of the control sections for Programmes 1–5 is 58,000 m 3 , 58,000 m 3 , 67,100 m 3 , 69,700 m 3 , and 69,900 m 3 . According to the construction traffic simulation results of Programmes 1–5, the 20t dump truck fully meets the slag-out requirements, resulting in no traffic congestion. From the perspective of the construction period, the beginning of the diversion tunnel excavation is the April of the first year. The construction period of the 1st diversion tunnel for Programmes 1–5 is 74.5 months, 67, 65, 64.5, and 63 months, respectively, and that of the 2nd diversion tunnel is 76, 72, 69, 66.5, and 66 months, respectively.
The construction period of Programme 5 is the shortest, and the equipment resource input is similar to that of the other four programmes, making it more economical. Based on the comprehensive analysis, Programme 5 can be used as the recommended construction programme.
Discussions
Numerous engineering applications show that the UCCSS is practical and reliable and has advantages in terms of parametric design, whole-process system simulation, easy operation, and strong expansion. First, a fully parametric design is adopted for different construction methods and working procedures so that programme adjustments can be easily made by modifying the parameters. Second, a dynamic simulation of construction transportation, resource allocation, period, and intensity during the entire process of excavation and lining construction of different underground cavities space types can be carried out. The traffic flow and transport intensity of each process time under different paths, as well as the excavation and lining intensities at any moment of construction, can be queried using this system. Third, the system model is relatively simple, owing to the functions of technical parameters that prompt, copy, modify, help, automatic update of the entire system, dynamic information queries, and error identification. Finally, owing to the developments in large-scale construction machinery and equipment and progress of tunnelling construction technology, innovations in underground engineering construction technology and updates of organisational management concepts will be effectively promoted by new methods, technologies, and equipment. New models and simulation programmes based on new mathematical models can be added to this system to adapt it for development.
However, in view of the current rapid developments in computer technology and engineering practice and demand for more comprehensive simulation functions, many shortcomings still remain in the UCCSS. First, visualisation technology is not implemented well in the system and the process of real-time simulation is not entirely fulfilled. Therefore, the follow-up needs to be improved based on these two aspects. Implementing 3D animation demonstration technology is suggested to demonstrate the complex construction process with moving images in a realistic manner and provide a visual analysis means for construction management. Second, developing a real-time construction simulation system is recommended for actual construction processes so that the actual situation can be fed back to the system in a timely manner to better guide the actual construction schedule.
Conclusions
The construction of underground cavities in hydraulic and hydropower projects involves many factors and it is an extremely complex process. It is of great significance to closely integrate construction simulation with actual production situations to improve the guidance of simulation results for practical engineering. This article innovatively introduces the principles of production line balance and rule cycle concept, combining technology with management, and a practical, expandable, full-featured, and easy-to-operate UCCSS is developed. The time-step method of the discrete system is adopted to perform hierarchical modelling, which divides the entire project into four levels, namely, unit project, units project, division project, and sub-project. Different excavation, lining, machinery equipment models and construction plans are implemented in the system based on the actual construction characteristics. Accoroding to the analysis of the construction transportation, construction intensity, and construction progress to obtain the optimal construction scheme of underground cavities construction. The proposed method is an efficient calculation and analysis tool for complex underground cavities construction, improves the modernisation level of construction organisation design to a certain extent, and has broad application prospects. The system is successfully applied to the construction organisation design of the diversion tunnels of the CB Hydropower Station, providing important technical support for the optimisation of the construction programme and decision-making management.
Data availability
All data generated or analysed during this study are included in this article.
Hajjar, D., & AbouRizk, S. Development of an object oriented framework for the simulation of earth moving operations. Proc., Intelligent Information Systems Conf., IEEE, New York, 326-330. https://doi.org/10.1109/iis.1997.645279 . (1997).
Yu, J., Zhong, D., Ren, B., Tong, D. & Hong, K. Probabilistic risk analysis of diversion tunnel construction simulation. Comput.-aided Civil Infrastruct. Eng. 32 (9), 748–771. https://doi.org/10.1111/mice.12276 (2017).
Article Google Scholar
Halpin, D. W. Cyclone-Method for modeling job site processes. J. Constr. Div. 103 (3), 489–499. https://doi.org/10.1061/jcceaz.0000712 (1977).
Paulson, B. C. Interactive graphics for simulating construction operations. J. Constr. Div. 104 (1), 69–76. https://doi.org/10.1061/jcceaz.0000758 (1978).
Chang, D. Resque [D] (University of Michigan, 1987).
Google Scholar
Ioannou, P. G. UM-CYCLONE user’s guide[D] (University of Michigan, 1989).
Halpin, D. W. Micro-CYCLONE User’s Manual (Purdue University, West Lafayette, 1990).
Liu, L. COOPS: Construction object-oriented process simulation system. https://deepblue.lib.umich.edu/handle/2027.42/128820 . (1991).
Huang, R., Grigoriadis, A. M. & Halpin, D. W. Simulation of cable-stayed bridges using disco. Winter Simul. Conf. , 1130-1136. https://doi.org/10.5555/193201.194680 (1994).
Martinez, J. C. & Ioannou, P. G. General purpose simulation with stroboscope. Winter Simul.Conf. , 1159-1166. https://doi.org/10.5555/193201.194688 (1994).
AbouRizk, S. & Mohamed, Y. Simphony: An integrated environment for construction simulation. Winter Simul.Conf. 2 , 1907–1914. https://doi.org/10.5555/510378.510656 (2000).
Kamat, V. R. & Martinez, J. C. Validating complex construction simulation models using 3D visualization. Syst. Anal. Model. Simul. 43 (4), 455–467. https://doi.org/10.1080/02329290290028507 (2003).
Lu, M., Lam, H. & Dai, F. Resource-constrained critical path analysis based on discrete event simulation and particle swarm optimization. Autom. Constr. 17 (6), 670–681. https://doi.org/10.1016/j.autcon.2007.11.004s (2008).
Article CAS Google Scholar
AbouRizk, S. M., & Hague, S. An overview of the COSYE environment for construction simulation. Proc. 2009 Winter Simulation Conference (WSC). https://doi.org/10.1109/wsc.2009.5429307 . (2009).
Alvanchi, A., Lee, S. & AbouRizk, S. Modeling framework and architecture of hybrid system dynamics and discrete event simulation for construction. Comput.-Aided Civil Infrastruct. Eng. 26 (2), 77–91. https://doi.org/10.1111/j.1467-8667.2010.00650.x (2011).
Denghua, Z. Simulation study of tunnel cycle construction process (in Chinese)[D] (University of Tianjin, 1987).
Liu, D., Xuan, P., Li, S. & Huang, P. Schedule risk analysis for TBM tunneling based on adaptive CYCLONE simulation in a geologic Uncertainty-Aware context. J. Comput. Civil Eng. 29 (6), https://doi.org/10.1061/(asce)cp.1943-5487.0000441 (2015).
Shahin, A., AbouRizk, S., Mohamed, Y. & Fernando, S. Simulation modeling of weather-sensitive tunnelling construction activities subject to cold weather. Can. J. Civ. Eng. 41 (1), 48–55. https://doi.org/10.1139/cjce-2013-0087 (2014).
Zhong, D., Bi, L., Yu, J. & Zhao, M. Robustness analysis of underground powerhouse construction simulation based on markov Chain monte carlo method. Sci. China. Technol. Sci. 59 (2), 252–264. https://doi.org/10.1007/s11431-015-5859-3 (2015).
Article ADS Google Scholar
Sharafat, A., Latif, K. & Seo, J. Risk analysis of TBM tunneling projects based on generic bow-tie risk analysis approach in difficult ground conditions. Tunn. Undergr. Space Technol. 111 , 103860 . https://doi.org/10.1016/j.tust.2021.103860 (2021).
Denghua, Z., Weibo, Z. & Jiaxiang, Z. Study on Dynamic Visual Simulation System for Complex Construction Processes (in Chinese). Hydroelectricity 12 , 28–30 (2000).
Wang Xiaoling, Qu., Liwen, R. B., Mengqi, Z., Yao, X. & Zhen, L. Dynamic visual simulation of diversion tunnel construction based on CATIA (in Chinese). J. Hydraulic Eng. 49 (03), 369–378. https://doi.org/10.13243/j.cnki.slxb.20170646 (2018).
Sharafat, A., Khan, M. S., Latif, K. & Seo, J. BIM-Based Tunnel Information Modeling framework for visualization, management, and simulation of Drill-and-Blast tunneling projects. J. Comput. Civil Eng. 35 (2). https://doi.org/10.1061/(asce)cp.1943-5487.0000955 (2021).
Rafsanjani, H. N. & Nabizadeh, A. H. Towards human-centered artificial intelligence (AI) in architecture, engineering, and construction (AEC) industry. Comput. Hum. Behav. Rep. 11 , 100319 . https://doi.org/10.1016/j.chbr.2023.100319 (2023).
Wang, M., Zhou, J., Chen, J., Jiang, N., Zhang, P., Li, H. Automatic identification of rock discontinuity and stability analysis of tunnel rock blocks using terrestrial laser scanning. J. Rock Mech. Geotech. Eng. 15 (7), 1810–1825. https://doi.org/10.1016/j.jrmge.2022.12.015 (2023).
Fengju, K. Modern simulation technology and applications (in Chinese) [M] (National Defense Industry Press, 2001).
Download references
Acknowledgements
We gratefully acknowledge the support of the Sichuan Youth Science and Technology Innovation Research Team Project (2020JDTD0006) and the Open Research Fund of Key Laboratory of Reservoir and Dam Safety Ministry of Water Resources (YK323002).
Author information
Authors and affiliations.
College of Water Resource and Hydropower, Sichuan University, Chengdu, 610065, China
Yu-han Ran, Hai-bo Li, Shun-tong Xu & Xing-guo Yang
State Key Laboratory of Hydraulics and Mountain River Engineering, Sichuan University, Chengdu, 610065, China
Hai-bo Li & Xing-guo Yang
Guiyang Engineering CO. LTD., Power China, Guiyang, 550081, China
Zhi-chao Yu
You can also search for this author in PubMed Google Scholar
Contributions
Yu-han Ran and Hai-bo Li wrote the main manuscript text . Hai-bo Li, Yu-han ran and and Xingguo Yang jointly developed the simulation system. Zhi-chao Yu prepared Figs. 4 and Table 1. All authors reviewed the manuscript.
Corresponding author
Correspondence to Hai-bo Li .
Ethics declarations
Competing interests.
The authors declare no competing interests.
Additional information
Publisher's note.
Springer Nature remains neutral with regard to jurisdictional claims in published maps and institutional affiliations.
Rights and permissions
Open Access This article is licensed under a Creative Commons Attribution-NonCommercial-NoDerivatives 4.0 International License, which permits any non-commercial use, sharing, distribution and reproduction in any medium or format, as long as you give appropriate credit to the original author(s) and the source, provide a link to the Creative Commons licence, and indicate if you modified the licensed material. You do not have permission under this licence to share adapted material derived from this article or parts of it. The images or other third party material in this article are included in the article’s Creative Commons licence, unless indicated otherwise in a credit line to the material. If material is not included in the article’s Creative Commons licence and your intended use is not permitted by statutory regulation or exceeds the permitted use, you will need to obtain permission directly from the copyright holder. To view a copy of this licence, visit http://creativecommons.org/licenses/by-nc-nd/4.0/ .
Reprints and permissions
About this article
Cite this article.
Ran, Yh., Li, Hb., Xu, St. et al. Construction simulation and scheme optimisation of complex underground cavities. Sci Rep 14 , 20879 (2024). https://doi.org/10.1038/s41598-024-71515-y
Download citation
Received : 13 May 2024
Accepted : 28 August 2024
Published : 06 September 2024
DOI : https://doi.org/10.1038/s41598-024-71515-y
Share this article
Anyone you share the following link with will be able to read this content:
Sorry, a shareable link is not currently available for this article.
Provided by the Springer Nature SharedIt content-sharing initiative
- Construction simulation; Underground cavities; Construction simulation system; Construction organszation
By submitting a comment you agree to abide by our Terms and Community Guidelines . If you find something abusive or that does not comply with our terms or guidelines please flag it as inappropriate.
Quick links
- Explore articles by subject
- Guide to authors
- Editorial policies
Sign up for the Nature Briefing newsletter — what matters in science, free to your inbox daily.

Information
- Author Services
Initiatives
You are accessing a machine-readable page. In order to be human-readable, please install an RSS reader.
All articles published by MDPI are made immediately available worldwide under an open access license. No special permission is required to reuse all or part of the article published by MDPI, including figures and tables. For articles published under an open access Creative Common CC BY license, any part of the article may be reused without permission provided that the original article is clearly cited. For more information, please refer to https://www.mdpi.com/openaccess .
Feature papers represent the most advanced research with significant potential for high impact in the field. A Feature Paper should be a substantial original Article that involves several techniques or approaches, provides an outlook for future research directions and describes possible research applications.
Feature papers are submitted upon individual invitation or recommendation by the scientific editors and must receive positive feedback from the reviewers.
Editor’s Choice articles are based on recommendations by the scientific editors of MDPI journals from around the world. Editors select a small number of articles recently published in the journal that they believe will be particularly interesting to readers, or important in the respective research area. The aim is to provide a snapshot of some of the most exciting work published in the various research areas of the journal.
Original Submission Date Received: .
- Active Journals
- Find a Journal
- Proceedings Series
- For Authors
- For Reviewers
- For Editors
- For Librarians
- For Publishers
- For Societies
- For Conference Organizers
- Open Access Policy
- Institutional Open Access Program
- Special Issues Guidelines
- Editorial Process
- Research and Publication Ethics
- Article Processing Charges
- Testimonials
- Preprints.org
- SciProfiles
- Encyclopedia
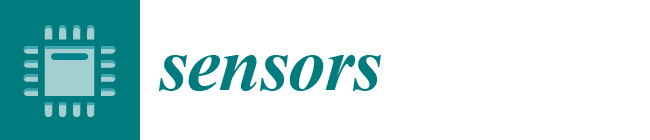
Article Menu

- Subscribe SciFeed
- Recommended Articles
- Google Scholar
- on Google Scholar
- Table of Contents
Find support for a specific problem in the support section of our website.
Please let us know what you think of our products and services.
Visit our dedicated information section to learn more about MDPI.
JSmol Viewer
A vision–language model-based traffic sign detection method for high-resolution drone images: a case study in guyuan, china.
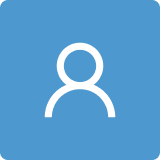
1. Introduction
2. existing deep-learning-based traffic sign detection method, 3. the vison language model-based traffic sign detection method, 3.1. keyword dictionary construction to explain traffic signs, 3.2. multi-modal feature extraction with contrastive language-image pretraining, 3.3. traffic sign classification with similarity measurement, 4. the traffic sign detection task: a case study in guyuan, china, 4.1. data collection and data preprocessing, 4.2. traffic sign detection with vlm and supervised yolo networks, 4.3. comparison with supervised yolo networks, 4.4. bootstrapping test on the small dataset, 5. the application of traffic sign detection on public datasets, 5.1. experiment configuration, 5.2. quantitative performance evaluation, 5.3. discussion on the detection result, 6. conclusions, author contributions, data availability statement, conflicts of interest.
- Canese, L.; Cardarilli, G.C.; Di Nunzio, L.; Fazzolari, R.; Famil Ghadakchi, H.; Re, M.; Spanò, S. Sensing and Detection of Traffic Signs Using CNNs: An Assessment on Their Performance. Sensors 2022 , 22 , 8830. [ Google Scholar ] [ CrossRef ] [ PubMed ]
- Sanyal, B.; Mohapatra, R.K.; Dash, R. Traffic Sign Recognition: A Survey. In Proceedings of the 2020 International Conference on Artificial Intelligence and Signal Processing (AISP), Amaravati, India, 10–12 January 2020. [ Google Scholar ]
- Lim, X.R.; Lee, C.P.; Lim, K.M.; Ong, T.S.; Alqahtani, A.; Ali, M. Recent Advances in Traffic Sign Recognition: Approaches and Datasets. Sensors 2023 , 23 , 4674. [ Google Scholar ] [ CrossRef ] [ PubMed ]
- Chakravarthy, A.S.; Sinha, S.; Narang, P.; Mandal, M.; Chamola, V.; Yu, F.R. DroneSegNet: Robust Aerial Semantic Segmentation for UAV-Based IoT Applications. IEEE Trans. Veh. Technol. 2022 , 71 , 4277–4286. [ Google Scholar ] [ CrossRef ]
- Arya, D.; Maeda, H.; Sekimoto, Y. From Global Challenges to Local Solutions: A Review of Cross-country Collaborations and Winning Strategies in Road Damage Detection. Adv. Eng. Inform. 2024 , 60 , 102388. [ Google Scholar ] [ CrossRef ]
- Du, J.; Zhang, R.; Gao, R.; Nan, L.; Bao, Y. RSDNet: A New Multiscale Rail Surface Defect Detection Model. Sensors 2024 , 24 , 3579. [ Google Scholar ] [ CrossRef ]
- Madani, A.; Yusof, R. Traffic sign recognition based on color, shape, and pictogram classification using support vector machines. Neural Comput. Appl. 2018 , 30 , 2807–2817. [ Google Scholar ] [ CrossRef ]
- Kerim, A.; Efe, M.Ö. Recognition of Traffic Signs with Artificial Neural Networks: A Novel Dataset and Algorithm. In Proceedings of the 2021 International Conference on Artificial Intelligence in Information and Communication (ICAIIC), Jeju Island, Republic of Korea, 13–16 April 2021; pp. 171–176. [ Google Scholar ]
- Soni, D.; Chaurasiya, R.K.; Agrawal, S. Improving the Classification Accuracy of Accurate Traffic Sign Detection and Recognition System Using HOG and LBP Features and PCA-Based Dimension Reduction. In Proceedings of the International Conference on Sustainable Computing in Science, Technology and Management (SUSCOM), Amity University Rajasthan, Jaipur, India, 20–22 January 2019. [ Google Scholar ]
- Namyang, N.; Phimoltares, S. Thai traffic sign classification and recognition system based on histogram of gradients, color layout descriptor, and normalized correlation coefficient. In Proceedings of the 2020-5th International Conference on Information Technology (InCIT), Chonburi, Thailand, 21–22 October 2020; pp. 270–275. [ Google Scholar ]
- Wang, B. Research on the Optimal Machine Learning Classifier for Traffic Signs. In Proceedings of the SHS Web of Conferences, Virtual Event, 26 August 2022; EDP Sciences: Les Ulis, France, 2022; Volume 144, p. 03014. [ Google Scholar ]
- Li, J.; Wang, Z. Real-time traffic sign recognition based on efficient CNNs in the wild. IEEE Trans. Intell. Transp. Syst. 2018 , 20 , 975–984. [ Google Scholar ] [ CrossRef ]
- Sokipriala, J.; Orike, S. Traffic sign classification comparison between various convolution neural network models. Int. J. Sci. Eng. Res. 2021 , 12 , 165–171. [ Google Scholar ] [ CrossRef ]
- Zhu, Y.; Yan, W.Q. Traffic sign recognition based on deep learning. Multimed. Tools Appl. 2022 , 81 , 17779–17791. [ Google Scholar ] [ CrossRef ]
- Redmon, J.; Divvala, S.; Girshick, R.; Farhadi, A. You Only Look Once: Unified, Real-Time Object Detection. In Proceedings of the 2016 IEEE Conference on Computer Vision and Pattern Recognition (CVPR), Las Vegas, NV, USA, 27–30 June 2016; pp. 779–788. [ Google Scholar ]
- Li, X.; Geng, S. Improved traffic sign detection for YOLOv5s. In Proceedings of the IEEE 4th International Conference on Computer Engineering and Application, Hangzhou, China, 7–8 April 2023; pp. 696–699. [ Google Scholar ]
- Yu, J.; Ye, X.; Tu, Q. Traffic Sign Detection and Recognition in Multiimages Using a Fusion Model With YOLO and VGG Network. Trans. Intell. Transp. Syst. 2022 , 23 , 16632–16642. [ Google Scholar ] [ CrossRef ]
- Girshick, R.; Donahue, J.; Darrell, T.; Malik, J. Region-Based Convolutional Networks for Accurate Object Detection and Segmentation. IEEE Trans. Pattern Anal. Mach. Intell. 2015 , 38 , 142–158. [ Google Scholar ] [ CrossRef ]
- Ren, S.; He, K.; Girshick, R.; Sun, J. Faster R-CNN: Towards real-time object detection with region proposal networks. Trans. Pattern Anal. Mach. Intell. 2017 , 39 , 1137–1149. [ Google Scholar ] [ CrossRef ] [ PubMed ]
- Zhang, J.; Xie, Z.; Sun, J.; Zou, X.; Wang, J. A cascaded R-CNN with multiscale attention and imbalanced samples for traffic sign detection. IEEE Access 2020 , 8 , 29742–29754. [ Google Scholar ] [ CrossRef ]
- Zhang, J.; Wang, W.; Lu, C.; Wang, J.; Sangaiah, A.K. Lightweight deep network for traffic sign classification. Ann. Telecommun. 2020 , 75 , 369–379. [ Google Scholar ] [ CrossRef ]
- Triki, N.; Karray, M.; Ksantini, M. A Real-Time Traffic Sign Recognition Method Using a New Attention-Based Deep Convolutional Neural Network for Smart Vehicles. Appl. Sci. 2023 , 13 , 4793. [ Google Scholar ] [ CrossRef ]
- Zhang, J.; Ye, Z.; Jin, X.; Wang, J.; Zhang, J. Real-time traffic sign detection based on multiscale attention and spatial information aggregator. J. Real-Time Image Process. 2022 , 19 , 1155–1167. [ Google Scholar ] [ CrossRef ]
- Carion, N.; Massa, F.; Synnaeve, G.; Usunier, N.; Kirillov, A.; Zagoruyko, S. End-to-end object detection with transformers. In Proceedings of the European Conference on Computer Vision, Glasgow, UK, 23–28 August 2020; pp. 213–229. [ Google Scholar ]
- Zhang, J.; Huang, J.; Jin, S.; Lu, S. Vision-Language Models for Vision Tasks: A Survey. arXiv 2023 , arXiv:2304.00685. [ Google Scholar ] [ CrossRef ]
- Jaiswal, A.; Ramesh Babu, A.; Zaki Zadeh, M.; Banerjee, D.; Makedon, F. A Survey on Contrastive Self-Supervised Learning. Technologies 2021 , 9 , 2. [ Google Scholar ] [ CrossRef ]
- Gui, J.; Chen, T.; Zhang, J.; Cao, Q.; Sun, Z.; Luo, H.; Tao, D. A Survey on Self-supervised Learning: Algorithms, Applications, and Future Trends. arXiv 2023 , arXiv:2301.05712. [ Google Scholar ] [ CrossRef ]
- Khan, S.; Naseer, M.; Khan, S.; Naseer, M.; City, M.; Dhabi, A.; Zamir, S.W.; Shah, M.; Hayat, M.; Zamir, S.W.; et al. Transformers in Vision: A Survey. ACM Comput. Surv. (CSUR) 2022 , 54 , 200. [ Google Scholar ] [ CrossRef ]
- Dosovitskiy, A.; Beyer, L.; Kolesnikov, A.; Weissenborn, D.; Zhai, X.; Unterthiner, T.; Dehghani, M.; Minderer, M.; Heigold, G.; Gelly, S.; et al. An Image is Worth 16×16 Words: Transformers for Image Recognition at Scale. arXiv 2021 , arXiv:2010.11929. [ Google Scholar ]
- Liu, Z.; Lin, Y.; Cao, Y.; Hu, H.; Wei, Y.; Zhang, Z.; Lin, S.; Guo, B. Swin Transformer: Hierarchical Vision Transformer using Shifted Windows. arXiv 2021 , arXiv:2103.14030. [ Google Scholar ]
- Redmon, J.; Farhadi, A. YOLO9000: Better, faster, stronger. In Proceedings of the 2017 IEEE Conference on Computer Vision and Pattern Recognition (CVPR), Honolulu, HI, USA, 21–26 July 2017; pp. 7263–7271. [ Google Scholar ]
- Redmon, J.; Farhadi, A. Yolov3: An incremental improvement. arXiv 2018 , arXiv:1804.02767. [ Google Scholar ]
- Bochkovskiy, A.; Wang, C.-Y.; Liao, H.-Y.M. Yolov4: Optimal speed and accuracy of object detection. arXiv 2020 , arXiv:2004.10934. [ Google Scholar ]
- Ultralytics. YOLOv5. Available online: https://github.com/ultralytics/yolov5 (accessed on 1 November 2020).
- Wang, C.-Y.; Bochkovskiy, A.; Liao, H.-Y.M. YOLOv7: Trainable bag-of-freebies sets new state-of-the-art for real-time object detectors. In Proceedings of the 2023 IEEE/CVF Conference on Computer Vision and Pattern Recognition (CVPR), Vancouver, BC, Canada, 17–24 June 2023; pp. 7464–7475. [ Google Scholar ]
- Jocher, G.; Chaurasia, A.; Qiu, J. Ultralytics YOLOv8. Available online: https://github.com/ultralytics/ultralytics (accessed on 20 June 2024).
- GB 5768-2022 ; Traffic Signs. Standardization Administration of China: Beijing, China, 2022.
- Li, J.; Li, D.; Xiong, C.; Hoi, S. BLIP: Bootstrapping Language-Image Pre-training for Unified Vision-Language Understanding and Generation. arXiv 2022 , arXiv:2201.12086v2. [ Google Scholar ]
- Li, J.; Li, D.; Savarese, S.; Hoi, S. BLIP-2: Bootstrapping Language-Image Pre-Training with Frozen Image Encoders and Large Language Models. arXiv 2023 , arXiv:2301.12597. [ Google Scholar ]
- Radford, A.; Kim, J.W.; Hallacy, C.; Ramesh, A.; Goh, G.; Agarwal, S.; Sastry, G.; Askell, A.; Mishkin, P.; Clark, J.; et al. Learning transferable visual models from natural language supervision. In Proceedings of the 38th International Conference on Machine Learning, PMLR, Virtual Event, 18–24 July 2021; pp. 8748–8763. [ Google Scholar ]
- Vaswani, A.; Shazeer, N.; Parmar, N.; Uszkoreit, J.; Jones, L.; Gomez, A.N.; Kaiser, Ł.; Polosukhin, I. Attention Is All You Need. arXiv 2017 , arXiv:1706.03762. [ Google Scholar ]
- Zhang, J.; Zou, X.; Kuang, L.D.; Wang, J.; Sherratt, R.S.; Yu, X. CCTSDB 2021: A more comprehensive traffic sign detection benchmark. Hum.-Centric Comput. Inf. Sci. 2022 , 12 , 23. [ Google Scholar ]
- Zhu, Z.; Liang, D.; Zhang, S.; Huang, X.; Li, B.; Hu, S. Traffic-sign detection and classification in the wild. In Proceedings of the IEEE Conference on Computer Vision and Pattern Recognition, Las Vegas, NV, USA, 26 June–1 July 2016; pp. 2110–2118. [ Google Scholar ]
- Zhang, J.; Lv, Y.; Tao, J.; Huang, F.; Zhang, J. A robust real-time anchor-free traffic sign detector with one-level feature. IEEE Trans. Emerg. Top. Comput. Intell. 2024 , 8 , 1437–1451. [ Google Scholar ] [ CrossRef ]
- Tian, Z.; Shen, C.; Chen, H.; He, T. FCOS: A simple and strong anchor free object detector. IEEE Trans. Pattern Anal. Mach. Intell. 2022 , 44 , 1922–1933. [ Google Scholar ] [ CrossRef ]
Click here to enlarge figure
Method | Accuracy (%) | Precision (%) | Recall (%) | F1 Score | FPS |
---|---|---|---|---|---|
VLM with dictionary1 | 85.6 | 77.8 | 85.0 | 0.80 | 14.98 |
VLM with dictionary2 | 89.2 | 75.7 | 78.2 | 0.75 | 14.98 |
YOLOv5 | 86.9 | 73.1 | 80.0 | 0.76 | 12.56 |
YOLOv8 | 82.6 | 61.9 | 76.0 | 0.68 | 12.53 |
Dataset | Accuracy (%) | Precision (%) | Recall (%) | F1 Score | FPS |
---|---|---|---|---|---|
CCTSDB2021 | 85.9 | 82.5 | 85.4 | 0.83 | 45.18 |
TT100K | 92.0 | 92.2 | 86.9 | 0.89 | 43.67 |
Methods | Metrics | XS | S | M | L | XL |
---|---|---|---|---|---|---|
VLM-based method | Precision (%) | 75.2 | 86.8 | 92.4 | 91.5 | 91.1 |
Recall (%) | 70.6 | 93.2 | 92.3 | 93.5 | 92.6 | |
Faster RCNN [ ] | Precision (%) | 77.1 | 83.6 | 89.0 | 85.1 | 85.3 |
Recall (%) | 48.7 | 78.1 | 79.2 | 88.1 | 81.3 | |
YOLOv5 [ ] | Precision (%) | 75.6 | 88.6 | 94.7 | 97.3 | 96.9 |
Recall (%) | 55.9 | 75.7 | 88.3 | 89.0 | 91.3 | |
FCOS [ ] | Precision (%) | 85.2 | 91.7 | 93.8 | 91.3 | 93.3 |
Recall (%) | 35.7 | 60.5 | 83.8 | 93.8 | 90.9 | |
One-level feature [ ] | Precision (%) | 77.3 | 85.7 | 89.8 | 90.8 | 88.5 |
Recall (%) | 86.8 | 82.3 | 90.7 | 97.9 | 99.1 |
Methods | Metrics | Sunny | Cloud | Night | Rain | Foggy | Snow |
---|---|---|---|---|---|---|---|
VLM-based method | Precision (%) | 87.1 | 93.5 | 83.7 | 53.9 | 43.1 | 59.3 |
Recall (%) | 92.1 | 95.9 | 83.8 | 65.1 | 60.8 | 66.7 | |
Faster RCNN [ ] | Precision (%) | 85.5 | 92.7 | 76.9 | 61.4 | 77.0 | 96.3 |
Recall (%) | 77.4 | 57.6 | 47.9 | 34.6 | 67.1 | 91.1 | |
YOLOv5 [ ] | Precision (%) | 95.9 | 94.0 | 86.1 | 47.9 | 64.8 | 96.1 |
Recall (%) | 85.1 | 81.2 | 60.6 | 46.7 | 81.3 | 80.7 | |
FCOS [ ] | Precision (%) | 93.9 | 97.0 | 85.1 | 67.8 | 66.7 | 94.5 |
Recall (%) | 75.5 | 68.7 | 55.6 | 31.1 | 38.8 | 63.2 | |
One-level feature [ ] | Precision (%) | 92.1 | 89.6 | 83.1 | 97.0 | 78.7 | 97.5 |
Recall (%) | 97.4 | 87.1 | 84.0 | 74.0 | 91.3 | 87.6 |
The statements, opinions and data contained in all publications are solely those of the individual author(s) and contributor(s) and not of MDPI and/or the editor(s). MDPI and/or the editor(s) disclaim responsibility for any injury to people or property resulting from any ideas, methods, instructions or products referred to in the content. |
Share and Cite
Yao, J.; Li, J.; Li, Y.; Zhang, M.; Zuo, C.; Dong, S.; Dai, Z. A Vision–Language Model-Based Traffic Sign Detection Method for High-Resolution Drone Images: A Case Study in Guyuan, China. Sensors 2024 , 24 , 5800. https://doi.org/10.3390/s24175800
Yao J, Li J, Li Y, Zhang M, Zuo C, Dong S, Dai Z. A Vision–Language Model-Based Traffic Sign Detection Method for High-Resolution Drone Images: A Case Study in Guyuan, China. Sensors . 2024; 24(17):5800. https://doi.org/10.3390/s24175800
Yao, Jianqun, Jinming Li, Yuxuan Li, Mingzhu Zhang, Chen Zuo, Shi Dong, and Zhe Dai. 2024. "A Vision–Language Model-Based Traffic Sign Detection Method for High-Resolution Drone Images: A Case Study in Guyuan, China" Sensors 24, no. 17: 5800. https://doi.org/10.3390/s24175800
Article Metrics
Article access statistics, further information, mdpi initiatives, follow mdpi.
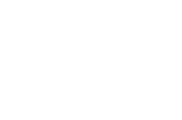
Subscribe to receive issue release notifications and newsletters from MDPI journals

IMAGES
VIDEO
COMMENTS
Blue Yonder's technology addressed not only international transportation needs but also domestic logistics. This meant managing logistics across multiple modes, such as truckload, less-than-truckload (LTL), intermodal, rail, parcel, ocean and air. The alliance team helped the organization standardize the processes and augment its existing ...
Transportation Management System Case Study ----- 1301 Perry Road, Suite 101 Plainfield IN 46168 1.317.838.8900 . MD Logistics Corporate Office 1301 Perry Rd ... current Red Prairie Warehouse Management System (WMS). This integration allows MD Logistics to find customers the most strategic carrier based on a variety of factors, including ...
Definition and Purpose of TMS. Transport Management Software, or TMS, is a powerful tool that helps businesses effectively manage their transportation operations. It is a software solution that streamlines and automates various tasks involved in transportation, such as freight management, route planning, load optimization, and documentation.
3Gtms Case Study: ODW Logistics. Read. ODW Logistics' transportation service began as an asset-based solution in the 1980s. Over the past decade, ODW's non-asset based transportation execution has seen phenomenal growth. However, the company's transportation management system (TMS) ... Source 3Gtms Aug 2016.
captures the essence of optimizing transportation logistics through Enterprise Architecture (EA) by presenting an Integrated Management Systems (IMS)-centered case study.
Transportation Management System is very needed in optimize efficiency and effectiveness on logistics company. ... A descriptive case study of a third-party CTM systems provider is employed to ...
The study examines the processes of the case study transport company, identifies the most significant constraints within them, investigates how a transport management system (TMS) software can eliminate those constraints, and provides a suggestion for adopting a specific TMS solution. The study
An investigative case study of implementing a Transport Management System (TMS) with a rail freight network Master's thesis in Supply Chain Management ANDREAS FAGERBERG DAVID UNGERTH DEPARTMENT OF TECHNOLOGY MANAGEMENT AND ECONOMICS DIVISION OF SERVICE MANAGEMENT AND LOGISTICS CHALMERS UNIVERSITY OF TECHNOLOGY Gothenburg, Sweden 2023 www ...
A Transportation Management System (TMS) is a software tool set that simplifies the planning, tracking, and delivery of goods throughout the supply chain and across multiple regions, jurisdictions, and transport modes. These systems are now essential tools in industries and businesses of all sizes. McKinsey's 2023 Digital Logistics survey of ...
CASE STUDYCASE STUDY:: TRANSPORTATION MANAGEMENT OUTSOURCE SOLUTION 2 Looking for a solution that would improve management of freight and increase customer service, Pilot Chemical decided to upgrade their logistics functions by implementing a Transportation Management System (TMS). Pilot had several goals for its TMS:
DECEMBER 10, 2021. Environmentally Sustainable Supply Chain Management implicates integrating environmental and financially feasible procedures during the SC lifecycle, from material selection to product design and development, manufacturing, packaging, transportation, storage, distribution, consumption, return and disposal. Case Study 75.
Transportation Management System (TMS) stores all transportation-related data maintained by the agency. This Oracle-based database, directly managed by TPD, ties all asset data to a single, all public ... This case study documents how MoDOT's Transportation Planning Division (TPD) coordinates with the Information Systems (IS) unit (the agency ...
Case Study: People and Processes Drive Supply Chain Improvements at Honeywell. TMC. MAY 8, 2019. Then you'll be able to leverage your transportation management system (TMS) to execute, automate, and optimize those processes, as well as gain visibility to business intelligence to drive continuous improvement.
The SAP TM implementation allowed the European trucking company to: Enhance logistics management. Simplify transportation planning. Gain more detailed and easy-to-use reporting. Increase the visibility of all transport operations thanks to the automated event monitoring system, SAP Event Management. Optimize transportation resource utilization.
Transportation Management System Case Study. Integrating with the Agile TMS, MD Logistics offers clients more efficient and effective transportation options. Transportation expenses associated with shipping commodities across the world can be mitigated with strategic freight decisions. Successful companies understand the importance of freight ...
StormProof also helps fuel truck drivers locate nearby carriers so they can track, update, and effectively manage third party carriers and partners. This cloud transportation management system features a smart dashboard with real-time analytics, and delivery tracking across multiple sites, making it an extremely sophisticated application in its ...
from a system level and secondly from the detailed case-study level. The case study was chosen by the project sponsors in order to assess the validity and ap-plicability of the method. 2 For a presentation of the Enterprise System Topology, see "Enterprise Methodology: an Ap-proach to Multisystems", in Complex Systems Design & Management ...
Case Study: Wal-Mart's Distribution and Logistics System. Abey Francis. As the world's largest retailer with net sales of almost $419 billion for the fiscal year 2011, Wal-Mart is considered a "best-in-class" company for its supply chain management practices. These practices are a key competitive advantage that have enabled Wal-Mart to ...
tions, Seoul adopted a holistic approach to intelligent transportation system (ITS) management. This case study explores how Seoul co. lects and analyzes urban mobility data to support evidence-based planning and city management.2In the early 2000s, despite a previous decade of investments in urban freeways, Seoul's roads remained highly con.
Case studies: Using FreightPOP shipping management and freight management software to improve supply chain operations and transportation management. ... G2 Grid® for Transportation Management Systems (TMS) "FreightPop has become part of our operating system so to speak, it brings all your carriers into one platform for quoting, tracking, and ...
Each Case Study is presented in detail on the Toolkit website. The information includes: Contextual information: Regulatory environment, operator information, basis of service organization and procurement, basis of financial support. ITS: Overall ITS approach, individual ITS systems implemented, technical details, means of operations management
The study was undertaken to assess the province of Marinduque's fire incidence from 2018 to 2022 and determine its firefighting capability, which includes fire prevention programs, tools, PPEs and Equipment (fire trucks), manpower, skills and trainings acquired, facilities and infrastructure and financial resources management.
Transport Case Studies
This study aims to design an environmental management information system (EMIS) by integrating all necessary environmental documents for project implementation based on ISO 14001:2015 and using an exploratory sequential mixed method of research. The agile project management methodology was also used to speculate how a project must be managed using environmental information.
Therefore, from the perspective of optimizing construction organization and management, this article comprehensively considers various factors in the construction process, innovatively introduces ...
As a fundamental element of the transportation system, traffic signs are widely used to guide traffic behaviors. In recent years, drones have emerged as an important tool for monitoring the conditions of traffic signs. However, the existing image processing technique is heavily reliant on image annotations. It is time consuming to build a high-quality dataset with diverse training images and ...